The Yield Strength For An Alloy That Has An Average
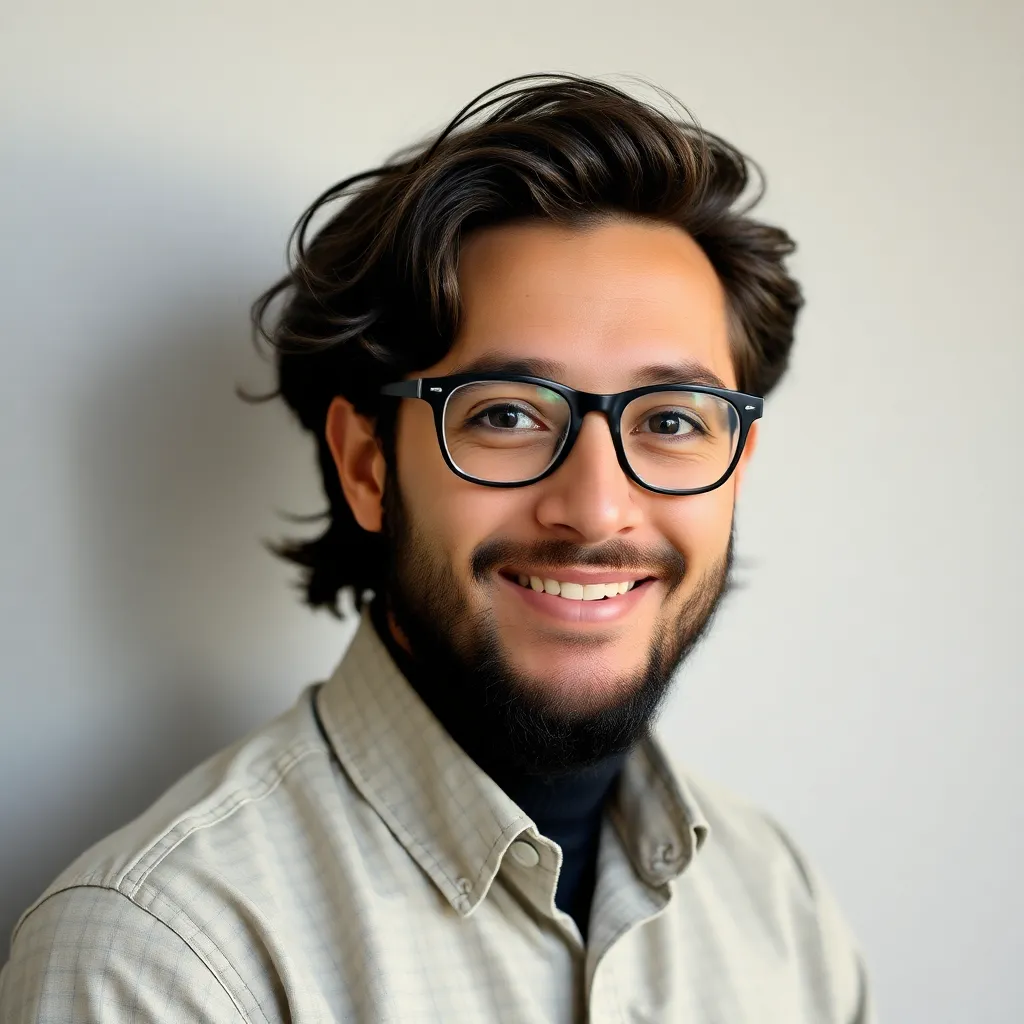
Holbox
Mar 28, 2025 · 6 min read
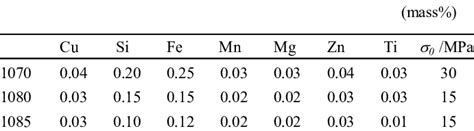
Table of Contents
- The Yield Strength For An Alloy That Has An Average
- Table of Contents
- Understanding Yield Strength in Alloys: A Comprehensive Guide
- What is Yield Strength?
- Defining Yield Strength: The 0.2% Offset Method
- Other Methods for Determining Yield Strength
- Factors Affecting Yield Strength in Alloys
- Composition: The Crucial Role of Alloying Elements
- Processing Techniques: Shaping the Mechanical Properties
- Temperature: The Temperature Dependence of Yield Strength
- Significance of Average Yield Strength
- The Impact of Testing Variability on Yield Strength
- Case Studies: Illustrating Yield Strength in Different Alloys
- Conclusion: The Indispensable Role of Yield Strength
- Latest Posts
- Latest Posts
- Related Post
Understanding Yield Strength in Alloys: A Comprehensive Guide
Yield strength is a crucial material property, especially when dealing with alloys. It represents the stress at which a material begins to deform plastically, meaning the deformation becomes permanent even after the stress is removed. Understanding the yield strength of an alloy is paramount for engineers and designers in ensuring structural integrity and safety in various applications. This comprehensive guide delves deep into the concept of yield strength, its determination, influencing factors, and the significance of average yield strength in alloy characterization.
What is Yield Strength?
Yield strength, often denoted as σ<sub>y</sub> or R<sub>e</sub>, is a measure of a material's resistance to plastic deformation. It signifies the point on a stress-strain curve where the material transitions from elastic behavior (where deformation is reversible) to plastic behavior (where deformation is permanent). This transition is not always abrupt, and several methods exist to define the yield strength depending on the material's behavior.
Defining Yield Strength: The 0.2% Offset Method
One common method for determining yield strength is the 0.2% offset method. This involves drawing a line parallel to the elastic portion of the stress-strain curve, offset by 0.2% strain. The intersection of this line with the stress-strain curve is defined as the yield strength. This method is particularly useful for materials that don't exhibit a clear yield point.
Other Methods for Determining Yield Strength
While the 0.2% offset method is widely used, other methods exist depending on the material and the desired accuracy:
- Proportional Limit: This is the stress up to which the stress-strain relationship is perfectly linear. However, this method is less precise and less commonly used as it's often difficult to accurately define the exact point of departure from linearity.
- Lower Yield Point and Upper Yield Point: Some materials, like mild steel, exhibit a clear yield point with a distinct upper and lower yield point. The lower yield point is often used as a measure of yield strength in such cases.
Factors Affecting Yield Strength in Alloys
Several factors significantly impact the yield strength of an alloy. Understanding these factors is critical in material selection and design.
Composition: The Crucial Role of Alloying Elements
The chemical composition of an alloy plays a pivotal role in determining its yield strength. Alloying elements are added to a base metal to improve its properties, often including yield strength. These additions can affect yield strength through several mechanisms:
- Solid Solution Strengthening: The addition of solute atoms into the base metal lattice distorts the lattice structure, hindering dislocation movement and thereby increasing yield strength. This is particularly effective when the solute atom size is significantly different from the solvent atom.
- Precipitation Hardening: Introducing precipitates within the alloy matrix can effectively impede dislocation movement, leading to a significant increase in yield strength. This process involves carefully controlling the precipitation of secondary phases during heat treatment.
- Grain Boundary Strengthening: Reducing the grain size of the alloy strengthens the material. Smaller grains create more grain boundaries, which act as barriers to dislocation motion. This is known as the Hall-Petch relationship, where yield strength is inversely proportional to the square root of the grain size.
Processing Techniques: Shaping the Mechanical Properties
The manufacturing and processing techniques used to create the alloy also strongly influence its yield strength:
- Cold Working (Strain Hardening): Deforming the alloy at room temperature introduces dislocations, leading to increased strength and hardness but reduced ductility.
- Heat Treatment: Different heat treatments, such as annealing, quenching, and tempering, significantly alter the microstructure of the alloy and thus its mechanical properties, including yield strength. Annealing softens the alloy, while quenching and tempering can increase yield strength.
Temperature: The Temperature Dependence of Yield Strength
Temperature has a substantial effect on the yield strength of alloys. Generally, yield strength decreases with increasing temperature. At higher temperatures, atomic vibrations increase, leading to easier dislocation movement and a reduction in strength.
Significance of Average Yield Strength
The average yield strength of an alloy is a statistically representative value obtained from multiple tensile tests. It’s crucial for several reasons:
- Design and Engineering Applications: Engineers use the average yield strength to design structures and components. A safety factor is often applied to account for variations in yield strength and other factors.
- Quality Control: The average yield strength provides a benchmark for quality control in the manufacturing process. Consistent average yield strength across batches indicates reliable production.
- Material Selection: Comparing the average yield strength of different alloys allows engineers to select the most appropriate material for a given application.
The Impact of Testing Variability on Yield Strength
It is crucial to recognize that the yield strength obtained from a single tensile test may not perfectly represent the true average yield strength of the alloy. Several sources of variability can impact the results:
- Specimen-to-Specimen Variation: Variations in the composition, microstructure, and processing of individual specimens can lead to differing yield strength values.
- Testing Equipment and Procedures: The accuracy and precision of the testing equipment and the consistency of testing procedures also influence the results.
- Environmental Factors: Temperature and humidity can influence the yield strength during testing.
To account for this variability, it is often necessary to conduct multiple tensile tests and determine the average yield strength along with the standard deviation or confidence interval. This provides a more reliable measure of the alloy's strength and helps characterize the inherent variability within the material.
Case Studies: Illustrating Yield Strength in Different Alloys
Let's consider a few examples of how yield strength is essential in different alloy applications:
- Aluminum Alloys in Aerospace: Aluminum alloys with high yield strengths are critical in aerospace applications due to their lightweight yet robust nature. The average yield strength is carefully controlled to ensure safety and reliability in aircraft components. Variations in yield strength due to manufacturing processes are minimized through rigorous quality control measures.
- Steel Alloys in Construction: High-strength steel alloys with high average yield strengths are utilized in construction, offering structural integrity in buildings and bridges. Accurate determination of yield strength is crucial to ensure the structural stability and safety of these constructions. Variations in yield strength can be addressed by specifying the desired range in the alloy standards.
- Titanium Alloys in Biomedical Implants: Titanium alloys, with their biocompatibility and high yield strength, are frequently used in biomedical implants. Their average yield strength is carefully characterized to ensure the implants can withstand the stresses of the human body without failure. Variations are managed via rigorous selection and quality control processes.
Conclusion: The Indispensable Role of Yield Strength
Yield strength is a fundamental material property that plays a vital role in engineering design, quality control, and material selection. Understanding the factors that influence yield strength, the methods used to determine it, and the significance of average yield strength are crucial for ensuring the safety, reliability, and performance of engineered structures and components across various industries. By carefully considering the average yield strength along with the variability inherent in testing, engineers and designers can make informed decisions that lead to successful and robust designs. The continued research and development in material science and engineering further refine our understanding and control over the yield strength of alloys, contributing to advancements in various technological fields.
Latest Posts
Latest Posts
-
Moles And Chemical Formulas Lab Report Answers
Mar 31, 2025
-
Unspoken Language Is Another Way To Describe Communication
Mar 31, 2025
-
Choose The Best Lewis Structure For Xei2
Mar 31, 2025
-
Which Of These Is Not A Product Of Glycolysis
Mar 31, 2025
-
Which Of The Following May Indicate A Potential Drug Overdose
Mar 31, 2025
Related Post
Thank you for visiting our website which covers about The Yield Strength For An Alloy That Has An Average . We hope the information provided has been useful to you. Feel free to contact us if you have any questions or need further assistance. See you next time and don't miss to bookmark.