An Equipment Replacement Decision Under Incremental Analysis Requires
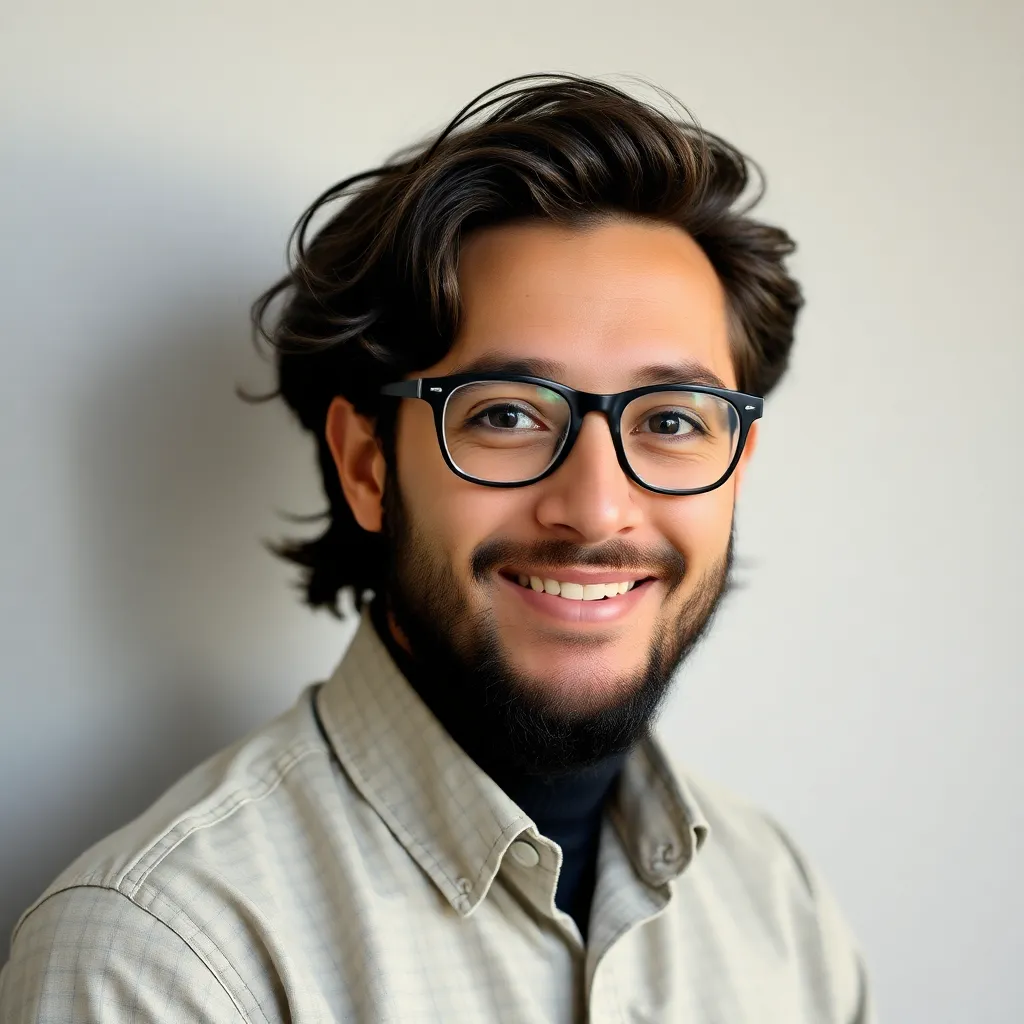
Holbox
May 10, 2025 · 6 min read
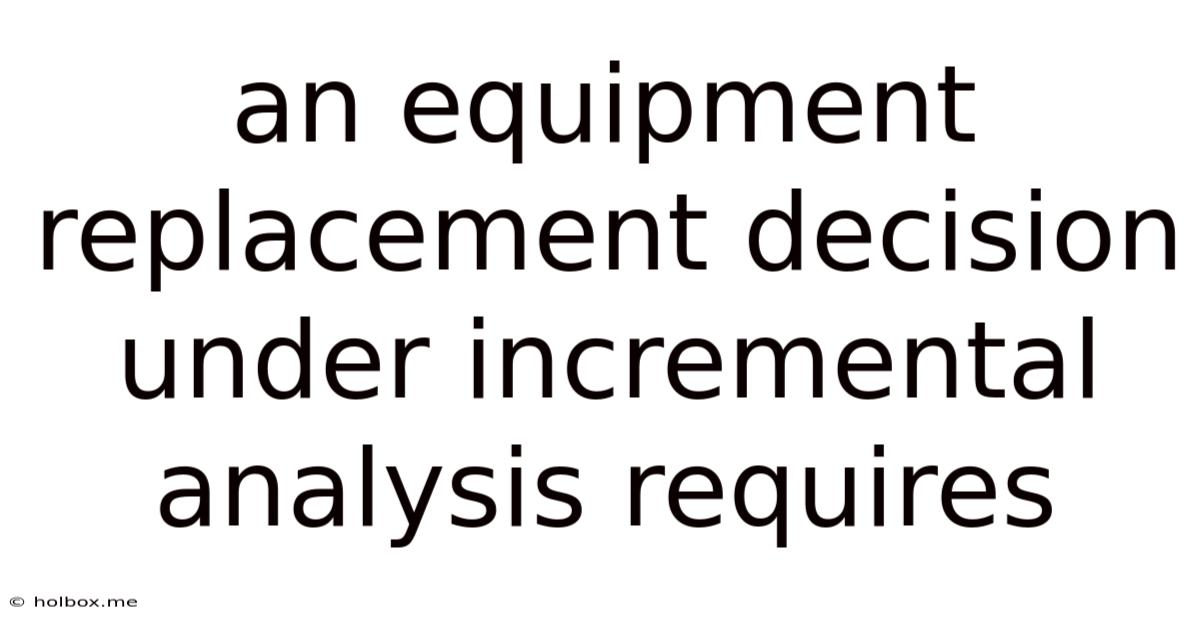
Table of Contents
- An Equipment Replacement Decision Under Incremental Analysis Requires
- Table of Contents
- Equipment Replacement Decision Under Incremental Analysis: A Comprehensive Guide
- Understanding Incremental Analysis in Equipment Replacement
- Key Factors in Equipment Replacement Decisions Using Incremental Analysis
- 1. Original Cost of the Old Equipment
- 2. Remaining Useful Life of the Old Equipment
- 3. Cost of the New Equipment
- 4. Useful Life and Salvage Value of the New Equipment
- 5. Operating Costs of the New and Old Equipment
- 6. Revenue Differences
- 7. Tax Implications
- Steps in Performing Incremental Analysis for Equipment Replacement
- 1. Define the Alternatives
- 2. Identify Relevant Costs and Benefits
- 3. Estimate Cash Flows
- 4. Discount Cash Flows
- 5. Calculate Net Present Value (NPV)
- 6. Compare NPVs
- 7. Consider Qualitative Factors
- Advanced Considerations in Incremental Analysis
- Sensitivity Analysis
- Scenario Planning
- Real Options
- Example of Incremental Analysis for Equipment Replacement
- Conclusion
- Latest Posts
- Related Post
Equipment Replacement Decision Under Incremental Analysis: A Comprehensive Guide
Equipment replacement decisions are crucial for maintaining operational efficiency and profitability in any business. These decisions, however, are rarely straightforward. They necessitate a careful evaluation of various factors, both financial and operational. Incremental analysis, a powerful decision-making tool, provides a structured framework for assessing the economic viability of replacing existing equipment. This article delves deep into the intricacies of equipment replacement decisions, focusing on the requirements and steps involved in using incremental analysis.
Understanding Incremental Analysis in Equipment Replacement
Incremental analysis, also known as differential analysis, focuses on the differences between alternatives rather than their absolute values. In the context of equipment replacement, it compares the costs and benefits of keeping the old equipment against the costs and benefits of acquiring new equipment. The core principle is to identify the incremental costs and benefits—that is, the changes in costs and benefits resulting from the decision to replace the equipment.
This approach is far more efficient and insightful than simply comparing the total costs of both alternatives. Total costs can be misleading, as they may include sunk costs (costs already incurred and irretrievable) that are irrelevant to the replacement decision. Incremental analysis helps you focus on the relevant costs and benefits that will influence your decision.
Key Factors in Equipment Replacement Decisions Using Incremental Analysis
Several factors need careful consideration when applying incremental analysis to an equipment replacement decision. These factors contribute to the overall cost and benefit calculation, ultimately guiding the decision-making process.
1. Original Cost of the Old Equipment
While the original cost of the old equipment is a sunk cost, its impact is felt indirectly. Its book value (original cost less accumulated depreciation) influences tax implications. Disposal of the old equipment may generate salvage value, which should be considered as an inflow in the analysis.
2. Remaining Useful Life of the Old Equipment
Accurately estimating the remaining useful life of the old equipment is crucial. This influences the calculation of depreciation expense, operating costs (maintenance, repairs), and potential revenue loss due to decreased efficiency or breakdowns.
3. Cost of the New Equipment
This includes the purchase price, installation costs, any necessary modifications, and potential training costs for personnel. Financing costs, such as loan interest, should also be factored into the incremental analysis.
4. Useful Life and Salvage Value of the New Equipment
Estimating the useful life of the new equipment is essential for determining its annual depreciation expense. The projected salvage value at the end of its useful life contributes to the overall financial assessment.
5. Operating Costs of the New and Old Equipment
A detailed comparison of operating costs for both the old and new equipment is fundamental. This includes direct costs like maintenance, repairs, energy consumption, and indirect costs like downtime and lost production. These costs should be estimated for the entire useful life of both options, discounted appropriately to reflect their present value.
6. Revenue Differences
The new equipment might lead to increased production, improved product quality, or reduced waste, resulting in higher revenue. Conversely, the old equipment might lead to decreased efficiency, higher defect rates, and ultimately reduced profitability. This revenue differential is a critical component of the incremental analysis.
7. Tax Implications
Depreciation, salvage value, and any capital gains or losses from the disposal of the old equipment all have tax implications. These tax effects need to be incorporated into the analysis, affecting the net cash flows associated with each option.
Steps in Performing Incremental Analysis for Equipment Replacement
The process of using incremental analysis for an equipment replacement decision involves several key steps:
1. Define the Alternatives
Clearly articulate the two alternatives: keeping the old equipment and replacing it with new equipment. This clarity provides a strong foundation for the subsequent analysis.
2. Identify Relevant Costs and Benefits
Carefully pinpoint the incremental costs and benefits associated with each alternative. Exclude irrelevant costs, such as sunk costs. This is a critical step to avoid confusion and inaccurate conclusions. Focus on quantifiable data whenever possible.
3. Estimate Cash Flows
Project the cash inflows and outflows associated with each alternative over their respective useful lives. This includes initial investment costs, operating costs, revenue, salvage value, and tax implications.
4. Discount Cash Flows
Due to the time value of money, future cash flows need to be discounted to their present value. A suitable discount rate, reflecting the company's cost of capital, should be utilized. This ensures that comparisons are made on an equivalent basis.
5. Calculate Net Present Value (NPV)
For each alternative, calculate the NPV by summing the discounted cash flows. A positive NPV suggests that the alternative adds value to the company, while a negative NPV indicates that it subtracts value.
6. Compare NPVs
Compare the NPVs of keeping the old equipment and replacing it with the new one. The alternative with the higher NPV is generally the preferred option.
7. Consider Qualitative Factors
While the NPV is a powerful quantitative measure, it's vital to consider qualitative factors as well. These include technological advancements, improved product quality, enhanced safety features, and improved employee morale. Sometimes, the qualitative advantages of new equipment might outweigh a slightly lower NPV.
Advanced Considerations in Incremental Analysis
While the basic steps outlined above provide a solid foundation, more advanced considerations can enhance the accuracy and comprehensiveness of the analysis:
Sensitivity Analysis
Conducting a sensitivity analysis examines how changes in key assumptions (e.g., discount rate, salvage value, operating costs) affect the NPV. This helps assess the robustness of the decision and identify critical uncertainties.
Scenario Planning
Developing different scenarios (optimistic, pessimistic, most likely) to reflect potential variations in future conditions can provide a more nuanced understanding of the potential outcomes.
Real Options
Incorporating real options analysis recognizes the flexibility inherent in equipment replacement decisions. For example, the option to upgrade or expand in the future can be valued and integrated into the overall analysis.
Example of Incremental Analysis for Equipment Replacement
Let's consider a simplified example. A company is deciding whether to replace an old machine (Machine A) with a new one (Machine B).
Item | Machine A (Keep) | Machine B (Replace) | Incremental Difference |
---|---|---|---|
Initial Investment | $0 | $100,000 | $100,000 |
Annual Operating Cost | $20,000 | $10,000 | -$10,000 |
Annual Revenue Increase | $0 | $15,000 | $15,000 |
Salvage Value | $5,000 | $20,000 | $15,000 |
Useful Life | 5 years | 5 years | |
Discount Rate | 10% | 10% |
By discounting these cash flows to their present value using a 10% discount rate and calculating the NPV for each scenario, a decision can be made based on the incremental NPV. A positive incremental NPV would favor replacing Machine A with Machine B.
Note: This is a simplified example. A real-world scenario would involve more detailed considerations, including tax implications, maintenance costs, and potential downtime.
Conclusion
Equipment replacement decisions are complex and require careful evaluation. Incremental analysis, with its focus on relevant costs and benefits, provides a structured framework for making informed decisions. By systematically considering all relevant factors, estimating cash flows, and employing appropriate discounting techniques, businesses can ensure that their equipment replacement decisions contribute to improved operational efficiency and profitability. Remember that while quantitative analysis like NPV is critical, qualitative factors should also inform the final decision. A thorough and well-executed incremental analysis significantly increases the chances of making the optimal equipment replacement decision.
Latest Posts
Related Post
Thank you for visiting our website which covers about An Equipment Replacement Decision Under Incremental Analysis Requires . We hope the information provided has been useful to you. Feel free to contact us if you have any questions or need further assistance. See you next time and don't miss to bookmark.