When Is Whmis Training Required Check All That Apply
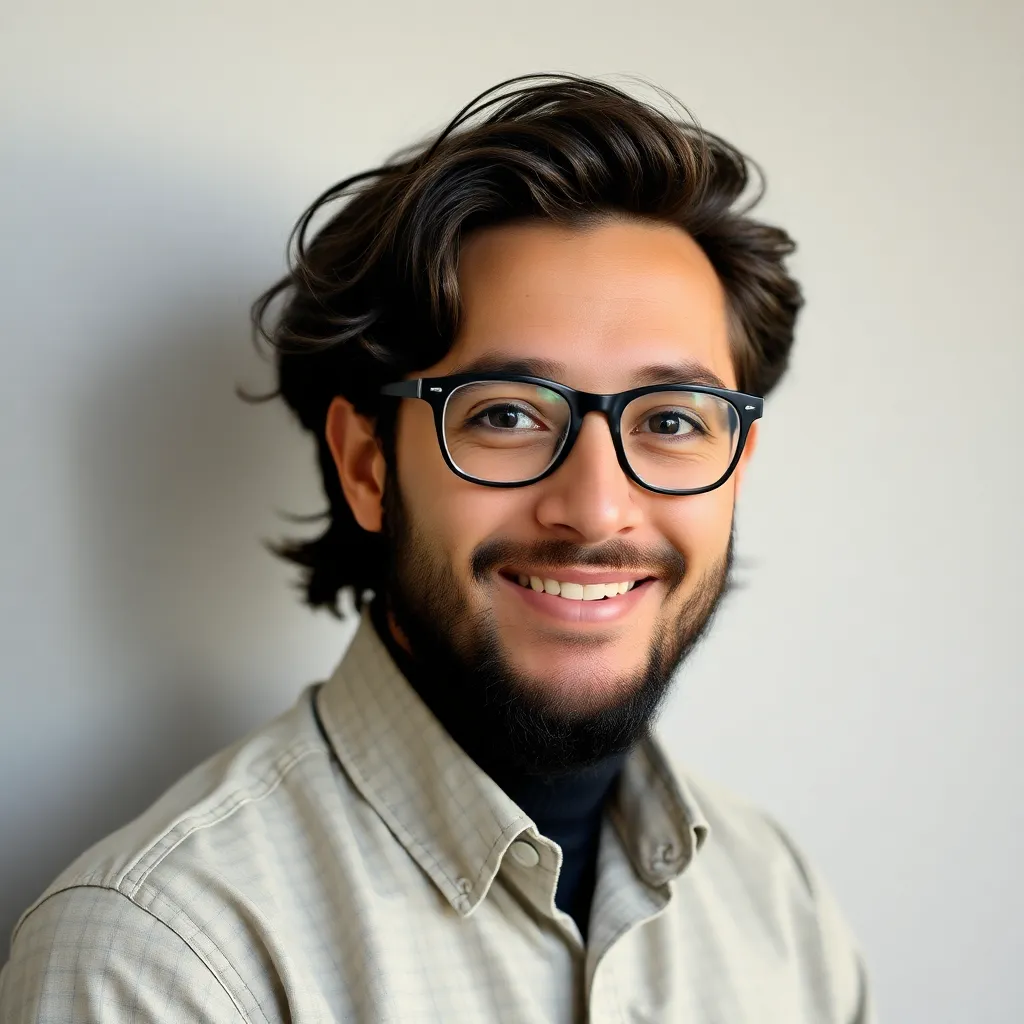
Holbox
Mar 10, 2025 · 6 min read
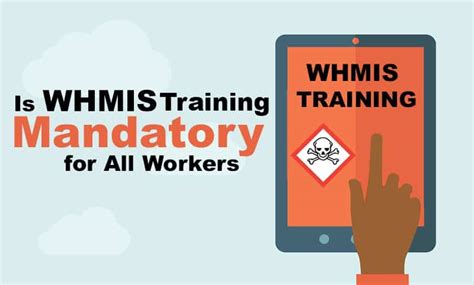
Table of Contents
When is WHMIS Training Required? Check All That Apply
Workplace safety is paramount, and the Workplace Hazardous Materials Information System (WHMIS) plays a crucial role in ensuring a safe working environment. Understanding when WHMIS training is required is vital for employers and employees alike. This comprehensive guide will clarify the situations mandating WHMIS training, leaving no room for ambiguity. We'll delve into various scenarios, offering a clear picture of who needs training and why. By the end, you'll be able to confidently determine when WHMIS training is absolutely necessary for your workplace.
Understanding WHMIS: The Foundation of Workplace Safety
Before we delve into the specifics of when WHMIS training is required, let's establish a solid understanding of WHMIS itself. WHMIS is a Canadian system designed to provide workers with the information they need to handle hazardous materials safely. It involves three key elements:
-
Hazard Communication: Manufacturers, importers, and suppliers are responsible for providing information about hazardous materials through labels, safety data sheets (SDS), and worker education programs.
-
Worker Education: This is where WHMIS training comes in. Workers must receive adequate training to understand the hazards associated with the materials they handle and how to work safely with them.
-
Workplace Controls: Employers must implement control measures to minimize risks associated with hazardous materials, including proper storage, handling procedures, and personal protective equipment (PPE).
Who Needs WHMIS Training? Check All That Apply
The simple answer is: anyone who may come into contact with hazardous materials in the workplace. However, this broad statement requires further clarification. Let's examine specific situations where WHMIS training is not just recommended but legally mandated:
1. All Employees Handling Hazardous Materials: The Most Common Scenario
This is the most straightforward scenario. If an employee handles, uses, stores, or even simply comes into contact with hazardous materials as part of their job duties, they require WHMIS training. This applies regardless of their role or seniority within the company. Examples include:
-
Manufacturing Workers: Those working directly with chemicals, solvents, or other hazardous materials in a production setting.
-
Laboratory Technicians: Scientists and technicians handling various chemicals and reagents in a laboratory environment.
-
Maintenance Personnel: Workers involved in cleaning, repairing, or maintaining equipment that uses or contains hazardous materials.
-
Shipping and Receiving Staff: Employees who handle incoming and outgoing shipments of hazardous materials.
-
Office Workers: Even those in office environments might handle cleaning supplies, glues, or other materials that require WHMIS training if their exposure could be considered significant.
Crucially: The level of training may vary depending on the specific hazards involved. Someone working with mildly hazardous cleaning supplies will require less intensive training than someone working with highly toxic chemicals.
2. New Employees: Induction and Ongoing Training
All new employees who will be handling hazardous materials, even those with prior experience, must receive WHMIS training as part of their workplace induction. This ensures they are familiar with the specific procedures and protocols in place at their new workplace.
Furthermore, WHMIS training isn't a one-time event. Ongoing training and refresher courses are essential to keep employees up-to-date on best practices, changes in regulations, and new hazards that may arise. Regular updates are crucial for maintaining a safe working environment.
3. Employees with Changing Roles: Adapting to New Hazards
If an employee’s job responsibilities change and they are now exposed to new hazardous materials, they require updated WHMIS training relevant to those specific materials. For example, an office worker transferred to a warehouse handling solvents would need supplementary WHMIS training focused on solvent safety.
4. Contractors and Subcontractors: Extending WHMIS Protection
Contractors and subcontractors working on a site where hazardous materials are present must also receive appropriate WHMIS training. The employer is responsible for ensuring that these workers are adequately trained before they begin work. This often involves providing specific training materials or verifying that the contractor's employees have already received relevant training elsewhere. Thorough documentation is key here.
5. Supervisors and Managers: Leading by Example
Supervisors and managers have an extra layer of responsibility. They not only need to understand WHMIS themselves but also need to be able to supervise and ensure compliance from their teams. Their training should encompass supervisory aspects, including enforcing safety regulations, investigating incidents, and conducting regular safety audits.
6. Any Employee Reporting Exposure to Hazardous Materials
Any employee who has experienced exposure to hazardous materials, regardless of whether they received prior training, should receive refresher training immediately. This helps to reinforce safety procedures and address any concerns or anxieties resulting from the incident. The focus will be on the specific hazard and the preventive measures to ensure future incidents are avoided.
What WHMIS Training Should Include
Effective WHMIS training goes beyond simply presenting the information. It needs to be interactive, engaging, and tailored to the specific hazards present in the workplace. Key components of comprehensive WHMIS training include:
-
Understanding WHMIS Legislation: Employees need to know the legal requirements and their responsibilities under WHMIS.
-
Identifying Hazardous Materials: Training should cover how to identify hazardous materials through labels, SDS, and other means.
-
Interpreting Labels and SDS: Employees must learn how to read and understand the information provided on labels and Safety Data Sheets.
-
Safe Handling Procedures: This should detail specific safe procedures for handling, storing, using, and disposing of hazardous materials.
-
Emergency Procedures: Employees need to know what to do in case of spills, leaks, or other emergencies involving hazardous materials.
-
Personal Protective Equipment (PPE): Training should include proper selection, use, and maintenance of appropriate PPE.
-
Workplace Controls: Employees should understand the various engineering, administrative, and personal protective controls in place in their workplace.
-
Reporting Procedures: Employees must know how to report incidents, near misses, and any concerns regarding hazardous materials.
Consequences of Inadequate WHMIS Training
Failing to provide adequate WHMIS training can have serious consequences, including:
-
Workplace Injuries and Illnesses: The most serious consequence is the potential for injury or illness to employees due to improper handling of hazardous materials.
-
Fines and Penalties: Employers can face significant fines and penalties for non-compliance with WHMIS regulations.
-
Loss of Productivity: Workplace incidents can lead to lost time, increased healthcare costs, and reduced productivity.
-
Damage to Reputation: A poor safety record can damage a company's reputation and make it difficult to attract and retain employees.
-
Legal Liability: Employers may face legal liability if a workplace accident occurs due to inadequate safety training.
Conclusion: Prioritizing WHMIS Training for a Safer Workplace
WHMIS training is not optional; it's a legal obligation and a moral imperative. By ensuring that all employees who may come into contact with hazardous materials receive adequate training, employers demonstrate their commitment to workplace safety. A robust WHMIS training program is an investment in the health, safety, and well-being of employees, leading to a more productive and responsible work environment. The cost of neglecting WHMIS training far outweighs the cost of implementing a comprehensive program. Remember, a safe workplace is a productive workplace. Don’t compromise on safety – prioritize WHMIS training.
Latest Posts
Latest Posts
-
A Single Nucleotide Deletion During Dna Replication
Mar 10, 2025
-
The Goal Of The Human Rights Code Is To
Mar 10, 2025
-
What Does The Law Assume A Reasonable And Prudent
Mar 10, 2025
-
Which Situation Poses A Risk Of High Centering
Mar 10, 2025
-
Predict The Major Product Of The Following Reaction
Mar 10, 2025
Related Post
Thank you for visiting our website which covers about When Is Whmis Training Required Check All That Apply . We hope the information provided has been useful to you. Feel free to contact us if you have any questions or need further assistance. See you next time and don't miss to bookmark.