Labor Efficiency Is Measured By The
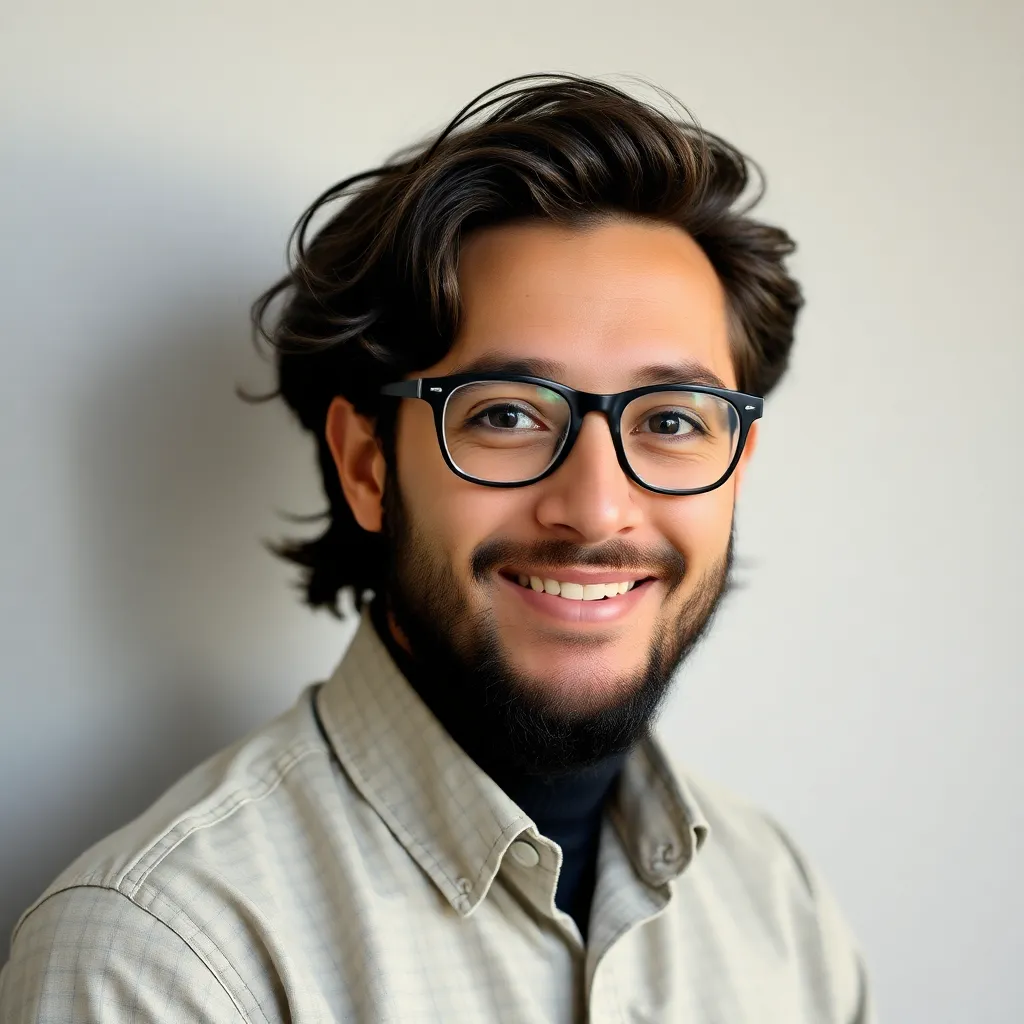
Holbox
Mar 28, 2025 · 7 min read

Table of Contents
- Labor Efficiency Is Measured By The
- Table of Contents
- Labor Efficiency: How It's Measured and How to Improve It
- What is Labor Efficiency?
- How is Labor Efficiency Measured?
- 1. Labor Productivity Ratio:
- 2. Unit Labor Cost:
- 3. Labor Cost Ratio:
- 4. Employee Turnover Rate:
- 5. Cycle Time and Throughput:
- Factors Influencing Labor Efficiency
- 1. Technology and Automation:
- 2. Employee Training and Skill Development:
- 3. Work Processes and Organization:
- 4. Employee Motivation and Engagement:
- 5. Equipment and Infrastructure:
- 6. Management Practices:
- 7. Employee Health and Well-being:
- 8. External Factors:
- Strategies for Improving Labor Efficiency
- 1. Process Optimization:
- 2. Technology Adoption:
- 3. Employee Empowerment and Skill Development:
- 4. Performance Management Systems:
- 5. Effective Communication and Collaboration:
- 6. Work-Life Balance Initiatives:
- 7. Regular Monitoring and Evaluation:
- Conclusion: The Importance of Continuous Improvement
- Latest Posts
- Latest Posts
- Related Post
Labor Efficiency: How It's Measured and How to Improve It
Labor efficiency is a crucial metric for any business, regardless of size or industry. It measures how effectively a company utilizes its workforce to produce goods or services. Understanding and improving labor efficiency directly impacts profitability, competitiveness, and overall business success. This comprehensive guide delves into the various methods of measuring labor efficiency, the key factors influencing it, and strategies for optimization.
What is Labor Efficiency?
Labor efficiency, in its simplest form, assesses how much output is generated relative to the labor input. A high level of labor efficiency indicates that a company is maximizing its workforce's productivity, while low efficiency signifies areas needing improvement. This isn't just about working harder; it's about working smarter. It involves optimizing processes, utilizing technology, and empowering employees to perform their tasks effectively.
Key Aspects of Labor Efficiency:
- Output: This refers to the quantity and quality of goods or services produced by the labor force. This could be anything from units manufactured to customer calls handled or projects completed.
- Input: This encompasses all resources consumed in the production process, primarily labor hours or costs, but also including materials, equipment, and energy.
- Time: Efficiency is inherently linked to time. Measuring the time taken to complete tasks is fundamental to assessing efficiency.
How is Labor Efficiency Measured?
There's no single universally accepted formula for measuring labor efficiency. The best method depends on the specific industry, business processes, and the nature of the work. However, several common approaches exist:
1. Labor Productivity Ratio:
This is perhaps the most straightforward method. It calculates the ratio of output to labor input:
Labor Productivity Ratio = Total Output / Total Labor Input
- Total Output: This can be measured in units produced, services rendered, sales generated, or any other relevant metric aligned with your business goals. Ensure consistent units of measurement throughout your calculations.
- Total Labor Input: This is typically measured in labor hours or labor costs. Consider using standard labor hours for a more consistent comparison across different periods or projects. Standard labor hours account for the expected time required for a task based on established norms and best practices.
Example: A manufacturing company produces 10,000 units in 500 labor hours. The labor productivity ratio is 20 units per labor hour (10,000 units / 500 hours).
2. Unit Labor Cost:
This metric focuses on the cost of labor per unit of output:
Unit Labor Cost = Total Labor Cost / Total Output
A lower unit labor cost generally indicates higher labor efficiency. This metric is particularly useful for comparing labor efficiency across different production lines, departments, or time periods.
Example: If the total labor cost is $50,000 and 10,000 units are produced, the unit labor cost is $5 per unit ($50,000 / 10,000 units).
3. Labor Cost Ratio:
This metric compares total labor costs to total sales revenue:
Labor Cost Ratio = Total Labor Cost / Total Revenue
This ratio helps understand the proportion of revenue spent on labor. A lower labor cost ratio typically indicates greater labor efficiency, assuming other factors remain constant.
Example: If total labor cost is $50,000 and total revenue is $200,000, the labor cost ratio is 0.25 or 25%.
4. Employee Turnover Rate:
While not a direct measure of efficiency, high employee turnover can negatively impact labor efficiency. Constant training and onboarding of new employees disrupt workflow and reduce productivity. Therefore, monitoring turnover is crucial for indirect assessment of efficiency.
Employee Turnover Rate = (Number of Employees Who Left / Average Number of Employees) x 100
A lower turnover rate suggests better employee retention and more stable, efficient operations.
5. Cycle Time and Throughput:
In manufacturing and process-oriented businesses, cycle time (the time it takes to complete a single process) and throughput (the rate of output over a period) are vital indicators of labor efficiency. Shorter cycle times and higher throughput indicate improved efficiency. Lean methodologies heavily utilize these metrics.
Factors Influencing Labor Efficiency
Numerous factors can impact the efficiency of your workforce. Understanding these factors is critical to implementing effective improvement strategies:
1. Technology and Automation:
Investing in appropriate technology and automation can significantly boost labor efficiency. Automation can handle repetitive tasks, reduce errors, and increase output with the same or fewer employees. Examples include robotic process automation (RPA), specialized software, and automated machinery.
2. Employee Training and Skill Development:
A well-trained and skilled workforce is essential for higher efficiency. Regular training programs equip employees with the necessary knowledge and skills to perform their tasks more effectively and efficiently. Investing in upskilling and reskilling initiatives enhances employee capabilities and adapts the workforce to changing technological landscapes.
3. Work Processes and Organization:
Inefficient work processes can significantly hinder labor efficiency. Streamlining workflows, eliminating bottlenecks, and implementing lean methodologies help optimize processes and reduce wasted time and resources. Effective organization, clear roles and responsibilities, and well-defined procedures are crucial.
4. Employee Motivation and Engagement:
Highly motivated and engaged employees are more productive and efficient. Creating a positive work environment, providing opportunities for growth and development, and recognizing and rewarding employees' contributions fosters motivation and boosts efficiency.
5. Equipment and Infrastructure:
Outdated or malfunctioning equipment can significantly reduce productivity. Regular maintenance, timely upgrades, and investment in reliable infrastructure are critical for ensuring smooth operations and maximizing labor efficiency.
6. Management Practices:
Effective leadership plays a vital role in optimizing labor efficiency. Strong management promotes clear communication, provides support and guidance to employees, and fosters a culture of continuous improvement. Utilizing data-driven decision-making and performance management systems contributes to efficiency improvements.
7. Employee Health and Well-being:
A healthy and well-rested workforce is a more productive one. Promoting employee wellness, offering health and wellness programs, and creating a supportive work-life balance contribute to greater efficiency by reducing absenteeism and improving overall performance.
8. External Factors:
External factors such as economic conditions, supply chain disruptions, and regulatory changes can indirectly impact labor efficiency. Effective risk management and contingency planning are essential to mitigate the impact of these factors.
Strategies for Improving Labor Efficiency
Based on the factors discussed, several strategies can be implemented to enhance labor efficiency:
1. Process Optimization:
Conduct thorough process mapping to identify bottlenecks, redundant tasks, and areas for improvement. Implement lean manufacturing principles like Kaizen to continuously improve processes and eliminate waste. Employ time-motion studies to analyze workflows and identify areas for optimization.
2. Technology Adoption:
Invest in technology that automates repetitive tasks, streamlines workflows, and improves data analysis. This includes ERP systems, CRM software, and other productivity tools. Explore the potential of artificial intelligence and machine learning to automate complex tasks and enhance decision-making.
3. Employee Empowerment and Skill Development:
Empower employees by giving them more autonomy and responsibility. Invest in comprehensive training programs to upgrade skills and knowledge. Encourage employee participation in process improvement initiatives to foster ownership and commitment.
4. Performance Management Systems:
Implement robust performance management systems to track key performance indicators (KPIs), provide regular feedback, and identify areas for improvement. Use data analytics to monitor labor efficiency trends and make data-driven decisions.
5. Effective Communication and Collaboration:
Promote open communication and collaboration among employees and teams. Utilize project management software to facilitate task management and track progress. Foster a culture of knowledge sharing and continuous learning.
6. Work-Life Balance Initiatives:
Create a supportive work environment that values employee well-being and work-life balance. Offer flexible work arrangements, promote employee wellness programs, and provide opportunities for personal and professional growth.
7. Regular Monitoring and Evaluation:
Continuously monitor key labor efficiency metrics to track progress and identify areas requiring attention. Regularly evaluate the effectiveness of implemented strategies and make adjustments as needed. Use data analytics to uncover trends and identify actionable insights.
Conclusion: The Importance of Continuous Improvement
Labor efficiency is a dynamic metric that requires continuous monitoring and improvement. By understanding the various methods for measurement, identifying key influencing factors, and implementing effective strategies, businesses can significantly enhance their workforce's productivity, reduce costs, and improve overall profitability. The journey toward optimal labor efficiency is a continuous process of refinement, adaptation, and commitment to ongoing improvement. Regular analysis, employee engagement, and technological innovation are critical elements in achieving and sustaining high levels of labor efficiency. Remember that focusing on both quantitative and qualitative aspects of labor efficiency will provide a more comprehensive understanding of your workforce's performance and allow for more targeted improvement strategies.
Latest Posts
Latest Posts
-
Which Statement About The Need For Faster Speed To Market Is True
Mar 31, 2025
-
Identify The Four Postulates Of Natural Selection
Mar 31, 2025
-
Select The Action For Which The Featured Muscle Is Responsible
Mar 31, 2025
-
Label The Components Of A Synapse
Mar 31, 2025
-
Cost Accounting Systems Are Used To
Mar 31, 2025
Related Post
Thank you for visiting our website which covers about Labor Efficiency Is Measured By The . We hope the information provided has been useful to you. Feel free to contact us if you have any questions or need further assistance. See you next time and don't miss to bookmark.