Similarities Between Job-order Costing And Process Costing Include The
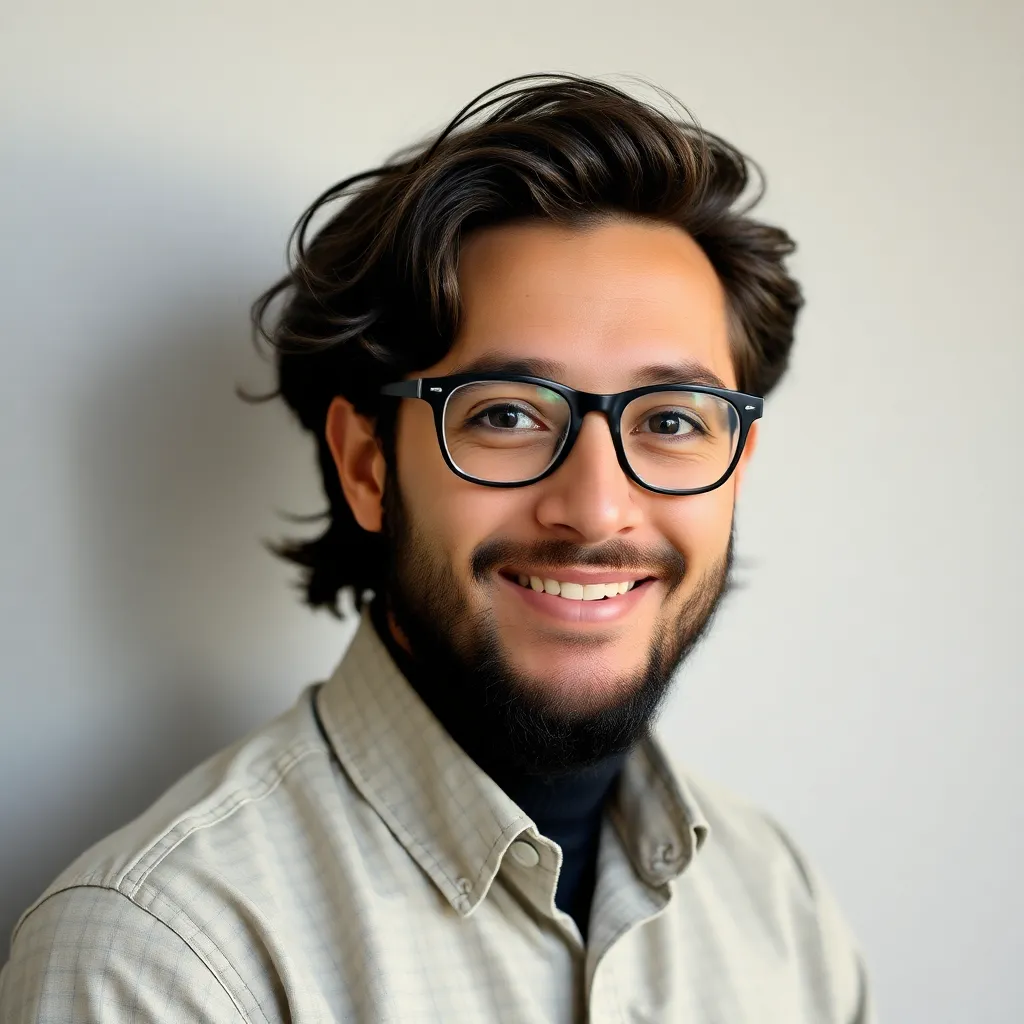
Holbox
Apr 25, 2025 · 5 min read
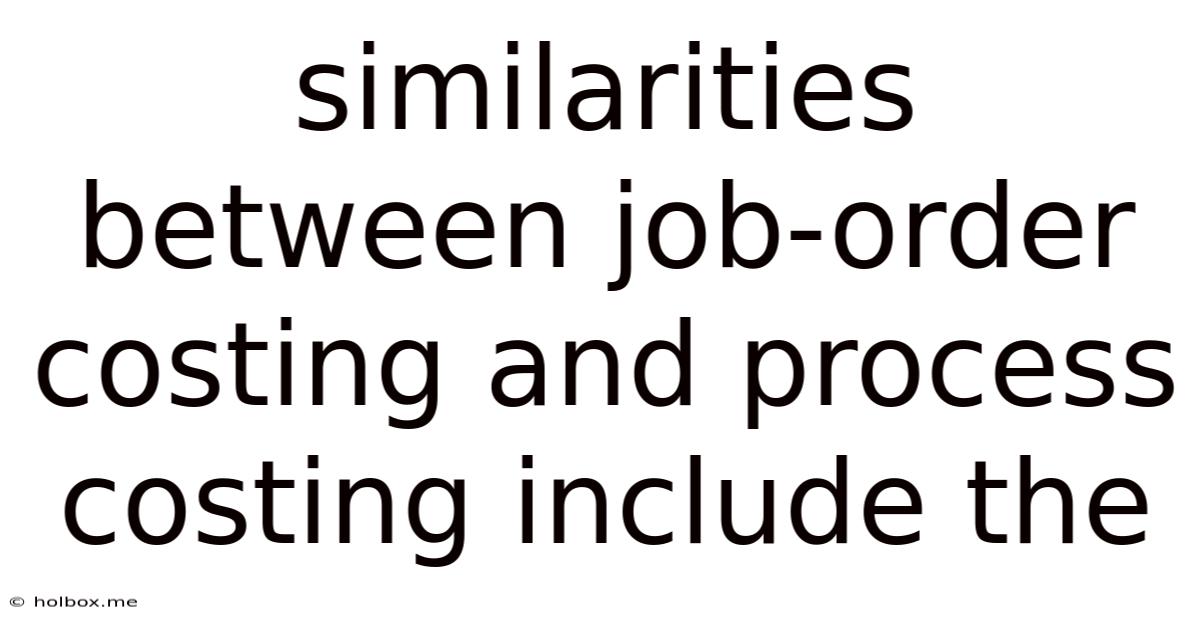
Table of Contents
- Similarities Between Job-order Costing And Process Costing Include The
- Table of Contents
- Similarities Between Job-Order Costing and Process Costing: A Deep Dive
- Fundamental Similarities: The Core Principles
- 1. Cost Accumulation: Tracking Direct and Indirect Costs
- 2. Cost Assignment: Linking Costs to Outputs
- 3. Cost Reconciliation: Ensuring Accuracy and Completeness
- 4. Inventory Valuation: Determining the Cost of Goods Sold and Inventory
- Deeper Dive into Similarities: Beyond the Basics
- 5. Cost Elements: Common Components Regardless of Methodology
- 6. Use of Predetermined Overhead Rates: Managing Indirect Costs
- 7. Cost Control and Efficiency Improvements: Shared Objectives
- 8. Management Decision-Making: Information for Strategic Planning
- Differences Despite Similarities: Understanding the Context
- Conclusion: A Holistic Perspective on Costing
- Latest Posts
- Latest Posts
- Related Post
Similarities Between Job-Order Costing and Process Costing: A Deep Dive
Job-order costing and process costing are two fundamental costing methods used in accounting to track the costs associated with producing goods or services. While they differ significantly in their application – job-order costing tracks costs for individual projects or jobs, while process costing tracks costs for mass-produced, homogenous products – they share several underlying similarities. Understanding these similarities helps businesses choose the appropriate costing method and gain a more comprehensive view of their cost structures.
Fundamental Similarities: The Core Principles
Both job-order costing and process costing are built upon the same fundamental accounting principles. These shared principles form the bedrock of their methodologies, even though their applications diverge significantly.
1. Cost Accumulation: Tracking Direct and Indirect Costs
At their core, both methods meticulously track and accumulate costs associated with production. This involves carefully recording both direct costs (directly attributable to a specific job or product, like raw materials and direct labor) and indirect costs (overhead costs, such as rent, utilities, and factory supervision, which are difficult to directly trace). The accuracy of cost accumulation is crucial for both systems, enabling businesses to make informed decisions regarding pricing, profitability, and operational efficiency.
Job-order costing assigns direct costs directly to specific jobs. Indirect costs are allocated to jobs using predetermined overhead rates, based on factors like machine hours or direct labor costs.
Process costing, on the other hand, aggregates direct and indirect costs for entire production processes. These costs are then allocated to units of output based on the number of units produced during the period.
2. Cost Assignment: Linking Costs to Outputs
The ultimate goal of both methods is to assign costs to the outputs – whether individual jobs or homogenous units. This assignment allows businesses to determine the cost per unit or per job, which is essential for pricing decisions and evaluating profitability.
Job-order costing clearly assigns costs to specific, identifiable jobs. The cost of a job is the sum of all direct materials, direct labor, and allocated overhead.
Process costing assigns the total cost of the production process to the total number of units produced. This results in a cost per unit, which reflects the average cost of production.
3. Cost Reconciliation: Ensuring Accuracy and Completeness
Both methods emphasize thorough cost reconciliation. This involves ensuring that all costs incurred during a period are accurately accounted for and allocated to either specific jobs or units of production. Any discrepancies require investigation to maintain the integrity of the costing system. Regular reconciliation helps identify potential inefficiencies or errors in cost tracking.
Job-order costing reconciles the costs of completed jobs with the work-in-process (WIP) inventory. This ensures that all costs associated with finished jobs are properly accounted for.
Process costing reconciles the costs of beginning and ending work-in-process inventory with the costs of units transferred to finished goods. This ensures the accurate tracking of costs through various stages of production.
4. Inventory Valuation: Determining the Cost of Goods Sold and Inventory
Accurate inventory valuation is critical for financial reporting. Both costing methods are used to determine the cost of goods sold (COGS) and the value of ending inventory, which directly impact a company’s financial statements.
Job-order costing directly assigns the cost of completed jobs to COGS. The cost of unfinished jobs remains in the WIP inventory account.
Process costing assigns the average cost per unit to the units sold (COGS) and the units remaining in inventory.
Deeper Dive into Similarities: Beyond the Basics
While the core principles form a strong foundation for comparison, a deeper examination reveals further subtle yet significant similarities between job-order costing and process costing.
5. Cost Elements: Common Components Regardless of Methodology
Both methods recognize and account for the same fundamental cost elements: direct materials, direct labor, and manufacturing overhead. The way these costs are tracked and allocated may differ, but their importance remains consistent across both systems. Analyzing these elements individually provides valuable insights into areas for potential cost reduction or improvement. Tracking and monitoring these components allows for effective cost management and performance evaluation.
6. Use of Predetermined Overhead Rates: Managing Indirect Costs
While the application varies, both methods often employ predetermined overhead rates to allocate indirect costs to production. This is crucial because indirect costs are difficult to track directly to specific jobs or units. Using a predetermined rate simplifies the process and avoids the complications of assigning overhead costs retrospectively. Regular review and adjustment of these rates ensure accuracy and relevance.
7. Cost Control and Efficiency Improvements: Shared Objectives
Both job-order and process costing are instrumental in achieving cost control and identifying opportunities for efficiency improvement. By meticulously tracking costs, businesses can pinpoint areas of inefficiency, optimize resource allocation, and enhance overall profitability. Regular cost analysis provides the data necessary for informed decision-making.
8. Management Decision-Making: Information for Strategic Planning
Both costing methods provide valuable data for managerial decision-making. The information generated is crucial for strategic planning, pricing strategies, and performance evaluation. This data-driven approach enables businesses to make informed choices and optimize their operations.
Differences Despite Similarities: Understanding the Context
While the similarities between job-order and process costing are considerable, their fundamental differences determine which method is suitable for a particular business. These differences primarily stem from the nature of the products or services being produced:
-
Job-order costing is best suited for businesses that produce unique or customized products, where each job or project has distinct characteristics. Examples include construction projects, custom furniture manufacturing, or specialized consulting services.
-
Process costing is ideally suited for businesses that produce large volumes of homogenous products using continuous or repetitive production processes. Examples include food processing, chemical manufacturing, or textile production.
Understanding these differences is vital for selecting the right costing method. Misapplication can lead to inaccurate cost information, potentially impacting profitability and strategic decision-making.
Conclusion: A Holistic Perspective on Costing
Both job-order costing and process costing, despite their contrasting applications, are rooted in shared fundamental principles. Recognizing these similarities offers a more holistic understanding of cost accounting and its vital role in business management. While the methods differ in their practical implementation, the ultimate goal remains the same: accurate cost tracking, efficient resource allocation, and informed decision-making for optimal business performance. By appreciating both the similarities and differences, businesses can select and effectively utilize the most appropriate costing method for their specific needs, ultimately achieving greater efficiency and profitability.
Latest Posts
Latest Posts
-
Which Of The Following Is A Lewis Acid
May 10, 2025
-
An Equipment Replacement Decision Under Incremental Analysis Requires
May 10, 2025
-
Case Study Touting The Benefits Of Business Analytics
May 10, 2025
-
Federal Sentencing Guidelines Established In 1991 Sought To
May 10, 2025
-
American Government In Black And White 5th Edition Pdf
May 10, 2025
Related Post
Thank you for visiting our website which covers about Similarities Between Job-order Costing And Process Costing Include The . We hope the information provided has been useful to you. Feel free to contact us if you have any questions or need further assistance. See you next time and don't miss to bookmark.