The Hydroelectric Turbine Shown In Fig
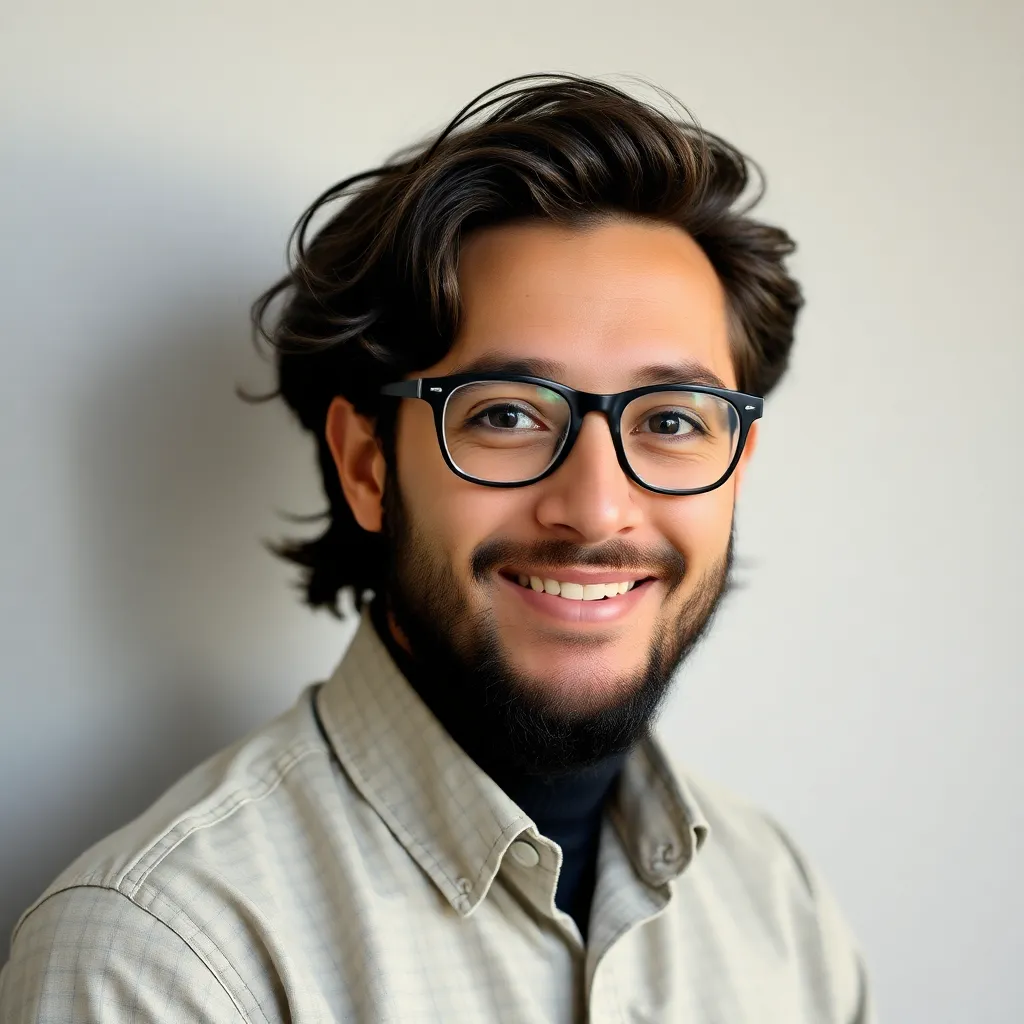
Holbox
Apr 26, 2025 · 7 min read
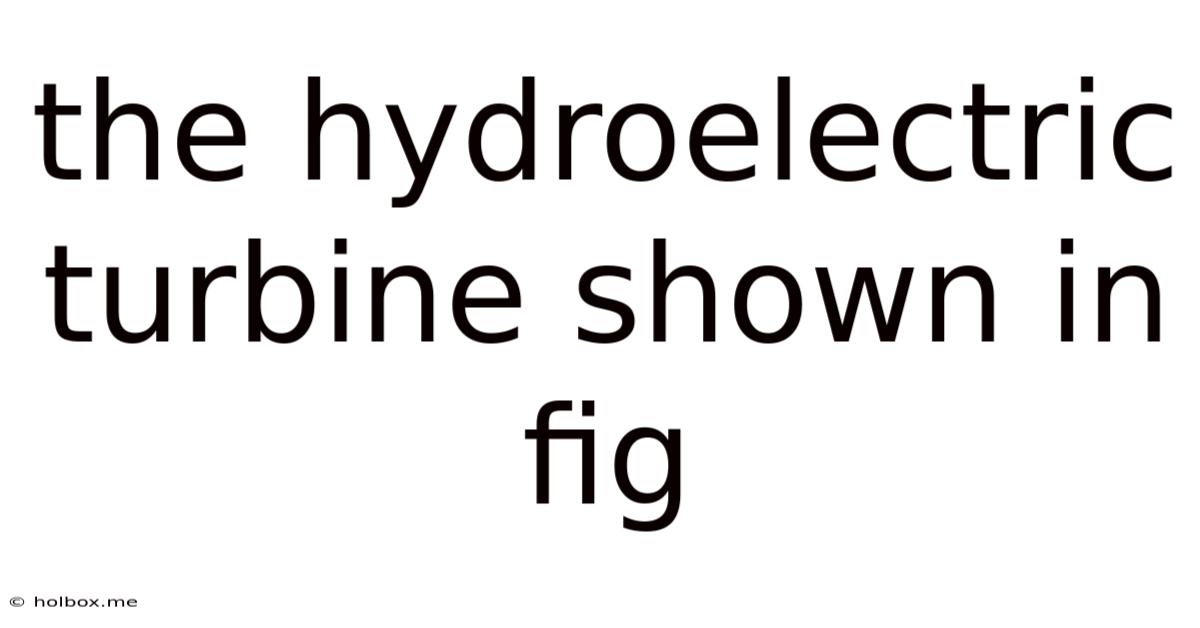
Table of Contents
- The Hydroelectric Turbine Shown In Fig
- Table of Contents
- Understanding Hydroelectric Turbines: A Deep Dive into Design, Operation, and Efficiency
- The Anatomy of a Hydroelectric Turbine
- 1. Runner: The Heart of the System
- 2. Casing: Providing Structural Integrity and Flow Control
- 3. Guide Vanes: Regulating Water Flow
- 4. Draft Tube: Energy Recovery and Efficient Discharge
- 5. Generator: Converting Mechanical Energy to Electrical Energy
- Types of Hydroelectric Turbines
- 1. Francis Turbine: Versatile and Widely Used
- 2. Kaplan Turbine: Ideal for Low-Head, High-Flow Applications
- 3. Pelton Turbine: High-Head, Low-Flow Specialist
- 4. Turgo Turbine: A Hybrid Approach
- 5. Bulb Turbine: Submerged Simplicity
- Efficiency Considerations in Hydroelectric Turbines
- 1. Hydraulic Efficiency: Minimizing Energy Losses
- 2. Mechanical Efficiency: Reducing Friction and Wear
- 3. Generator Efficiency: Optimizing Electrical Power Output
- 4. Overall Efficiency: The Sum of its Parts
- Future Trends in Hydroelectric Turbine Technology
- 1. Advanced Materials: Enhanced Durability and Efficiency
- 2. Computational Fluid Dynamics (CFD): Optimized Designs
- 3. Smart Grid Integration: Optimized Power Management
- 4. Environmental Considerations: Sustainable Designs
- Conclusion
- Latest Posts
- Latest Posts
- Related Post
Understanding Hydroelectric Turbines: A Deep Dive into Design, Operation, and Efficiency
(Figure Placeholder: Imagine a detailed diagram or photograph of a hydroelectric turbine here. This would ideally show key components like the runner, casing, guide vanes, draft tube, etc.)
Hydroelectric power, a cornerstone of renewable energy, relies heavily on the efficient conversion of water's potential energy into electricity. At the heart of this process lies the hydroelectric turbine, a sophisticated machine that harnesses the kinetic energy of flowing water to rotate a generator, ultimately producing electricity. This article provides a comprehensive overview of hydroelectric turbines, delving into their design, operational principles, different types, efficiency considerations, and future trends.
The Anatomy of a Hydroelectric Turbine
A hydroelectric turbine, despite its variations in design, typically consists of several key components working in concert:
1. Runner: The Heart of the System
The runner, also known as the impeller, is the turbine's core component. It's a rotor with a series of blades designed to capture the kinetic energy of the water jet. The shape and arrangement of these blades are crucial to the turbine's efficiency and performance characteristics. The runner's rotation drives the generator, directly converting hydraulic power into mechanical power. The material selection for the runner is critical, considering factors such as water pressure, corrosive properties, and wear resistance. Common materials include stainless steel, cast iron, and composite materials.
2. Casing: Providing Structural Integrity and Flow Control
The casing encloses the entire turbine, providing structural support and directing the flow of water. It's designed to withstand the high pressure exerted by the water, ensuring the structural integrity of the entire system. The casing also houses the guide vanes and other essential components. Precision engineering and robust materials are essential to its construction to prevent leaks and ensure long-term durability.
3. Guide Vanes: Regulating Water Flow
Guide vanes are adjustable blades strategically positioned before the runner. Their primary function is to control the flow rate and direction of the water jet striking the runner blades. By adjusting the guide vane angle, the operator can precisely regulate the turbine's speed and power output. Precise control of the guide vanes is vital for efficient operation and preventing damage to the turbine.
4. Draft Tube: Energy Recovery and Efficient Discharge
The draft tube is a crucial component that connects the turbine outlet to the tailrace (the downstream channel). Its purpose is to recover some of the remaining kinetic energy in the water leaving the runner. By gradually expanding the cross-sectional area of the draft tube, the water velocity is reduced, converting kinetic energy back into pressure energy. This pressure recovery improves the overall efficiency of the turbine. The design of the draft tube is carefully optimized to minimize energy losses and maximize the pressure recovery.
5. Generator: Converting Mechanical Energy to Electrical Energy
The generator is directly connected to the turbine's shaft. As the runner rotates, it drives the generator, converting the mechanical energy into electrical energy. The type of generator used (e.g., synchronous or asynchronous) influences the overall performance and characteristics of the hydroelectric power plant. High-efficiency generators are critical to maximizing the plant's overall power output and minimizing energy losses.
Types of Hydroelectric Turbines
Hydroelectric turbines are categorized into different types depending on the head (water pressure) and flow rate. The optimal turbine type is selected based on the specific characteristics of the site:
1. Francis Turbine: Versatile and Widely Used
Francis turbines are arguably the most widely used type of hydroelectric turbine, suitable for medium-head applications (10-500 meters). They are characterized by a radial inflow design, where water enters the runner radially and exits axially. Their adaptability to varying head conditions and high efficiency makes them a popular choice for a wide range of hydroelectric power plants.
2. Kaplan Turbine: Ideal for Low-Head, High-Flow Applications
Kaplan turbines are designed for low-head, high-flow applications. They feature adjustable blades both on the runner and guide vanes, enabling efficient operation over a wide range of flow rates. This adaptability makes them suitable for river power plants where the flow rate fluctuates significantly. Their axial flow design contributes to their high efficiency in low-head scenarios.
3. Pelton Turbine: High-Head, Low-Flow Specialist
Pelton turbines are ideal for high-head, low-flow applications, commonly found in mountainous regions. They utilize a high-velocity jet of water that impinges on buckets or cups attached to the runner. This impact generates rotational force, driving the generator. Their simplicity and robustness make them suitable for remote locations with minimal maintenance access.
4. Turgo Turbine: A Hybrid Approach
Turgo turbines are a relatively newer type of impulse turbine, combining aspects of Pelton and tangential flow designs. They are suitable for medium-head applications and are known for their high efficiency and compact design. Their single-jet design simplifies construction and maintenance compared to multi-jet Pelton turbines.
5. Bulb Turbine: Submerged Simplicity
Bulb turbines are submerged units where the generator is integrated into the turbine casing, housed within a bulb-shaped structure. This design minimizes space requirements and is ideal for run-of-river installations. They are typically used in low-head applications with high flow rates.
Efficiency Considerations in Hydroelectric Turbines
The efficiency of a hydroelectric turbine is crucial to maximizing power generation and minimizing environmental impact. Several factors contribute to a turbine's overall efficiency:
1. Hydraulic Efficiency: Minimizing Energy Losses
Hydraulic efficiency represents the ratio of power transferred to the runner to the power available in the water jet. Losses can occur due to friction, turbulence, and inefficient blade design. Optimization of the runner and guide vane geometry is critical to maximizing hydraulic efficiency.
2. Mechanical Efficiency: Reducing Friction and Wear
Mechanical efficiency accounts for energy losses due to friction within the turbine's mechanical components (e.g., bearings, shafts). Regular maintenance and lubrication are crucial to minimizing these losses and maximizing efficiency. The selection of appropriate materials with low friction coefficients also plays a significant role.
3. Generator Efficiency: Optimizing Electrical Power Output
Generator efficiency relates to the conversion of mechanical energy from the turbine into electrical energy. High-efficiency generators with minimal losses are critical to maximizing overall plant output. Modern generator designs incorporate advanced technologies to enhance efficiency.
4. Overall Efficiency: The Sum of its Parts
The overall efficiency of a hydroelectric turbine is the product of its hydraulic, mechanical, and generator efficiencies. Maximizing each component's efficiency contributes to the overall efficiency of the power generation system. Regular monitoring and optimization of the turbine's performance are essential to maintain high overall efficiency.
Future Trends in Hydroelectric Turbine Technology
Ongoing research and development continuously strive to improve hydroelectric turbine efficiency and performance. Key trends include:
1. Advanced Materials: Enhanced Durability and Efficiency
The use of advanced materials such as composite materials and high-strength alloys is improving turbine durability and efficiency. These materials enable lighter, more robust designs, reducing mechanical losses and extending the lifespan of the turbine.
2. Computational Fluid Dynamics (CFD): Optimized Designs
CFD simulations are increasingly used to optimize turbine blade designs, minimizing energy losses and maximizing efficiency. These sophisticated simulations allow engineers to test different designs virtually, reducing the need for expensive and time-consuming physical prototypes.
3. Smart Grid Integration: Optimized Power Management
Integrating hydroelectric turbines with smart grids enables better power management and grid stability. The ability to adjust the turbine's power output in response to changing grid demands enhances the overall efficiency and reliability of the power system.
4. Environmental Considerations: Sustainable Designs
Growing environmental concerns are driving the development of more environmentally friendly hydroelectric turbine designs. This includes minimizing the environmental impact of construction and operation, reducing noise pollution, and preserving fish habitats.
Conclusion
Hydroelectric turbines are essential components of sustainable energy production, converting the power of flowing water into clean, renewable electricity. Understanding their design, operational principles, and efficiency considerations is crucial for maximizing their potential and contributing to a cleaner energy future. The ongoing advancements in turbine technology are paving the way for even more efficient and sustainable hydroelectric power generation, addressing the global energy demand while minimizing environmental impact. From the intricate design of the runner blades to the sophisticated control systems, every aspect of these remarkable machines is geared towards harnessing nature’s power effectively and efficiently. Further research and innovation in this field will continue to play a critical role in ensuring a sustainable energy supply for generations to come.
Latest Posts
Latest Posts
-
How Did Ronald Reagan Win Over The Religious Right
May 12, 2025
-
A List Of Community Piano Schools In The U S
May 12, 2025
-
Which Statement Is True Regarding Bsl1 And Bsl2 Laboratories
May 12, 2025
-
The Correlation Coefficient Is A Measure Of
May 12, 2025
-
Identify The Three Phases Of Mitosis In The Following Photomicrographs
May 12, 2025
Related Post
Thank you for visiting our website which covers about The Hydroelectric Turbine Shown In Fig . We hope the information provided has been useful to you. Feel free to contact us if you have any questions or need further assistance. See you next time and don't miss to bookmark.