A Factor That Causes Overhead Costs Is Called A
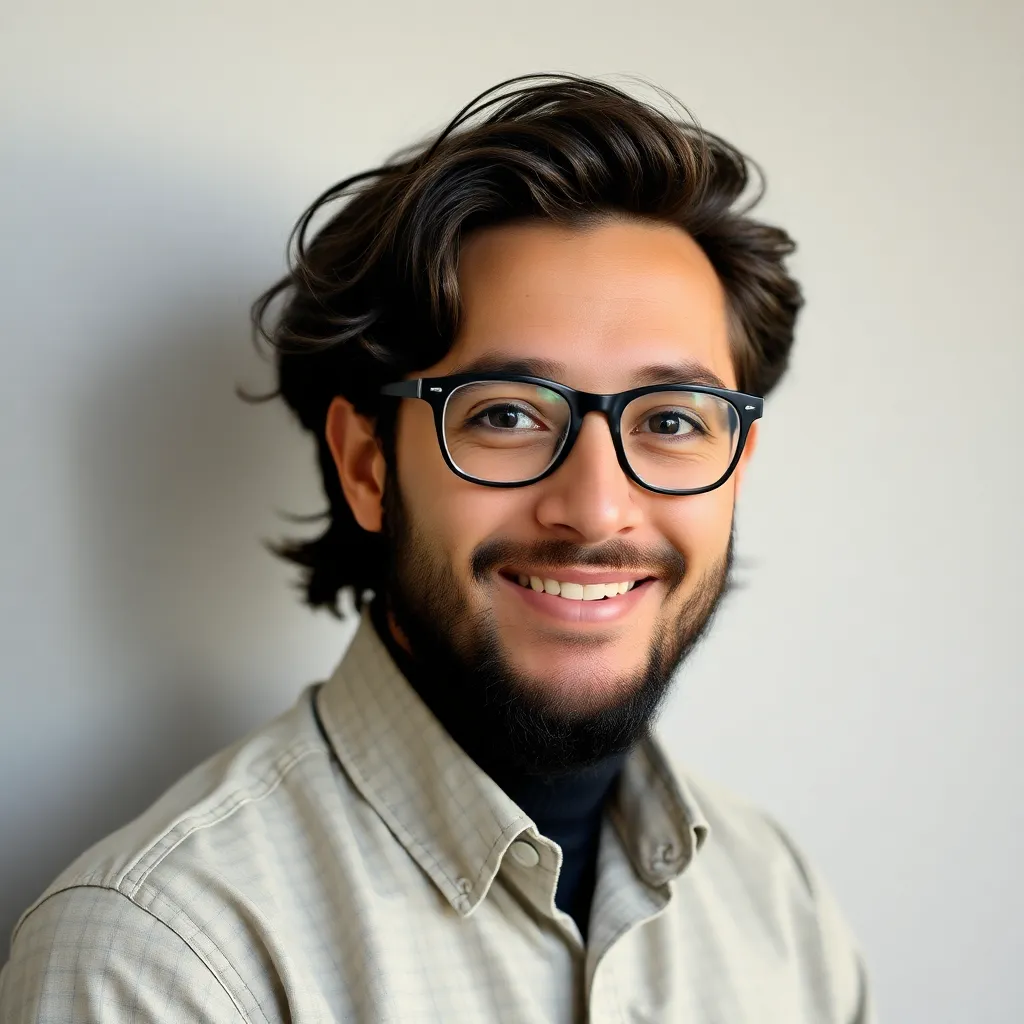
Holbox
Mar 20, 2025 · 6 min read
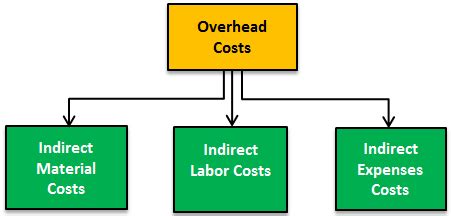
Table of Contents
- A Factor That Causes Overhead Costs Is Called A
- Table of Contents
- A Factor That Causes Overhead Costs is Called a Cost Driver
- What are Overhead Costs?
- Defining Cost Drivers: The Root Cause of Overhead
- 1. Volume-Based Cost Drivers
- 2. Activity-Based Cost Drivers
- 3. Complexity-Based Cost Drivers
- 4. Capacity-Based Cost Drivers
- Identifying Cost Drivers: A Practical Approach
- Managing and Controlling Overhead Costs
- The Impact of Cost Drivers on Profitability and Strategic Decisions
- Conclusion: Mastering Cost Drivers for Business Success
- Latest Posts
- Latest Posts
- Related Post
A Factor That Causes Overhead Costs is Called a Cost Driver
Understanding overhead costs is crucial for any business, regardless of size or industry. These costs, unlike direct costs tied to specific products or services, are indirect expenses necessary for the overall operation of the business. But what causes these overhead costs? The answer lies in understanding cost drivers. A factor that causes overhead costs is called a cost driver. This comprehensive guide will delve deep into the concept of cost drivers, exploring their various types, how to identify them, and their impact on profitability and strategic decision-making.
What are Overhead Costs?
Before diving into cost drivers, let's solidify our understanding of overhead costs themselves. Overhead costs are expenses that aren't directly tied to producing goods or services. They're the necessary expenses incurred to keep the business running. Examples include:
- Rent: The cost of leasing or owning the space where your business operates.
- Utilities: Electricity, water, gas, and internet bills.
- Salaries of Support Staff: Pay for administrative staff, human resources, accounting, and other support functions.
- Insurance: Liability, property, and other insurance premiums.
- Depreciation: The reduction in value of assets over time.
- Maintenance and Repairs: Costs associated with keeping equipment and facilities in good working order.
- Marketing and Advertising: Expenses related to promoting your products or services.
These costs are essential for business operations but are difficult to directly allocate to individual products or services. Understanding what drives these costs is key to managing them effectively.
Defining Cost Drivers: The Root Cause of Overhead
A cost driver is any factor that influences the level of overhead costs incurred. These are the underlying reasons why your overhead costs are what they are. Identifying cost drivers is the first step toward effectively managing and controlling overhead expenses. They can be broadly categorized into several types:
1. Volume-Based Cost Drivers
These are cost drivers directly related to the volume of activity or production within the business. The higher the volume, the higher the overhead cost. Examples include:
- Number of units produced: Higher production volume often means increased costs associated with electricity consumption, machine maintenance, and direct labor for support functions.
- Number of orders processed: More orders generally lead to higher administrative costs, shipping expenses, and customer service expenses.
- Machine hours: The more a machine is used, the higher the costs of maintenance, repairs, and depreciation.
- Direct labor hours (for support staff): The more hours support staff work, the higher their associated salaries and benefits costs.
2. Activity-Based Cost Drivers
These drivers are related to specific activities within the business, irrespective of production volume. Even with low production, these activities still incur costs. Examples include:
- Number of customer service calls: Each call requires time and resources, driving up overhead costs related to customer service staff and systems.
- Number of design changes: Frequent design alterations can lead to increased costs in engineering, prototyping, and documentation.
- Number of inspections: Quality control and inspections increase costs through labor and equipment expenses.
- Number of purchase orders: Processing numerous purchase orders adds to administrative overhead.
3. Complexity-Based Cost Drivers
These drivers are related to the complexity of the business's operations, processes, or products. Higher complexity often equates to higher overhead costs. Examples include:
- Product complexity: Manufacturing complex products requires more specialized equipment, skilled labor, and detailed instructions, thereby increasing overhead.
- Process complexity: Intricate production processes may involve more steps, specialized personnel, and sophisticated control systems, raising overhead expenses.
- Number of product lines: Managing a diverse range of products requires more inventory management, marketing resources, and potentially specialized equipment.
- Technological complexity: Adopting advanced technologies can lead to higher initial investment costs, training expenses, and ongoing maintenance costs.
4. Capacity-Based Cost Drivers
These drivers relate to the capacity or scale of the business's operations. Having a larger capacity, even if not fully utilized, can increase fixed overhead costs. Examples include:
- Size of facilities: Larger facilities result in higher rent, utilities, and maintenance costs.
- Number of employees: A larger workforce necessitates increased payroll costs, benefits expenses, and administrative support.
- Equipment capacity: Purchasing larger or more sophisticated equipment leads to higher initial investment, depreciation, and potentially higher maintenance costs.
Identifying Cost Drivers: A Practical Approach
Identifying the most significant cost drivers for your business is a critical step in controlling overhead. Here's a systematic approach:
-
Analyze your overhead costs: Begin by reviewing your past financial statements, breaking down overhead costs into specific categories. Identify the largest expense categories.
-
Gather data: Collect data related to various activities and factors within your business. This could include production volume, number of orders, machine hours, number of customer service calls, etc.
-
Correlation analysis: Examine the correlation between the identified overhead cost categories and the various data points. Look for strong positive correlations. A strong positive correlation suggests a significant cost driver.
-
Activity-based costing (ABC): ABC is a more sophisticated approach that assigns overhead costs based on the specific activities that consume resources. It's particularly useful for identifying activity-based cost drivers.
-
Consult with experts: Seek assistance from accountants, management consultants, or industry specialists to gain a deeper understanding of potential cost drivers within your industry.
Managing and Controlling Overhead Costs
Once you've identified your major cost drivers, you can implement strategies to effectively manage and control overhead costs:
- Improve efficiency: Streamline processes, automate tasks, and optimize resource utilization to reduce costs driven by volume or activity.
- Negotiate better deals: Negotiate favorable contracts with suppliers, landlords, and service providers to reduce costs associated with rent, utilities, and other expenses.
- Invest in technology: Implement technologies that enhance efficiency, automate processes, and reduce labor costs.
- Outsource non-core functions: Outsource certain functions to specialized providers to potentially reduce costs and improve efficiency.
- Right-size your operations: Optimize the size of your facilities and workforce to align with your actual needs and capacity.
- Regular cost analysis: Continuously monitor your overhead costs and re-evaluate your cost drivers to identify areas for improvement.
The Impact of Cost Drivers on Profitability and Strategic Decisions
Understanding cost drivers has a profound impact on your business's profitability and strategic decision-making:
- Pricing strategies: Accurate identification of cost drivers helps in setting appropriate prices that cover both direct and indirect costs.
- Product costing: Knowing your cost drivers enables accurate product costing, helping you make informed decisions about which products to produce and at what price.
- Strategic planning: Understanding cost drivers helps in forecasting future costs and making informed strategic decisions related to expansion, investment, and resource allocation.
- Performance evaluation: Tracking and analyzing cost drivers allows you to monitor the effectiveness of cost-control measures and assess the performance of various business units or departments.
- Benchmarking: Comparing your cost drivers with those of competitors helps identify areas for improvement and gain a competitive advantage.
Conclusion: Mastering Cost Drivers for Business Success
In conclusion, a factor that causes overhead costs is called a cost driver. Identifying and understanding these cost drivers is not merely an accounting exercise; it's a critical aspect of strategic management. By systematically identifying and analyzing your cost drivers, you gain valuable insights into your business operations, enabling you to make informed decisions about pricing, resource allocation, and overall business strategy. Proactive management of cost drivers is crucial for enhancing profitability, improving efficiency, and achieving long-term business success. Continuously monitoring and analyzing your cost drivers is an ongoing process requiring vigilance and adaptation to changing market conditions and business needs. This ongoing effort will ultimately contribute to a healthier financial bottom line and a more sustainable business model.
Latest Posts
Latest Posts
-
Determine Where To Dispose Of Each Type Of Waste
Mar 21, 2025
-
Rna Polymerase Is Guided By The
Mar 21, 2025
-
Pensions Are Referred To As Defined Benefits Plans Because
Mar 21, 2025
-
Drag The Appropriate Labels To Their Respective Targets Facial Nerve
Mar 21, 2025
-
How Are An Interval And A Segment Different
Mar 21, 2025
Related Post
Thank you for visiting our website which covers about A Factor That Causes Overhead Costs Is Called A . We hope the information provided has been useful to you. Feel free to contact us if you have any questions or need further assistance. See you next time and don't miss to bookmark.