Partially Complete Units Are Known As Inventory.
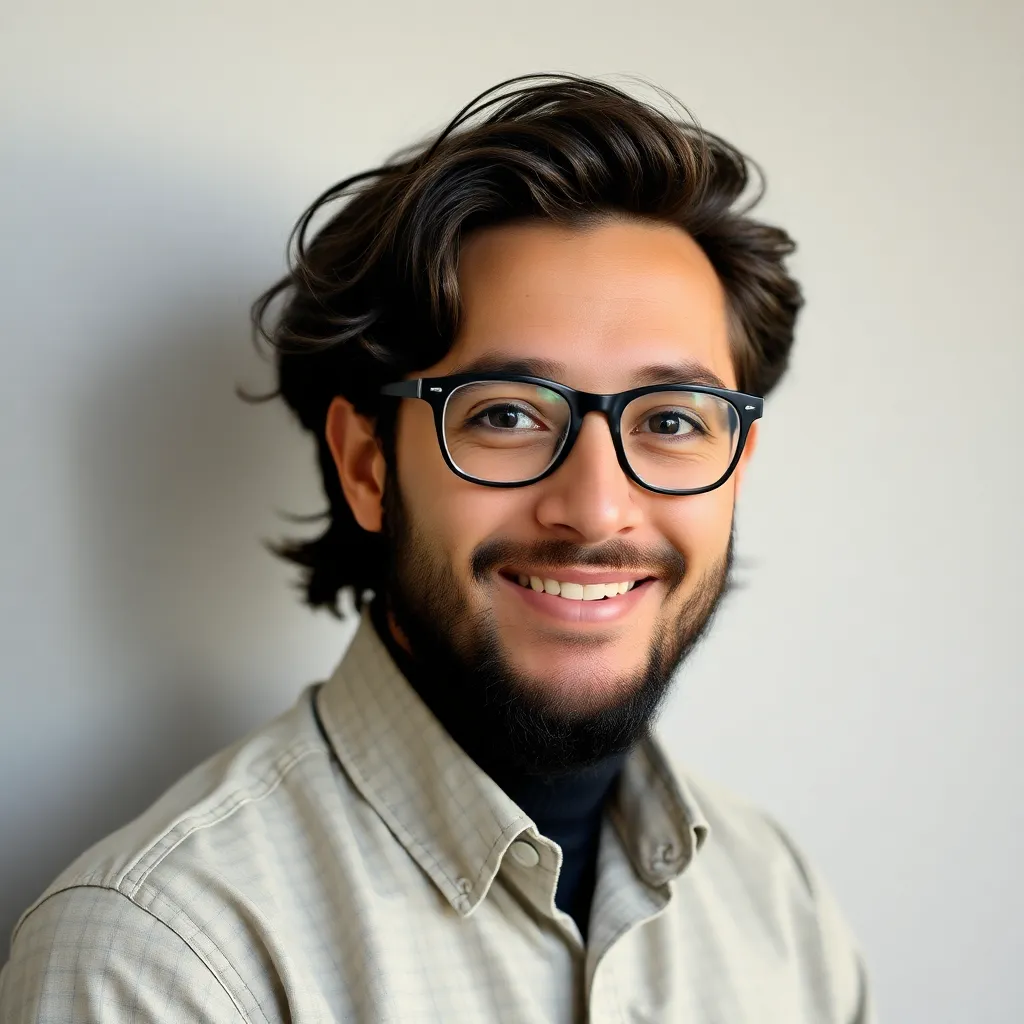
Holbox
Mar 20, 2025 · 6 min read
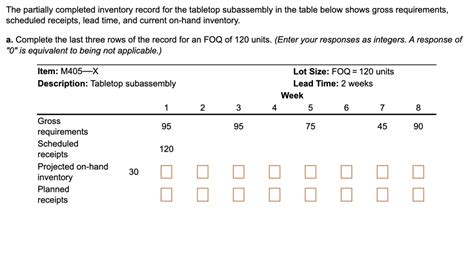
Table of Contents
Partially Complete Units: A Deep Dive into Inventory Management
Partially complete units represent a significant challenge and opportunity within inventory management. Understanding their impact on financial reporting, production efficiency, and overall supply chain health is crucial for any business dealing with work-in-progress (WIP) inventory. This article will explore the complexities of partially complete units, examining their classification, valuation, and the strategies used to effectively manage them.
What are Partially Complete Units?
Partially complete units, often referred to as work-in-progress (WIP), are goods that are in the process of being manufactured but are not yet finished. They represent a stage in the production process where some, but not all, of the necessary operations have been completed. These units are a vital part of the inventory, but their incomplete nature presents unique challenges for accounting, inventory control, and overall business decision-making. Unlike finished goods, which are ready for sale or distribution, WIP requires further processing before it reaches its final state. Think of a car assembly line: a chassis with an engine but no wheels is a partially complete unit; it's not a finished car, nor is it a pile of raw materials.
The Importance of Accurate WIP Tracking
Accurate tracking of partially complete units is paramount for several reasons:
1. Cost Accounting:
Determining the cost of goods sold (COGS) accurately necessitates knowing the cost associated with each partially complete unit. This involves tracking direct materials, direct labor, and manufacturing overhead applied to each unit at each stage of production. Inaccurate tracking leads to skewed COGS figures, affecting profitability analysis and potentially misleading financial reporting.
2. Production Scheduling:
Monitoring WIP levels provides valuable insights into the production process. Bottlenecks can be identified by observing where units accumulate, indicating areas needing improvement or adjustments in resource allocation. Effective scheduling depends on a clear understanding of the current state of production, including the number and stage of completion of partially complete units.
3. Inventory Valuation:
Accurately valuing WIP is crucial for balance sheet accuracy. Various methods exist, each with its own strengths and weaknesses. We'll discuss these methods in detail later.
4. Forecasting Demand:
Knowing the number of units in various stages of completion allows for more accurate forecasting of future finished goods availability. This impacts production planning, sales projections, and overall supply chain management.
Methods for Valuing Partially Complete Units
The valuation of WIP inventory is a complex task, as it lacks the clear-cut value of finished goods. Several methods exist, each with its own advantages and disadvantages:
1. Specific Identification:
This method is best suited for situations where individual units can be easily tracked throughout the production process. It involves directly tracking the costs associated with each individual partially complete unit. While accurate, it's often impractical for high-volume production environments.
2. First-In, First-Out (FIFO):
FIFO assumes that the first units started are the first units completed. This simplifies valuation, particularly when dealing with similar units. However, it may not reflect the actual flow of goods in some production processes.
3. Last-In, First-Out (LIFO):
LIFO assumes that the last units started are the first units completed. This method can be advantageous in inflationary environments, as it reduces taxable income. However, it can lead to a mismatch between the cost of goods sold and the current market value of the inventory.
4. Weighted-Average Cost:
This method calculates the average cost of all units in production, simplifying valuation and reducing the complexity of tracking individual unit costs. It's particularly useful for mass production scenarios where tracking individual costs is impractical.
5. Moving Average Cost:
Similar to the weighted-average method, the moving average method updates the average cost continuously as new units are added to the WIP inventory. This provides a more dynamic reflection of costs compared to the standard weighted-average method.
Challenges in Managing Partially Complete Units
Managing WIP inventory presents several unique challenges:
1. Storage and Handling:
Partially complete units often require specialized storage and handling to prevent damage or deterioration. This adds complexity and cost to the inventory management process. Space optimization and efficient material flow are critical.
2. Tracking and Monitoring:
Tracking the progress and costs of individual partially complete units can be labor-intensive, particularly in complex production environments. Effective inventory management systems, including barcodes, RFID tags, and sophisticated software, are essential for accurate tracking.
3. Obsolescence and Scrap:
Partially complete units are susceptible to obsolescence or scrap if production changes or errors occur. Effective quality control and timely adjustments to production processes are crucial to minimize losses.
4. Valuation Accuracy:
As previously discussed, accurately valuing WIP inventory can be difficult, leading to inaccuracies in financial statements and potentially impacting business decisions.
Strategies for Effective WIP Management
Effective management of partially complete units requires a multi-faceted approach:
1. Robust Inventory Management System (IMS):
Implementing a robust IMS is crucial for tracking units, costs, and progress. Modern systems utilize barcodes, RFID tags, and sophisticated software to provide real-time visibility into the production process.
2. Lean Manufacturing Principles:
Adopting lean manufacturing principles, such as Just-in-Time (JIT) inventory, can minimize WIP levels by reducing the amount of time units spend in the production process. This minimizes storage costs and reduces the risk of obsolescence.
3. Efficient Production Planning:
Careful production planning, utilizing forecasting techniques and capacity analysis, can help to optimize production flow and minimize the buildup of WIP.
4. Regular Inventory Audits:
Regular audits of the WIP inventory help to identify discrepancies, ensure accuracy of valuations, and highlight areas for improvement in the production process.
5. Continuous Improvement:
Continuously evaluating the WIP management process and implementing improvements based on data analysis is essential for optimizing efficiency and reducing costs. Regular review of metrics and feedback loops are critical here.
6. Technology Integration:
Integrating technology, such as ERP systems and automated data collection tools, can significantly enhance WIP management. Real-time data provides better insights and enables timely intervention when needed.
The Impact of Partially Complete Units on Financial Statements
WIP inventory is reported as a current asset on the balance sheet. Its valuation directly impacts the accuracy of the company's financial position. Overvaluation or undervaluation can lead to misrepresentations of profitability and liquidity. The cost of goods sold (COGS) calculation is also significantly influenced by the proper valuation of WIP. Inaccurate costing of WIP translates directly into inaccurate COGS, affecting gross profit and net income calculations.
Conclusion: Mastering the Art of WIP Management
Partially complete units are an inherent part of many manufacturing processes. Effectively managing them is crucial for maintaining accurate financial records, optimizing production efficiency, and ensuring a healthy supply chain. By implementing robust inventory management systems, adopting lean principles, and continuously improving processes, businesses can minimize the challenges associated with WIP and unlock the opportunities it presents. Accurate tracking, timely valuation, and strategic planning are key to mastering the complexities of WIP management and achieving improved financial performance and operational excellence. Remember, a well-managed WIP inventory is a cornerstone of a successful and profitable business.
Latest Posts
Latest Posts
-
Why Might A Company Carry Inventory
Mar 20, 2025
-
The Use Of Money Contributes To Economic Efficiency Because
Mar 20, 2025
-
A Favorable Cost Variance Occurs When
Mar 20, 2025
-
What Is The Likely Product Of The Reaction Shown
Mar 20, 2025
-
Which One Of The Following Is A Strong Acid
Mar 20, 2025
Related Post
Thank you for visiting our website which covers about Partially Complete Units Are Known As Inventory. . We hope the information provided has been useful to you. Feel free to contact us if you have any questions or need further assistance. See you next time and don't miss to bookmark.