The Formula To Determine The Materials To Be Purchased Is
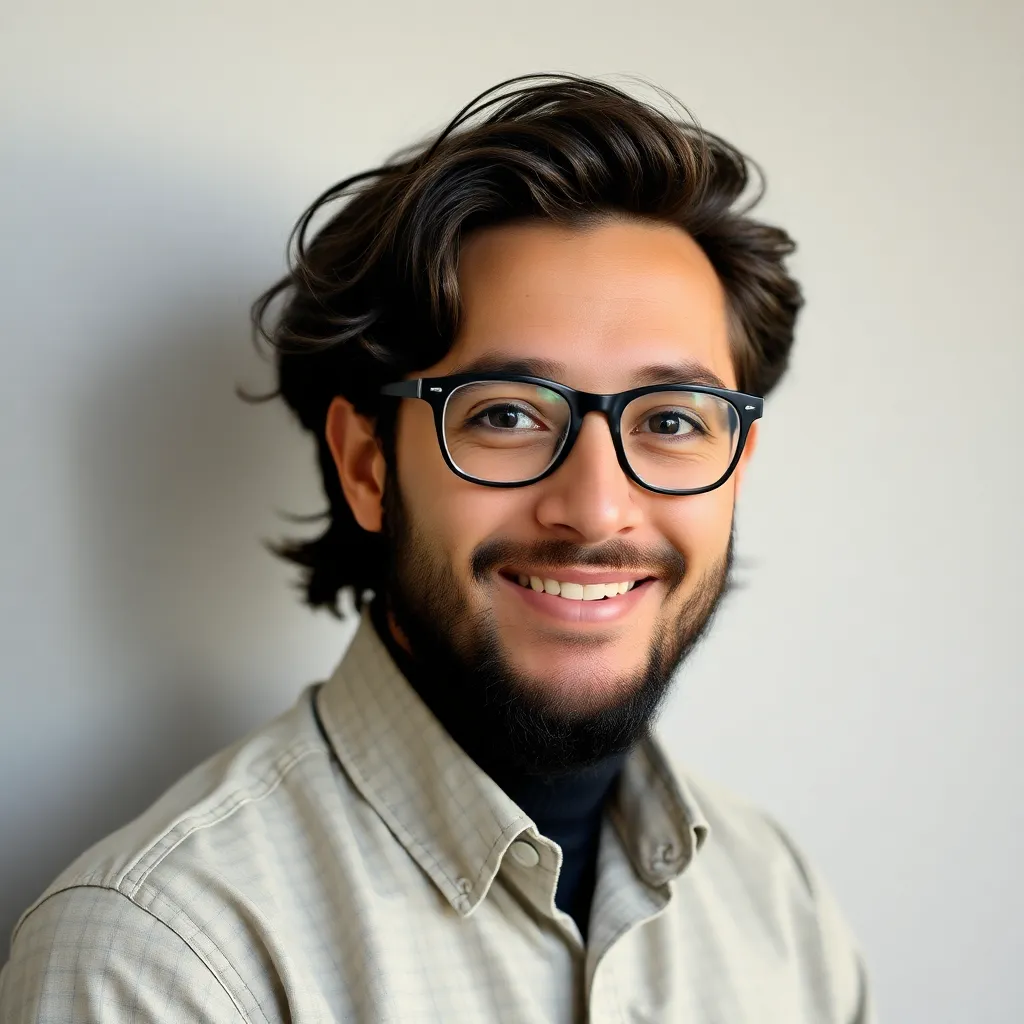
Holbox
Mar 15, 2025 · 7 min read
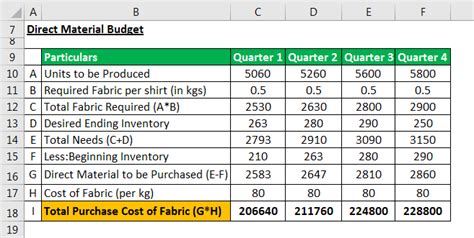
Table of Contents
The Formula to Determine Materials to Purchase: A Comprehensive Guide
Determining the right quantity of materials to purchase is crucial for any business, impacting profitability, operational efficiency, and overall success. Getting it wrong can lead to costly overstocking, tying up capital and risking obsolescence, or frustrating production delays due to shortages. This comprehensive guide will delve into the formula, factors, and strategies for accurately determining materials to purchase, ensuring your business maintains optimal inventory levels.
Understanding the Core Formula: Material Requirements Planning (MRP)
While there isn't one single, universally applicable "formula," the most robust method for calculating material needs is Material Requirements Planning (MRP). MRP is a production planning and inventory control system that uses a bill of materials (BOM), inventory data, and a master production schedule (MPS) to calculate the exact quantity and timing of material purchases.
The basic MRP formula isn't a simple equation, but rather a series of calculations and considerations:
1. Master Production Schedule (MPS): This is your starting point. The MPS outlines the planned production of finished goods over a specific period, specifying the quantity and timing of each product.
2. Bill of Materials (BOM): The BOM is a detailed list of all the raw materials, components, sub-assemblies, and parts needed to manufacture a single unit of a finished product. It breaks down the product's structure, specifying the quantity of each item required.
3. Inventory Records: This encompasses your current stock levels for each material. Accurate inventory tracking is paramount for MRP's effectiveness. It should include:
- On-hand quantity: The amount of material currently in stock.
- Scheduled receipts: Materials already ordered and expected to arrive.
- Lead time: The time it takes to receive an order from the supplier once it's placed.
The Calculation Process:
MRP systematically works backward from the MPS. For each finished product in the MPS, it uses the BOM to determine the raw materials required. It then subtracts the on-hand quantity and scheduled receipts from the total material needs to determine the net requirements. Finally, it accounts for lead times to determine when to place purchase orders to ensure timely material availability.
Beyond the Basics: Factors Influencing Material Purchase Decisions
While MRP provides a robust framework, several other factors significantly influence the quantity of materials a business should purchase:
1. Demand Forecasting:
Accurate demand forecasting is the bedrock of effective material planning. Several techniques exist, each with its own strengths and weaknesses:
- Time series analysis: Uses historical sales data to predict future demand. Methods include moving averages, exponential smoothing, and ARIMA models.
- Causal forecasting: Considers external factors that influence demand, such as economic conditions, seasonality, and marketing campaigns.
- Qualitative forecasting: Relies on expert opinions and market research to estimate future demand, useful when historical data is limited or unreliable.
2. Lead Time Variability:
Lead times are rarely constant. Supplier delays, transportation issues, or unexpected disruptions can significantly impact the timing of material delivery. Buffer stock is often necessary to mitigate the risk of production delays caused by lead time variability.
3. Safety Stock:
Safety stock is the extra inventory held to protect against unforeseen events, such as unexpected demand spikes, supplier disruptions, or quality issues. The optimal safety stock level depends on several factors:
- Demand variability: Higher demand variability requires higher safety stock levels.
- Lead time variability: Longer and more unpredictable lead times also necessitate higher safety stock.
- Service level: The desired probability of meeting customer demand. A higher service level requires more safety stock.
4. Economic Order Quantity (EOQ):
EOQ is a model that determines the optimal order quantity to minimize total inventory costs. It balances the cost of ordering (order costs) with the cost of holding inventory (carrying costs). The EOQ formula is:
EOQ = √[(2DS)/H]
Where:
- D = Annual demand
- S = Ordering cost per order
- H = Holding cost per unit per year
The EOQ model assumes constant demand and lead times, which is often unrealistic. However, it provides a useful starting point for determining order quantities.
5. Supplier Relationships:
Strong relationships with reliable suppliers are critical. Reliable suppliers offer predictable lead times, consistent quality, and potentially favorable pricing and payment terms. This can significantly reduce the need for excessive safety stock and improve overall planning efficiency.
6. Storage Capacity:
Physical limitations on storage space constrain the amount of inventory a business can hold. Businesses must balance the need for safety stock and efficient production with available warehouse capacity.
7. Material Obsolescence:
The risk of material obsolescence, especially for technology-related products, must be considered. Businesses need to carefully balance purchasing enough material to meet demand with the risk that the material may become outdated or unusable before it's consumed.
8. Price Volatility:
Fluctuations in raw material prices can significantly impact profitability. Businesses may consider hedging strategies, such as forward contracts or options, to mitigate the risk of price increases. Alternatively, they may adjust their purchasing strategies to take advantage of lower prices when available.
Advanced Techniques and Considerations
1. Just-in-Time (JIT) Inventory Management:
JIT is a system that aims to minimize inventory levels by receiving materials only when they are needed for production. It requires close collaboration with suppliers and highly efficient production processes. While potentially highly cost-effective, JIT systems are vulnerable to disruptions in the supply chain.
2. Vendor Managed Inventory (VMI):
VMI is a system where the supplier manages the inventory levels of its products at the customer's facility. The supplier monitors inventory levels, forecasts demand, and places orders to maintain optimal stock levels. This approach necessitates a high degree of trust and transparency between the supplier and the customer.
3. Enterprise Resource Planning (ERP) Systems:
ERP systems integrate various business functions, including production planning, inventory management, and supply chain management. These systems provide a comprehensive view of the business's operations and can significantly enhance the accuracy and efficiency of material planning.
Implementing the Formula: A Step-by-Step Approach
-
Accurate Forecasting: Begin by developing a robust demand forecast. Consider using a combination of quantitative and qualitative methods to achieve the most accurate prediction possible.
-
Detailed BOM: Ensure your BOM is meticulously accurate and up-to-date. Any inaccuracies in the BOM will propagate through the entire planning process.
-
Inventory Tracking: Implement a robust inventory management system to track on-hand quantities, scheduled receipts, and material movements accurately. Consider using barcode or RFID technology for efficient tracking.
-
Lead Time Analysis: Carefully analyze your historical lead times to understand their variability. Include buffer time to account for potential delays.
-
Safety Stock Calculation: Use appropriate safety stock calculation methods based on demand variability, lead time variability, and desired service levels.
-
MRP Software: Utilize MRP software to automate the calculation process. This significantly reduces the time and effort required for manual calculations and minimizes the risk of errors.
-
Regular Review and Adjustment: Regularly review your material plans and make necessary adjustments based on actual demand, lead times, and other relevant factors. The goal is to continuously refine your planning process to improve its accuracy and effectiveness.
-
Supplier Collaboration: Maintain strong relationships with your suppliers. Open communication and collaboration can significantly improve the accuracy and efficiency of your material planning.
Conclusion: Optimizing Your Material Procurement
Determining the right amount of materials to purchase is a complex but crucial aspect of business management. While there’s no single magical "formula," combining the principles of MRP with sound forecasting, inventory management practices, and consideration of relevant factors will significantly improve your procurement process. By implementing the steps outlined above, and continuously refining your approach based on experience and data, you can optimize your material purchases, reduce costs, minimize waste, and ensure the timely availability of materials to meet production needs and customer demand. Investing in accurate forecasting and efficient inventory management systems represents a worthwhile investment in overall business success.
Latest Posts
Latest Posts
-
Which Of The Following Best Describes Shareholders Equity
Mar 15, 2025
-
The Following Two Develop To Form Shoot And Roots
Mar 15, 2025
-
The Mean Of The Sample Means
Mar 15, 2025
-
Choose The Best Description Of The Cell Cytoskeleton
Mar 15, 2025
-
Identification Of Selected Anions Lab Answers
Mar 15, 2025
Related Post
Thank you for visiting our website which covers about The Formula To Determine The Materials To Be Purchased Is . We hope the information provided has been useful to you. Feel free to contact us if you have any questions or need further assistance. See you next time and don't miss to bookmark.