Control Limits Tend To Be Wider For More Variable Processes.
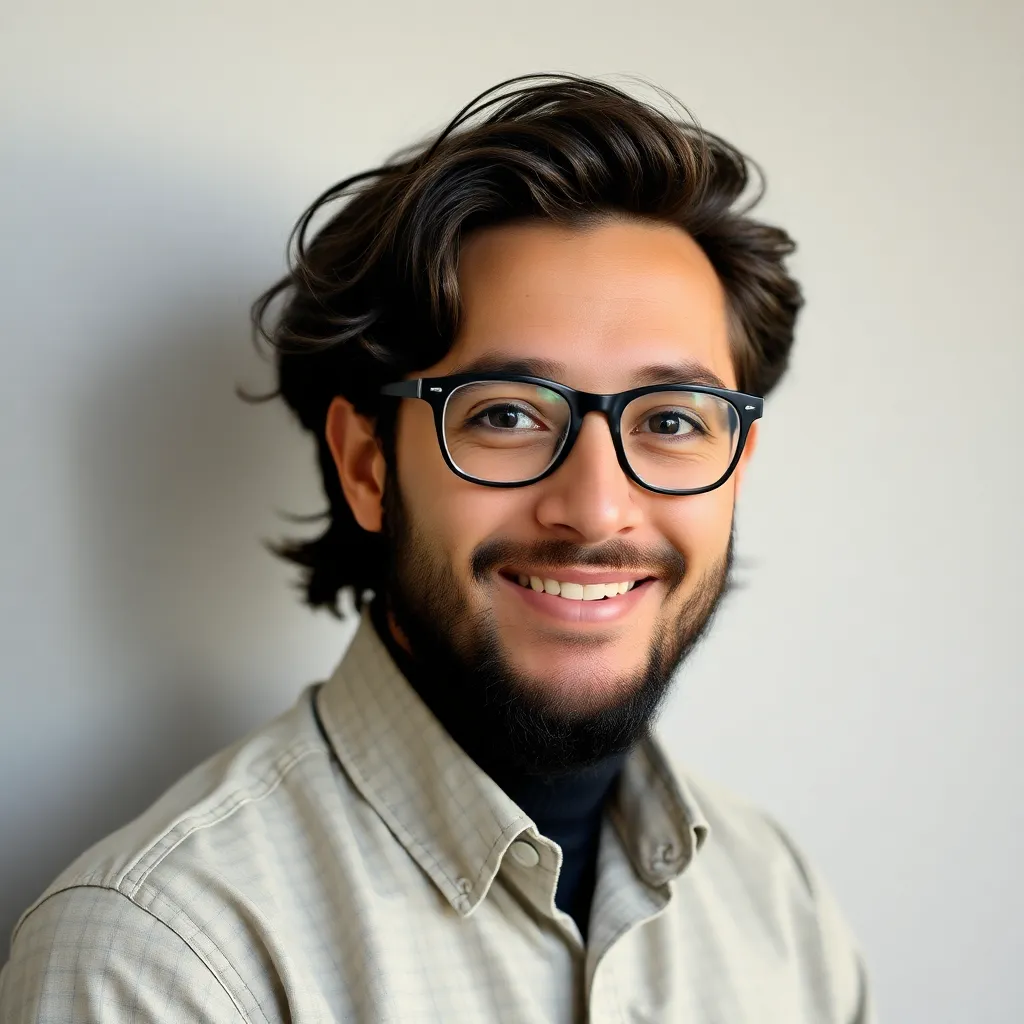
Holbox
Mar 15, 2025 · 6 min read

Table of Contents
Control Limits Tend to Be Wider for More Variable Processes: A Deep Dive into Statistical Process Control
Statistical Process Control (SPC) is a powerful methodology used to monitor and improve processes by identifying and reducing variability. A cornerstone of SPC is the use of control charts, which graphically display data collected over time, allowing for the detection of trends and anomalies. A key element of control charts is the concept of control limits. A common observation, and indeed a fundamental principle of SPC, is that control limits tend to be wider for more variable processes. This article will delve deep into this principle, exploring its underlying reasons, practical implications, and the importance of understanding process variability in achieving effective process control.
Understanding Control Limits and Process Variability
Before exploring the relationship between control limits and process variability, let's clarify the meaning of both terms.
Control Limits: The Boundaries of Expected Variation
Control limits are statistically determined boundaries on a control chart. They represent the acceptable range of variation for a process under stable conditions. Data points falling within these limits are considered to be consistent with the inherent variability of the process. Points falling outside the control limits indicate potential problems or special causes of variation requiring investigation. Control limits are typically calculated using statistical methods, most commonly based on the process mean and standard deviation. The most common limits are the 3-sigma limits, representing approximately 99.73% of the data points when the process is in control.
Process Variability: The Heart of the Matter
Process variability refers to the extent to which individual measurements or observations in a process differ from each other. High process variability indicates a process that is prone to producing inconsistent results, while low variability implies a more stable and predictable process. Several sources can contribute to process variability, including:
-
Common Cause Variation: This inherent variability is always present in a process, representing the normal fluctuations expected from random sources. Common cause variations are often difficult and costly to eliminate entirely. Examples include minor fluctuations in raw materials, slight differences in operator techniques, or minor variations in equipment performance.
-
Special Cause Variation: These are assignable causes of variation, often stemming from specific events or factors that disrupt the normal process behavior. Examples include equipment malfunction, changes in raw materials, operator errors, or changes in the process itself. Identifying and eliminating special causes of variation is crucial for improving process capability.
The level of process variability significantly influences the width of the control limits.
Why Wider Control Limits for More Variable Processes?
The core reason why control limits are wider for more variable processes lies in the statistical foundation of control charts. The control limits are calculated based on the process's inherent variability, typically measured by the standard deviation (σ). A process with a larger standard deviation implies greater inherent variability.
The calculation of control limits often involves multiples of the standard deviation. For example, the upper control limit (UCL) and lower control limit (LCL) for a process using 3-sigma limits are calculated as:
- UCL = Process Mean + 3σ
- LCL = Process Mean - 3σ
From these formulas, it's clear that a larger standard deviation (σ) directly results in wider control limits. A process with high variability (large σ) will have wider control limits than a process with low variability (small σ). This wider range reflects the higher degree of inherent fluctuation expected in a more variable process. Narrower limits for a highly variable process would lead to frequent false alarms, masking actual out-of-control conditions and hindering effective monitoring.
Practical Implications of Wider Control Limits
Understanding that control limits adapt to process variability has significant practical implications:
1. Avoiding False Alarms:
Wider control limits for more variable processes prevent an excessive number of false alarms. These false alarms, often caused by normal process fluctuation, can lead to wasted resources spent investigating non-existent problems. Focusing on genuine out-of-control signals allows for efficient problem-solving.
2. Accurate Process Monitoring:
Wider limits provide a more realistic representation of the process's natural variation, allowing for accurate monitoring of significant shifts or trends. A system with narrower limits on a highly variable process might not accurately reflect the actual shifts in the process, potentially leading to delayed responses to genuine problems.
3. Improved Process Capability Analysis:
The relationship between control limits and process variability plays a crucial role in process capability analysis. Process capability studies assess the ability of a process to meet specifications. Understanding the inherent variability of the process is essential for determining if the process is capable of meeting the required specifications.
4. Effective Problem Solving:
When an out-of-control point is detected, the wider control limits in a high-variability process provide a clearer indication of a significant deviation from the norm. This facilitates more efficient investigation and remediation of the root causes of the out-of-control condition.
Managing High Variability Processes
Managing processes with high variability requires a multifaceted approach:
1. Identifying and Eliminating Special Causes of Variation:
Systematic investigation of out-of-control points is crucial for identifying and eliminating special causes. This may involve using various problem-solving methodologies such as root cause analysis, Pareto charts, and fishbone diagrams. Addressing these special causes significantly reduces the overall process variability.
2. Process Improvement Initiatives:
Implement process improvement methodologies such as Lean and Six Sigma to systematically reduce process variation. These methodologies focus on identifying and eliminating waste, standardizing processes, and enhancing process efficiency.
3. Robust Process Design:
Designing processes that are less sensitive to variations in input parameters can help mitigate the effects of variability. This includes the selection of robust materials, equipment, and operating procedures.
4. Process Monitoring and Control:
Continuously monitor the process using control charts and other monitoring tools to detect and respond quickly to changes in variability. This proactive approach helps prevent minor variations from escalating into larger problems.
Conclusion: Embracing the Dynamics of Control Limits
The observation that control limits tend to be wider for more variable processes is not a limitation of SPC but rather a fundamental reflection of the process's inherent behavior. Understanding this relationship is essential for effective process monitoring and improvement. By acknowledging and adapting to the process variability, we can avoid the pitfalls of false alarms, accurately assess process capability, and efficiently address true out-of-control conditions. The goal is not merely to control the process within limits but to continuously reduce variability, ultimately leading to a more stable, efficient, and predictable process. This journey towards lower variability requires a holistic approach, encompassing process improvement initiatives, effective problem-solving strategies, and a deep understanding of the underlying statistical principles of SPC. By embracing the dynamics of control limits and their relationship with process variability, organizations can harness the full potential of SPC to achieve superior process performance.
Latest Posts
Latest Posts
-
Utma Accounts Are Opened Under The Tax Id Of The
Mar 17, 2025
-
In Which Situations Can Simplifying Jobs Be Most Beneficial
Mar 17, 2025
-
For The Hr Planning Process How Should Goals Be Determined
Mar 17, 2025
-
How Does A Shortcut Link To Another File
Mar 17, 2025
-
Cash Flows From Financing Activities Do Not Include
Mar 17, 2025
Related Post
Thank you for visiting our website which covers about Control Limits Tend To Be Wider For More Variable Processes. . We hope the information provided has been useful to you. Feel free to contact us if you have any questions or need further assistance. See you next time and don't miss to bookmark.