Simulation To Produce An Aggregate Plan
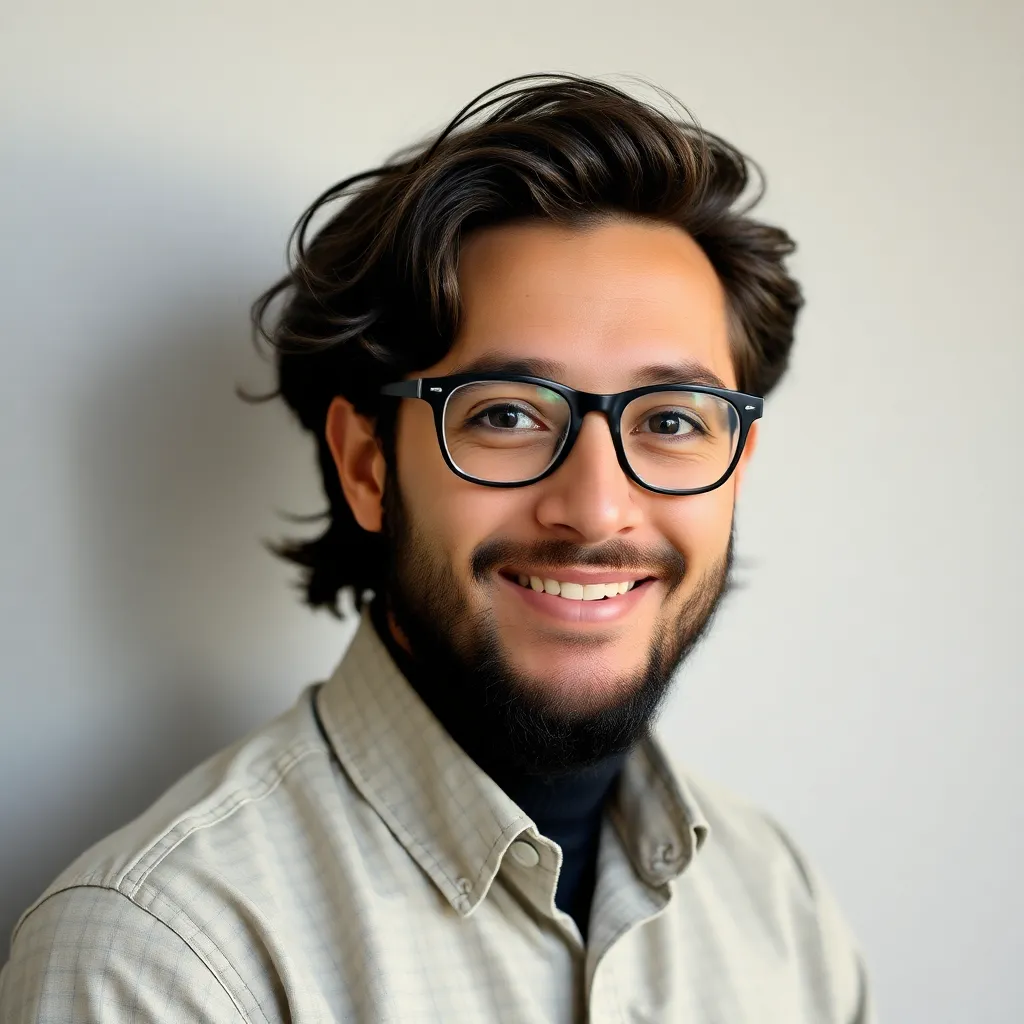
Holbox
Mar 27, 2025 · 6 min read
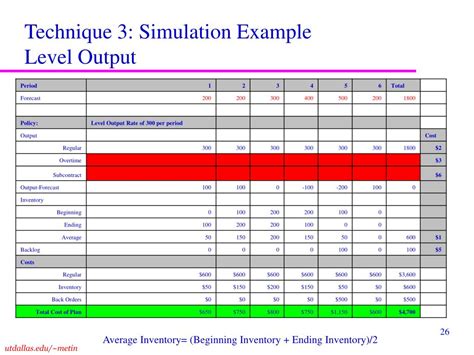
Table of Contents
- Simulation To Produce An Aggregate Plan
- Table of Contents
- Simulation to Produce an Aggregate Plan: A Comprehensive Guide
- Understanding Aggregate Planning and its Challenges
- The Power of Simulation in Aggregate Planning
- Types of Simulation Used in Aggregate Planning
- 1. Monte Carlo Simulation
- 2. Discrete Event Simulation (DES)
- 3. Agent-Based Simulation (ABS)
- Implementing Simulation for Aggregate Planning: A Step-by-Step Guide
- 1. Define the Problem and Objectives
- 2. Data Collection and Analysis
- 3. Model Development
- 4. Model Validation and Verification
- 5. Experimentation and Analysis
- 6. Implementation and Monitoring
- Software Tools for Simulation in Aggregate Planning
- Conclusion: Enhancing Aggregate Planning with Simulation
- Latest Posts
- Latest Posts
- Related Post
Simulation to Produce an Aggregate Plan: A Comprehensive Guide
Aggregate planning, the process of aligning supply and demand over the medium term (typically 3-18 months), is crucial for operational efficiency and profitability. While various techniques exist, simulation offers a powerful approach to explore different scenarios, evaluate trade-offs, and arrive at an optimal aggregate plan. This comprehensive guide delves into the application of simulation in aggregate planning, covering its advantages, methodologies, and implementation strategies.
Understanding Aggregate Planning and its Challenges
Aggregate planning aims to meet forecasted demand while optimizing resource utilization. Key decisions include:
- Production levels: Determining the quantity of goods to produce each period.
- Workforce levels: Adjusting the number of employees to match production needs.
- Inventory levels: Managing stock levels to balance carrying costs with stockout risks.
- Backordering: Accepting orders that can't be immediately fulfilled, leading to potential customer dissatisfaction.
- Subcontracting: Outsourcing production to external suppliers.
Traditional methods like linear programming often struggle with the inherent complexities of aggregate planning. These complexities include:
- Demand uncertainty: Forecasts are rarely perfectly accurate.
- Stochastic lead times: The time it takes to produce goods can vary.
- Resource limitations: Production capacity, workforce availability, and materials may be constrained.
- Multiple conflicting objectives: Balancing cost minimization, customer service level, and capacity utilization requires careful consideration.
The Power of Simulation in Aggregate Planning
Simulation, a technique for modeling and analyzing complex systems, overcomes many of these limitations. By mimicking the real-world operations of a business, simulation enables planners to:
- Assess risk: Evaluate the impact of uncertain demand, lead times, and other factors.
- Test different strategies: Compare the performance of various aggregate plans under various conditions.
- Optimize resource allocation: Identify the best combination of production levels, workforce sizes, and inventory strategies.
- Improve decision-making: Gain a better understanding of the system’s behavior and make more informed decisions.
- Visualize outcomes: Present results in a clear, understandable format, facilitating communication with stakeholders.
Types of Simulation Used in Aggregate Planning
Several simulation methodologies can be used in aggregate planning:
1. Monte Carlo Simulation
This probabilistic method involves generating random numbers to represent uncertain variables like demand. By repeating the simulation many times, a distribution of possible outcomes is generated, giving insights into the likelihood of different scenarios. For instance, you can simulate 1000 different demand scenarios and assess the performance of your aggregate plan under each. The resulting distribution will highlight the potential risks and rewards of your plan.
Advantages: Handles uncertainty effectively, provides a range of potential outcomes.
Disadvantages: Can be computationally intensive, requires careful selection of probability distributions for uncertain variables.
2. Discrete Event Simulation (DES)
DES models the system as a sequence of events occurring over time. These events might include the arrival of orders, completion of production runs, or changes in workforce levels. The simulation tracks the system's state as these events occur and updates variables like inventory levels and backorders accordingly. DES is particularly useful when modelling detailed operational processes.
Advantages: Can model complex systems with many interacting elements, provides detailed insights into system dynamics.
Disadvantages: Requires significant model building effort, can be computationally expensive for large-scale systems.
3. Agent-Based Simulation (ABS)
ABS models the system as a collection of autonomous agents that interact with each other and their environment. In aggregate planning, agents could represent individual customers, suppliers, or production facilities. This approach is especially valuable when modelling systems with complex interactions and emergent behavior. For example, ABS can model how changes in customer demand impact the entire supply chain and allow for the examination of supply chain resilience.
Advantages: Captures complex interactions between agents, suitable for modelling emergent behavior.
Disadvantages: Can be challenging to build and validate, requires significant computational resources.
Implementing Simulation for Aggregate Planning: A Step-by-Step Guide
The successful implementation of simulation for aggregate planning requires a systematic approach:
1. Define the Problem and Objectives
Clearly articulate the problem you are trying to solve and the objectives you hope to achieve. This might involve minimizing costs, maximizing customer service levels, or improving resource utilization. A well-defined problem statement is crucial for guiding the entire simulation process. For example, a clearly defined objective could be: "Minimize total cost while maintaining a 95% customer service level."
2. Data Collection and Analysis
Gather relevant historical data on demand, lead times, production capacity, and other relevant factors. Analyze this data to identify patterns, trends, and variability. This step is critical for accurate model calibration and validation. Data sources could include sales records, production logs, and supplier information.
3. Model Development
Construct a simulation model that accurately represents the system under consideration. This involves defining the system's components, their interactions, and the relationships between variables. The choice of simulation methodology will depend on the complexity of the system and the desired level of detail. Software packages like Arena, AnyLogic, or Simul8 are often used for this task.
4. Model Validation and Verification
Before using the model for decision-making, it's essential to validate and verify it. Validation ensures the model accurately represents the real-world system, while verification confirms that the model is internally consistent and free of errors. Techniques such as comparing simulation outputs to historical data or using expert judgment can help in this process.
5. Experimentation and Analysis
Run the simulation with different input parameters and aggregate planning strategies. Analyze the results to identify the optimal plan or range of plans that best achieve your objectives. This might involve using statistical techniques to compare the performance of different strategies and to quantify the uncertainty associated with the results. Sensitivity analysis should also be undertaken to see how changes to key inputs impact the outcome.
6. Implementation and Monitoring
Once the optimal aggregate plan is identified, implement it in your organization. Monitor the system's performance over time and make adjustments as needed. Continuously evaluating performance against predictions will allow for improvement of the model and greater accuracy of future simulations.
Software Tools for Simulation in Aggregate Planning
Several software packages facilitate simulation modeling, including:
- AnyLogic: A versatile platform supporting various simulation methodologies (agent-based, system dynamics, discrete event).
- Arena: A widely-used discrete event simulation software.
- Simul8: User-friendly software suitable for various simulation needs.
- MATLAB/Simulink: Powerful tools for modeling and simulation, often used for advanced applications.
Conclusion: Enhancing Aggregate Planning with Simulation
Simulation is a powerful technique for improving aggregate planning decisions. By considering uncertainty, testing multiple strategies, and optimizing resource allocation, simulation empowers businesses to achieve greater efficiency, profitability, and customer satisfaction. While implementing a simulation model requires effort and expertise, the benefits significantly outweigh the cost, particularly in complex and uncertain environments. By combining solid data analysis with appropriate software tools, organisations can significantly improve their aggregate planning processes. Remember to continuously refine your model and incorporate new data to maximize its effectiveness over time. The iterative nature of simulation makes it a valuable tool for continuous improvement.
Latest Posts
Latest Posts
-
Financial Wellness Includes A Persons Ability To
Mar 30, 2025
-
Select The Element Whose Lewis Symbol Is Correct
Mar 30, 2025
-
Draw The Major Organic Product Of The Bronsted Acid Base Reaction
Mar 30, 2025
-
State Statutory Law Is Created By
Mar 30, 2025
-
The First Step In Controlling Consists Of
Mar 30, 2025
Related Post
Thank you for visiting our website which covers about Simulation To Produce An Aggregate Plan . We hope the information provided has been useful to you. Feel free to contact us if you have any questions or need further assistance. See you next time and don't miss to bookmark.