A Successful Quality Strategy Begins With
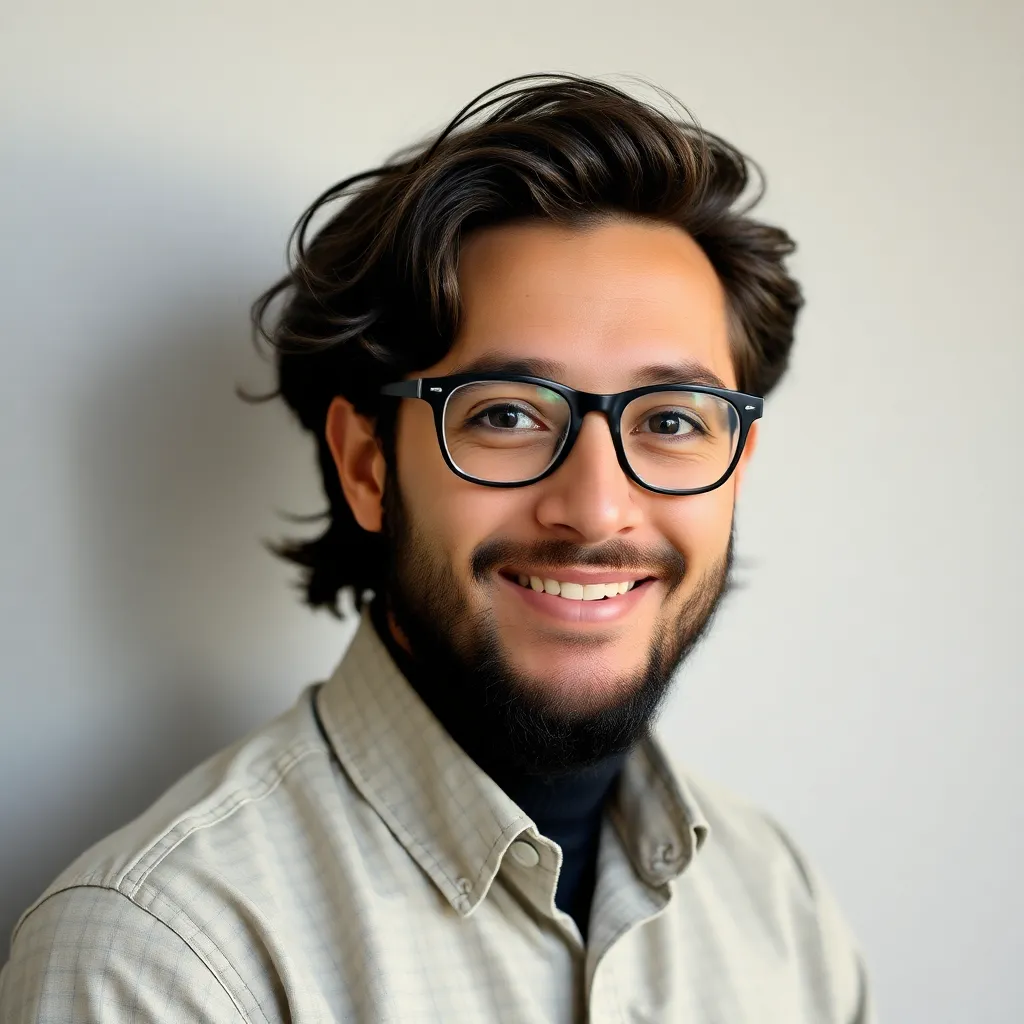
Holbox
Mar 20, 2025 · 7 min read
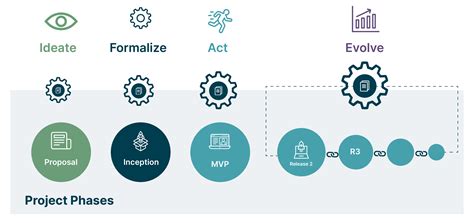
Table of Contents
A Successful Quality Strategy Begins With: A Comprehensive Guide
A successful quality strategy isn't a one-size-fits-all solution; it's a journey, a continuous process of improvement, adaptation, and innovation. It's not just about meeting minimum standards; it's about exceeding expectations and creating a culture of excellence that permeates every aspect of your organization. This comprehensive guide will delve into the fundamental building blocks of a robust quality strategy, exploring where it begins and how to nurture its growth.
1. A Clear Understanding of "Quality"
Before embarking on any quality strategy, you must define what "quality" means within the context of your specific business. This goes beyond simply meeting specifications; it involves understanding your customer's needs and expectations.
Defining Quality from the Customer's Perspective
- Voice of the Customer (VOC): Actively solicit feedback through surveys, focus groups, reviews, and social media monitoring. Understanding what truly matters to your customers is paramount. Are they focused on price, performance, reliability, aesthetics, or customer service?
- Customer Segmentation: Divide your customer base into distinct groups based on their needs and preferences. A quality strategy tailored to one segment might not be effective for another. This allows for targeted quality initiatives.
- Competitive Analysis: Analyze your competitors' offerings and identify areas where you can excel. Understanding the market landscape and your competitors' strengths and weaknesses informs your quality goals.
Internal Definition of Quality
Beyond customer expectations, you need a clear internal definition of quality.
- Quality Metrics: Establish measurable KPIs (Key Performance Indicators) to track progress and identify areas needing improvement. This could include defect rates, customer satisfaction scores, cycle times, and process efficiency.
- Quality Standards: Align your processes with relevant industry standards and best practices (e.g., ISO 9001, Six Sigma). This provides a framework and benchmark for continuous improvement.
- Employee Involvement: Quality is not just the responsibility of a dedicated quality department; it should be ingrained in the culture of every employee. Empowering employees to identify and address quality issues is essential.
2. Leadership Commitment and Cultural Transformation
A successful quality strategy requires unwavering commitment from leadership at all levels. It's not just a directive; it needs to be a core value embedded within the organizational culture.
Leading by Example
- Visible Leadership: Leaders should actively participate in quality initiatives, attend improvement meetings, and champion the cause. This demonstrates their commitment and encourages employee participation.
- Resource Allocation: Allocate sufficient resources (budget, time, personnel) to support quality improvement efforts. This shows that quality is a priority, not an afterthought.
- Accountability: Establish clear accountability for quality outcomes. Individuals and teams should be responsible for meeting quality targets and addressing issues.
Fostering a Culture of Continuous Improvement
- Open Communication: Encourage open communication and feedback at all levels. Employees should feel comfortable reporting defects, suggesting improvements, and participating in problem-solving.
- Training and Development: Invest in training and development to enhance employee skills and knowledge related to quality. This includes training on quality management systems, problem-solving techniques, and customer service.
- Employee Empowerment: Empower employees to take ownership of quality issues and implement improvements. This fosters a sense of responsibility and pride in their work.
- Reward and Recognition: Recognize and reward employees who contribute to quality improvement. This can be through formal awards, bonuses, or simply public acknowledgment.
3. Process Improvement and Optimization
Once you have a clear understanding of quality and a culture that supports it, you can focus on optimizing your processes.
Process Mapping and Analysis
- Identify Key Processes: Map out all critical processes involved in delivering your products or services. This provides a visual representation of the workflow and helps identify bottlenecks and areas for improvement.
- Analyze Process Efficiency: Evaluate the efficiency and effectiveness of each process. Identify areas where waste, defects, or delays occur. Tools like Value Stream Mapping can be particularly helpful.
- Root Cause Analysis: Use techniques like the 5 Whys or Fishbone diagrams to identify the root causes of quality problems. Addressing the root causes, rather than just the symptoms, is critical for sustainable improvement.
Implementing Lean and Six Sigma Principles
- Lean Principles: Implement lean principles to eliminate waste (muda) in all its forms – waste of time, materials, motion, etc. Lean methodologies focus on streamlining processes and optimizing efficiency.
- Six Sigma: Utilize Six Sigma methodologies to reduce variation and improve process capability. Six Sigma aims to achieve near-perfect quality by minimizing defects and improving consistency.
- Kaizen Events: Conduct regular Kaizen events (continuous improvement workshops) to identify and implement small, incremental improvements. These events involve employees from different departments working together to solve problems and improve processes.
4. Data-Driven Decision Making and Measurement
A successful quality strategy relies heavily on data-driven decision-making. Tracking and analyzing key metrics provides insights into your performance and areas for improvement.
Key Performance Indicators (KPIs)
- Defect Rates: Track the number of defects per unit or per process. This helps identify areas with high defect rates that require attention.
- Customer Satisfaction: Measure customer satisfaction through surveys, reviews, and feedback. High customer satisfaction indicates a strong quality strategy.
- Cycle Time: Monitor the time it takes to complete a process. Reducing cycle time improves efficiency and customer satisfaction.
- Process Yield: Measure the percentage of units that pass inspection without defects. Improving process yield reduces waste and improves efficiency.
Data Analysis and Reporting
- Data Visualization: Use dashboards and charts to visualize key metrics and make data easily understandable.
- Regular Reporting: Generate regular reports on quality performance to track progress and identify trends.
- Statistical Process Control (SPC): Utilize SPC techniques to monitor process variation and identify potential problems before they escalate.
5. Supplier Management and Partnerships
The quality of your products or services is often dependent on the quality of your suppliers. Establishing strong relationships with reliable suppliers is crucial.
Supplier Selection and Qualification
- Supplier Audits: Conduct regular audits of your suppliers to ensure they meet your quality standards.
- Performance Evaluation: Evaluate supplier performance based on key metrics, such as on-time delivery, quality of materials, and responsiveness.
- Continuous Improvement Collaboration: Collaborate with your suppliers to identify and implement improvements in their processes.
Collaborative Relationships
- Open Communication: Maintain open communication channels with your suppliers to address issues promptly.
- Long-Term Partnerships: Foster long-term relationships with your suppliers to build trust and mutual understanding.
- Shared Goals: Align your goals with your suppliers' goals to ensure everyone is working towards the same objectives.
6. Continuous Improvement and Adaptation
A successful quality strategy is not a static entity; it requires continuous improvement and adaptation to changing circumstances.
Regularly Review and Update Your Strategy
- Market Changes: Adapt your quality strategy to reflect changes in market demand and customer expectations.
- Technological Advancements: Embrace new technologies and tools to improve quality and efficiency.
- Internal Changes: Adjust your quality strategy to accommodate changes in your organization's structure, processes, or personnel.
Embrace Innovation and Experimentation
- New Technologies: Explore new technologies that can improve quality, such as AI-powered quality control systems or advanced automation.
- New Methods: Test new methods and techniques for process improvement and problem-solving.
- Learn from Mistakes: Analyze failures and use them as learning opportunities to improve your processes.
7. Measuring the Success of Your Quality Strategy
Finally, it's crucial to regularly measure the success of your quality strategy. This involves tracking key metrics and comparing your performance against your goals.
Measuring ROI
- Reduced Defects: Quantify the reduction in defects and the cost savings associated with improved quality.
- Increased Efficiency: Measure improvements in efficiency and productivity.
- Improved Customer Satisfaction: Track improvements in customer satisfaction scores.
- Enhanced Brand Reputation: Assess the impact of improved quality on your brand reputation and market share.
A successful quality strategy is a holistic endeavor, requiring a commitment to excellence across all facets of the organization. It’s a continuous cycle of improvement, adaptation, and innovation, powered by strong leadership, empowered employees, and a data-driven approach. By focusing on these key elements, businesses can build a robust quality strategy that delivers exceptional results and sustainable success.
Latest Posts
Latest Posts
-
Differentiate Y Sec I Tan I
Mar 21, 2025
-
Human Anatomy And Physiology Lab Manual
Mar 21, 2025
-
Sophia Operates Her Own Accounting Practice
Mar 21, 2025
-
How Many Different Kinds Of 13c Peaks Will Be Seen
Mar 21, 2025
-
Which Of The Following Accurately Describes A Supply Chain Map
Mar 21, 2025
Related Post
Thank you for visiting our website which covers about A Successful Quality Strategy Begins With . We hope the information provided has been useful to you. Feel free to contact us if you have any questions or need further assistance. See you next time and don't miss to bookmark.