Costs Developed Which Identify What Products Should Cost Are Called
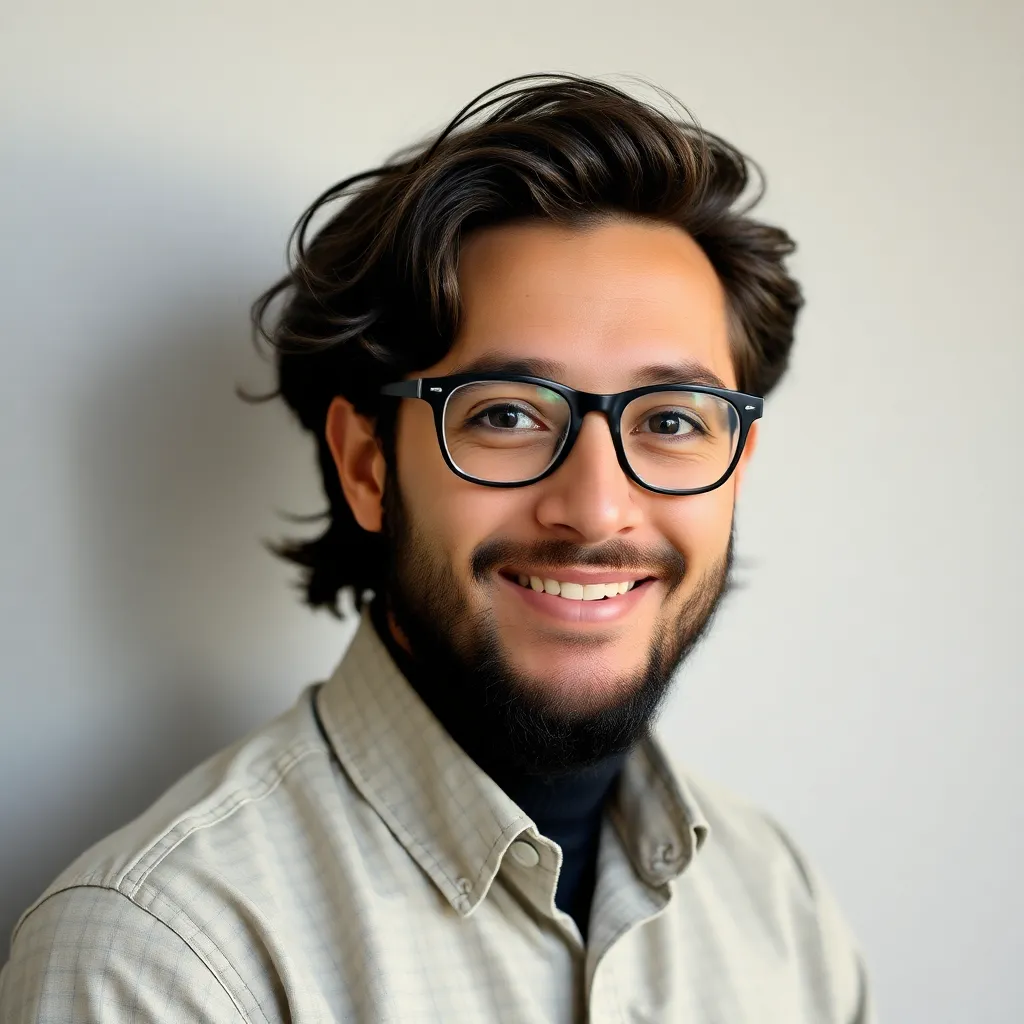
Holbox
Mar 26, 2025 · 6 min read
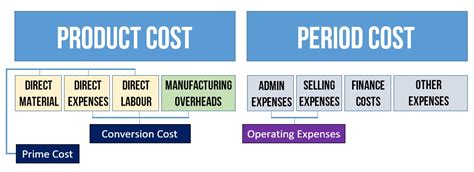
Table of Contents
- Costs Developed Which Identify What Products Should Cost Are Called
- Table of Contents
- Costing Methods: Identifying the True Price of Your Products
- Understanding Costing Methods: A Foundation for Pricing
- Key Costing Methods: A Detailed Analysis
- 1. Job Order Costing
- 2. Process Costing
- 3. Activity-Based Costing (ABC)
- 4. Lean Accounting
- 5. Target Costing
- Choosing the Right Costing Method
- Costing and Pricing: A Synergistic Relationship
- Beyond the Basics: Advanced Costing Concepts
- Conclusion: Mastering Costing for Business Success
- Latest Posts
- Latest Posts
- Related Post
Costing Methods: Identifying the True Price of Your Products
Determining the cost of your products is far more complex than simply adding up the raw materials and labor. Understanding the true cost involves a nuanced approach encompassing various costing methods, each with its own strengths and weaknesses. These methods are crucial for pricing strategies, profitability analysis, and informed business decisions. This in-depth article explores the various costing methods used to determine product costs, highlighting their applications and limitations.
Understanding Costing Methods: A Foundation for Pricing
Costing methods are systematic processes used to assign costs to products or services. They provide a crucial foundation for setting prices that ensure profitability while remaining competitive in the market. Accurate costing prevents underpricing (losing potential profit) and overpricing (losing market share). The choice of costing method depends on several factors, including the nature of the business, the complexity of the production process, and the level of detail required.
Key Costing Methods: A Detailed Analysis
Several costing methods exist, each offering a different perspective on product cost. The most common include:
1. Job Order Costing
Job order costing is ideal for businesses producing unique or custom products. Each product or job is treated as a separate cost unit, tracking costs directly related to that specific job. This method allows for precise cost determination for each individual project.
How it works: Costs are accumulated for each job, including direct materials, direct labor, and manufacturing overhead. These costs are then allocated to the job, providing a detailed cost breakdown.
Example: A custom furniture maker using job order costing would track the cost of wood, labor, and finishing materials for each individual piece of furniture.
Advantages: Provides accurate cost information for each job, facilitating better pricing and profitability analysis.
Disadvantages: Can be time-consuming and labor-intensive, particularly for businesses with numerous jobs. It requires meticulous record-keeping.
2. Process Costing
Process costing is best suited for businesses producing large volumes of homogeneous products. Costs are averaged across the entire production process rather than tracked for individual units.
How it works: Total costs are accumulated for a specific period and then divided by the number of units produced to arrive at an average cost per unit.
Example: A food processing plant producing canned goods would use process costing, averaging the cost of ingredients, labor, and manufacturing overhead across all cans produced.
Advantages: Simple and efficient for high-volume, standardized products, reducing administrative overhead.
Disadvantages: May not accurately reflect the cost of individual units, particularly if there's significant variation in production or material usage. It masks inefficiencies in the production process.
3. Activity-Based Costing (ABC)
Activity-based costing (ABC) is a more sophisticated method that allocates overhead costs based on the activities that drive those costs. This approach is particularly useful when overhead costs represent a significant portion of total costs.
How it works: ABC identifies various activities involved in production and assigns costs to those activities. These costs are then allocated to products based on their consumption of those activities.
Example: A company manufacturing electronics might allocate overhead costs based on the number of machine hours, inspections, or design changes needed for each product.
Advantages: Provides a more accurate representation of product costs, especially when overhead is complex and varies widely between products. It highlights cost drivers and allows for better cost control.
Disadvantages: More complex and time-consuming to implement than traditional costing methods. Requires detailed information on activities and their associated costs.
4. Lean Accounting
Lean accounting aligns with lean manufacturing principles, focusing on eliminating waste and improving efficiency. It emphasizes value-added activities and provides timely, relevant cost information to support continuous improvement.
How it works: Lean accounting focuses on tracking costs related to value-added activities and identifying non-value-added costs that can be eliminated. It uses visual management tools and streamlined processes to improve cost control.
Example: A company using lean accounting might track the cost of defects, rework, and inventory holding to identify areas for improvement.
Advantages: Supports continuous improvement efforts, improves efficiency, and reduces costs by focusing on value-added activities.
Disadvantages: Requires a significant change in organizational culture and processes. May not be suitable for all types of businesses.
5. Target Costing
Target costing is a proactive approach that determines the desired cost of a product before starting the design and production process. This method sets a target cost based on market price and desired profit margin.
How it works: The desired selling price is determined, and the desired profit margin is subtracted to establish the target cost. The design and production processes are then optimized to meet this target cost.
Example: A company developing a new smartphone might set a target cost based on the anticipated market price and desired profit. The engineers would then work to design and manufacture the phone within this cost constraint.
Advantages: Encourages innovation and cost-reduction efforts early in the product development process. Helps ensure product profitability before significant resources are invested.
Disadvantages: Requires accurate market research and forecasting. Can be challenging to meet target costs if unforeseen complications arise during development.
Choosing the Right Costing Method
The selection of the most appropriate costing method depends on several factors:
- Type of Product: Job order costing is suitable for customized products, while process costing is appropriate for mass-produced, standardized goods.
- Production Volume: High-volume production often favors process costing, while lower volumes might necessitate job order costing.
- Complexity of Production: Simple production processes may be adequately served by simpler costing methods, while complex processes may benefit from ABC costing.
- Management Objectives: Lean accounting aligns with lean manufacturing goals, while target costing focuses on achieving specific cost targets.
- Available Resources: Implementing more sophisticated methods like ABC costing requires more resources and expertise.
Costing and Pricing: A Synergistic Relationship
Accurate costing is essential for effective pricing. Once the cost of a product is determined, businesses can add a markup to arrive at a selling price that ensures profitability. However, the pricing strategy must also consider market factors such as competition, consumer demand, and perceived value.
Beyond the Basics: Advanced Costing Concepts
While the above methods represent the core of product costing, several advanced concepts further refine the process:
- Cost-Volume-Profit (CVP) Analysis: This tool examines the relationship between cost, volume, and profit to help businesses make informed decisions about pricing, production volume, and sales mix.
- Life Cycle Costing: This approach considers the total cost of a product over its entire life cycle, from design and development to disposal, helping businesses make informed decisions about product design and materials.
- Throughput Accounting: This method focuses on throughput (revenue generated from sales) and operational expenses, ignoring traditional inventory valuations. It is particularly useful in environments with high inventory levels.
Conclusion: Mastering Costing for Business Success
Mastering costing methods is paramount for achieving profitability and making informed business decisions. By understanding the nuances of various costing techniques and selecting the most suitable method for their specific business context, companies can gain valuable insights into their product costs, optimize their pricing strategies, and ultimately enhance their overall financial performance. The choice isn't about picking the "best" method universally, but rather the method best aligned with the unique characteristics and goals of the individual business. Continuous monitoring, evaluation, and adaptation of costing methods are key to staying competitive and profitable in dynamic markets.
Latest Posts
Latest Posts
-
There Are Five Advantages Of Using Games In Science
Mar 30, 2025
-
How Did The Great Depression Change American Attitudes About Welfare
Mar 30, 2025
-
Consider The Following Transactions For Thomas Company
Mar 30, 2025
-
An Income Statement Would Not Include
Mar 30, 2025
-
While You Are On The Phone With A Member
Mar 30, 2025
Related Post
Thank you for visiting our website which covers about Costs Developed Which Identify What Products Should Cost Are Called . We hope the information provided has been useful to you. Feel free to contact us if you have any questions or need further assistance. See you next time and don't miss to bookmark.