Non-value-added Activities In A Process Design Can Be Eliminated By
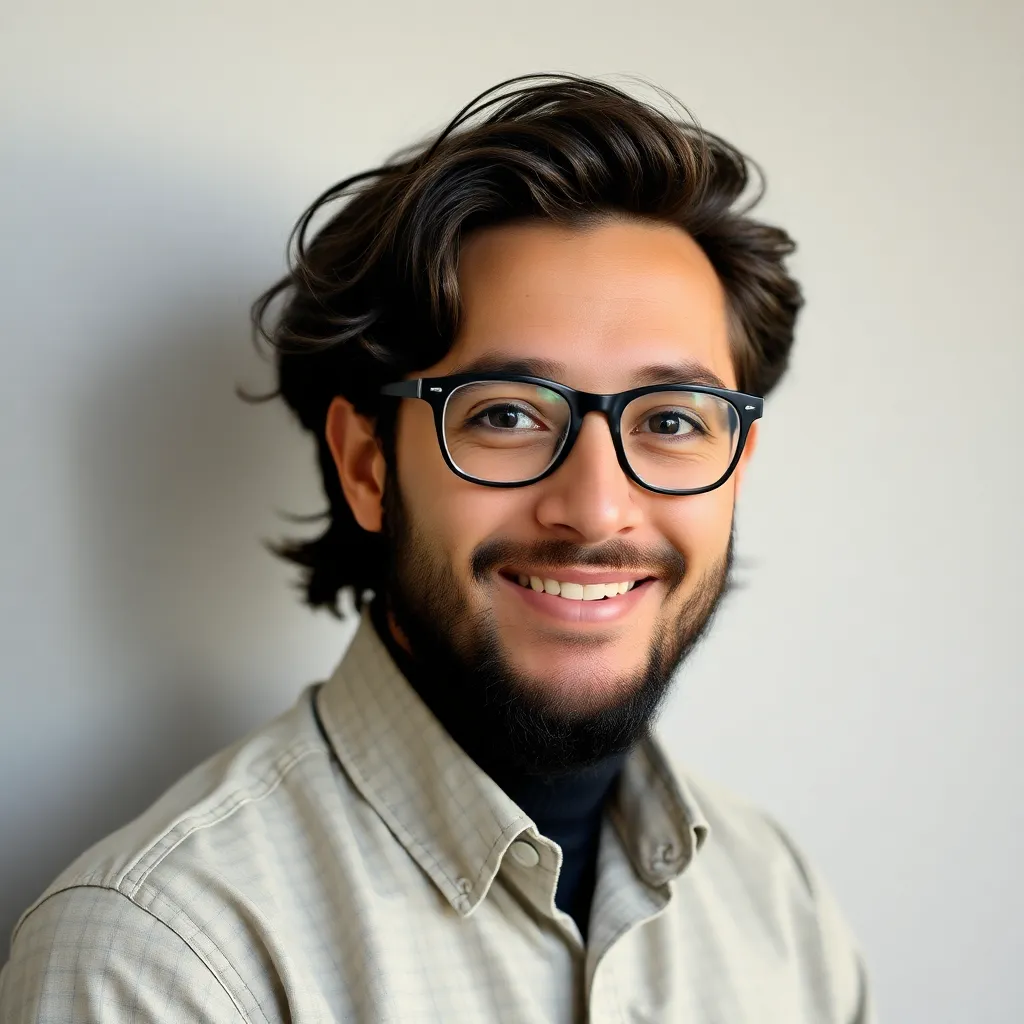
Holbox
Mar 23, 2025 · 6 min read

Table of Contents
- Non-value-added Activities In A Process Design Can Be Eliminated By
- Table of Contents
- Eliminating Non-Value-Added Activities in Process Design: A Comprehensive Guide
- Understanding Value-Added and Non-Value-Added Activities
- Identifying Non-Value-Added Activities: A Systematic Approach
- 1. Value Stream Mapping (VSM):
- 2. Process Flowcharting:
- 3. Time and Motion Studies:
- 4. Customer Surveys and Feedback:
- Eliminating Non-Value-Added Activities: Practical Strategies
- 1. Automation:
- 2. Simplification:
- 3. Kaizen Events:
- 4. Technology Integration:
- 5. Lean Principles:
- 6. Employee Empowerment:
- 7. Process Re-engineering:
- Measuring the Success of Non-Value-Added Activity Elimination
- Continuous Improvement: The Ongoing Journey
- Latest Posts
- Latest Posts
- Related Post
Eliminating Non-Value-Added Activities in Process Design: A Comprehensive Guide
Improving efficiency and profitability hinges on streamlining processes and eliminating non-value-added activities. These activities, while often seemingly necessary, consume resources without directly contributing to the customer's perceived value. Identifying and removing them is crucial for achieving operational excellence. This article delves deep into various methods for eliminating non-value-added activities, providing practical strategies and examples for process improvement.
Understanding Value-Added and Non-Value-Added Activities
Before diving into elimination strategies, it's essential to clearly define what constitutes value-added and non-value-added activities. This distinction forms the foundation of any successful process improvement initiative.
Value-Added Activities: These directly transform the product or service, bringing it closer to meeting customer needs. They are activities the customer is willing to pay for. Key characteristics include:
- Customer Perception: The activity directly adds value from the customer's perspective.
- Transformation: The activity physically or functionally changes the product or service.
- Necessity: The activity is essential for delivering the product or service.
Examples of Value-Added Activities:
- Manufacturing: Assembling components, machining parts, painting a finished product.
- Service: Providing customer consultations, performing medical procedures, developing software features.
- Retail: Selling a product, providing customer service, processing a transaction.
Non-Value-Added Activities: These consume resources (time, money, materials) without adding direct value to the product or service from the customer's viewpoint. They are often seen as necessary evils within a process, but they represent areas for significant improvement.
Characteristics of Non-Value-Added Activities:
- No Customer Value: The activity doesn't improve the product or service in the eyes of the customer.
- No Transformation: The activity doesn't change the physical or functional characteristics.
- Potential for Elimination: The activity could be eliminated or significantly reduced without impacting the final product or service.
Examples of Non-Value-Added Activities:
- Manufacturing: Unnecessary inspections, excessive movement of materials, long waiting times between processes.
- Service: Excessive paperwork, redundant approvals, lengthy customer hold times.
- Retail: Long checkout lines, searching for misplaced items, dealing with returns due to poor quality.
Identifying Non-Value-Added Activities: A Systematic Approach
Identifying non-value-added activities requires a systematic and objective approach. Here are some effective methods:
1. Value Stream Mapping (VSM):
VSM is a powerful visualization technique that maps out the entire flow of materials and information within a process. It helps identify bottlenecks, waste, and non-value-added activities. By visually representing the process, teams can easily pinpoint areas for improvement. Key steps include:
- Process Definition: Clearly define the beginning and end points of the process.
- Data Collection: Gather data on processing times, inventory levels, and transportation times.
- Mapping: Create a visual representation of the process, including all activities.
- Analysis: Identify non-value-added activities and bottlenecks.
- Improvement Plan: Develop a plan to eliminate or reduce non-value-added activities.
2. Process Flowcharting:
Similar to VSM, process flowcharting graphically represents the steps involved in a process. This allows for a clear identification of each step's contribution to value. By examining each step, teams can determine which are necessary and which can be eliminated. Flowcharting facilitates a granular level of examination, enhancing the accuracy of non-value-added activity identification.
3. Time and Motion Studies:
These studies involve carefully observing and measuring the time spent on each step within a process. By analyzing the data, teams can identify activities that consume excessive time without adding value. This approach is particularly useful for identifying inefficiencies in manual processes.
4. Customer Surveys and Feedback:
Gathering feedback directly from customers can highlight activities that are perceived as non-value-added. Customers are the ultimate judge of value; understanding their perspective is critical to truly identifying unnecessary activities.
Eliminating Non-Value-Added Activities: Practical Strategies
Once non-value-added activities are identified, various strategies can be employed for their elimination or reduction:
1. Automation:
Automating repetitive or manual tasks can significantly reduce time and resources spent on non-value-added activities. Automation can improve accuracy and consistency, while freeing up employees to focus on higher-value tasks. Examples include using robotics in manufacturing or implementing automated customer service systems.
2. Simplification:
Streamlining processes by removing unnecessary steps or simplifying existing ones can eliminate non-value-added activities. This often involves re-engineering processes to make them more efficient and straightforward. Careful analysis of each step is essential to ensure simplification doesn't compromise quality or customer satisfaction.
3. Kaizen Events:
These short, focused improvement events involve cross-functional teams working collaboratively to identify and eliminate waste. By focusing on a specific process area, Kaizen events can achieve rapid and significant improvements. They foster a culture of continuous improvement and empower employees to contribute to process optimization.
4. Technology Integration:
Implementing new technologies, such as enterprise resource planning (ERP) systems or customer relationship management (CRM) systems, can automate tasks, improve data management, and reduce redundancies. This integration streamlines communication and information flow, reducing non-value-added activities related to data entry, retrieval, and communication.
5. Lean Principles:
Lean manufacturing principles, such as eliminating waste (muda), value stream mapping, and just-in-time inventory management, provide a comprehensive framework for identifying and eliminating non-value-added activities. Adopting lean methodologies can transform a company's operational efficiency and contribute to a culture of continuous improvement. Lean methodologies emphasize systematic waste reduction impacting all aspects of the process.
6. Employee Empowerment:
Empowering employees to identify and suggest improvements can unlock innovative solutions for eliminating non-value-added activities. Encouraging a culture of continuous improvement and providing employees with the tools and resources to make changes is critical for fostering creativity and engagement.
7. Process Re-engineering:
This involves a fundamental redesign of business processes to achieve dramatic improvements in efficiency, quality, and customer satisfaction. Process re-engineering is often used to tackle complex problems and achieve significant breakthroughs in process improvement.
Measuring the Success of Non-Value-Added Activity Elimination
After implementing strategies to eliminate non-value-added activities, it's essential to measure the success of the changes. Key metrics include:
- Cycle Time Reduction: Measuring the time it takes to complete a process from start to finish.
- Cost Reduction: Assessing the reduction in expenses related to materials, labor, and overhead.
- Throughput Improvement: Evaluating the increase in the amount of output produced.
- Defect Rate Reduction: Monitoring the decrease in the number of defects or errors.
- Customer Satisfaction: Assessing customer feedback to determine the impact of changes on customer perception of value.
Continuous Improvement: The Ongoing Journey
Eliminating non-value-added activities is not a one-time event, but an ongoing journey. Regularly reviewing processes, seeking employee feedback, and staying abreast of new technologies are essential for maintaining a competitive edge. Continuous improvement requires a commitment to excellence and a culture that embraces change.
By implementing these strategies and continually monitoring results, organizations can significantly improve efficiency, reduce costs, and enhance customer satisfaction. The elimination of non-value-added activities is a key driver of operational excellence, leading to a more profitable and sustainable business. Remember, continuous refinement is crucial; what's effective today may require adjustments tomorrow to stay ahead of the curve and optimize processes for maximum efficiency.
Latest Posts
Latest Posts
-
If Laura Has Bipolar Disorder Then She
Mar 26, 2025
-
Business Law Text And Cases 15th Edition
Mar 26, 2025
-
Product Costs That Have Become Expenses Can Be Found In
Mar 26, 2025
-
If The Formula In Cell D49
Mar 26, 2025
-
What Makes Agglutination By Antibodies Possible
Mar 26, 2025
Related Post
Thank you for visiting our website which covers about Non-value-added Activities In A Process Design Can Be Eliminated By . We hope the information provided has been useful to you. Feel free to contact us if you have any questions or need further assistance. See you next time and don't miss to bookmark.