Mass Production Focuses On Producing Blank______.
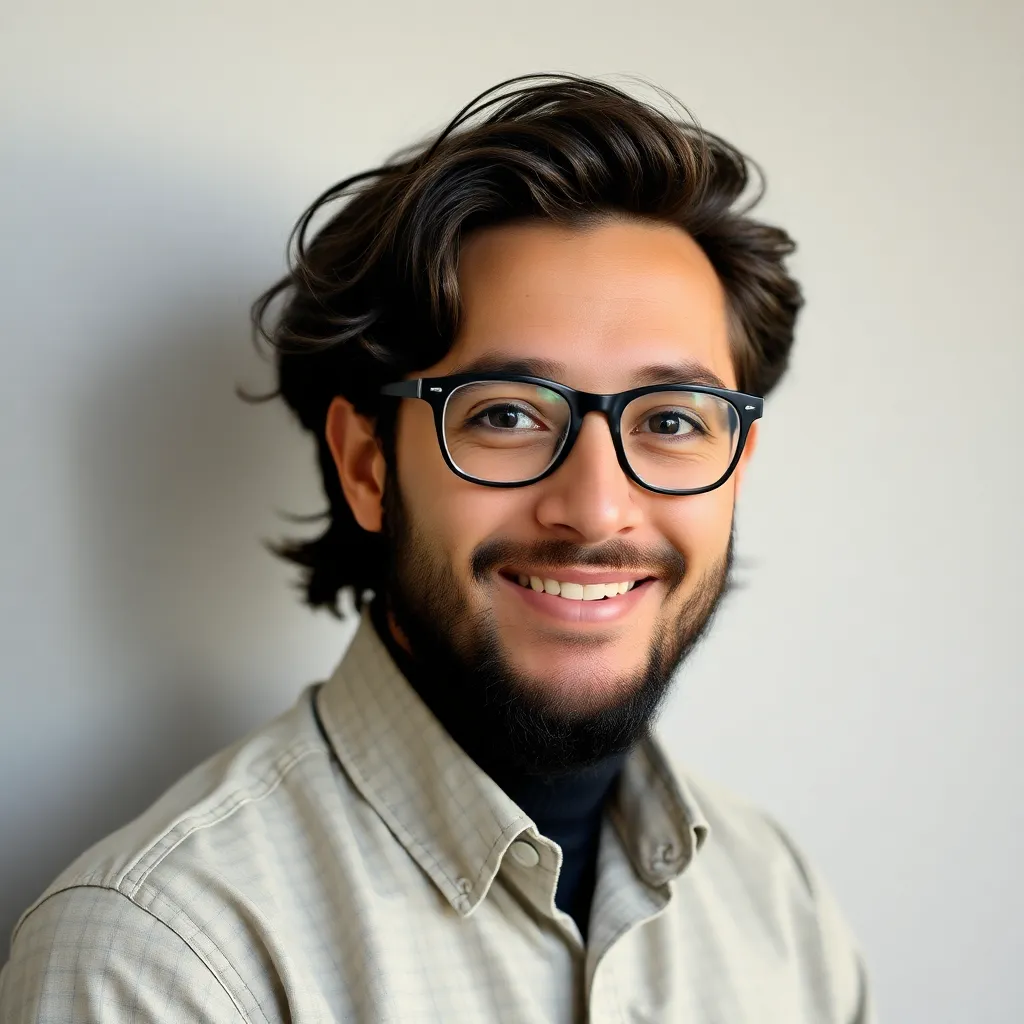
Holbox
Mar 16, 2025 · 6 min read
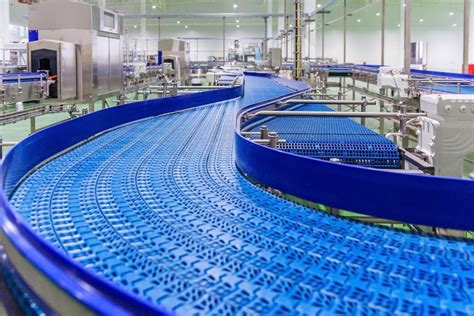
Table of Contents
Mass Production Focuses on Producing High Volumes of Standardized Goods
Mass production, a cornerstone of modern manufacturing, centers on producing high volumes of standardized goods. This approach contrasts sharply with bespoke or handcrafted methods, emphasizing efficiency, economies of scale, and consistent product quality. Understanding the core principles of mass production is crucial for businesses seeking to optimize their manufacturing processes and achieve significant cost reductions. This article delves into the intricacies of mass production, exploring its defining characteristics, advantages, disadvantages, historical context, and its ongoing evolution in the face of technological advancements and changing consumer demands.
The Pillars of Mass Production: Standardization and Efficiency
At its heart, mass production relies on two fundamental principles: standardization and efficiency. Standardization means creating identical or nearly identical products. This allows for streamlined production processes, reducing variability and simplifying quality control. Every component is designed to precise specifications, ensuring interchangeability and minimizing the need for customized adjustments during assembly. This focus on standardization is key to achieving high production volumes at a lower cost per unit.
Efficiency is the other crucial pillar. Mass production employs techniques to optimize every step of the manufacturing process, from material sourcing to final product delivery. This includes:
-
Specialization of Labor: Workers are assigned specific tasks, allowing them to become highly proficient in their areas of expertise. This division of labor significantly increases productivity.
-
Assembly Lines: Products move along a continuous assembly line, with each worker contributing a specific step in the manufacturing process. This sequential arrangement minimizes wasted time and movement.
-
Interchangeable Parts: Standardized parts can easily replace each other, simplifying repairs and reducing downtime. This interchangeability minimizes the need for specialized tools and expertise for maintenance.
-
Automation: The incorporation of automated machinery and robotics further enhances efficiency by reducing human error, increasing speed, and enabling continuous operation.
The Historical Evolution of Mass Production: From Eli Whitney to the Modern Era
The roots of mass production can be traced back to the late 18th and early 19th centuries. Eli Whitney's interchangeable parts concept, initially developed for firearms manufacturing, laid the groundwork for the mass production revolution. His innovative approach demonstrated that identical parts could be produced efficiently, simplifying assembly and reducing costs. This was a significant leap forward from the previous reliance on handcrafted, bespoke items.
The early 20th century saw the rise of the assembly line, famously pioneered by Henry Ford at his Ford Motor Company. Ford's innovative application of the assembly line to automobile production dramatically reduced manufacturing time and costs, making automobiles accessible to a much wider segment of the population. This success story catapulted mass production to prominence, transforming various industries.
The post-World War II era witnessed further refinement of mass production techniques, with the adoption of more sophisticated automation, improved materials handling, and advanced quality control methods. The emphasis shifted towards optimizing supply chains, minimizing waste, and improving overall productivity.
Advantages of Mass Production: Economies of Scale and Cost Reduction
Mass production offers numerous advantages, making it a highly attractive manufacturing approach for many industries:
-
Economies of Scale: Producing high volumes of goods lowers the per-unit cost. Fixed costs (like machinery and factory rent) are spread across a larger number of units, resulting in significant cost savings.
-
Lower Prices: The reduced production costs translate into lower prices for consumers, increasing market accessibility and demand.
-
Increased Efficiency: Streamlined processes and automation significantly increase production efficiency, leading to higher output with fewer resources.
-
Consistent Quality: Standardization and quality control mechanisms ensure consistent product quality, reducing defects and customer complaints.
-
Faster Production Time: Assembly lines and automation dramatically accelerate the production process, enabling quicker delivery to meet market demands.
-
Increased Profitability: The combination of reduced costs, higher output, and increased sales leads to improved profitability for businesses.
Disadvantages of Mass Production: Limitations and Challenges
While offering substantial benefits, mass production also has several limitations:
-
High Initial Investment: Setting up a mass production system requires significant upfront investment in machinery, infrastructure, and training. This can be a barrier to entry for smaller businesses.
-
Lack of Customization: Mass production prioritizes standardization, limiting options for customization or personalization. This can be a drawback in markets with diverse consumer preferences.
-
Dependence on Technology: Mass production relies heavily on technology and automation. Equipment malfunctions or disruptions in the supply chain can significantly impact production.
-
Potential for Job Displacement: Automation and increased efficiency can lead to job displacement, requiring workforce retraining and adaptation to new roles.
-
Environmental Impact: High production volumes can result in increased energy consumption, waste generation, and environmental pollution. Sustainable manufacturing practices are crucial to mitigate these effects.
-
Rigid Processes: The standardized nature of mass production makes it less flexible to respond to sudden changes in market demand or consumer preferences. Adapting to new product designs or features can be time-consuming and costly.
Mass Production in the Modern Era: Lean Manufacturing and Technological Advancements
In recent decades, mass production has evolved to incorporate more flexible and efficient methodologies, particularly lean manufacturing. Lean manufacturing focuses on eliminating waste in all forms, including excess inventory, unnecessary movement, and defects. This approach aims to optimize the entire production process, improving efficiency and responsiveness to changing market conditions.
Technological advancements have also played a crucial role in modernizing mass production. Computer-aided design (CAD) and computer-aided manufacturing (CAM) systems are widely used to design products and manage manufacturing processes. Robotics and automation continue to advance, allowing for greater precision, speed, and efficiency. 3D printing is emerging as a promising technology for customized production, potentially bridging the gap between mass production and personalized manufacturing.
The integration of big data analytics and the Internet of Things (IoT) offers further opportunities to optimize mass production processes. Data-driven insights can enhance predictive maintenance, improve quality control, and facilitate better inventory management. Connected machines and sensors enable real-time monitoring of production lines, allowing for prompt identification and resolution of issues.
The Future of Mass Production: Adaptability and Sustainability
The future of mass production will likely involve a greater emphasis on adaptability and sustainability. Businesses must be able to respond swiftly to changing consumer preferences, incorporating customization and personalization options while maintaining efficiency and cost-effectiveness. Sustainable manufacturing practices will become increasingly important, reducing environmental impact and promoting responsible resource management.
Mass customization, a hybrid approach that combines the efficiency of mass production with the personalization of bespoke manufacturing, is gaining traction. This allows businesses to offer a wider range of product variations tailored to specific customer needs while still benefiting from economies of scale.
The increasing focus on circular economy principles will also influence mass production. This involves designing products for durability, repairability, and recyclability, minimizing waste and maximizing resource utilization. The adoption of innovative materials and manufacturing processes that reduce environmental impact will be essential for sustainable mass production.
Conclusion: The Enduring Relevance of Mass Production
Despite the emergence of alternative manufacturing approaches, mass production remains a fundamental and highly relevant approach to manufacturing. Its ability to deliver high volumes of standardized goods at competitive prices continues to be a driving force in global economies. However, the ongoing evolution of mass production, incorporating lean manufacturing principles, advanced technologies, and a growing emphasis on sustainability, is crucial for ensuring its long-term viability and adaptability in a dynamic and increasingly competitive global marketplace. The future of mass production lies in its ability to embrace change and adapt to the evolving needs of consumers and the environment, while retaining its core strengths of efficiency and cost-effectiveness.
Latest Posts
Latest Posts
-
A Positive Return On Investment For Education Happens When
Mar 17, 2025
-
What Is The Value Of I
Mar 17, 2025
-
The Accounts In The Ledger Of Monroe Entertainment Co
Mar 17, 2025
-
A Process Cost Accounting System Is Most Appropriate When
Mar 17, 2025
-
An Example Of A Breach Of Ephi Is
Mar 17, 2025
Related Post
Thank you for visiting our website which covers about Mass Production Focuses On Producing Blank______. . We hope the information provided has been useful to you. Feel free to contact us if you have any questions or need further assistance. See you next time and don't miss to bookmark.