Conveyors Should Be Equipped With Which Of The Following
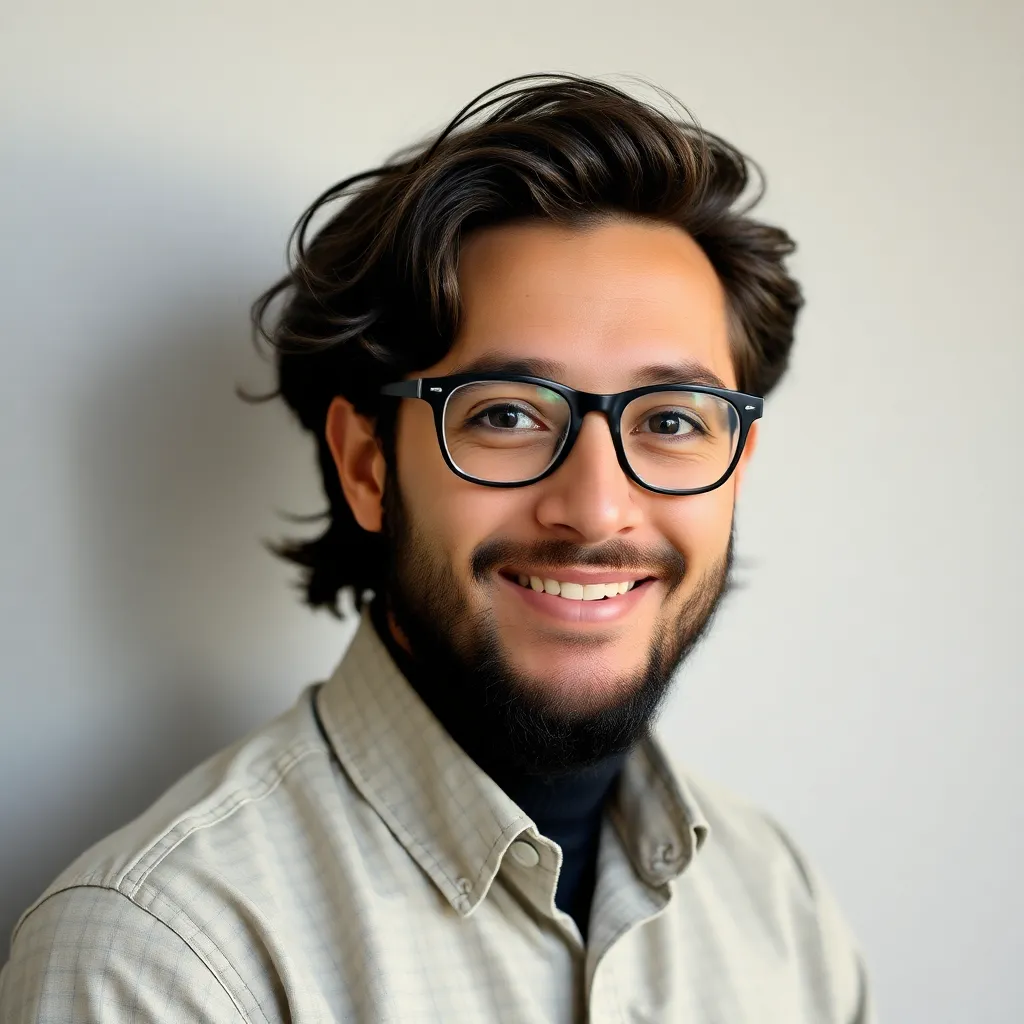
Holbox
Mar 20, 2025 · 7 min read
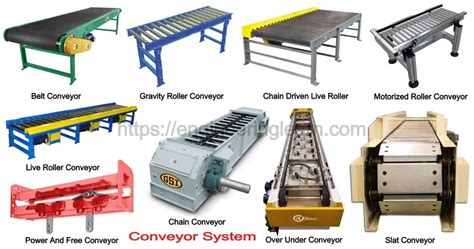
Table of Contents
Conveyors Should Be Equipped With Which of the Following: A Comprehensive Guide to Conveyor Safety and Efficiency
Conveyors are the backbone of countless industries, from manufacturing and warehousing to airports and postal services. Their efficient operation is crucial for productivity and profitability. However, safety and efficiency are not mutually exclusive; in fact, they are intrinsically linked. A safe conveyor system is inherently a more efficient one. This article delves into the essential components and safety features that should be equipped on every conveyor system to maximize both safety and operational efficiency.
Essential Components for Optimal Conveyor Performance
Before we dive into safety features, let's establish a foundation of essential components that contribute to a high-performing conveyor system. These components are the building blocks upon which safety features are implemented.
1. Robust Frame and Structure:
- Material Selection: The frame should be constructed from durable, high-quality materials like steel or aluminum, chosen based on the specific application and load requirements. Corrosion resistance is crucial in environments with exposure to moisture or chemicals.
- Structural Integrity: The frame must be designed to withstand the intended load capacity, including both the weight of the conveyed material and any dynamic forces during operation. Regular inspections for structural damage are essential.
- Modular Design: A modular design allows for easier maintenance, upgrades, and adjustments to accommodate changing needs. This flexibility reduces downtime and improves overall efficiency.
2. High-Performance Motors and Drives:
- Power and Torque: The motor must deliver sufficient power and torque to handle the intended load and speed requirements. Oversized motors can lead to energy waste, while undersized motors can result in system failure.
- Variable Speed Control: Variable speed drives (VSDs) offer precise control over conveyor speed, optimizing throughput and reducing energy consumption. They also allow for smoother starts and stops, reducing stress on the system and improving safety.
- Emergency Stop Mechanisms: Reliable and readily accessible emergency stop switches are paramount for immediate shutdowns in case of accidents or malfunctions.
3. Reliable Belt, Roller, or Chain Mechanisms:
- Material Selection: The choice of belt, roller, or chain depends on the specific application. Factors such as the type of material being conveyed, speed requirements, and environmental conditions all play a crucial role. Consider durability, friction resistance, and chemical compatibility.
- Tensioning Systems: Proper tensioning is vital to prevent belt slippage, chain slack, or roller misalignment, all of which can impact efficiency and safety. Regular tension checks and adjustments are necessary.
- Tracking Systems: Accurate tracking systems ensure the conveyed material stays centered on the conveyor, preventing jams and spills. This is especially crucial for high-speed conveyors carrying fragile items.
4. Efficient Load Handling and Transfer Systems:
- Feeders and Discharge Points: Well-designed feeders ensure a consistent and controlled flow of material onto the conveyor, while efficient discharge points prevent bottlenecks and material buildup.
- Transfer Mechanisms: For multi-conveyor systems, smooth and reliable transfer mechanisms are crucial to avoid material jams and damage. This often involves carefully designed transition points and potentially impact-absorbing systems.
- Material Handling Accessories: Consider the need for additional accessories like diverters, chutes, and incline mechanisms to optimize the flow of materials according to specific operational requirements.
Safety Features: Protecting Workers and Equipment
Safety should be paramount in every stage of conveyor design, installation, and operation. These essential safety features significantly reduce the risk of accidents and ensure a safe working environment.
1. Emergency Stop Systems:
- Multiple Stops: Multiple easily accessible emergency stop buttons strategically placed along the conveyor's length are crucial. These should be clearly marked and readily visible.
- Fail-Safe Mechanisms: The emergency stop system should be designed with fail-safe mechanisms to ensure a complete and immediate shutdown in the event of power failure or system malfunction.
- Lockout/Tagout Procedures: Clear lockout/tagout procedures should be implemented to prevent accidental restarts during maintenance or repairs.
2. Guarding and Enclosures:
- Full Enclosures: Wherever feasible, full enclosures should be used to prevent accidental contact with moving parts. This is particularly important for high-speed conveyors and those carrying hazardous materials.
- Point-of-Operation Guards: Where full enclosures aren’t practical, point-of-operation guards should be installed to protect workers from pinch points, nip points, and other potential hazards. These guards should be robust and securely fastened.
- Access Points: Any access points to the conveyor should be properly guarded and secured, ensuring easy access for maintenance while preventing accidental entry during operation.
3. Safety Sensors and Monitoring Systems:
- Presence Sensors: Presence sensors detect the presence of workers or objects in hazardous areas, automatically stopping the conveyor to prevent accidents.
- Speed Monitoring Systems: Systems that monitor conveyor speed and automatically shut down the system if it deviates from preset parameters help prevent overspeeding and related risks.
- Vibration Monitoring: Monitoring system vibrations can help detect early signs of mechanical wear and tear, preventing potential failures before they occur.
4. Lighting and Warning Systems:
- Adequate Lighting: Proper lighting in and around the conveyor area is essential for ensuring worker visibility and safe operation.
- Warning Signs and Labels: Clear warning signs and labels must be used to identify hazards and provide safety instructions. These should be prominently displayed and easily understandable.
- Audible Warnings: Audible alarms can alert workers to potential hazards, such as impending shutdowns or malfunctions.
5. Training and Procedures:
- Comprehensive Training: All workers operating or maintaining conveyors should receive comprehensive training on safe operating procedures, emergency shutdown procedures, and lockout/tagout protocols.
- Regular Inspections: Regular inspections of the conveyor system are crucial to identify and address potential safety hazards before they lead to accidents. A clear inspection checklist should be developed and followed.
- Emergency Response Plan: A well-defined emergency response plan should be in place, outlining procedures for handling various types of accidents or emergencies. This plan should include detailed steps, contact information for emergency services, and designated personnel responsibilities.
Optimizing Conveyor Efficiency: Beyond Safety
While safety is paramount, efficient conveyor operation significantly impacts productivity and profitability. Several strategies can optimize efficiency beyond simply implementing safety features:
1. Regular Maintenance:
- Preventative Maintenance Schedule: A comprehensive preventative maintenance schedule is crucial to detect and address minor issues before they escalate into major problems, causing downtime and costly repairs.
- Lubrication and Cleaning: Regular lubrication of moving parts and cleaning of the conveyor belt or rollers minimizes friction and extends the lifespan of components.
- Component Replacements: Proactive replacement of worn or damaged components prevents unexpected failures and minimizes downtime.
2. Process Optimization:
- Material Flow Analysis: Analyze the material flow to identify bottlenecks and inefficiencies. This may involve adjusting conveyor speed, optimizing loading and unloading points, or reconfiguring the layout.
- Load Balancing: Evenly distributing the load across the conveyor minimizes stress on individual components, extending their lifespan and improving overall efficiency.
- Integration with other Systems: Integrating the conveyor system with other automated systems, like robotics or warehouse management systems, can significantly streamline operations and enhance efficiency.
3. Energy Efficiency:
- Variable Speed Drives (VSDs): VSDs allow for precise speed control, reducing energy consumption by only using the necessary power.
- Energy-Efficient Motors: Choosing energy-efficient motors and drives can significantly reduce energy consumption over the long term.
- Belt Material Selection: Selecting belt materials with low friction coefficients reduces energy loss due to friction.
4. Data Analytics and Monitoring:
- Real-time Monitoring: Implementing real-time monitoring systems allows for immediate detection of issues, such as belt slippage or motor overload, enabling prompt intervention to prevent costly downtime.
- Predictive Maintenance: Data analytics can predict potential equipment failures based on historical data and current operational parameters, enabling proactive maintenance and preventing unexpected disruptions.
- Performance Metrics: Tracking key performance indicators (KPIs) such as throughput, downtime, and energy consumption provides valuable insights into the conveyor system's performance, allowing for data-driven improvements.
Conclusion:
Equipping conveyors with the right components and safety features is a crucial investment that pays off in enhanced safety, increased efficiency, and reduced operational costs. By prioritizing both safety and efficiency, businesses can ensure a smooth, productive, and safe working environment, maximizing profitability and minimizing risk. Remember that a proactive approach to maintenance, regular inspections, and ongoing employee training are essential to maintain a safe and productive conveyor system for years to come. A holistic approach that combines robust design, preventative maintenance, and proactive safety measures is the key to achieving optimal results.
Latest Posts
Latest Posts
-
How Do Smartphones Achieve Images With High Dynamic Range
Mar 20, 2025
-
Based On Values In Cells A51 A55
Mar 20, 2025
-
A Frequent Reason For A Stock Split Is To
Mar 20, 2025
-
Mutual Interdependence Means That Each Firm In An Oligopoly
Mar 20, 2025
-
Why Might A Company Carry Inventory
Mar 20, 2025
Related Post
Thank you for visiting our website which covers about Conveyors Should Be Equipped With Which Of The Following . We hope the information provided has been useful to you. Feel free to contact us if you have any questions or need further assistance. See you next time and don't miss to bookmark.