Which Of The Following Best Characterizes Jit Systems
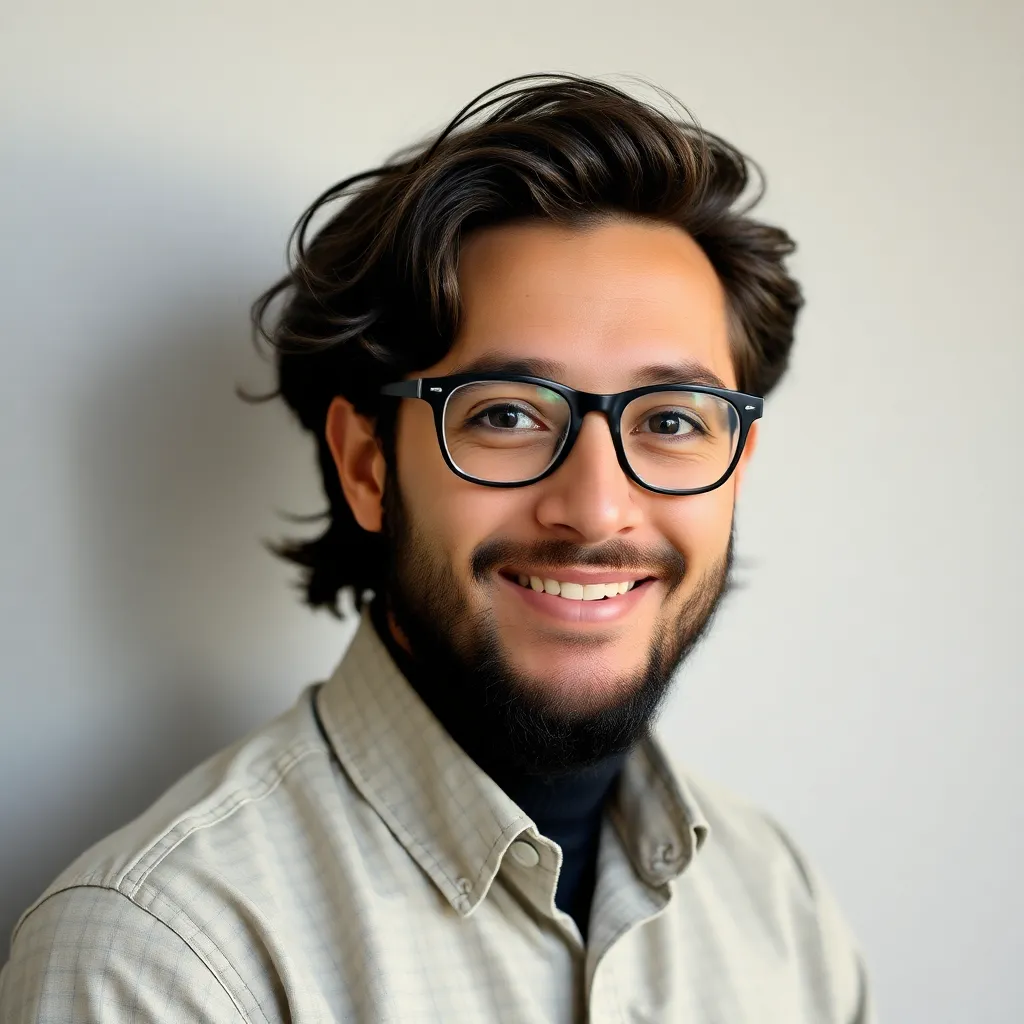
Holbox
Mar 28, 2025 · 6 min read
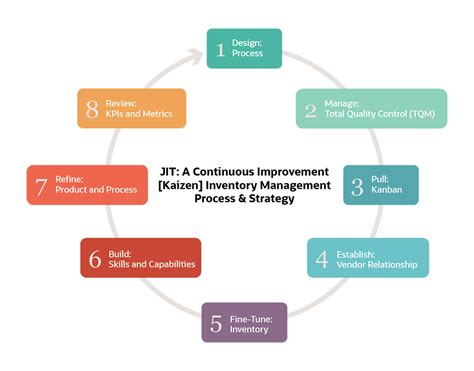
Table of Contents
- Which Of The Following Best Characterizes Jit Systems
- Table of Contents
- Which of the Following Best Characterizes JIT Systems? A Deep Dive into Just-in-Time Manufacturing
- Core Principles of JIT Systems
- 1. Waste Reduction (Muda): The Cornerstone of JIT
- 2. Pull System: Demand-Driven Production
- 3. Continuous Improvement (Kaizen): A Culture of Enhancement
- 4. Total Quality Management (TQM): Quality Built-In, Not Inspected In
- 5. Supplier Partnerships: Close Collaboration
- Comparing JIT with Other Inventory Management Systems
- Misconceptions about JIT Systems
- Successfully Implementing and Maintaining a JIT System
- Conclusion: Understanding the Essence of JIT
- Latest Posts
- Latest Posts
- Related Post
Which of the Following Best Characterizes JIT Systems? A Deep Dive into Just-in-Time Manufacturing
Just-in-time (JIT) manufacturing, also known as lean manufacturing, has revolutionized the way businesses approach production. Instead of large inventories clogging up warehouses, JIT focuses on producing goods only when they're needed. But understanding what truly characterizes JIT systems requires a deeper look beyond the surface. This article will explore the core principles of JIT, compare and contrast it with other inventory management systems, and address common misconceptions to provide a comprehensive understanding of what truly defines a successful JIT implementation.
Core Principles of JIT Systems
Several key principles underpin the effectiveness of JIT systems. Understanding these principles is crucial to recognizing a true JIT implementation versus a system that merely incorporates some JIT elements.
1. Waste Reduction (Muda): The Cornerstone of JIT
The elimination of waste, often referred to as "muda" in Japanese, is paramount in JIT. This encompasses seven types of waste:
- Transportation: Unnecessary movement of materials or products.
- Inventory: Excess stock tying up capital and space.
- Motion: Unnecessary movements of people or equipment.
- Waiting: Idle time for machines, workers, or materials.
- Overproduction: Producing more than is needed, leading to waste and obsolescence.
- Over-processing: Performing more work than is necessary to meet customer requirements.
- Defects: Errors in production leading to rework, scrap, and customer dissatisfaction.
Successfully implementing JIT requires a relentless focus on identifying and eliminating these forms of waste across the entire value stream.
2. Pull System: Demand-Driven Production
Unlike traditional push systems, where production is based on forecasts and planned schedules, JIT employs a pull system. Production is triggered by actual customer demand. This ensures that only what is needed is produced, minimizing waste and inventory. Kanban systems, visual signals indicating the need for replenishment, are frequently used to manage the flow of materials in a pull system.
3. Continuous Improvement (Kaizen): A Culture of Enhancement
JIT is not a static system; it's a continuous improvement process. Kaizen, the Japanese term for continuous improvement, is integral to JIT. Regularly reviewing processes, identifying bottlenecks, and implementing small, incremental changes are crucial for maintaining efficiency and competitiveness. This constant striving for perfection is what allows JIT systems to adapt and improve over time.
4. Total Quality Management (TQM): Quality Built-In, Not Inspected In
Quality is not an afterthought in JIT; it's built into the process. Total Quality Management (TQM) principles are essential, ensuring that defects are prevented rather than detected and corrected later. This prevents waste caused by rework, scrap, and customer returns. Employee empowerment and problem-solving are key components of TQM within a JIT environment.
5. Supplier Partnerships: Close Collaboration
JIT systems rely heavily on strong relationships with suppliers. Suppliers need to be reliable and able to deliver high-quality materials precisely when needed. This necessitates close collaboration, often involving long-term contracts and shared information systems to ensure a smooth flow of materials.
Comparing JIT with Other Inventory Management Systems
Understanding JIT requires comparing it with other inventory management systems like:
1. Just-in-Case (JIC) Inventory: This traditional approach emphasizes holding large inventories as a buffer against unforeseen events like supply chain disruptions or unexpected demand spikes. While offering a safety net, JIC ties up significant capital, increases storage costs, and risks obsolescence.
2. Materials Requirements Planning (MRP): MRP uses a bill of materials and master production schedule to plan and schedule the acquisition of raw materials and components. While more sophisticated than simple JIC, MRP still relies on forecasting and can lead to excess inventory if demand predictions are inaccurate.
3. Enterprise Resource Planning (ERP): ERP systems integrate various business functions, including inventory management. While ERP can incorporate JIT principles, it's a broader system that can be used with various inventory management approaches. The successful implementation of JIT within an ERP framework requires careful configuration and process optimization.
In contrast to these systems, JIT:
- Minimizes inventory holding costs: By reducing inventory levels significantly.
- Reduces waste: By focusing on eliminating all forms of muda.
- Improves quality: By building quality into the process from the start.
- Increases responsiveness to customer demand: By producing only what is needed, when it is needed.
- Requires strong supplier relationships: To ensure timely delivery of high-quality materials.
Misconceptions about JIT Systems
Several misconceptions surround JIT systems. Understanding these helps clarify the true nature of a successful JIT implementation.
1. JIT is Only for Manufacturing: While JIT originated in manufacturing, its principles can be applied to various industries, including services, healthcare, and even software development. The core focus on reducing waste, improving flow, and responding to demand applies universally.
2. JIT Eliminates All Inventory: A completely zero-inventory system is unrealistic and often impractical. JIT aims to minimize inventory to the optimal level necessary to meet demand while minimizing waste. Some safety stock might be maintained to account for minor variations in demand or supply.
3. JIT is Easy to Implement: Implementing JIT effectively requires a significant cultural shift, process redesign, and close collaboration with suppliers. It's not a quick fix but a long-term commitment requiring substantial investment in training, technology, and process improvement.
Successfully Implementing and Maintaining a JIT System
Successful JIT implementation involves several key steps:
1. Value Stream Mapping: Identify all steps in the production process and pinpoint areas of waste. This visual representation allows for targeted improvement efforts.
2. Process Improvement: Implement strategies to eliminate waste, streamline processes, and optimize workflow. This might involve implementing cellular manufacturing, 5S methodologies (Sort, Set in Order, Shine, Standardize, Sustain), or Kanban systems.
3. Supplier Relationships: Foster close collaborations with suppliers, ensuring timely delivery of high-quality materials. This may involve joint planning, shared information systems, and long-term contracts.
4. Employee Training and Empowerment: Train employees on JIT principles, empower them to identify and solve problems, and foster a culture of continuous improvement (Kaizen).
5. Continuous Monitoring and Improvement: Regularly monitor key performance indicators (KPIs) like inventory levels, lead times, defect rates, and production efficiency. Continuously analyze data and implement improvements to optimize the system over time.
Conclusion: Understanding the Essence of JIT
In conclusion, JIT systems are far more than simply reducing inventory; they represent a fundamental shift in manufacturing philosophy. They're characterized by a relentless focus on waste reduction, a pull system driven by actual demand, a culture of continuous improvement, strong supplier partnerships, and a commitment to total quality management. While implementing JIT requires significant effort and commitment, the rewards—reduced costs, improved quality, increased efficiency, and enhanced customer responsiveness—make it a powerful tool for achieving competitive advantage in today's dynamic business environment. Understanding these core principles and avoiding common misconceptions is crucial for any organization considering implementing a true JIT system. The key to success lies in embracing the underlying philosophy of continuous improvement and striving for operational excellence across the entire value chain.
Latest Posts
Latest Posts
-
Consumers Seek To Maximize Satisfaction Based On
Mar 31, 2025
-
Label The Parts Of The Skin And Subcutaneous Tissue
Mar 31, 2025
-
The Contractile Molecules In Muscle Cells Are Blank
Mar 31, 2025
-
The Text Defines As The Flow Of Events Or Transactions
Mar 31, 2025
-
Bond Ratings Classify Bonds Based On
Mar 31, 2025
Related Post
Thank you for visiting our website which covers about Which Of The Following Best Characterizes Jit Systems . We hope the information provided has been useful to you. Feel free to contact us if you have any questions or need further assistance. See you next time and don't miss to bookmark.