All Of The Following Are Manufacturing Costs Except
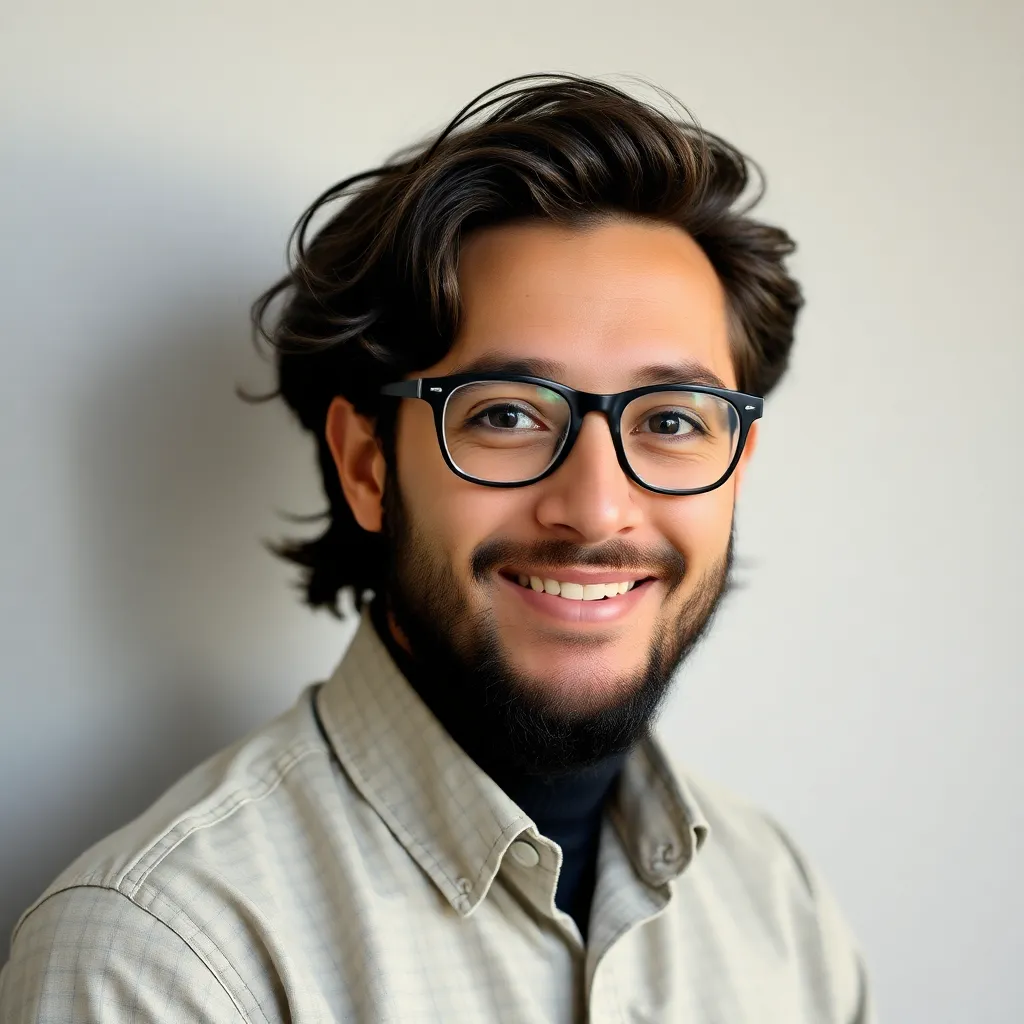
Holbox
Mar 15, 2025 · 6 min read
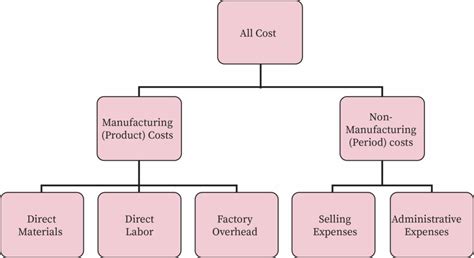
Table of Contents
- All Of The Following Are Manufacturing Costs Except
- Table of Contents
- All of the Following Are Manufacturing Costs Except: A Deep Dive into Cost Classification
- Defining Manufacturing Costs
- 1. Direct Materials
- 2. Direct Labor
- 3. Manufacturing Overhead
- Costs That Are Not Manufacturing Costs
- 1. Selling and Administrative Expenses
- 2. Research and Development (R&D) Costs
- 3. Financing Costs
- 4. General and Administrative Overhead Costs (Beyond Manufacturing)
- 5. Distribution Costs (Beyond Shipping)
- Analyzing Cost Structures for Effective Decision-Making
- Conclusion: The Importance of Accurate Cost Classification
- Latest Posts
- Latest Posts
- Related Post
All of the Following Are Manufacturing Costs Except: A Deep Dive into Cost Classification
Understanding manufacturing costs is crucial for businesses to effectively manage their finances, price their products competitively, and maximize profitability. Accurate cost accounting allows for informed decision-making, from production planning to pricing strategies. But what exactly constitutes a manufacturing cost? This comprehensive guide will explore the various types of manufacturing costs and clarify which expenses don't fall under this category.
Defining Manufacturing Costs
Manufacturing costs represent all expenses directly incurred in the production of goods. These costs are essential to transform raw materials into finished products ready for sale. They are a critical component of the cost of goods sold (COGS) and directly impact a company's profitability. We categorize manufacturing costs into three main groups:
1. Direct Materials
These are the raw materials that become an integral part of the finished product. They are easily traceable to specific units of production and are directly consumed in the manufacturing process. Examples include:
- Raw materials: The basic substances used in manufacturing, like wood for furniture, steel for cars, or cotton for textiles.
- Components: Pre-manufactured parts incorporated into the final product, such as engine parts in a car or microchips in a computer.
- Packaging materials: Materials directly used in packaging the finished goods for sale, though some packaging might be considered indirect if it's for storage rather than final sale.
Key characteristic: Direct materials are physically incorporated into the finished product and their cost is directly attributable to the product.
2. Direct Labor
This encompasses the wages and benefits paid to employees directly involved in the production process. These are the individuals who physically transform raw materials into finished goods. Examples include:
- Assembly line workers: Employees directly assembling products on a production line.
- Machine operators: Workers operating machinery used in the manufacturing process.
- Quality control inspectors: Inspectors directly checking the quality of the finished goods during the production process.
Key characteristic: Direct labor is easily traceable to specific products and is directly involved in the physical transformation of raw materials.
3. Manufacturing Overhead
This is a catch-all category encompassing all indirect costs related to the manufacturing process. These costs are difficult or impossible to trace directly to specific products but are necessary for production to occur. Examples include:
- Factory rent: The cost of renting the factory building where production takes place.
- Utilities: Electricity, water, and gas used in the manufacturing facility.
- Depreciation of factory equipment: The allocation of the cost of factory equipment over its useful life.
- Factory supplies: Indirect materials like lubricants, cleaning supplies, and small tools used in the factory.
- Supervisory salaries: Salaries of supervisors overseeing the production process.
- Insurance on factory equipment: The cost of insurance coverage for factory machinery.
- Property taxes on factory: Taxes levied on the factory building and land.
Key characteristic: Manufacturing overhead costs are indirect, meaning they are not easily traceable to specific products but are essential for the manufacturing process. They are often allocated to products using methods like machine hours or direct labor costs.
Costs That Are Not Manufacturing Costs
While the above categories represent the core components of manufacturing costs, several expenses fall outside this definition. Understanding this distinction is vital for accurate financial reporting and decision-making. Here are some examples:
1. Selling and Administrative Expenses
These costs are associated with selling the finished goods and managing the overall business operations. They are not directly involved in the production process itself. Examples include:
- Sales salaries and commissions: Compensation paid to sales representatives.
- Advertising and marketing costs: Expenses incurred promoting the product.
- Shipping and delivery costs: Costs associated with transporting finished goods to customers (Note: This can sometimes be considered part of COGS depending on accounting practices).
- Administrative salaries: Salaries of administrative staff, such as accountants and office managers.
- Rent for office space: Cost of renting office space separate from the factory.
- Legal and professional fees: Costs associated with legal and professional services.
Key characteristic: These expenses support the business but are not directly involved in the production of goods. They are usually expensed in the period they are incurred.
2. Research and Development (R&D) Costs
These costs are incurred in the development of new products or processes. While crucial for long-term growth, they are not part of the manufacturing cost of existing products. Examples include:
- Salaries of research scientists: Compensation paid to scientists working on new product development.
- Laboratory equipment and supplies: Costs associated with research and development activities.
- Patent and trademark fees: Costs associated with protecting intellectual property.
Key characteristic: R&D costs are future-oriented and are capitalized or expensed depending on accounting standards, but they are not directly attributable to the cost of producing existing products.
3. Financing Costs
These are expenses related to borrowing money to finance the business. They are not directly related to the production process. Examples include:
- Interest expense: Interest paid on loans and other debt.
- Bank charges: Fees charged by banks for services.
Key characteristic: Financing costs are related to the business's capital structure and are not directly involved in the production of goods.
4. General and Administrative Overhead Costs (Beyond Manufacturing)
This category includes indirect costs related to the general operations of the business, but are beyond the manufacturing facility itself. These are distinct from manufacturing overhead and are expensed separately. Examples include:
- Executive salaries: Salaries of top management executives.
- Legal and consulting fees (general business): Fees related to business operations outside of production.
- Insurance (general business): Insurance coverage for the general business operations.
5. Distribution Costs (Beyond Shipping)
While shipping can be part of COGS, broader distribution costs are generally not considered manufacturing costs. These are the expenses associated with getting the product to the consumer after it leaves the manufacturing facility.
- Warehouse storage: Costs of storing finished goods before distribution.
- Sales representative travel: Expenses related to sales representative travel, separate from delivery of goods.
Analyzing Cost Structures for Effective Decision-Making
Understanding the difference between manufacturing costs and other expenses is critical for various business decisions:
- Pricing: Accurate cost accounting is fundamental to setting profitable prices. Knowing the exact manufacturing cost allows for accurate pricing calculations, ensuring sufficient profit margins.
- Inventory Valuation: Correct classification of costs impacts inventory valuation, which affects the balance sheet and income statement.
- Performance Evaluation: Tracking manufacturing costs helps identify areas for efficiency improvements and cost reduction strategies.
- Process Improvement: Analyzing cost data helps pinpoint bottlenecks and inefficiencies in the production process, facilitating process optimization.
- Strategic Planning: A clear understanding of cost structures is crucial for informed strategic decisions, such as capacity expansion or product diversification.
Conclusion: The Importance of Accurate Cost Classification
Accurately classifying costs as manufacturing or non-manufacturing is vital for sound financial management and informed strategic decisions. While the core components of manufacturing costs – direct materials, direct labor, and manufacturing overhead – are relatively straightforward, the boundary between these and other expenses can sometimes be nuanced. This article has provided a comprehensive overview of manufacturing costs, highlighted the expenses that do not qualify, and emphasized the importance of rigorous cost accounting practices. By clearly distinguishing between these categories, businesses can gain valuable insights into their operational efficiency, improve profitability, and make well-informed choices that drive sustainable growth.
Latest Posts
Latest Posts
-
The Range Of Which Function Includes 4
Mar 16, 2025
-
Po Box 98878 Las Vegas Nv
Mar 16, 2025
-
Goods In Transit Are Included In A Purchasers Inventory
Mar 16, 2025
-
A Rise In The General Level Of Prices
Mar 16, 2025
-
The Empirical Method Of Study Is Based On
Mar 16, 2025
Related Post
Thank you for visiting our website which covers about All Of The Following Are Manufacturing Costs Except . We hope the information provided has been useful to you. Feel free to contact us if you have any questions or need further assistance. See you next time and don't miss to bookmark.