Effective Capacity Is Always Blank______ Design Capacity.
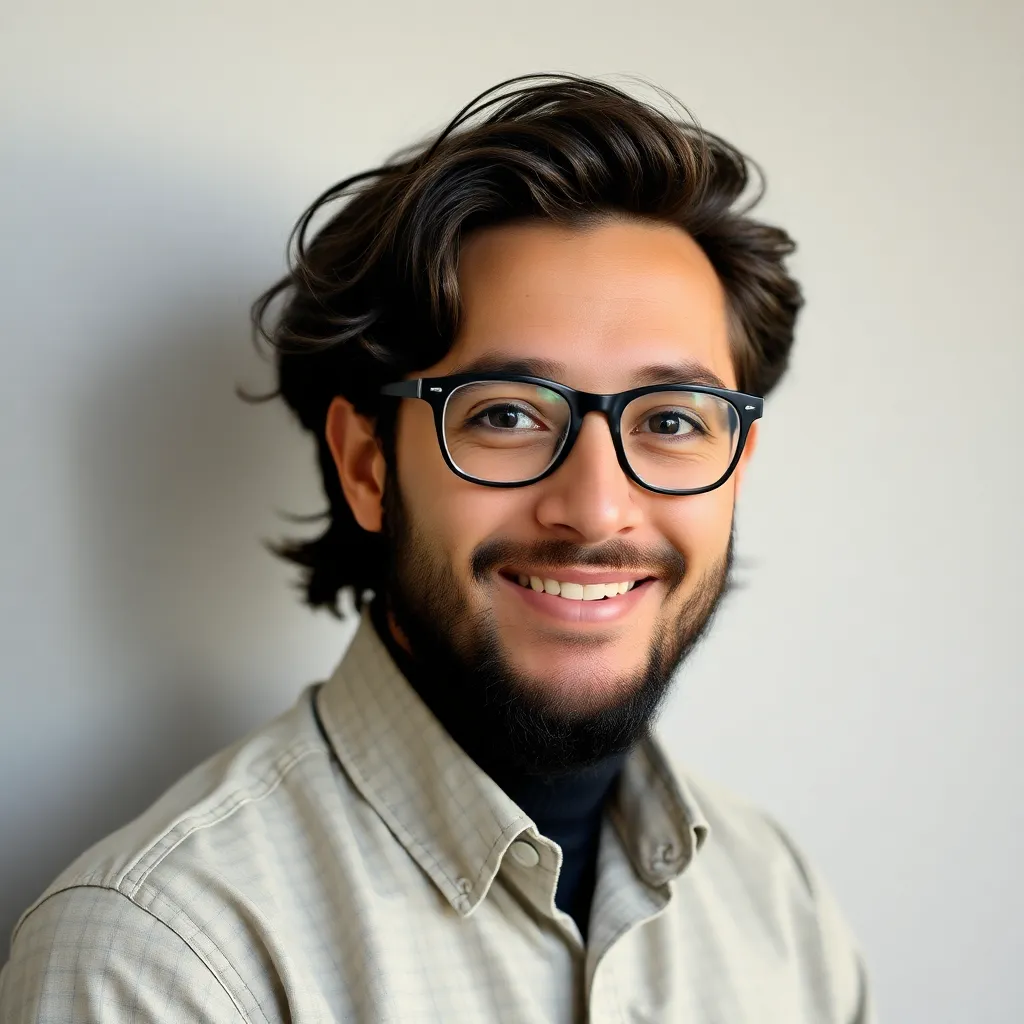
Holbox
Mar 20, 2025 · 5 min read
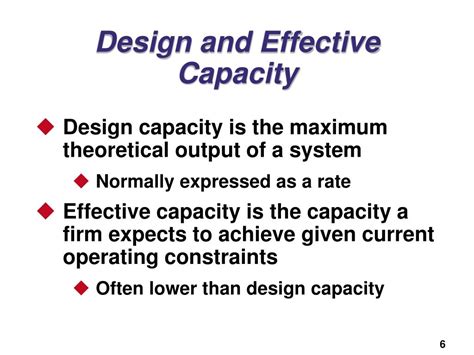
Table of Contents
Effective Capacity is Always Less Than Design Capacity: Understanding the Gap
Effective capacity, the actual output a system can achieve given its current operational realities, is always less than design capacity, the maximum output a system could theoretically achieve under ideal conditions. This fundamental difference stems from a multitude of factors that invariably impact real-world production environments. Understanding this gap is critical for effective operations management, strategic planning, and achieving optimal productivity. This article delves deep into the reasons why this disparity exists, exploring the key factors contributing to the difference and offering strategies for bridging the gap between design and effective capacity.
The Fundamental Discrepancy: Why Effective Capacity Always Lags
The core reason why effective capacity consistently falls short of design capacity lies in the inherent imperfections of real-world operations. Design capacity represents an idealized scenario, often based on optimistic assumptions about equipment performance, workforce efficiency, and the absence of unforeseen disruptions. In contrast, effective capacity reflects the realities of operational constraints, inefficiencies, and unforeseen events that inevitably impact production.
1. Equipment Downtime and Maintenance: A Major Contributor
Manufacturing plants and other operational systems rely heavily on machinery and equipment. However, even the most advanced equipment experiences downtime. This downtime can stem from various sources:
- Scheduled maintenance: Regular maintenance is crucial for preventing breakdowns and ensuring equipment longevity. However, this planned downtime directly reduces the time available for production.
- Unscheduled downtime: Unexpected breakdowns, malfunctions, and repairs account for significant unplanned downtime, often causing production delays and bottlenecks.
- Equipment failures: Aging equipment or poor maintenance can lead to increased failure rates, resulting in substantial lost production time.
2. Workforce Availability and Efficiency: Human Factors in Capacity
While design capacity often assumes a perfectly efficient and always-available workforce, reality dictates otherwise:
- Absenteeism and turnover: Illness, vacations, and employee turnover all contribute to reduced workforce availability, directly impacting production capacity.
- Training and skill gaps: Inadequate training or a lack of skilled workers can lead to slower production rates and higher error rates.
- Motivation and morale: A demotivated or disengaged workforce is less productive, directly impacting effective capacity.
- Human error: Mistakes and inefficiencies introduced by human operators are inevitable and contribute to reduced output.
3. Material and Supply Chain Constraints: The Bottleneck Effect
Efficient production relies on a consistent flow of raw materials, components, and supplies. However, disruptions in the supply chain can severely limit production:
- Supplier delays: Delays in receiving raw materials or components from suppliers can halt or slow down production.
- Inventory shortages: Insufficient stock of necessary materials can lead to production stoppages.
- Quality issues: Receiving defective materials can cause delays, reworking, and scrap, reducing effective capacity.
- Logistics bottlenecks: Delays in transportation, storage, or handling of materials can create bottlenecks that impede production.
4. Unforeseen Events and External Factors: The Unpredictable Impacts
Real-world operations are subject to unforeseen events that can significantly impact capacity:
- Natural disasters: Natural calamities like floods, earthquakes, or hurricanes can cause extensive damage and halt operations for prolonged periods.
- Power outages: Interruptions in power supply can bring production to a complete standstill.
- Economic downturns: Reduced demand and market instability can lead to lower production volumes, even if the system has the capacity to produce more.
- Unexpected breakdowns: Equipment failures beyond normal wear and tear can lead to unexpected downtime.
- Regulatory changes: New regulations or compliance requirements might impact operations, causing delays or restricting production.
5. Process Inefficiencies and Bottlenecks: Optimizing Workflow
Even with adequate resources, inefficient processes can drastically reduce output:
- Poor layout design: A poorly designed factory layout can create bottlenecks and slow down workflow.
- Inefficient processes: Outdated or poorly designed processes can waste time and resources.
- Lack of automation: Manual processes can be slower and more prone to error compared to automated systems.
- Poor communication: Ineffective communication between departments or teams can lead to delays and misunderstandings.
Bridging the Gap: Strategies for Maximizing Effective Capacity
While the gap between design and effective capacity is inevitable, businesses can employ several strategies to minimize this difference and maximize their operational efficiency.
1. Preventative Maintenance and Equipment Optimization: Proactive Approach
Implementing a robust preventative maintenance program is crucial to minimizing unscheduled downtime. This includes regular inspections, cleaning, lubrication, and part replacements to prevent equipment failures. Investing in more reliable and efficient equipment can also enhance productivity.
2. Workforce Development and Engagement: Investing in People
Investing in employee training and development is key to improving workforce skills and efficiency. Creating a positive and engaging work environment can boost morale and productivity. Effective workforce planning, including anticipating and addressing potential absences, is essential for consistent capacity.
3. Supply Chain Management and Risk Mitigation: Ensuring Material Flow
Establishing strong relationships with reliable suppliers and diversifying supply sources can mitigate risks associated with supplier delays. Implementing robust inventory management systems ensures the availability of necessary materials. Proactive risk assessment and mitigation strategies can help prepare for potential supply chain disruptions.
4. Process Improvement and Lean Manufacturing: Optimizing Workflow
Implementing lean manufacturing principles can identify and eliminate waste in production processes, streamlining workflows and improving efficiency. This includes techniques like value stream mapping, 5S methodology, and Kaizen events to continuously improve processes. Investing in automation technology can further reduce manual labor, errors, and process times.
5. Real-time Monitoring and Data Analytics: Informed Decision-Making
Utilizing real-time data monitoring and analytics can help identify potential bottlenecks and inefficiencies in real-time. This data-driven approach allows for proactive interventions to address issues before they significantly impact production. Predictive maintenance techniques can also leverage data to anticipate equipment failures and schedule maintenance accordingly.
6. Capacity Planning and Forecasting: Strategic Approach
Accurate capacity planning and forecasting are crucial for matching production capacity to anticipated demand. This involves considering various factors like seasonal variations, market trends, and potential growth opportunities. Regular review and adjustment of capacity plans ensure alignment with changing business needs.
The Continuous Pursuit of Optimality: A Dynamic Balance
The gap between design and effective capacity represents a dynamic challenge for businesses of all sizes. It's not a static problem to be solved once and for all, but rather an ongoing process of optimization. By understanding the contributing factors and implementing proactive strategies, businesses can significantly narrow this gap, leading to increased productivity, improved profitability, and a stronger competitive advantage. The continuous pursuit of optimizing processes and resources is critical for maximizing effective capacity and achieving operational excellence. Regular monitoring, analysis, and adaptation are key to maintaining a robust and efficient operational system that consistently delivers on its potential.
Latest Posts
Latest Posts
-
Coding Exercise Decoding A Message From A Text File Pytthon
Mar 20, 2025
-
Arrange The Pathophysiological Events Of Acne In The Correct Sequence
Mar 20, 2025
-
Evaluate The Definite Integral 1 3 1 7x Dx 0
Mar 20, 2025
-
Four Athletes From The Republic Of Korea
Mar 20, 2025
-
Partially Complete Units Are Known As Inventory
Mar 20, 2025
Related Post
Thank you for visiting our website which covers about Effective Capacity Is Always Blank______ Design Capacity. . We hope the information provided has been useful to you. Feel free to contact us if you have any questions or need further assistance. See you next time and don't miss to bookmark.