Standard Costs Are Used In The Calculation Of
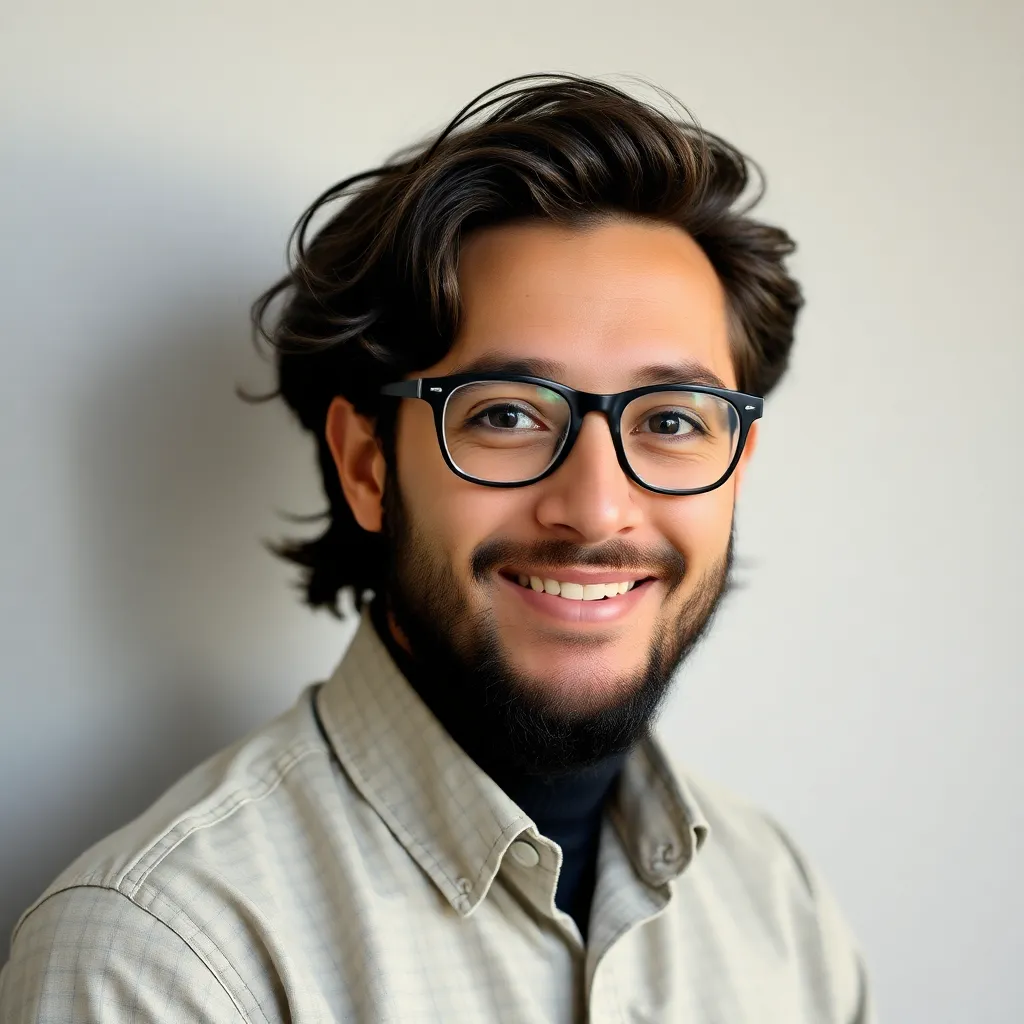
Holbox
Mar 14, 2025 · 7 min read
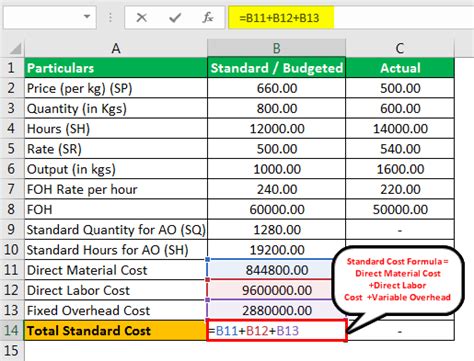
Table of Contents
Standard Costs: The Cornerstone of Cost Calculation and Management
Standard costing is a powerful tool used in managerial accounting to plan, control, and evaluate the costs of production. It involves setting predetermined costs for materials, labor, and overhead, which are then compared to actual costs to identify variances and improve efficiency. This article will delve into the intricate details of how standard costs are used in the calculation of various aspects of a business's financial performance. We'll explore the process of setting standards, analyzing variances, and the crucial role standard costing plays in effective management decision-making.
What are Standard Costs?
Standard costs represent the expected or predetermined costs associated with producing a single unit of a product or service. They are meticulously planned and based on efficient production levels, realistic material usage, and expected labor hours. These standards are not arbitrary; they are derived from thorough analysis, historical data, engineering estimates, and industry best practices. The process of establishing standard costs requires a detailed understanding of all the elements involved in production.
Key Components of Standard Costs
Standard costs encompass three primary elements:
-
Standard Material Cost: This includes the standard quantity of materials required per unit and the standard price per unit of material. For example, a standard cost for a cake might include the standard weight of flour, sugar, and eggs, each priced at a predetermined rate. Variations in quality or market fluctuations are factored in to create a realistic standard.
-
Standard Labor Cost: This component combines the standard hours of labor needed to produce one unit with the standard labor rate per hour. This requires careful analysis of the production process to determine the necessary time and skill levels required. Considerations like employee efficiency and training are incorporated.
-
Standard Overhead Cost: This is the most complex element, encompassing all indirect costs associated with production, such as factory rent, utilities, depreciation of machinery, and supervision. Overhead costs are often allocated based on a predetermined overhead rate, usually tied to a cost driver like direct labor hours or machine hours. Accurate allocation is crucial for meaningful variance analysis.
Calculating Standard Costs: A Step-by-Step Guide
The calculation of standard costs involves a methodical process:
-
Determine Standard Material Costs: This necessitates identifying the standard quantity of each raw material required per unit of output. This is often based on engineering specifications, past experience, and anticipated improvements in efficiency. The standard price per unit of material is also established, considering anticipated market prices and potential discounts for bulk purchases.
- Example: If producing one widget requires 2 pounds of steel at a standard price of $5 per pound, the standard material cost for steel is $10 per widget (2 pounds * $5/pound).
-
Determine Standard Labor Costs: This involves estimating the standard labor hours required per unit of output. This is often determined through time and motion studies or expert opinion. The standard labor rate per hour is also established, factoring in wage rates, employee benefits, and expected overtime.
- Example: If producing one widget requires 0.5 hours of labor at a standard rate of $20 per hour, the standard labor cost is $10 per widget (0.5 hours * $20/hour).
-
Determine Standard Overhead Costs: This is often the most challenging aspect, due to the indirect nature of overhead costs. A predetermined overhead rate is calculated by dividing the estimated total overhead costs for the period by the estimated total activity level (e.g., machine hours, direct labor hours). This rate is then multiplied by the standard activity level per unit to obtain the standard overhead cost per unit.
- Example: If the estimated total overhead for the year is $100,000, and the estimated total machine hours are 10,000, the predetermined overhead rate is $10 per machine hour ($100,000 / 10,000 hours). If one widget requires 1 machine hour, the standard overhead cost per widget is $10.
-
Calculate Total Standard Cost: The total standard cost per unit is the sum of the standard material cost, standard labor cost, and standard overhead cost.
- Example: Using the figures from the previous examples, the total standard cost per widget is $30 ($10 material + $10 labor + $10 overhead).
Analyzing Variances: Identifying the Gaps
The real power of standard costing lies in its ability to identify variances—the differences between actual and standard costs. Analyzing these variances provides valuable insights into operational efficiency and allows for corrective actions. There are several types of variances:
Material Variances
-
Material Price Variance: This measures the difference between the actual price paid for materials and the standard price. A favorable variance indicates that materials were purchased at a lower price than expected, while an unfavorable variance suggests higher-than-expected prices.
-
Material Usage Variance: This measures the difference between the actual quantity of materials used and the standard quantity allowed for actual production. A favorable variance implies that less material was used than anticipated, whereas an unfavorable variance suggests higher-than-expected material consumption.
Labor Variances
-
Labor Rate Variance: This reflects the difference between the actual labor rate paid and the standard labor rate. A favorable variance indicates lower-than-expected labor costs, while an unfavorable variance suggests higher labor costs than anticipated.
-
Labor Efficiency Variance: This measures the difference between the actual labor hours used and the standard labor hours allowed for actual production. A favorable variance shows that less labor time was used than expected, while an unfavorable variance points to higher labor hours than planned.
Overhead Variances
Overhead variances are more complex because overhead costs are indirect. Common variances include:
-
Variable Overhead Spending Variance: This compares actual variable overhead costs to the budget for variable overhead, based on actual activity levels.
-
Variable Overhead Efficiency Variance: This reflects the difference between the actual level of the activity (e.g., machine hours) and the standard activity level for actual output.
-
Fixed Overhead Budget Variance: This compares actual fixed overhead costs to the budgeted fixed overhead costs.
-
Fixed Overhead Volume Variance: This measures the difference between the budgeted fixed overhead and the fixed overhead absorbed based on the standard activity level for actual production.
Using Standard Costs for Decision Making
The information derived from standard costing and variance analysis is invaluable for managerial decision-making. It empowers businesses to:
-
Improve Production Efficiency: By identifying and analyzing variances, managers can pinpoint areas where production processes can be improved, leading to reduced material usage, labor hours, and overall costs.
-
Enhance Cost Control: The systematic tracking of costs against standards promotes better cost control and encourages managers to actively monitor and manage expenses.
-
Set Realistic Budgets: Standard costs provide a reliable basis for setting realistic budgets and financial forecasts.
-
Improve Product Pricing: Understanding the cost structure through standard costing allows businesses to set competitive and profitable product prices.
-
Evaluate Performance: Standard costing offers a benchmark for evaluating the performance of different departments and production units.
Limitations of Standard Costing
While standard costing is a robust tool, it is important to acknowledge its limitations:
-
Inflexibility: Standard costs can be inflexible in rapidly changing environments, as the standards may quickly become outdated. Regular reviews and updates are necessary to maintain accuracy.
-
Complexity: Implementing and maintaining a standard costing system can be complex and time-consuming, requiring significant upfront investment and ongoing effort.
-
Oversimplification: Standard costing may oversimplify complex production processes, leading to inaccurate cost allocations and variance analyses.
-
Focus on Efficiency: While crucial, a sole focus on efficiency might compromise other important factors such as quality and employee morale.
Conclusion
Standard costs are an integral part of effective cost management. The process of setting, monitoring, and analyzing these standards offers invaluable insights into operational efficiency, cost control, and performance evaluation. While there are limitations to be considered, the benefits of improved decision-making, better cost control, and enhanced profitability far outweigh the challenges, making standard costing an essential tool for any organization aiming to optimize its financial performance. By understanding how standard costs are used in the calculation of material, labor, and overhead costs, and by effectively analyzing variances, businesses can achieve significant improvements in efficiency and profitability. The insights gained from this system provide a robust framework for informed strategic and operational decision-making.
Latest Posts
Latest Posts
-
Think About Consumer Complaints Which Of The Following Is Correct
Mar 14, 2025
-
Which Of The Following Disorders Involves The Vertebrae
Mar 14, 2025
-
How Does The Full Path Attribution Model Calculate Credit
Mar 14, 2025
-
The Allowance Method Is Required By
Mar 14, 2025
-
A Circuit Is Constructed With 5 Capacitors And A Battery
Mar 14, 2025
Related Post
Thank you for visiting our website which covers about Standard Costs Are Used In The Calculation Of . We hope the information provided has been useful to you. Feel free to contact us if you have any questions or need further assistance. See you next time and don't miss to bookmark.