The Amount Of Inspection Needed Depends On __________ And __________.
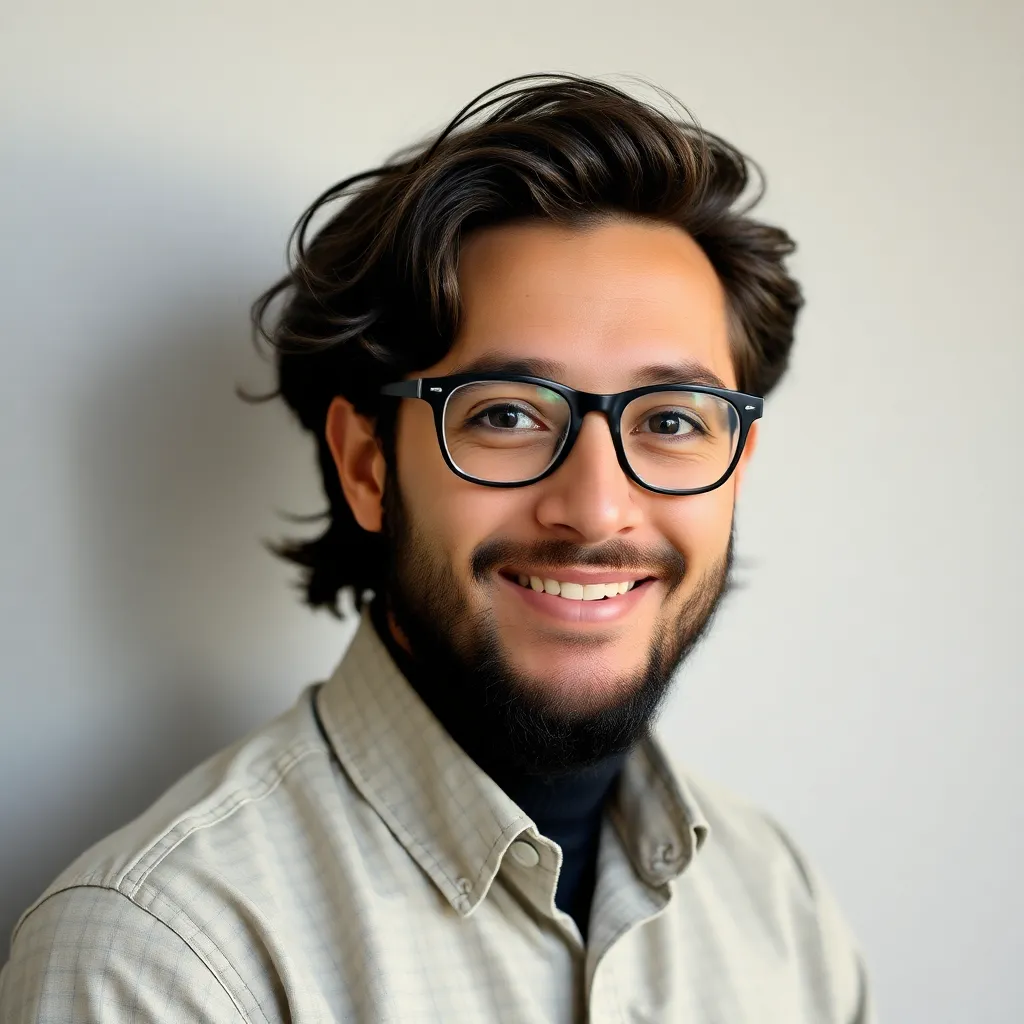
Holbox
Mar 20, 2025 · 6 min read
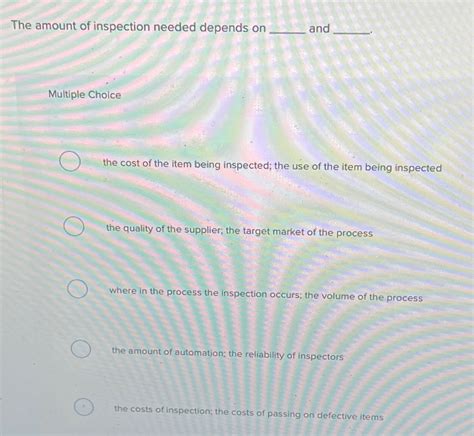
Table of Contents
The Amount of Inspection Needed Depends on Risk and Context
The amount of inspection required for any given process, product, or system isn't a fixed number. It's a dynamic variable that shifts based on a careful assessment of two crucial factors: risk and context. This isn't a simple equation, but a nuanced consideration that demands a thorough understanding of potential failure points and the surrounding circumstances. Let's delve deeper into how these factors dictate inspection intensity.
Understanding the Risk Factor: A Multifaceted Assessment
Risk, in this context, isn't just the probability of something going wrong. It's a complex calculation encompassing the likelihood of failure and the severity of the consequences should that failure occur. A high-risk scenario demands far more rigorous inspection than a low-risk one. Several elements contribute to the overall risk assessment:
1. Potential for Harm:
This is perhaps the most critical component. What are the potential consequences of a failure? Are we talking about minor inconvenience, significant financial loss, environmental damage, or even loss of life? The higher the potential for harm, the more intensive the inspection process needs to be.
- Example: Inspecting a child's toy for sharp edges carries a lower risk than inspecting the structural integrity of a bridge. A minor defect in the toy might result in a small scratch, while a similar defect in the bridge could lead to catastrophic collapse.
2. Probability of Failure:
This element assesses how likely a failure is to occur. Past performance data, design flaws, material weaknesses, and environmental factors all play a crucial role here. Statistical analysis and historical records can help quantify this probability.
- Example: A new design with untested components will have a higher probability of failure than a well-established design with a proven track record. Consequently, the former would need much more rigorous inspection.
3. Cost of Failure:
Beyond the immediate harm, consider the financial, legal, and reputational costs associated with failure. These costs can be immense, extending far beyond the initial repair or replacement.
- Example: A faulty component in a medical device might necessitate costly recalls, legal battles, and damage to the manufacturer's reputation. These factors justify a higher level of inspection during the manufacturing process.
4. Criticality of the System:
Some systems are more critical than others. A minor defect in a non-critical system may be tolerable, but the same defect in a critical system could have catastrophic consequences. This needs to be carefully assessed.
- Example: The inspection of a safety-critical system like an aircraft's flight control system requires an exponentially higher level of scrutiny compared to a less critical system like an in-flight entertainment system.
Understanding the Context Factor: Beyond Risk Alone
While risk is paramount, the context in which the inspection takes place also heavily influences the intensity and scope of the process. Context encompasses several crucial elements:
1. Regulatory Requirements:
Government regulations, industry standards, and legal mandates play a vital role in determining the required level of inspection. These regulations often specify minimum inspection standards based on the nature of the product or process. Ignoring these requirements can lead to legal ramifications and penalties.
- Example: Food processing plants are subject to stringent inspections to ensure food safety, exceeding the inspection requirements for a furniture manufacturer.
2. Environmental Conditions:
The environment in which the product or process operates can influence the need for inspection. Harsh environmental conditions might increase the likelihood of deterioration or failure, necessitating more frequent inspections.
- Example: Equipment operating in extreme temperatures or corrosive environments requires more frequent and thorough inspections compared to equipment operating in more benign conditions.
3. Technology Used:
The technology employed in the inspection process itself matters. Advanced inspection technologies, such as non-destructive testing (NDT) methods, allow for more thorough and efficient inspections, potentially reducing the need for manual inspections.
- Example: Using X-ray inspection for detecting internal flaws in castings is far more efficient and effective than relying solely on visual inspection.
4. Available Resources:
The resources available – including time, budget, personnel, and equipment – also affect the scope and intensity of inspection. Limited resources might necessitate prioritizing inspections based on risk levels, focusing on the most critical areas first.
- Example: A small business might need to prioritize inspections based on available resources, focusing on high-risk areas and potentially sacrificing the frequency of inspections in lower-risk areas.
5. Past Performance:
A product or process with a history of consistent quality and reliability might require less frequent inspections compared to one with a history of failures or defects. This historical data provides valuable insights into potential failure points.
- Example: A manufacturing process with a long track record of zero defects might require less frequent inspections than a process with a history of recurring defects.
6. Customer Expectations:
Customer expectations also influence the level of inspection. Customers purchasing high-value or safety-critical products often expect a higher level of quality assurance, leading to more rigorous inspection protocols.
- Example: The aerospace industry has extremely high standards for quality and safety, resulting in an extremely rigorous inspection process.
Optimizing Inspection Strategies: A Balanced Approach
The goal isn't simply to maximize inspection but to optimize it. Over-inspection can be wasteful and costly, while under-inspection can lead to dangerous consequences. A balanced approach is crucial, and several strategies can contribute to achieving this:
-
Risk-Based Inspection: Prioritize inspections based on the identified risk levels, focusing more resources on high-risk areas.
-
Statistical Process Control (SPC): Employ statistical methods to monitor the process and detect anomalies early on, minimizing the need for extensive inspections.
-
Preventive Maintenance: Implement a robust preventive maintenance program to reduce the likelihood of failures and minimize the need for reactive inspections.
-
Non-Destructive Testing (NDT): Utilize advanced NDT methods to thoroughly inspect components and systems without causing damage.
-
Continuous Improvement: Regularly review and refine the inspection process based on data analysis and feedback to improve efficiency and effectiveness.
Conclusion: A Dynamic and Iterative Process
The amount of inspection needed is not a static quantity; it's a dynamic variable continuously adjusted based on the evolving risk profile and context. By carefully considering the interplay of risk and context, implementing appropriate inspection strategies, and embracing continuous improvement, organizations can optimize their inspection processes, ensuring product safety, quality, and efficiency while avoiding unnecessary costs and delays. The ultimate aim is to achieve a balance – a level of inspection that effectively mitigates risk without being overly burdensome or inefficient. This requires ongoing vigilance, data-driven decision making, and a commitment to continuous improvement. Only then can organizations confidently navigate the complexities of ensuring product and process integrity.
Latest Posts
Latest Posts
-
Closing Entries Are Journalized And Posted
Mar 20, 2025
-
Match Each Device To A Category
Mar 20, 2025
-
Organic Intellectual Disability Is Caused By
Mar 20, 2025
-
Which Of The Following Is Not A Source Document
Mar 20, 2025
-
The Crossover Point Is That Production Quantity Where
Mar 20, 2025
Related Post
Thank you for visiting our website which covers about The Amount Of Inspection Needed Depends On __________ And __________. . We hope the information provided has been useful to you. Feel free to contact us if you have any questions or need further assistance. See you next time and don't miss to bookmark.