The Optimum Level Of Inspection Is Where The:
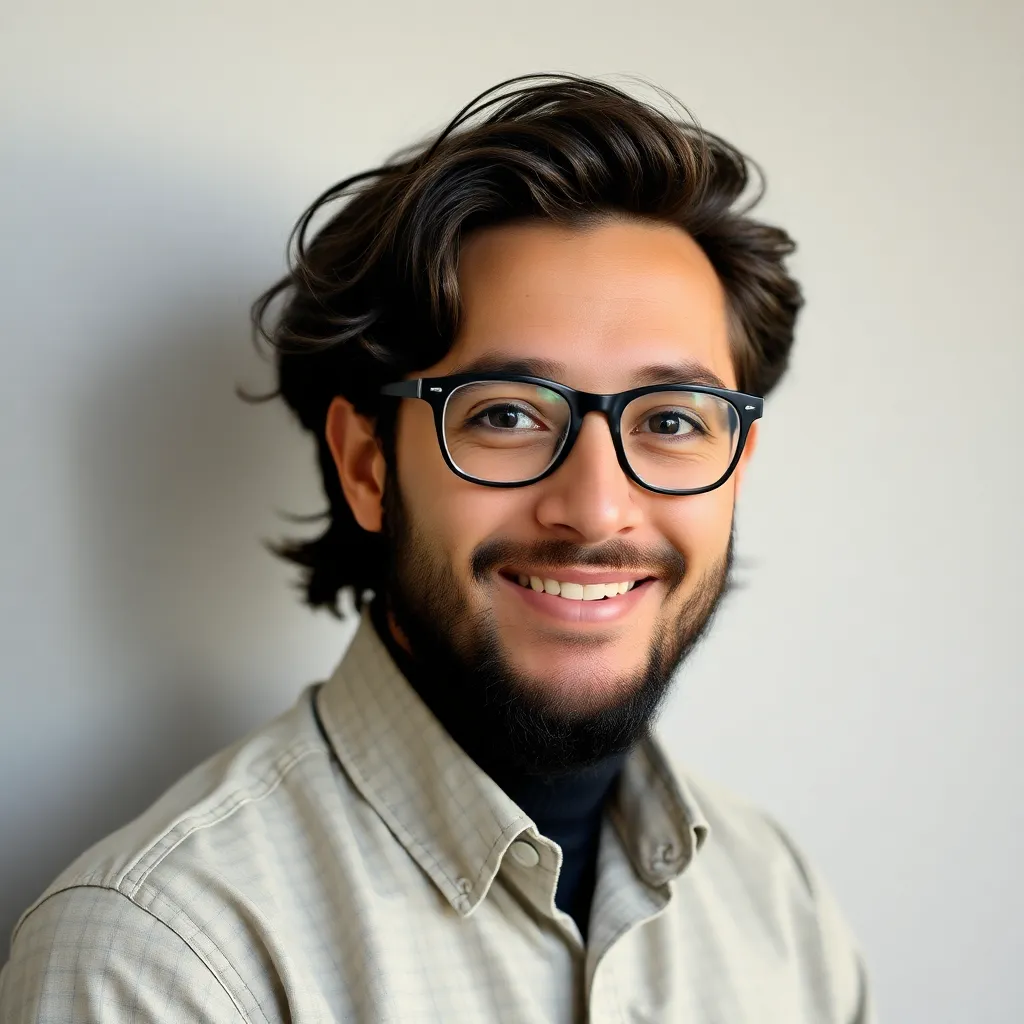
Holbox
Mar 28, 2025 · 5 min read
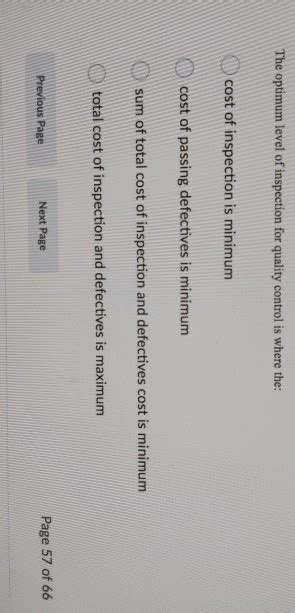
Table of Contents
- The Optimum Level Of Inspection Is Where The:
- Table of Contents
- The Optimum Level of Inspection: Where the Cost of Inspection Meets the Cost of Defects
- Understanding the Costs Involved
- 1. Cost of Inspection:
- 2. Cost of Defects:
- Methods for Determining the Optimum Level of Inspection
- 1. Cost-Benefit Analysis:
- 2. Statistical Process Control (SPC):
- 3. Acceptance Sampling Plans:
- 4. Risk-Based Inspection:
- Factors Influencing the Optimum Level of Inspection
- Implementing and Monitoring the Optimum Level of Inspection
- Conclusion: A Continuous Pursuit of Balance
- Latest Posts
- Latest Posts
- Related Post
The Optimum Level of Inspection: Where the Cost of Inspection Meets the Cost of Defects
The quest for the perfect balance between thorough inspection and efficient resource allocation is a constant challenge across numerous industries. Determining the optimum level of inspection—the point where the cost of inspection equals the cost of defects—is crucial for maximizing profitability and minimizing risks. This seemingly simple equation, however, involves a complex interplay of factors that require careful consideration. This article delves deep into understanding this crucial balance, exploring various inspection methods, cost analysis techniques, and the critical role of risk assessment in achieving the optimum level of inspection.
Understanding the Costs Involved
Before diving into methodologies for determining the optimum level of inspection, it's crucial to clearly define the costs involved. These costs can be broadly categorized into:
1. Cost of Inspection:
This encompasses all expenses related to the inspection process itself. It includes:
- Labor costs: Salaries and wages of inspectors, including overtime and benefits.
- Equipment costs: Purchase, maintenance, and calibration of inspection equipment (e.g., measuring instruments, testing devices, X-ray machines).
- Materials costs: Consumables used during the inspection process (e.g., test fluids, cleaning agents).
- Administrative costs: Record-keeping, data analysis, and report generation.
- Downtime costs: Production losses due to time spent on inspection. This can be a significant factor if inspection interrupts the production flow.
2. Cost of Defects:
This refers to the financial consequences of allowing defective products to reach the market or further stages of production. It can be far more significant than the cost of inspection and includes:
- Scrap and rework costs: The expense of discarding or repairing defective products. This also includes the cost of the raw materials used to produce these defective products.
- Warranty costs: Expenses associated with repairing or replacing defective products under warranty. This includes labor, parts, and shipping costs.
- Liability costs: Legal fees, settlements, and damage to reputation resulting from defective products causing harm or injury.
- Loss of sales: Reduced customer satisfaction and loss of future sales due to product defects. This includes both direct loss of sales from defective products and loss of potential future business due to reputational damage.
- Recall costs: The significant expenses associated with retrieving defective products from the market. This can be extremely costly, including labor, transportation, and customer relations.
Methods for Determining the Optimum Level of Inspection
Several methods can be employed to determine the optimum level of inspection. These methods often involve a combination of statistical analysis and risk assessment:
1. Cost-Benefit Analysis:
This approach directly compares the cost of inspection with the cost of defects. By plotting the cost of inspection against the cost of defects at various inspection levels, a graph can be generated. The optimum level is where the combined cost (cost of inspection + cost of defects) is minimized. This involves careful data collection and analysis to accurately estimate the cost of defects at different inspection intensities. This method requires meticulous record-keeping to effectively determine the costs associated with both inspection and defects. Failing to accurately reflect these costs can lead to inaccurate results.
2. Statistical Process Control (SPC):
SPC utilizes statistical methods to monitor and control the production process, aiming to reduce defects before they occur. Control charts, such as X-bar and R charts, are used to track process variations. By identifying and addressing sources of variation, SPC can minimize the need for extensive inspection. This preventative approach is often more cost-effective than relying solely on post-production inspection. The effectiveness of SPC relies heavily on the accuracy and consistency of data collection. Outliers and inaccurate data can lead to misleading conclusions and ineffective process adjustments.
3. Acceptance Sampling Plans:
These plans define the sample size and acceptance criteria for a batch of products. The plan dictates the number of units to inspect from a batch and the maximum number of defective units allowed before rejecting the entire batch. Various sampling plans exist, offering varying levels of stringency, depending on the risk tolerance. These plans utilize statistical principles to balance the risk of accepting defective products with the cost of inspection. Selecting the appropriate sampling plan requires careful consideration of the acceptable level of risk and the cost implications of both acceptance and rejection of batches.
4. Risk-Based Inspection:
This approach prioritizes inspection based on the potential risk associated with different product components or processes. Components with high failure rates or significant consequences of failure are inspected more thoroughly than those with lower risks. This method is particularly effective when dealing with complex products or systems with varying risk profiles. Effective risk-based inspection requires a thorough understanding of the product, its intended use, and the potential consequences of failure. Accurate risk assessment is critical to ensuring resources are appropriately allocated.
Factors Influencing the Optimum Level of Inspection
Several factors influence the optimum level of inspection:
- Product complexity: More complex products typically require more rigorous inspection.
- Cost of defects: High-cost defects justify more extensive inspection.
- Production volume: High-volume production might warrant automated inspection methods to maintain efficiency.
- Inspection technology: Advances in inspection technology can reduce inspection costs and improve accuracy.
- Regulatory requirements: Industry regulations and standards may dictate minimum inspection requirements.
- Customer expectations: Customer demand for high quality can influence inspection levels.
- Historical data: Analysis of historical defect rates can inform future inspection strategies.
Implementing and Monitoring the Optimum Level of Inspection
Once the optimum level of inspection has been determined, it's essential to implement and continuously monitor the chosen strategy. This involves:
- Training and qualification: Ensuring that inspectors possess the necessary skills and training.
- Equipment maintenance: Regular maintenance and calibration of inspection equipment.
- Data collection and analysis: Accurate and timely data collection for performance monitoring.
- Process improvement: Continuously analyzing inspection results to identify areas for process improvement.
- Regular review: Periodically reviewing the effectiveness of the inspection strategy and adjusting as needed.
Conclusion: A Continuous Pursuit of Balance
Determining the optimum level of inspection is not a one-time event but rather a continuous process of balancing the cost of inspection against the cost of defects. By employing appropriate methodologies, considering relevant factors, and continuously monitoring the results, organizations can achieve the optimal balance, leading to improved product quality, reduced costs, and enhanced profitability. The key lies in a proactive and data-driven approach that adapts to changing circumstances and technological advancements, ensuring that the inspection process remains efficient and effective in safeguarding both product quality and financial resources. The pursuit of this balance is an ongoing journey requiring consistent attention and refinement.
Latest Posts
Latest Posts
-
Database File Maintenance Typically Involves Select All That Apply
Apr 01, 2025
-
Henry Is Working At The Hospital Information Desk
Apr 01, 2025
-
When It Comes To Management Issues Small Businesses
Apr 01, 2025
-
This Type Of Industry Is Classified As
Apr 01, 2025
-
Complete The Balanced Neutralization Equation For The Reaction Below
Apr 01, 2025
Related Post
Thank you for visiting our website which covers about The Optimum Level Of Inspection Is Where The: . We hope the information provided has been useful to you. Feel free to contact us if you have any questions or need further assistance. See you next time and don't miss to bookmark.