The First Step In Applying Activity-based Costing Is
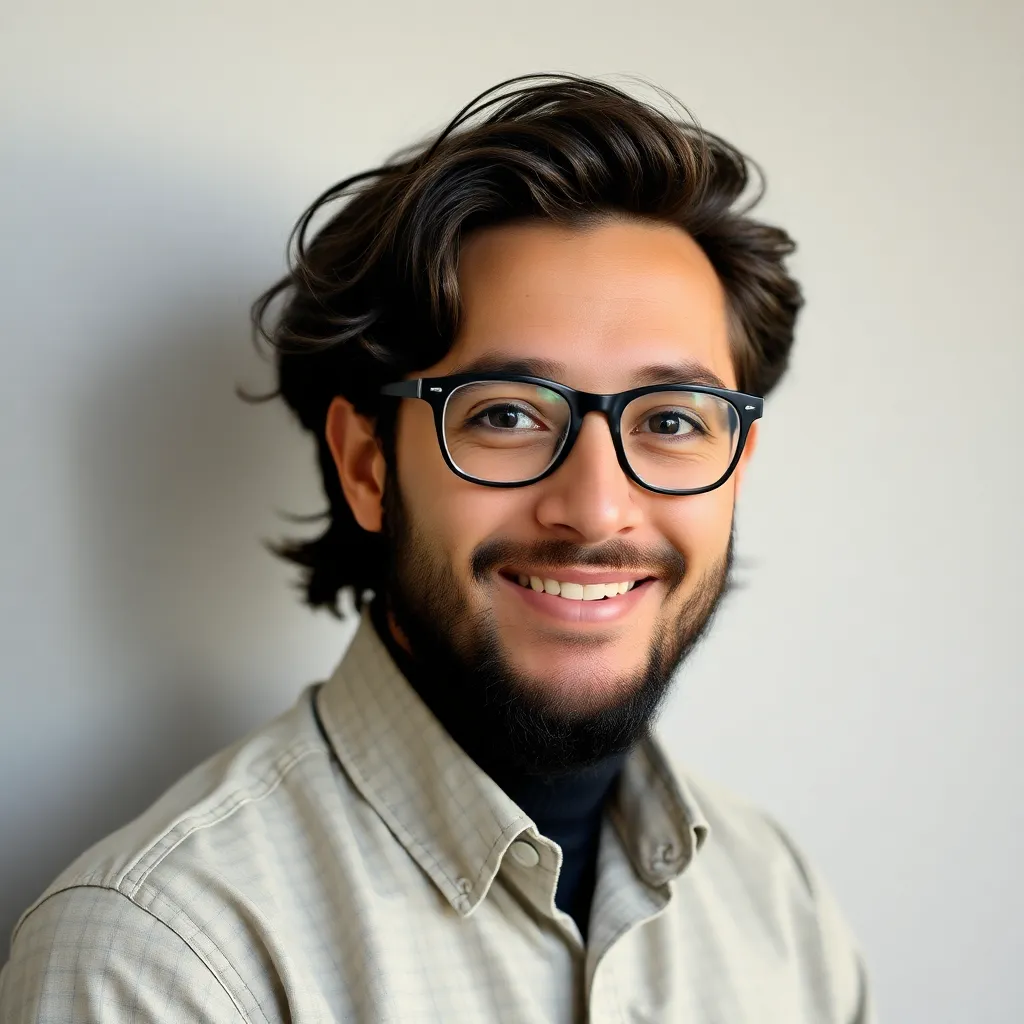
Holbox
Mar 20, 2025 · 6 min read
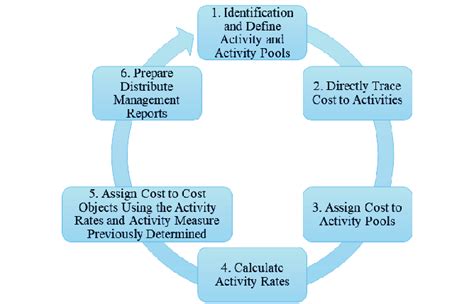
Table of Contents
The First Step in Applying Activity-Based Costing is: Identifying and Defining Activities
Activity-based costing (ABC) is a powerful costing method that moves beyond traditional approaches by focusing on the activities that drive costs. Unlike traditional costing systems that allocate overhead costs based on volume measures like machine hours or direct labor hours, ABC meticulously traces costs to specific activities and then assigns those costs to products or services based on their consumption of those activities. The accuracy and granularity offered by ABC provide businesses with significantly improved insights into their cost structure, leading to better pricing strategies, more efficient operations, and enhanced profitability. But before you can reap these benefits, you must take the crucial first step: identifying and defining activities.
Understanding the Foundation: Why Activity Identification is Paramount
The success of any ABC implementation hinges on the meticulous identification and precise definition of activities. This initial stage sets the stage for all subsequent steps. If activities are poorly defined or crucial activities are overlooked, the entire costing system will be flawed, leading to inaccurate cost allocations and ultimately, poor decision-making.
This step goes beyond simply listing tasks. It requires a deep understanding of the organization's operations, its value chain, and the resources consumed in producing its products or services. Think of it as creating a detailed blueprint of your business processes. Only with a comprehensive understanding of these activities can you accurately trace costs and understand where your money is truly being spent.
The Process of Identifying and Defining Activities: A Detailed Guide
Identifying and defining activities is an iterative process that often involves input from various departments and levels within the organization. Here's a step-by-step guide:
1. Start with a Broad Perspective: Mapping the Value Chain
Begin by examining the organization's overall value chain. This involves identifying all the key processes involved in delivering products or services to customers. Consider each stage, from raw material acquisition to product delivery and after-sales service. This broad overview helps you establish a framework for identifying more granular activities.
2. Conduct Interviews and Observations: Gathering First-hand Information
Don't rely solely on existing documentation. Conduct interviews with employees at all levels involved in the production process. These interviews should aim to understand not just what they do, but how they do it, the resources they utilize (materials, labor, equipment, etc.), and any bottlenecks or inefficiencies they encounter. Supplement these interviews with direct observation of the actual work being performed. This firsthand perspective is invaluable in identifying hidden or overlooked activities.
3. Document Activities: Creating a Comprehensive Activity List
Based on the information gathered from the value chain analysis and the interviews/observations, create a comprehensive list of all activities. Be as detailed as possible. Instead of a vague activity like "manufacturing," break it down into specific activities such as "machine setup," "material handling," "quality inspection," "assembly," and "packaging." The more specific you are, the more accurate your cost allocation will be.
4. Categorize Activities: Grouping Similar Activities Together
Once you have a comprehensive list, categorize activities into meaningful groups. This can be done by function (e.g., production, marketing, sales), by process (e.g., order fulfillment, product design), or by cost driver (e.g., machine hours, number of orders). This grouping simplifies the subsequent cost allocation process.
5. Define Activities Precisely: Establishing Clear Boundaries
For each activity, develop a clear and concise definition. Specify the inputs, outputs, and the resources consumed. Avoid ambiguity. For instance, instead of defining "machine setup" vaguely, describe it precisely: "The time spent preparing a machine for production, including changing tools, adjusting settings, and performing test runs." This level of detail prevents misinterpretations and ensures consistent cost allocation.
6. Identify Cost Drivers: Determining What Drives the Cost of Each Activity
This is a critical step. A cost driver is a factor that causes the cost of an activity to increase or decrease. For example, the cost driver for "machine setup" might be the number of setups, while the cost driver for "material handling" might be the number of material moves. Identifying cost drivers allows you to accurately allocate costs to products or services based on their consumption of activities.
Examples of Activities and Their Corresponding Cost Drivers
To illustrate the process, let's consider a manufacturing company producing two products: Product A and Product B. Here are some examples of activities and their potential cost drivers:
-
Activity: Machine Setup
- Cost Driver: Number of setups
- Product A: 10 setups
- Product B: 20 setups
-
Activity: Quality Inspection
- Cost Driver: Number of inspections
- Product A: 50 inspections
- Product B: 100 inspections
-
Activity: Material Handling
- Cost Driver: Number of material moves
- Product A: 100 moves
- Product B: 200 moves
-
Activity: Order Processing
- Cost Driver: Number of orders
- Product A: 50 orders
- Product B: 100 orders
-
Activity: Customer Service
- Cost Driver: Number of customer service calls
- Product A: 25 calls
- Product B: 75 calls
These examples demonstrate how different products consume activities at varying rates. This difference is critical in understanding the true cost of each product. Product B, for example, consumes more of almost every activity than Product A, indicating it may be more costly to produce despite traditional costing methods potentially suggesting otherwise.
Overcoming Challenges in Activity Identification
While the process seems straightforward, several challenges can arise during activity identification:
-
Resistance to Change: Employees may be resistant to the changes brought about by ABC implementation. Addressing concerns and providing training is crucial for success.
-
Data Collection Difficulties: Gathering accurate data on activity costs and consumption can be time-consuming and complex. Invest in robust data collection systems and processes.
-
Complexity: ABC can be a complex system, requiring significant upfront investment in time and resources. Start with a pilot project to test the system before full-scale implementation.
-
Subjectivity: Defining activities and identifying cost drivers can involve some subjectivity. Establish clear guidelines and involve multiple stakeholders to minimize bias.
The Importance of Continuous Improvement
Activity identification is not a one-time event. As the business evolves, new activities may emerge, existing activities may change, and cost drivers may shift. Regular review and refinement of the activity list and cost drivers are essential to ensure the accuracy and relevance of the ABC system. This iterative process ensures that the ABC system remains a valuable tool for managing costs and making informed business decisions.
Linking Activity Identification to Other ABC Steps
The identification and definition of activities is the cornerstone of the entire ABC process. It directly impacts the subsequent steps:
-
Cost Pool Assignment: Once activities are identified and categorized, costs are assigned to cost pools, which are groupings of similar activities.
-
Cost Driver Identification: As previously discussed, identifying cost drivers for each activity is crucial for accurate cost allocation.
-
Cost Allocation: Costs are allocated to products or services based on their consumption of activities and their associated cost drivers.
-
Cost Analysis and Decision Making: The resulting cost information is analyzed to identify areas for improvement and to support informed decision-making regarding pricing, product mix, and operational efficiency.
In conclusion, the first step in applying activity-based costing, identifying and defining activities, is not merely a procedural step; it is the foundation upon which the entire system is built. Its accuracy and comprehensiveness directly influence the reliability and value of the cost information generated, ultimately affecting the strategic decisions made by the organization. Therefore, meticulous planning, thorough data collection, and continuous refinement are essential for a successful ABC implementation. Ignoring this crucial first step can render the entire ABC process ineffective and ultimately, a waste of resources. By investing the necessary time and effort in this foundational step, businesses can unlock the significant benefits that activity-based costing offers.
Latest Posts
Latest Posts
-
The Norton Introduction To Literature 14th Edition
Mar 21, 2025
-
As It Relates To International Trade Dumping
Mar 21, 2025
-
Differentiate Y Sec I Tan I
Mar 21, 2025
-
Human Anatomy And Physiology Lab Manual
Mar 21, 2025
-
Sophia Operates Her Own Accounting Practice
Mar 21, 2025
Related Post
Thank you for visiting our website which covers about The First Step In Applying Activity-based Costing Is . We hope the information provided has been useful to you. Feel free to contact us if you have any questions or need further assistance. See you next time and don't miss to bookmark.