The First Step In Controlling Consists Of
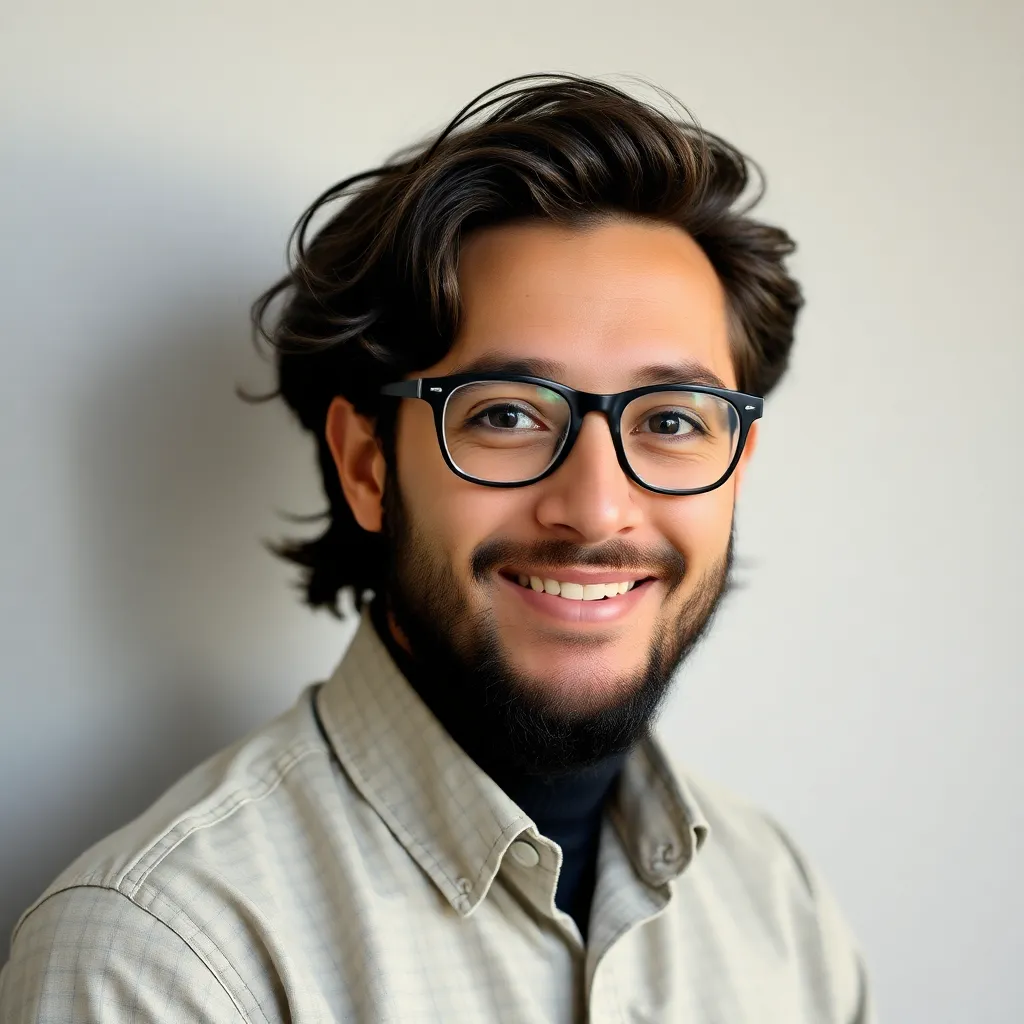
Holbox
Mar 30, 2025 · 6 min read

Table of Contents
- The First Step In Controlling Consists Of
- Table of Contents
- The First Step in Controlling Consists Of: Understanding and Defining the Controllable
- Defining the Scope of Control: What Are We Managing?
- Identifying Key Variables
- Establishing Benchmarks and Baselines
- The Importance of Measurability and Data Collection
- Data Collection Methods
- Data Analysis and Interpretation
- Implementing Control Mechanisms: Feedback Loops and Corrective Actions
- Feedback Loops: The Engine of Control
- Corrective Actions: Addressing Deviations
- Continuous Improvement: The Ongoing Nature of Control
- Adaptability and Flexibility
- Documentation and Record Keeping
- Examples of Control in Different Contexts
- Conclusion: The Foundation of Effective Control
- Latest Posts
- Latest Posts
- Related Post
The First Step in Controlling Consists Of: Understanding and Defining the Controllable
Controlling, in its broadest sense, encompasses the processes we use to ensure things happen as planned. Whether we're talking about managing a complex project, regulating a manufacturing process, or simply maintaining a healthy lifestyle, the fundamental principle remains the same: achieving desired outcomes through proactive monitoring and corrective action. However, before we even begin to control, there's a crucial preliminary stage that often gets overlooked: understanding and precisely defining what we're attempting to control. This first step lays the foundation for effective control and determines its ultimate success or failure.
Defining the Scope of Control: What Are We Managing?
This initial phase involves a thorough analysis of the system or process you intend to manage. What are the specific elements, variables, or outcomes you aim to influence? Vague goals lead to ineffective control mechanisms. Instead of aiming for "improved productivity," for instance, define specific, measurable, achievable, relevant, and time-bound (SMART) objectives. This might translate to "increase production output by 15% within the next quarter by implementing a new workflow."
Identifying Key Variables
Once you've established your overarching goal, break it down into its constituent parts. Identify the key performance indicators (KPIs) that reflect progress towards your objective. These KPIs are the variables you will actively monitor and control. For example, in the productivity improvement scenario:
- Number of units produced per hour: This quantifies direct output.
- Defect rate: Measures the quality of production.
- Employee absenteeism: Reflects potential workflow disruptions.
- Machine downtime: Indicates potential bottlenecks in the process.
Identifying these key variables provides a framework for establishing appropriate control measures. Ignoring crucial variables can lead to skewed results and ineffective control strategies.
Establishing Benchmarks and Baselines
Before attempting to control anything, you need a point of reference. Establish a baseline—the current state of the system or process before any interventions. This baseline provides a comparative measure for assessing the impact of your control efforts. For example, before implementing the new workflow, gather data on the current production output, defect rate, and other KPIs. This baseline data forms the foundation for evaluating the success of your control strategy.
Benchmarks are also crucial. These represent the target level of performance you aim to achieve. They can be internal (previous performance records) or external (industry averages, best practices). For instance, you might benchmark your target production output against the industry leader's performance. Establishing both baselines and benchmarks allows you to track progress, identify deviations, and adjust your control mechanisms accordingly.
The Importance of Measurability and Data Collection
Effective control hinges on the ability to measure and quantify progress. Your chosen KPIs must be objectively measurable and quantifiable. Qualitative assessments are helpful but are often subjective and less reliable for accurate control.
Data Collection Methods
Select appropriate data collection methods that align with your KPIs. This might include:
- Direct observation: Observing the process firsthand.
- Data logging: Automatically recording data from machines or systems.
- Surveys and questionnaires: Gathering feedback from employees or customers.
- Performance reports: Analyzing existing operational data.
The choice of method depends on the nature of the system, the resources available, and the accuracy required. Regardless of the method, ensure your data collection process is consistent, reliable, and free from bias.
Data Analysis and Interpretation
Collected data is useless without proper analysis. Utilize appropriate statistical techniques or data visualization tools to interpret the data and identify trends, patterns, and deviations from benchmarks. This analysis reveals areas where corrective action is necessary. For example, if the defect rate consistently exceeds the benchmark, it indicates a need to investigate the root cause and implement corrective measures.
Implementing Control Mechanisms: Feedback Loops and Corrective Actions
With a clear understanding of what's being controlled, a baseline established, and data consistently collected and analyzed, it's time to implement control mechanisms. These mechanisms are the tools and processes you use to influence the system and steer it towards the desired outcome.
Feedback Loops: The Engine of Control
A critical element of effective control is the feedback loop. This is the process of constantly monitoring the system, comparing its performance against established benchmarks, and taking corrective action when deviations occur. Feedback loops ensure continuous improvement and adaptation.
- Monitoring: Regular and systematic observation of KPIs.
- Comparison: Comparing actual performance against targets.
- Correction: Implementing actions to address deviations.
The frequency of monitoring and the sensitivity of the feedback loop depend on the nature of the system and the criticality of the controlled variables. A high-risk system, such as a nuclear reactor, requires much more frequent monitoring and immediate corrective action than, say, a routine office task.
Corrective Actions: Addressing Deviations
When deviations from the benchmark occur, prompt and appropriate corrective actions are crucial. This requires identifying the root cause of the deviation, not just treating the symptoms. For instance, if the production output is below target, don't just push employees harder. Investigate potential bottlenecks, equipment malfunctions, or training needs. Corrective actions might include:
- Process adjustments: Modifying the workflow or production methods.
- Technological upgrades: Investing in new equipment or software.
- Training and development: Improving employee skills and knowledge.
- Resource allocation: Redirecting resources to address bottlenecks.
Effective corrective actions are data-driven and implemented with a clear understanding of the cause-and-effect relationship.
Continuous Improvement: The Ongoing Nature of Control
Control isn't a one-time event; it's an ongoing process of continuous improvement. Regular review of the control system itself is essential. This involves assessing the effectiveness of the chosen KPIs, the accuracy of the data collection methods, and the efficiency of the corrective actions.
Adaptability and Flexibility
The control system should be adaptable and flexible to accommodate changing circumstances. Market fluctuations, technological advancements, or unforeseen events may require adjustments to the control mechanisms. The ability to respond quickly and effectively to these changes is crucial for maintaining control.
Documentation and Record Keeping
Maintain thorough documentation of all aspects of the control process, including the definition of goals, the selection of KPIs, data collection methods, corrective actions, and the results achieved. This documentation is essential for evaluating the effectiveness of the control system and making informed decisions about future improvements.
Examples of Control in Different Contexts
The principles of control apply across diverse fields. Here are some examples:
- Manufacturing: Controlling production quality, output, and costs through statistical process control (SPC) and other quality management systems.
- Project management: Controlling project timelines, budgets, and resources through Gantt charts, critical path analysis, and progress reports.
- Financial management: Controlling expenses, revenues, and cash flow through budgeting, forecasting, and financial reporting.
- Healthcare: Controlling infection rates, patient outcomes, and resource allocation through quality assurance programs and performance monitoring.
- Personal development: Controlling diet, exercise, and stress levels to achieve health and wellness goals.
Conclusion: The Foundation of Effective Control
The first step in controlling any system or process lies in a comprehensive understanding and precise definition of what's being controlled. This includes identifying key variables, establishing baselines and benchmarks, and selecting appropriate data collection and analysis methods. By laying this foundation, you set the stage for effective control mechanisms, continuous improvement, and the achievement of your desired outcomes. Remember, effective control isn't about micromanagement; it's about proactive monitoring, intelligent adaptation, and data-driven decision-making to achieve consistent and predictable results. Failing to properly define and understand what you're attempting to control is setting yourself up for failure before you even begin.
Latest Posts
Latest Posts
-
Rank The Measurements In Order From Smallest To Largest
Apr 03, 2025
-
The Following Events Pertain To Super Cleaning Company
Apr 03, 2025
-
How Far Will You Travel Portfolio
Apr 03, 2025
-
If Muffins And Bagels Are Substitutes
Apr 03, 2025
-
Perfect Parties Inc Has Several Divisions
Apr 03, 2025
Related Post
Thank you for visiting our website which covers about The First Step In Controlling Consists Of . We hope the information provided has been useful to you. Feel free to contact us if you have any questions or need further assistance. See you next time and don't miss to bookmark.