High Holding Costs Tend To Favor Inventory Levels And Replenishment.
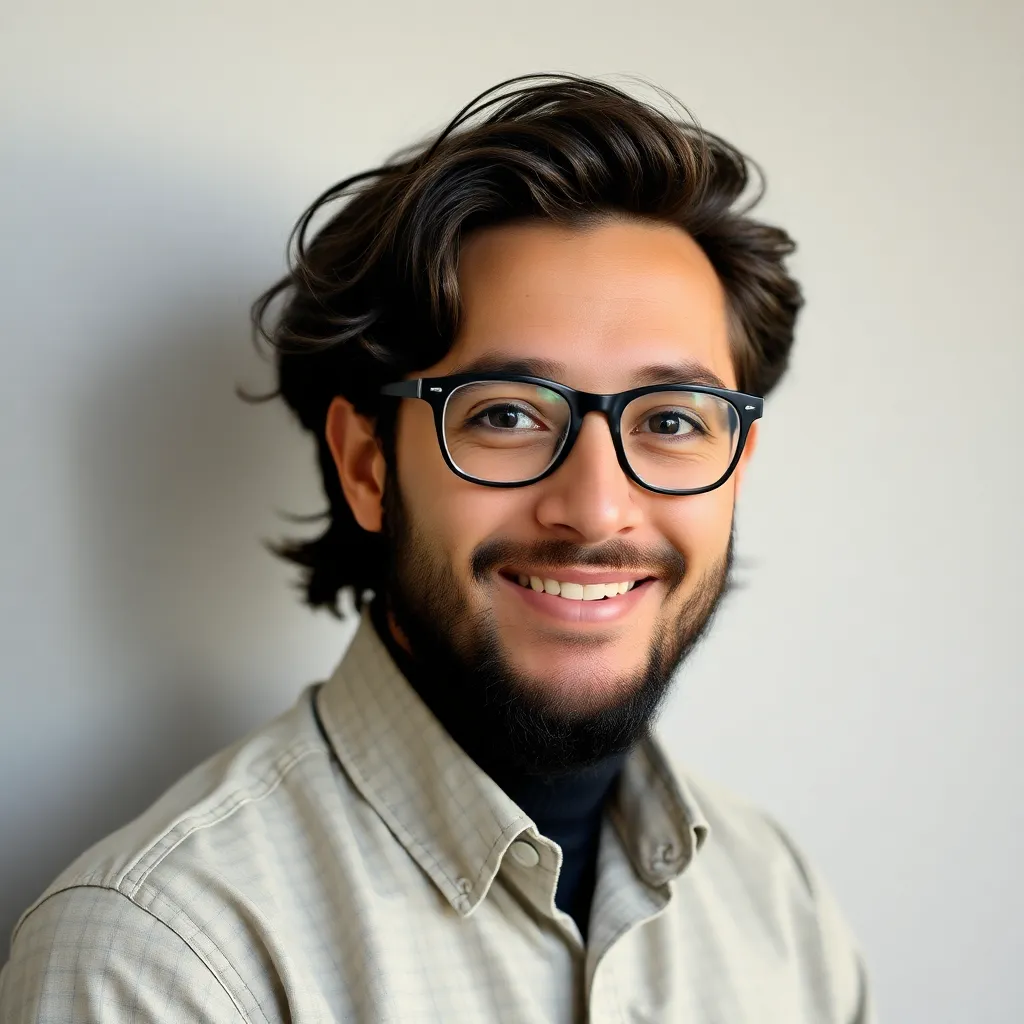
Holbox
Mar 19, 2025 · 6 min read
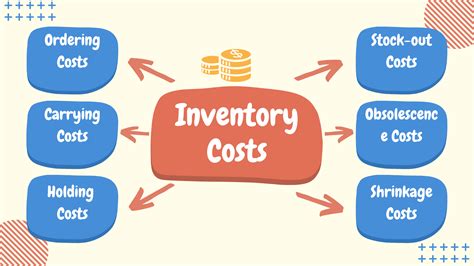
Table of Contents
High Holding Costs Tend to Favor Lower Inventory Levels and Replenishment Strategies
High holding costs significantly impact inventory management strategies. Contrary to the initial assumption in the title, high holding costs actually favor lower inventory levels and more frequent, smaller replenishments. This article delves deep into the dynamics of inventory holding costs, examining their influence on inventory levels and exploring optimal replenishment strategies to minimize overall costs and maximize efficiency.
Understanding Inventory Holding Costs
Before we delve into the relationship between holding costs and inventory levels, it's crucial to understand what constitutes holding costs. These aren't simply the costs of storing goods in a warehouse. Holding costs encompass a broader range of expenses associated with maintaining inventory:
1. Storage Costs:
- Warehouse Rent: The cost of leasing or owning warehouse space, including utilities (electricity, heating, cooling).
- Racking and Shelving: The investment in storage infrastructure.
- Insurance: Protecting inventory against damage, theft, or loss.
- Security: Measures to safeguard the inventory from unauthorized access.
2. Capital Costs:
- Opportunity Cost: The potential return on investment (ROI) that could have been earned by investing the capital tied up in inventory elsewhere. This is often the most significant holding cost component.
- Interest on Loans: If inventory financing is used, interest payments add to the holding cost.
3. Obsolescence and Deterioration Costs:
- Spoilage: Perishable goods or those with a short shelf life incur spoilage costs.
- Obsolescence: Products that become outdated or unmarketable due to technological advancements or changes in consumer preferences.
- Shrinkage: Loss of inventory due to theft, damage, or inaccurate record-keeping.
4. Insurance and Taxes:
- Property Taxes: Taxes levied on inventory held in warehouses.
- Insurance Premiums: Protecting against various risks associated with inventory storage.
The Inverse Relationship: High Holding Costs and Low Inventory Levels
The core principle is simple: higher holding costs directly incentivize businesses to minimize the amount of inventory they hold. Each unit of inventory held incurs these costs over time. Therefore, the more inventory a company holds, the higher its overall holding costs will be.
For instance, if the cost of holding one unit of a product for a year is $10, holding 1000 units will cost $10,000 annually. This substantial expense motivates businesses to implement strategies to reduce inventory levels.
Replenishment Strategies in Response to High Holding Costs
When holding costs are high, businesses naturally shift towards inventory management strategies that emphasize frequent, smaller replenishments. This contrasts with strategies employed when holding costs are low, where larger, less frequent orders might be more economical. Here are some key replenishment strategies favored under high holding costs:
1. Just-in-Time (JIT) Inventory Management:
JIT is a highly efficient inventory management system that aims to receive goods only when needed for production or sale. This minimizes the amount of inventory held at any given time, directly addressing the challenge of high holding costs. JIT requires strong supplier relationships, precise demand forecasting, and excellent logistical coordination. However, it can be vulnerable to supply chain disruptions.
2. Vendor-Managed Inventory (VMI):
VMI allows suppliers to manage a company's inventory levels. The supplier monitors inventory levels, forecasts demand, and automatically replenishes stock as needed. This approach leverages the supplier's expertise and reduces the burden on the company's internal inventory management team. It also promotes closer collaboration and streamlined processes.
3. Frequent Small Orders:
Instead of placing large, infrequent orders, businesses opt for smaller, more frequent orders to maintain optimal inventory levels. This approach allows for better control over inventory and reduces the risk of obsolescence or spoilage. However, it might increase ordering costs slightly. The trade-off, however, is often worthwhile considering the significant reduction in holding costs.
4. Lean Manufacturing Principles:
Lean manufacturing focuses on eliminating waste in all aspects of production, including inventory. It aligns perfectly with the need to minimize holding costs by promoting efficiency, reducing lead times, and improving production processes. Lean principles encourage continuous improvement and waste reduction across the supply chain.
Analyzing the Trade-Off: Holding Costs vs. Ordering Costs
While minimizing holding costs is crucial, businesses must also consider ordering costs. Placing frequent orders, even if they're small, involves administrative expenses, transportation costs, and potential handling fees. Therefore, there's a trade-off between holding costs and ordering costs. The optimal strategy involves finding the balance point where the total cost (holding costs + ordering costs) is minimized.
This optimal point is often determined using quantitative models like the Economic Order Quantity (EOQ) model. EOQ helps calculate the optimal order size that minimizes total inventory costs. However, the EOQ model’s accuracy depends on several assumptions, including constant demand and lead times. In reality, demand and lead times fluctuate. Therefore, more sophisticated inventory management systems, such as those incorporating forecasting and demand planning, are often employed.
Technological Advancements and Inventory Management
Technological advancements play a significant role in managing inventory effectively under high holding costs. Several technologies help optimize inventory levels and reduce associated costs:
1. Inventory Management Software:
Sophisticated software systems provide real-time visibility into inventory levels, track stock movements, and automate ordering processes. This enables businesses to make informed decisions based on accurate data, minimizing holding costs and preventing stockouts.
2. Radio Frequency Identification (RFID):
RFID technology allows for automated tracking of inventory items, providing real-time information on location, quantity, and movement. This improves inventory accuracy, reduces shrinkage, and facilitates efficient stock management.
3. Demand Forecasting Software:
Accurate demand forecasting is crucial for minimizing inventory levels. Advanced forecasting software uses historical data, market trends, and other factors to predict future demand, allowing businesses to adjust ordering quantities accordingly.
4. Supply Chain Management Systems:
Integrated supply chain management (SCM) systems provide end-to-end visibility into the supply chain, enabling better coordination between suppliers, manufacturers, and distributors. This streamlines processes, reduces lead times, and allows for more efficient inventory management.
Case Studies: High Holding Costs and Replenishment Strategies
While specific data from private companies regarding their inventory costs is often confidential, we can illustrate the impact of high holding costs through hypothetical examples and general industry trends:
Scenario 1: Perishable Goods: A grocery store dealing with highly perishable goods (e.g., fresh produce) faces extremely high holding costs due to spoilage. They would heavily rely on JIT inventory management, frequent deliveries from suppliers, and careful demand forecasting to minimize waste and holding costs.
Scenario 2: High-Tech Electronics: A company selling high-tech electronics with rapid technological advancements also faces significant obsolescence risk. Holding costs are high due to potential obsolescence. This company would prioritize frequent, smaller replenishments, and potentially adopt a more agile manufacturing approach to respond quickly to changing market demands.
Scenario 3: Seasonal Products: A retailer selling seasonal products (e.g., winter coats) experiences high holding costs for unsold inventory after the season ends. They need to accurately predict demand and manage inventory carefully to avoid excessive stock after the peak selling season. This might involve aggressive discounting strategies to sell off excess inventory before it becomes obsolete.
Conclusion: Embracing the Challenges of High Holding Costs
High holding costs present significant challenges, but they also drive innovation and efficiency in inventory management. By adopting appropriate replenishment strategies, leveraging technological advancements, and carefully analyzing the trade-off between holding costs and ordering costs, businesses can effectively mitigate the negative impacts of high holding costs, optimize inventory levels, and ultimately improve profitability. The key lies in proactive management, accurate data analysis, and a willingness to embrace efficient and adaptable inventory management practices. The strategies discussed here offer a solid foundation for navigating the complexities of inventory management in environments characterized by substantial holding costs. Continuous monitoring, adaptation, and optimization are crucial for long-term success.
Latest Posts
Latest Posts
-
What Does The Suffix Crasia Mean
Mar 19, 2025
-
Outdoor Exit Discharge Requirements Include All Of These Factors Except
Mar 19, 2025
-
Which Would Yield The Highest Performance
Mar 19, 2025
-
The Knee Jerk Reflex Is An Example Of A
Mar 19, 2025
-
What Can Tangled Lead Wires Lead To
Mar 19, 2025
Related Post
Thank you for visiting our website which covers about High Holding Costs Tend To Favor Inventory Levels And Replenishment. . We hope the information provided has been useful to you. Feel free to contact us if you have any questions or need further assistance. See you next time and don't miss to bookmark.