Why Might A Company Carry Inventory
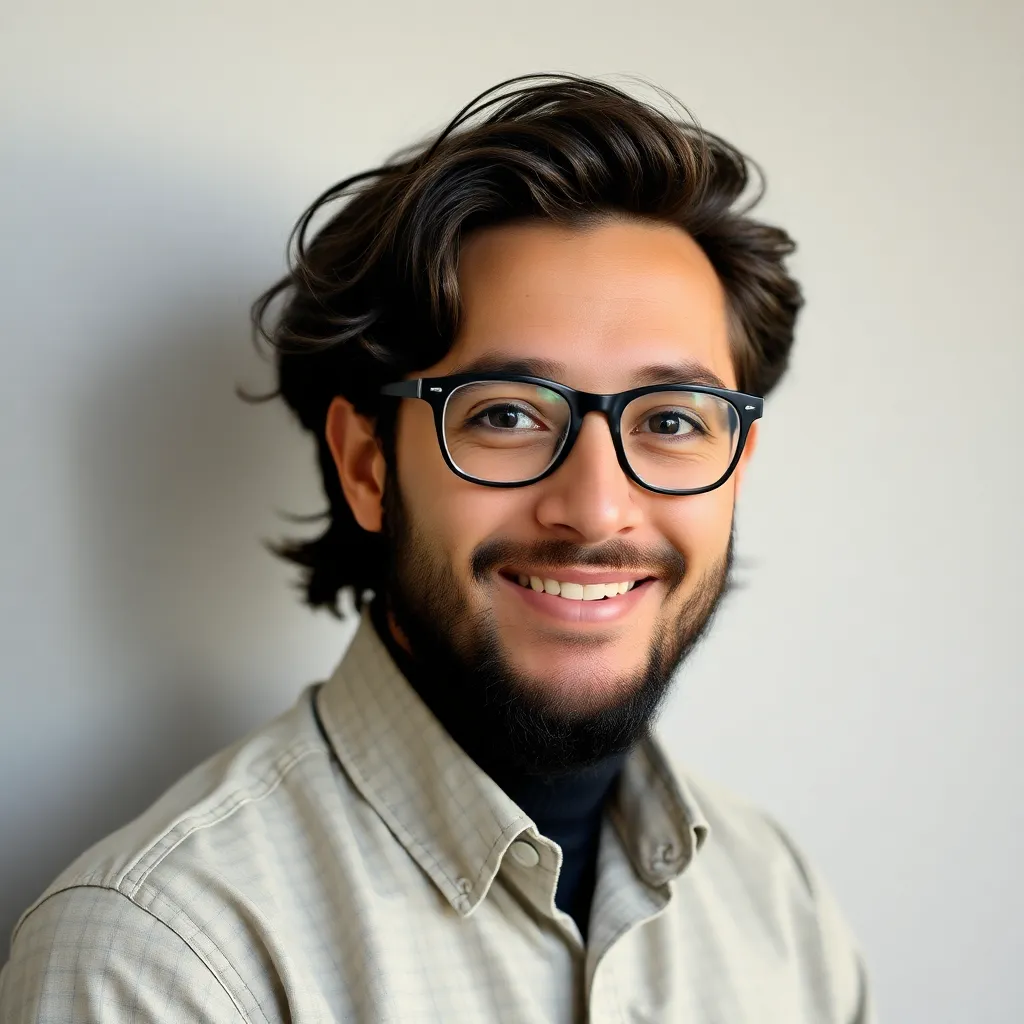
Holbox
Mar 20, 2025 · 6 min read
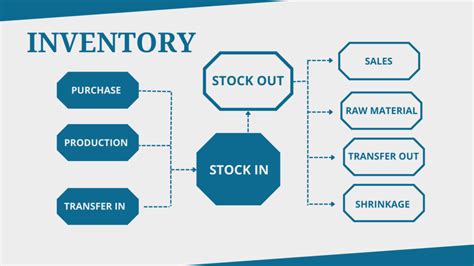
Table of Contents
Why Might a Company Carry Inventory? A Deep Dive into Inventory Management Strategies
Inventory management is a critical aspect of any successful business, regardless of its size or industry. The decision of whether or not to carry inventory, and how much to carry, is a strategic one with significant implications for profitability, customer satisfaction, and overall business health. While some businesses operate with a lean inventory model, others find significant advantages in holding substantial stock. This article delves into the multifaceted reasons why a company might choose to carry inventory, exploring the nuances of different inventory management strategies and the crucial factors influencing this decision.
The Core Advantages of Holding Inventory
Carrying inventory isn't simply about having goods on hand; it's a strategic tool offering numerous advantages, directly impacting a company's bottom line and its relationship with customers.
1. Meeting Customer Demand and Ensuring Sales
This is arguably the most fundamental reason. Having inventory readily available allows companies to fulfill customer orders promptly. This immediacy translates to higher customer satisfaction, repeat business, and a stronger competitive edge. Imagine a customer needing a product urgently – a company with sufficient inventory can secure the sale while a competitor with depleted stock loses the opportunity. This is particularly crucial in industries with high customer demand and short lead times.
2. Preventing Stockouts and Lost Sales
Stockouts, the dreaded state of running out of inventory, can severely impact revenue. They not only lead to lost sales in the immediate term but can also damage a company's reputation and erode customer loyalty. Customers who encounter stockouts may switch to competitors, leading to a potential loss of market share. Carrying sufficient inventory acts as a buffer, mitigating the risk of stockouts and maintaining a consistent flow of sales.
3. Taking Advantage of Economies of Scale and Bulk Purchasing
Purchasing inventory in bulk often comes with significant cost advantages. Companies can negotiate lower prices per unit by ordering larger quantities, reducing the overall cost of goods sold. This strategy is particularly effective for products with stable demand and long shelf lives. While holding larger quantities incurs storage costs, the savings from bulk purchasing frequently outweigh these expenses.
4. Smoothing Out Production and Stabilizing Operations
In manufacturing and production environments, carrying inventory can help stabilize operations by decoupling production from demand fluctuations. This means that even if demand fluctuates significantly, the company can maintain a consistent production schedule, avoiding costly disruptions and overtime. This is particularly beneficial in industries with seasonal demand or unpredictable market trends.
5. Capitalizing on Market Opportunities and Price Fluctuations
Inventory can act as a strategic asset, allowing companies to respond effectively to unexpected market opportunities. For instance, if a competitor experiences a stockout or a sudden surge in demand arises, a company with adequate inventory can quickly capitalize on the situation, gaining market share and revenue. Similarly, companies might hold inventory to mitigate risks associated with price fluctuations. By purchasing in anticipation of price increases, they can safeguard their profit margins.
The Costs and Risks Associated with Holding Inventory
While the advantages are undeniable, carrying inventory is not without its challenges. Several costs and risks must be carefully considered:
1. Holding Costs: Storage, Insurance, and Obsolescence
Inventory holding costs can be substantial. These costs include storage fees, insurance premiums, taxes, and the risk of obsolescence or spoilage. The longer inventory sits in storage, the higher these costs become. This is particularly true for perishable goods or products with short shelf lives. Effective inventory management techniques are crucial to minimize these costs.
2. Financial Investment and Tied-Up Capital
Inventory represents a significant investment of capital. The money tied up in inventory could be used for other purposes, such as research and development, marketing, or expansion. This opportunity cost must be carefully weighed against the benefits of carrying inventory. Efficient inventory management minimizes the amount of capital tied up in stock.
3. Risk of Damage, Theft, or Spoilage
Inventory is susceptible to damage, theft, or spoilage, leading to financial losses. Implementing robust security measures and proper storage conditions is essential to mitigate these risks. Regular inventory checks and efficient stock rotation are vital for minimizing losses due to spoilage or obsolescence.
4. Complexity of Inventory Management
Managing inventory effectively requires sophisticated systems and processes. Accurate tracking of inventory levels, forecasting demand, and managing the supply chain are essential tasks. This can involve significant investment in technology, training, and personnel. Poor inventory management can lead to inefficiencies, stockouts, and increased costs.
Different Inventory Management Strategies
Companies employ various strategies to manage their inventory effectively, balancing the benefits of holding stock with the associated costs and risks. These strategies include:
1. Just-in-Time (JIT) Inventory
This lean manufacturing approach aims to minimize inventory levels by ordering and receiving materials only when needed for production. JIT reduces storage costs and the risk of obsolescence, but it requires a highly efficient and reliable supply chain. Any disruption in the supply chain can severely impact production.
2. Economic Order Quantity (EOQ)
This model determines the optimal order quantity that minimizes the total costs of ordering and holding inventory. It balances the costs of placing frequent orders with the costs of holding large quantities of inventory. EOQ models help companies find the sweet spot between minimizing costs and ensuring sufficient stock.
3. Materials Requirements Planning (MRP)
MRP is a production planning and inventory control system that uses bills of materials and master production schedules to determine the quantities and timing of materials needed for production. MRP helps companies plan their inventory needs more accurately and avoid stockouts or excess inventory. It requires detailed information about production processes and demand forecasts.
4. Vendor-Managed Inventory (VMI)
In VMI, the supplier manages the inventory levels for its customers. The supplier is responsible for replenishing inventory as needed, based on the customer's demand. This approach reduces the burden on the customer's inventory management team and can improve efficiency. However, it requires a high degree of trust and collaboration between the supplier and the customer.
5. Safety Stock
This is a buffer stock held to mitigate against unexpected demand fluctuations or supply chain disruptions. Safety stock reduces the risk of stockouts but increases holding costs. The appropriate level of safety stock depends on the variability of demand and the lead time for replenishment.
Conclusion: The Strategic Importance of Inventory Decisions
The decision of whether and how much inventory to carry is a critical strategic decision that significantly impacts a company's financial performance, customer satisfaction, and overall competitiveness. There's no one-size-fits-all answer; the optimal inventory management strategy depends on various factors, including industry, product characteristics, demand patterns, supply chain reliability, and the company's risk tolerance. Careful consideration of the benefits and costs associated with inventory, coupled with the implementation of an appropriate inventory management strategy, is essential for achieving optimal business outcomes. By meticulously analyzing demand forecasts, optimizing supply chains, and employing sophisticated inventory management techniques, companies can effectively leverage inventory as a strategic asset, driving profitability and securing a competitive edge in the marketplace.
Latest Posts
Latest Posts
-
Two Spacecraft Are Following Paths In Space Given By
Mar 21, 2025
-
When Consumers Decide To Purchase A Particular Product They
Mar 21, 2025
-
Refer To Figure 4 17 At A Price Of
Mar 21, 2025
-
For A Company Providing Services As Opposed To Products
Mar 21, 2025
-
Online Buying In Organizational Markets Is Prominent Because Internet Technology
Mar 21, 2025
Related Post
Thank you for visiting our website which covers about Why Might A Company Carry Inventory . We hope the information provided has been useful to you. Feel free to contact us if you have any questions or need further assistance. See you next time and don't miss to bookmark.