What Is A Downfall To Just-in-time Manufacturing And Inventory Management
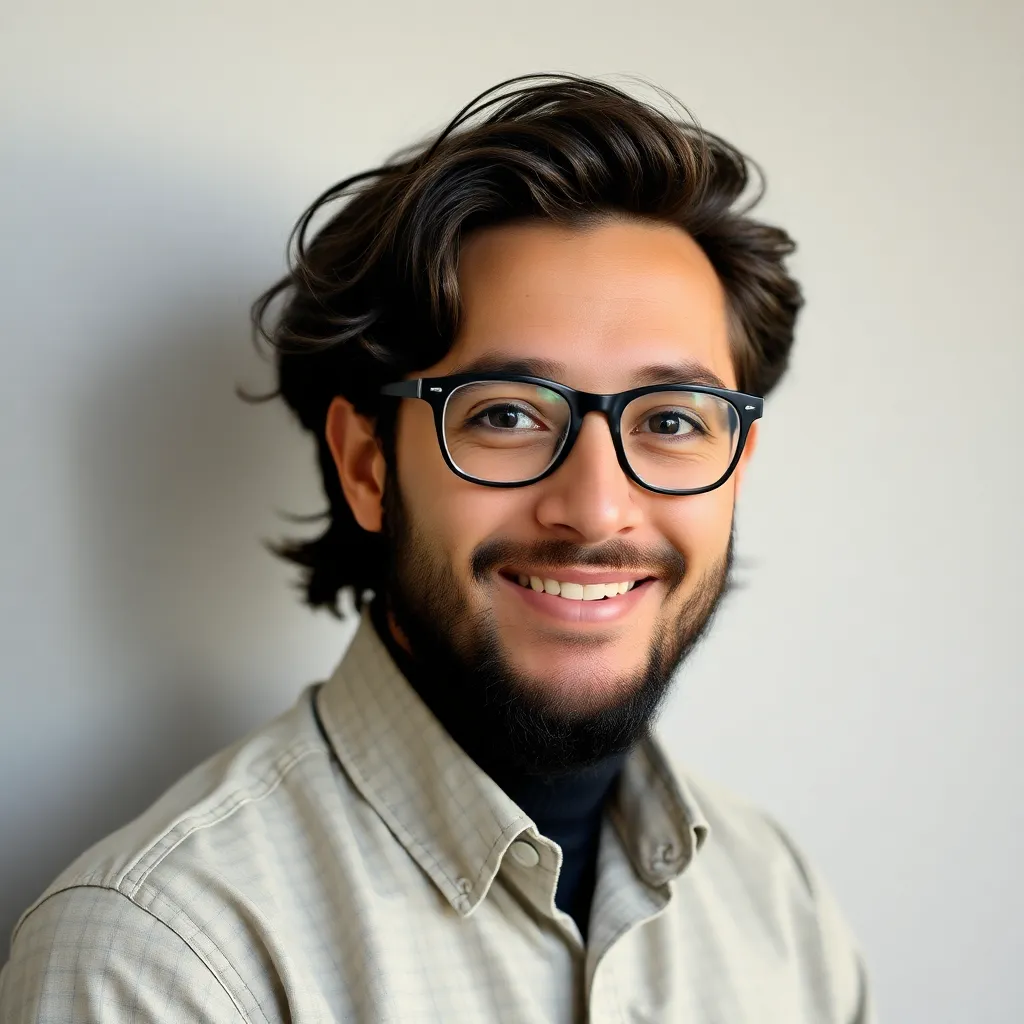
Holbox
Mar 30, 2025 · 7 min read
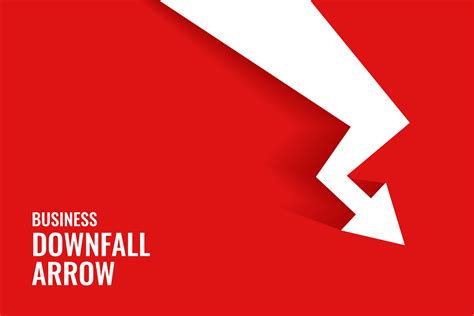
Table of Contents
- What Is A Downfall To Just-in-time Manufacturing And Inventory Management
- Table of Contents
- The Downside of Just-in-Time (JIT) Manufacturing and Inventory Management
- Vulnerability to Supply Chain Disruptions
- Impacts of Disruptions
- Dependence on Reliable Suppliers
- Supplier Challenges
- Lack of Buffer Stock and Increased Risk
- Risks and Mitigation
- Increased Pressure on Suppliers and Internal Processes
- Pressure Points
- Higher Transportation Costs
- Transportation Considerations
- The Importance of Accurate Forecasting
- Forecasting Challenges
- Need for Highly Skilled Workforce
- Workforce Needs
- High Risk of Quality Issues
- Quality Control Challenges
- Conclusion: Balancing the Benefits and Drawbacks of JIT
- Latest Posts
- Latest Posts
- Related Post
The Downside of Just-in-Time (JIT) Manufacturing and Inventory Management
Just-in-time (JIT) manufacturing and inventory management, a lean manufacturing system pioneered by Toyota, has revolutionized how businesses manage their supply chains. By minimizing waste and optimizing inventory levels, JIT promises significant cost savings and increased efficiency. However, while the benefits are undeniable under ideal conditions, the system also presents several significant downsides that can severely impact a business if not carefully considered and mitigated. This article delves into the potential pitfalls of JIT, exploring the challenges and vulnerabilities it presents in various operational aspects.
Vulnerability to Supply Chain Disruptions
Perhaps the most significant downfall of JIT is its extreme vulnerability to supply chain disruptions. The core principle of JIT – receiving materials only when needed – creates a highly fragile system. Any unforeseen event, however small, can have cascading effects throughout the production process.
Impacts of Disruptions
-
Delays in Delivery: A simple delay in the delivery of a single component, due to unforeseen circumstances like natural disasters, transportation issues, or supplier failures, can bring the entire production line to a standstill. This leads to lost production time, unmet customer orders, and significant financial losses.
-
Increased Lead Times: The reliance on timely delivery means that lead times are inherently shorter than in traditional inventory management systems. While this is advantageous in normal circumstances, it significantly amplifies the impact of any disruption. A small delay can translate into substantial delays in final product delivery.
-
Stockouts: The absence of buffer stock leaves the company extremely vulnerable to stockouts. This can lead to lost sales, dissatisfied customers, and damage to brand reputation. The ripple effect can extend beyond immediate sales, impacting future orders and customer loyalty.
Dependence on Reliable Suppliers
JIT relies heavily on strong, reliable supplier relationships. The success of JIT hinges on the ability of suppliers to deliver high-quality materials, precisely on time, and in the exact quantities required. Any failure in this area can cripple the entire system.
Supplier Challenges
-
Supplier Dependence: A high degree of dependence on a limited number of suppliers increases the risk of disruptions if one supplier experiences problems. This lack of diversification exposes the company to significant vulnerabilities.
-
Supplier Capacity: Suppliers need to be capable of meeting fluctuating demand. If a supplier struggles to meet the required production volumes, it can create bottlenecks and production delays.
-
Supplier Quality Control: Consistent product quality from suppliers is paramount. Defective materials received under JIT can halt production and require costly rework or scrap.
Lack of Buffer Stock and Increased Risk
The absence of buffer stock, a key characteristic of JIT, significantly increases the risk of production interruptions. While reducing storage costs and waste is a major benefit of JIT, it also leaves the business with limited capacity to absorb unexpected issues.
Risks and Mitigation
-
Demand Fluctuations: Unexpected surges in demand can overwhelm the system, leading to production delays and missed deadlines. While forecasting can mitigate some of this risk, unpredictable market shifts are difficult to anticipate precisely.
-
Machine Breakdowns: Equipment failures, even minor ones, can halt production immediately, as there is no reserve of materials or finished goods. This highlights the need for robust maintenance schedules and backup equipment.
-
Natural Disasters and Other Unforeseen Events: External events like natural disasters, political instability, or pandemics can severely impact the supply chain, rendering JIT highly vulnerable. Businesses implementing JIT must have robust contingency plans for such scenarios.
Increased Pressure on Suppliers and Internal Processes
Implementing JIT puts significant pressure on both suppliers and internal processes. The need for precise timing and coordination demands higher levels of efficiency and communication across the entire supply chain. This can lead to various challenges.
Pressure Points
-
Supplier Relationships: Strong, collaborative relationships with suppliers are essential. Open communication, shared information, and mutual trust are critical to ensure smooth operations. However, building and maintaining these relationships requires significant investment in time and resources.
-
Internal Coordination: Internal processes must be highly efficient and synchronized. This requires sophisticated planning and control systems, as well as highly trained and skilled employees.
-
Information Technology: Effective information sharing and real-time visibility across the supply chain are crucial. This requires investment in advanced information technology systems and data analytics capabilities.
Higher Transportation Costs
While JIT reduces inventory holding costs, it often leads to more frequent and smaller shipments, potentially resulting in higher transportation costs per unit. This trade-off needs careful consideration, especially when dealing with geographically dispersed suppliers.
Transportation Considerations
-
Increased Frequency of Shipments: Smaller, more frequent deliveries are necessary to maintain the just-in-time flow of materials. This can lead to higher transportation costs compared to larger, less frequent shipments.
-
Transportation Reliability: The reliance on timely delivery means that transportation disruptions can have a severe impact on production. Choosing reliable transportation providers and having backup plans in place is crucial.
-
Transportation Costs Calculation: A thorough cost-benefit analysis should be conducted to compare the overall costs of JIT, including transportation, against traditional inventory management systems.
The Importance of Accurate Forecasting
The success of JIT is heavily reliant on accurate demand forecasting. Inaccurate forecasting can lead to either excess inventory (defeating the purpose of JIT) or stockouts, both of which have negative consequences.
Forecasting Challenges
-
Demand Variability: Inaccurate forecasting is particularly problematic in industries with fluctuating demand patterns. Overestimating demand results in excess inventory, while underestimating demand leads to stockouts.
-
Seasonality: Seasonal fluctuations in demand can make accurate forecasting more challenging. Businesses need to incorporate seasonal factors into their forecasting models.
-
External Factors: External factors like economic downturns, changes in consumer preferences, or technological advancements can significantly impact demand and make accurate forecasting difficult.
Need for Highly Skilled Workforce
JIT requires a highly skilled and adaptable workforce. Employees need to be proficient in problem-solving, continuous improvement, and efficient workflow management. Lack of training and skill development can hinder the successful implementation of JIT.
Workforce Needs
-
Cross-Training: Employees need to be cross-trained to perform multiple tasks, as the system demands flexibility and adaptability.
-
Problem-Solving Skills: The ability to quickly identify and resolve problems is essential in a system with minimal buffer stock.
-
Communication and Collaboration: Effective communication and collaboration within the team and with suppliers are critical for smooth operations.
High Risk of Quality Issues
While JIT aims to minimize waste, the pressure to maintain a continuous flow of materials can increase the risk of quality issues. A rush to meet deadlines can lead to shortcuts in quality control, resulting in defective products or increased scrap rates. This is especially true if suppliers also operate under tight deadlines.
Quality Control Challenges
-
Supplier Quality Control: Relying on timely deliveries necessitates a very high degree of confidence in supplier quality control processes. Regular audits and inspections are crucial.
-
In-Process Quality Control: Robust in-process quality control procedures are essential to identify and rectify defects promptly, minimizing their impact on production.
-
Quality Assurance: A dedicated quality assurance team is necessary to monitor the entire process, from raw materials to finished goods, ensuring consistently high quality.
Conclusion: Balancing the Benefits and Drawbacks of JIT
Just-in-time manufacturing and inventory management offers significant advantages, including reduced inventory costs, improved efficiency, and less waste. However, it’s crucial to acknowledge and address the substantial downsides. The system’s vulnerability to supply chain disruptions, reliance on perfect supplier performance, and need for a highly skilled workforce necessitate careful planning, robust contingency plans, and a deep understanding of the potential risks. Before implementing JIT, businesses must thoroughly assess their capabilities, evaluate their supplier relationships, and establish robust systems for quality control, demand forecasting, and risk management. A successful JIT implementation depends on balancing the benefits with the inherent challenges and mitigating the potential pitfalls. Only then can a company truly harness the power of JIT to achieve its operational goals.
Latest Posts
Latest Posts
-
Which Of These Relationships Is True Of An Uncharged Atom
Apr 02, 2025
-
Nested Loop Java Ascll Art Pictures
Apr 02, 2025
-
The Last Dance Encountering Death And Dying
Apr 02, 2025
-
Which One Of The Following Is A Strong Base
Apr 02, 2025
-
A Benchmark Pe Ratio Can Be Determined Using
Apr 02, 2025
Related Post
Thank you for visiting our website which covers about What Is A Downfall To Just-in-time Manufacturing And Inventory Management . We hope the information provided has been useful to you. Feel free to contact us if you have any questions or need further assistance. See you next time and don't miss to bookmark.