Allocation Bases That Do Not Drive Overhead Costs
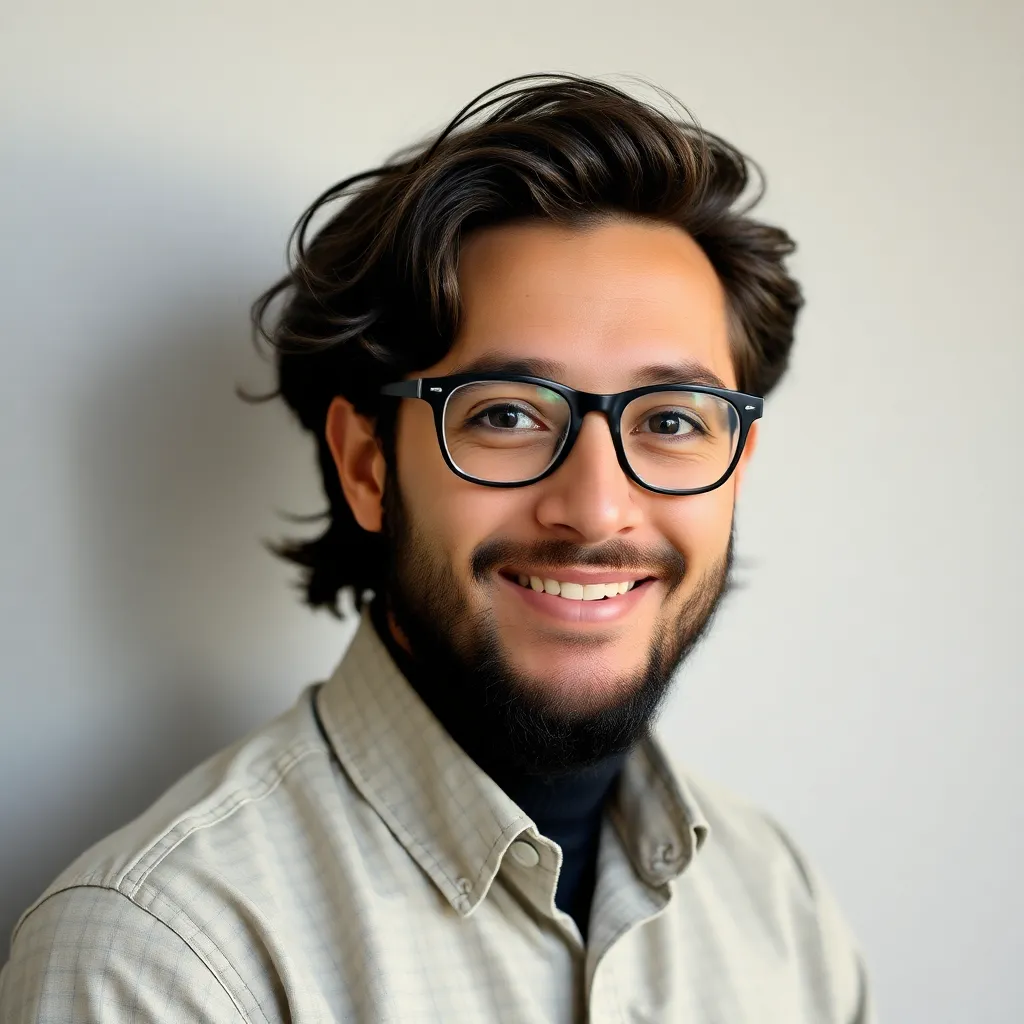
Holbox
Mar 15, 2025 · 7 min read
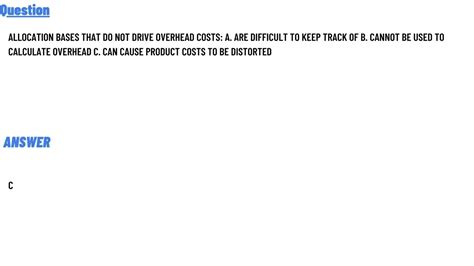
Table of Contents
Allocation Bases That Do Not Drive Overhead Costs: A Comprehensive Guide
Selecting the right allocation base for overhead costs is crucial for accurate cost accounting and effective management decision-making. However, many commonly used bases don't accurately reflect the actual drivers of overhead. Using inappropriate allocation bases can lead to distorted product costs, flawed pricing strategies, and ultimately, poor business decisions. This article delves deep into the intricacies of overhead allocation, highlighting allocation bases that often fail to accurately reflect overhead costs and exploring more suitable alternatives.
Understanding Overhead Costs and Allocation
Overhead costs, also known as indirect costs, are expenses that aren't directly traceable to specific products or services. Examples include rent, utilities, depreciation of equipment, and salaries of support staff. Allocating these costs is essential to determine the full cost of production and provide a more comprehensive picture of profitability.
The goal of overhead allocation is to assign these indirect costs to cost objects (products, services, departments) in a fair and accurate manner. This process uses an allocation base, a measurable factor that reflects the consumption of overhead resources. The problem arises when the chosen base doesn't accurately reflect the actual consumption of resources.
Allocation Bases That Often Fail: A Critical Analysis
Several commonly used allocation bases, while seemingly straightforward, often fail to accurately capture the drivers of overhead costs. Let's analyze some of the most prevalent offenders:
1. Direct Labor Hours: A Historical Relic
For many years, direct labor hours were a popular allocation base. The assumption was that overhead costs increased proportionally with the number of direct labor hours worked. However, this is increasingly inaccurate in today's automated manufacturing environments. Automation reduces the reliance on direct labor, yet overhead costs remain, if not increase, due to the cost of maintaining sophisticated machinery and technology. Using direct labor hours in such a setting misallocates overhead, potentially undercosting automated products and overcosting labor-intensive ones.
Why it fails: Ignores the impact of automation, technology, and indirect labor. Doesn't reflect the true drivers of modern overhead costs.
2. Machine Hours: A Limited Perspective
Machine hours, while seemingly a more relevant metric than direct labor hours in automated environments, also has limitations. It assumes a linear relationship between machine usage and overhead costs. This overlooks various factors like setup time, idle time, and the varying complexity of different tasks performed on the same machine. A highly complex operation performed for a short time might consume more resources (maintenance, specialized tools) than a simpler operation running for longer.
Why it fails: Ignores setup times, idle times, and varying complexity of operations. Assumes a uniform consumption of overhead resources per machine hour, which is often not the case.
3. Direct Material Costs: A Misleading Proxy
Using direct material costs as an allocation base implies that overhead costs are directly proportional to the value of raw materials used. This approach is flawed as it doesn't account for the various other factors contributing to overhead. A product with high material costs doesn't automatically incur higher overhead. Conversely, a product with low material costs might require extensive machine processing and specialized setup, thereby incurring significant overhead.
Why it fails: Ignores the complexities of production processes. Fails to reflect the diverse drivers of overhead costs beyond material consumption.
4. Sales Revenue: A Poor Indicator of Resource Consumption
Allocating overhead based on sales revenue connects overhead costs to the final output rather than the resources consumed during production. This approach is inappropriate as it doesn't reflect the actual consumption of overhead resources during the production process itself. A product with high sales might have low resource consumption and vice-versa.
Why it fails: Focuses on output rather than resource consumption. Distorts cost allocations, especially for products with differing production complexities but similar sales revenue.
Superior Allocation Bases: A Path to Accuracy
Instead of the flawed bases discussed above, organizations should seek allocation bases that accurately reflect the consumption of overhead resources. These include:
1. Activity-Based Costing (ABC): A More Precise Approach
ABC is a sophisticated costing method that identifies the activities that drive overhead costs and assigns these costs to products or services based on their consumption of these activities. It acknowledges that various activities consume overhead resources differently. For instance, setting up a machine is an activity that consumes significant overhead, and ABC allocates the setup costs to products based on the number of setups required for their production.
Advantages of ABC: More accurate allocation, better understanding of cost drivers, improved pricing decisions, better product mix decisions.
2. Number of Setups: Targeting Setup Costs
Directly using the number of production setups as an allocation base captures the costs associated with machine setup, tooling changes, and other preparation activities. This is particularly beneficial in environments with diverse product lines and frequent production changes.
Advantages of using Number of Setups: Accurate allocation of setup-related overhead, improved understanding of setup cost impact, encourages streamlining setup procedures.
3. Number of Orders: Addressing Order-Related Costs
In manufacturing and service industries, processing customer orders involves administrative and logistical costs. Using the number of orders as an allocation base directly reflects these costs, assigning them more accurately to products or services based on the resources consumed in processing individual orders.
Advantages of using Number of Orders: Accurate allocation of order-related overhead, improved understanding of order processing costs, encourages efficient order processing.
4. Number of Machine Hours (with Refinement): Addressing Machine-Related Costs (with caveats)
While machine hours alone can be misleading, combining it with detailed activity analysis can improve accuracy. For instance, differentiating between different types of machine usage (e.g., cutting, grinding, polishing) and allocating overhead based on the hours spent on each activity can offer a more nuanced and accurate approach.
Advantages of using Refined Machine Hours: Improved allocation accuracy in comparison to simple machine hours, better identification of machine-specific cost drivers, more accurate cost allocation.
5. Direct Labor Costs (with careful consideration): Focusing on skilled labor
While simple direct labor hours are often inadequate, focusing on the cost of direct labor can be more relevant in situations where the skill level and associated cost of labor significantly impact overhead. Highly skilled labor might require more supervision, specialized equipment, or training programs, thereby impacting overhead.
Advantages of using Direct Labor Costs (with caveats): Relatively easy to track, can be relevant in situations where labor skill directly influences overhead, but needs to be used with caution.
Choosing the Right Allocation Base: A Strategic Approach
The selection of an appropriate allocation base is a strategic decision. It necessitates a thorough understanding of the organization's cost structure, production processes, and the drivers of overhead. Consider the following factors:
- Nature of Overhead Costs: Identify the specific types of overhead costs and the activities that drive them.
- Production Processes: Analyze the complexity and nature of production processes to identify the resources consumed.
- Product Diversity: Consider the diversity of products or services produced and their consumption of resources.
- Cost-Benefit Analysis: Evaluate the cost and benefits of different allocation methods. While more sophisticated methods like ABC might be more accurate, they can also be more complex and expensive to implement.
Conclusion: Towards Accurate and Effective Cost Allocation
Selecting the right allocation base is paramount for accurate cost accounting and informed decision-making. Many traditional allocation bases, such as direct labor hours and direct material costs, often fail to capture the nuances of modern production environments and the diverse drivers of overhead costs. By shifting toward more sophisticated methods like Activity-Based Costing (ABC) and carefully selecting bases reflecting actual resource consumption (such as number of setups, number of orders, or refined machine hours), organizations can achieve a more accurate and reliable allocation of overhead costs. This leads to improved product costing, better pricing strategies, enhanced profitability, and ultimately, a stronger competitive position. Remember that continuous monitoring and refinement of the allocation base is crucial to ensure its ongoing accuracy and relevance.
Latest Posts
Latest Posts
-
Identification Of Selected Anions Lab Answers
Mar 15, 2025
-
All Of The Following Are Manufacturing Costs Except
Mar 15, 2025
-
Jess Notices A Low Fuel Light
Mar 15, 2025
-
Draw An Outer Electron Box Diagram For A Cation
Mar 15, 2025
-
The Image Depicts What Mechanism Of Evolution
Mar 15, 2025
Related Post
Thank you for visiting our website which covers about Allocation Bases That Do Not Drive Overhead Costs . We hope the information provided has been useful to you. Feel free to contact us if you have any questions or need further assistance. See you next time and don't miss to bookmark.