Cpk Is Useful Even When The Process Is Not Centered.
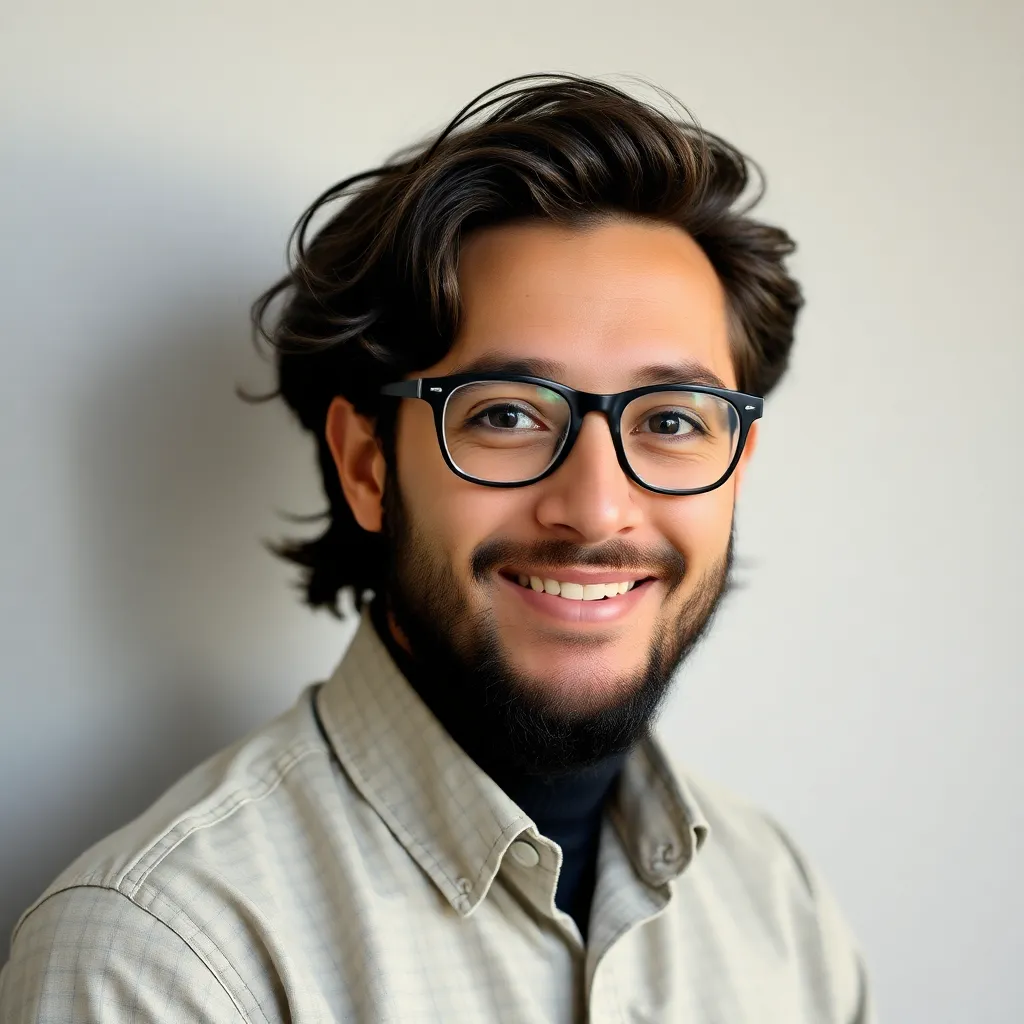
Holbox
Mar 20, 2025 · 5 min read
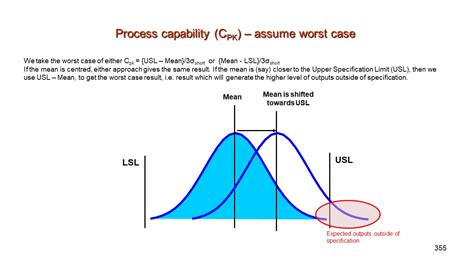
Table of Contents
CPk is Useful Even When the Process is Not Centered
Process capability analysis is a crucial tool in quality management, providing insights into a process's ability to meet predefined specifications. The most commonly used metric in this analysis is the Capability Index, often represented as Cpk. Many believe that Cpk is only useful when a process is centered – meaning the process mean is exactly halfway between the upper and lower specification limits (USL and LSL). This misconception limits the understanding and application of this valuable tool. This article will demonstrate why Cpk remains a highly valuable metric even when the process mean is not centered.
Understanding Cpk and Its Components
Before delving into the nuances of off-center processes, let's briefly review the fundamentals of Cpk. Cpk is calculated using the following formula:
Cpk = min[(USL - X̄) / 3σ, (X̄ - LSL) / 3σ]
Where:
- USL: Upper Specification Limit
- LSL: Lower Specification Limit
- X̄: Process Mean
- σ: Process Standard Deviation
This formula essentially measures the minimum distance between the process mean and the nearest specification limit, divided by three times the process standard deviation. This three-sigma representation relates to the natural variation within the process and assumes a normal distribution.
A higher Cpk value indicates a more capable process. Generally, a Cpk of 1.33 or higher is considered acceptable, demonstrating that the process consistently produces outputs within the specified limits.
The Misconception: Cpk Requires Centered Processes
The common misunderstanding arises from the relationship between Cpk and another capability index, Cp. Cp only considers the process spread relative to the specification width, irrespective of the process mean:
Cp = (USL - LSL) / 6σ
Cp essentially focuses on the process's precision and consistency, regardless of whether the process mean is centered. However, Cp doesn't account for the process's location relative to the specification limits.
This is where Cpk comes into play. Cpk incorporates both the process spread (like Cp) and the process mean's position relative to the specification limits. It's a more comprehensive measure of process capability, providing a clearer picture of the process's ability to consistently meet specifications.
Why Cpk is Useful with Off-Centered Processes
Even when a process isn't centered, Cpk provides crucial information:
1. Identifying the Magnitude of the Problem:
An off-centered process will inherently have a lower Cpk than a centered process with the same standard deviation. This lower Cpk value directly quantifies the extent of the problem. A Cpk of 1.0, for example, indicates that the process is only marginally capable, even if the spread is acceptable. This immediate quantification helps prioritize improvement efforts.
2. Prioritizing Improvement Efforts:
Cpk helps pinpoint the specific area requiring attention. If the Cpk is low due to a lack of centering, it clearly signals the need to adjust the process mean. This directs improvement efforts towards the root cause of the off-center process, rather than wasting resources on unnecessary adjustments to the process spread.
3. Tracking Improvement Progress:
As corrective actions are implemented to center the process, Cpk provides a quantitative measure to track the improvement. Monitoring changes in Cpk values shows the effectiveness of the implemented changes. This data-driven approach ensures that improvements are focused and yield measurable results.
4. Comparing Processes:
Even if two processes have different degrees of centering, Cpk enables a direct comparison of their capability. It provides a standardized metric to evaluate and rank processes based on their overall ability to meet specifications, irrespective of their mean location. This is useful for resource allocation and decision-making.
5. Risk Assessment:
A low Cpk value, regardless of centering, indicates a higher risk of producing non-conforming products. This knowledge is critical for proactive risk management and helps in making informed decisions regarding product release, customer communication, and potential recall strategies.
Examples Illustrating Cpk's Value in Off-Center Processes
Let's consider two scenarios:
Scenario 1: Centered Process
- USL: 100
- LSL: 0
- X̄: 50
- σ: 8.33
Cp = (100 - 0) / (6 * 8.33) = 2 Cpk = min[(100 - 50) / (3 * 8.33), (50 - 0) / (3 * 8.33)] = 2
Scenario 2: Off-Centered Process
- USL: 100
- LSL: 0
- X̄: 60
- σ: 8.33
Cp = (100 - 0) / (6 * 8.33) = 2 Cpk = min[(100 - 60) / (3 * 8.33), (60 - 0) / (3 * 8.33)] = 1.33
Notice that in Scenario 2, the process is not centered, but Cpk still provides valuable information. Although the process spread remains the same (Cp = 2), the off-center process results in a lower Cpk (1.33), indicating a higher risk of producing out-of-specification products. This information would be missed if only Cp was considered.
Beyond the Basics: Interpreting Cpk Values
Interpreting Cpk values necessitates a holistic approach. Simply looking at a single numerical value isn't sufficient; it's important to analyze the Cpk in conjunction with other process data, such as the process mean, standard deviation, and the shape of the process distribution. Visual tools like histograms and control charts can offer valuable insights that supplement the numerical Cpk value. This helps identify the underlying reasons for the low Cpk and guide appropriate corrective actions.
Conclusion: Cpk Remains Essential Regardless of Centering
While a centered process is ideal, it's not a prerequisite for using Cpk effectively. Cpk's true power lies in its ability to provide a comprehensive measure of process capability, regardless of the process mean's position. It quantifies the potential for producing non-conforming outputs, identifies areas for improvement, and enables effective monitoring of progress. By understanding and effectively using Cpk, even in off-centered processes, organizations can enhance their quality management strategies, reduce waste, and ultimately improve product quality. Ignoring Cpk simply because the process mean is off-center deprives organizations of a powerful tool for enhancing their quality control and management systems. This comprehensive understanding and utilization of Cpk are vital for the continuous improvement of any process.
Latest Posts
Latest Posts
-
Rna Polymerase Is Guided By The
Mar 21, 2025
-
Pensions Are Referred To As Defined Benefits Plans Because
Mar 21, 2025
-
Drag The Appropriate Labels To Their Respective Targets Facial Nerve
Mar 21, 2025
-
How Are An Interval And A Segment Different
Mar 21, 2025
-
The Two Main Types Of Data Are
Mar 21, 2025
Related Post
Thank you for visiting our website which covers about Cpk Is Useful Even When The Process Is Not Centered. . We hope the information provided has been useful to you. Feel free to contact us if you have any questions or need further assistance. See you next time and don't miss to bookmark.