Production Order Processing Is An Example Of A
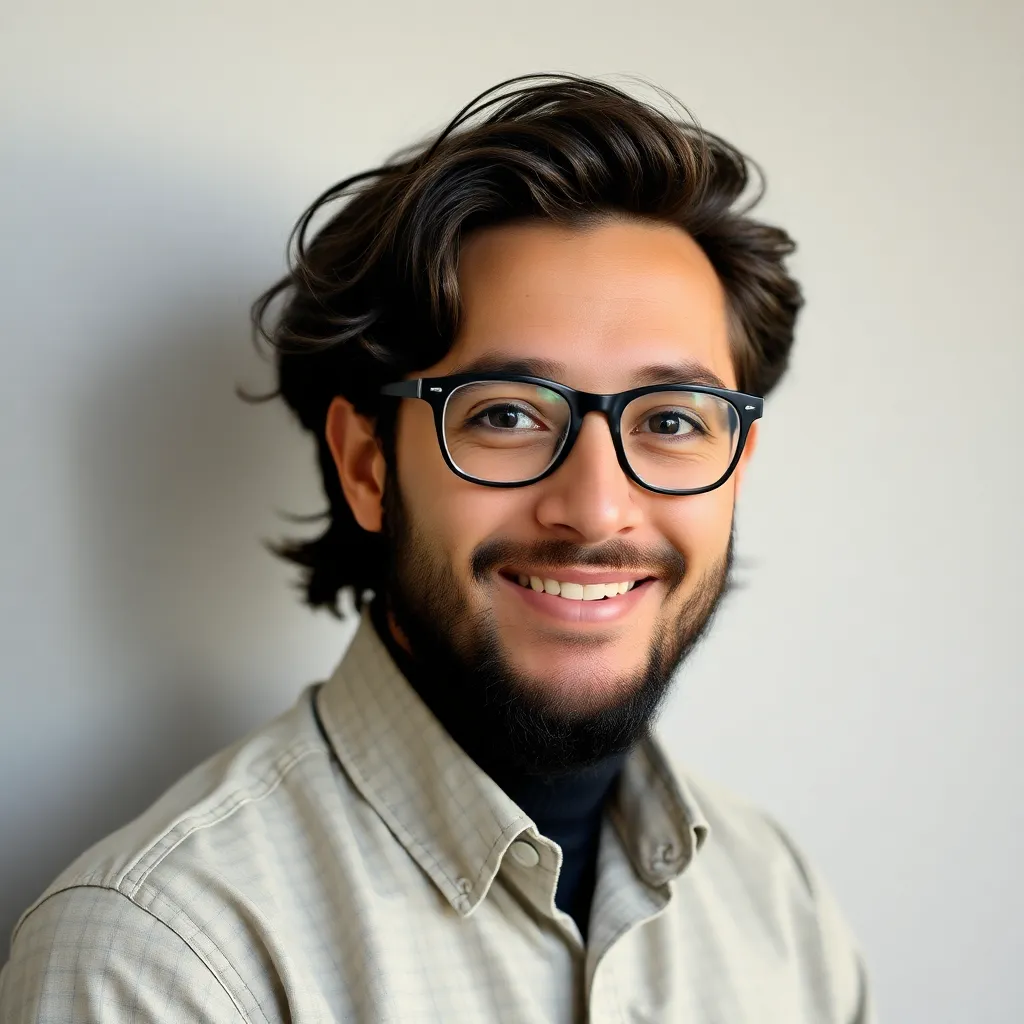
Holbox
Mar 21, 2025 · 6 min read
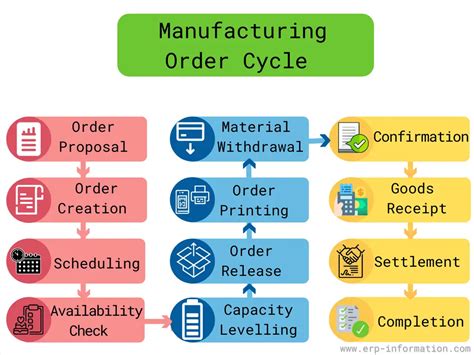
Table of Contents
- Production Order Processing Is An Example Of A
- Table of Contents
- Production Order Processing is an Example of a Transaction Processing System (TPS)
- Understanding Transaction Processing Systems (TPS)
- How Production Order Processing Fits the TPS Model
- 1. Order Creation & Data Capture: The Genesis of a Transaction
- 2. Material Requirements Planning (MRP): Efficient Resource Allocation
- 3. Production Scheduling and Execution: Orchestrating the Process
- 4. Quality Control and Inspection: Ensuring Standards are Met
- 5. Completion and Reporting: The Final Transaction
- Production Order Processing as a Sub-System within a Larger ERP System
- Benefits of a Robust Production Order Processing System
- Challenges in Production Order Processing
- Conclusion: The Vital Role of TPS in Modern Manufacturing
- Latest Posts
- Latest Posts
- Related Post
Production Order Processing is an Example of a Transaction Processing System (TPS)
Production order processing is a prime example of a Transaction Processing System (TPS). A TPS is a type of information system designed to handle the multitude of routine, day-to-day business transactions that are vital to a company's operation. These systems focus on efficiency, accuracy, and reliability in recording and processing these transactions, which form the bedrock of an organization's data. Let's delve deeper into why production order processing perfectly embodies the characteristics of a TPS and explore its intricacies.
Understanding Transaction Processing Systems (TPS)
Before we dissect production order processing, let's establish a firm understanding of what constitutes a TPS. At its core, a TPS is characterized by its focus on structured transactions. These are discrete, well-defined events that involve data modification, like creating a new order, updating an inventory count, or processing a payment. TPS systems are built to handle a high volume of these transactions concurrently, often involving multiple users and databases.
Key features of a TPS include:
- Data Capture: Accurately and efficiently capturing data related to each transaction.
- Data Processing: Processing the captured data to update relevant databases and produce reports.
- Data Storage: Securely storing the transaction data for future retrieval and analysis.
- Data Output: Providing users with timely and relevant information regarding the transactions.
- Real-time processing: Many TPS offer real-time or near real-time processing to ensure immediate feedback and efficient workflow.
- Reliability and Accuracy: TPS are designed with mechanisms to ensure data integrity and prevent errors.
How Production Order Processing Fits the TPS Model
Production order processing perfectly exemplifies a TPS because it involves the systematic recording and processing of numerous structured transactions throughout the manufacturing process. Let's explore the various stages:
1. Order Creation & Data Capture: The Genesis of a Transaction
The process begins with the creation of a production order. This involves capturing crucial data points, including:
- Product specifications: Detailed description of the product to be manufactured, including materials, dimensions, and quality standards.
- Quantity: Number of units to be produced.
- Due date: Target completion date for the order.
- Production resources: Allocation of machinery, equipment, and personnel required.
- Materials requirements: Identification and quantity of raw materials needed.
This data capture phase is crucial for a TPS, ensuring accurate and complete information enters the system. Any inaccuracies here can cascade through the entire manufacturing process, leading to delays, errors, and ultimately, financial losses.
2. Material Requirements Planning (MRP): Efficient Resource Allocation
Once the order is created, a Material Requirements Planning (MRP) system, often integrated with the TPS, determines the required materials and their availability. This involves:
- Checking inventory: Verifying the current stock levels of necessary raw materials.
- Generating purchase orders: If materials are lacking, the system automatically generates purchase orders to replenish inventory.
- Scheduling: Optimizing the timing of material delivery to ensure timely production.
This stage showcases the data processing capabilities of a TPS. It leverages stored data (inventory levels) to make informed decisions, improving resource allocation and minimizing production downtime.
3. Production Scheduling and Execution: Orchestrating the Process
The TPS then facilitates production scheduling, assigning the order to relevant production lines, machines, and personnel. This often involves:
- Work order generation: Creating detailed work instructions for each production stage.
- Machine scheduling: Assigning machines and equipment based on availability and capabilities.
- Labor assignment: Allocating personnel with the necessary skills to perform specific tasks.
- Real-time monitoring: Tracking production progress and identifying potential bottlenecks.
This stage highlights the real-time processing capabilities of a TPS. Monitoring progress and adjusting schedules allows for timely intervention and prevents production delays.
4. Quality Control and Inspection: Ensuring Standards are Met
During production, quality control checks are performed at various stages. These inspections generate data regarding:
- Product defects: Recording instances of non-conformance to quality standards.
- Rework requirements: Identifying units requiring correction or modification.
- Scrap generation: Tracking discarded materials due to defects.
This information is fed back into the TPS, providing valuable insights for process improvement. This feedback loop is vital for continuous enhancement and maintaining product quality.
5. Completion and Reporting: The Final Transaction
Once the production order is completed, the TPS records the final data points:
- Completion date: Recording the actual date of order completion.
- Total units produced: Number of units successfully manufactured.
- Material consumption: Actual quantity of materials used.
- Labor hours: Total time spent on the production.
- Production costs: Calculating the overall cost of production.
This final stage generates comprehensive reports that serve various purposes, including cost accounting, inventory management, and performance analysis. This reporting capability is a core function of a TPS, providing management with critical information for decision-making.
Production Order Processing as a Sub-System within a Larger ERP System
Often, a production order processing system doesn't exist in isolation. It's frequently integrated into a larger Enterprise Resource Planning (ERP) system. An ERP system is a comprehensive suite of integrated applications that manage and integrate all facets of a business. Within this larger system, the production order processing module plays a vital role.
The integration with other ERP modules strengthens the TPS's capabilities:
- Integration with Sales & Marketing: Production orders are initiated based on sales forecasts and customer orders, creating a seamless flow of information.
- Integration with Inventory Management: Real-time inventory updates ensure accurate material allocation and timely procurement.
- Integration with Finance: Production cost data is automatically integrated into the financial reporting system, facilitating accurate accounting and budgeting.
- Integration with Human Resources: Employee performance and labor costs are tracked, allowing for improved resource allocation and payroll processing.
This integration significantly enhances the efficiency and effectiveness of the entire enterprise. It eliminates data silos, minimizes errors, and fosters a more streamlined workflow.
Benefits of a Robust Production Order Processing System
Implementing a robust and well-integrated production order processing system offers numerous benefits:
- Improved Efficiency: Streamlined processes reduce lead times and increase output.
- Reduced Costs: Optimized resource allocation minimizes waste and lowers production costs.
- Enhanced Quality Control: Rigorous tracking and inspection improve product quality.
- Better Inventory Management: Accurate inventory levels reduce stockouts and excess inventory.
- Improved Decision Making: Data-driven insights facilitate better planning and strategic decisions.
- Increased Transparency: Real-time tracking provides better visibility into production processes.
- Improved Customer Satisfaction: Timely delivery and high-quality products enhance customer satisfaction.
Challenges in Production Order Processing
Despite the numerous advantages, implementing and maintaining a successful production order processing system presents several challenges:
- Data Integration: Integrating the TPS with other systems can be complex and time-consuming.
- System Complexity: Managing a large and complex TPS can be difficult.
- Data Security: Protecting sensitive production data requires robust security measures.
- User Training: Effective use requires adequate training for all users.
- Maintenance & Updates: Regular maintenance and updates are crucial for optimal performance.
Conclusion: The Vital Role of TPS in Modern Manufacturing
Production order processing is undeniably a quintessential example of a transaction processing system. Its role in efficient manufacturing is paramount, contributing to streamlined operations, improved quality control, and better decision-making. By understanding the intricacies of TPS and its integration within a broader ERP system, businesses can optimize their production processes, leading to increased profitability and a stronger competitive edge in the modern manufacturing landscape. The focus on real-time data, accuracy, and integration with other business functions makes the production order processing system a cornerstone of any successful manufacturing enterprise. The continuous evolution of technology ensures that TPS will remain a vital component of efficient and effective production for years to come.
Latest Posts
Latest Posts
-
Histamine Serotonin And Bradykinin Are All
Mar 24, 2025
-
30 40 50 40 45 50
Mar 24, 2025
-
A Trial Balance Will Not Balance If
Mar 24, 2025
-
Which Best Describes The Terrorist Planning Cycle
Mar 24, 2025
-
Once A Firm Has Invested In Continues Proess Improvemnt
Mar 24, 2025
Related Post
Thank you for visiting our website which covers about Production Order Processing Is An Example Of A . We hope the information provided has been useful to you. Feel free to contact us if you have any questions or need further assistance. See you next time and don't miss to bookmark.