Regular Inspections Performed In Facilities Are Called
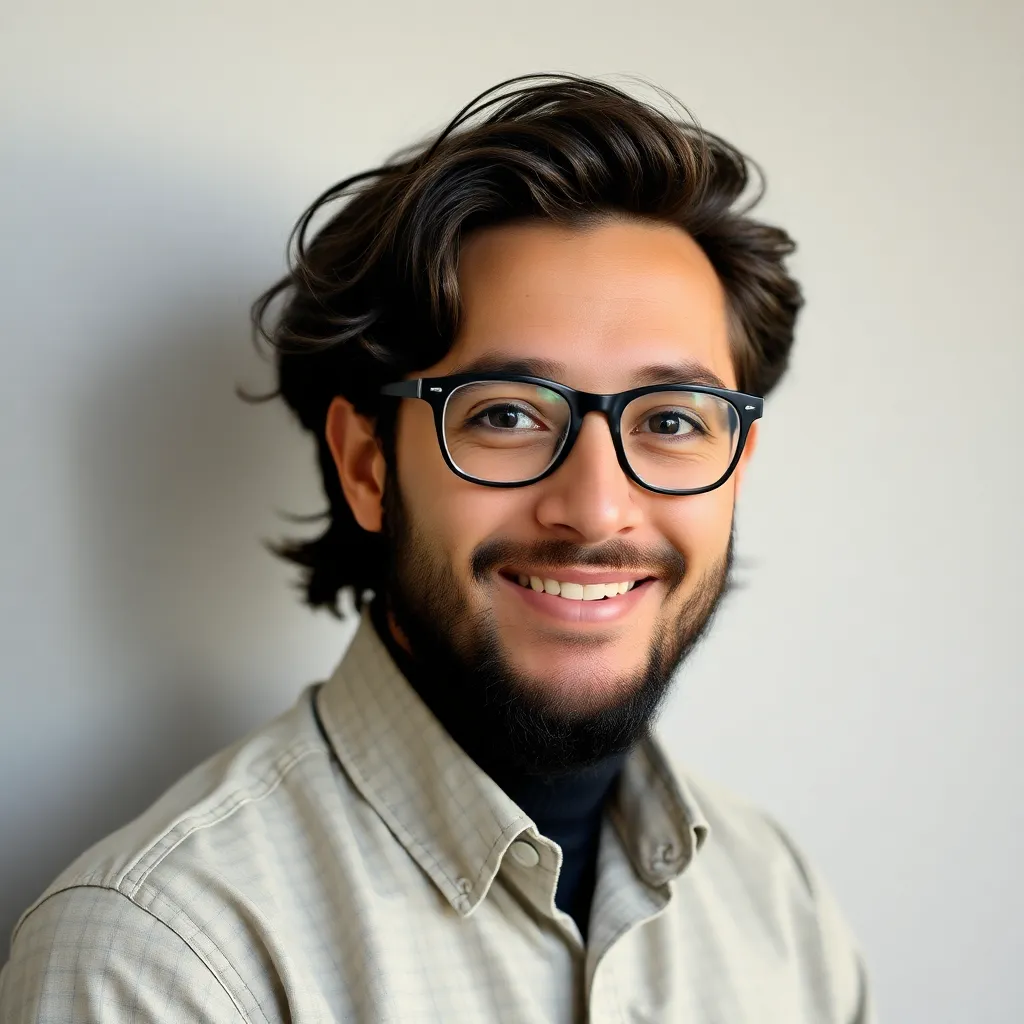
Holbox
Mar 23, 2025 · 6 min read
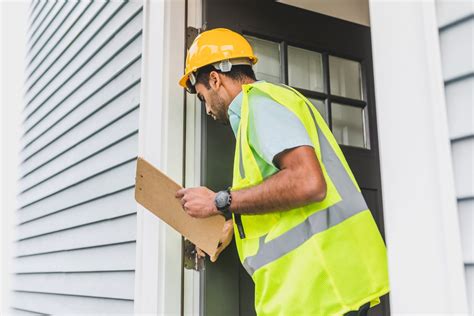
Table of Contents
- Regular Inspections Performed In Facilities Are Called
- Table of Contents
- Regular Inspections Performed in Facilities are Called: A Comprehensive Guide to Facility Management
- Understanding the Nomenclature: What are Regular Inspections Called?
- Types of Regular Inspections and Their Specific Names
- 1. Building Inspections: Assessing the Structure and Systems
- 2. Equipment Inspections: Maintaining Operational Efficiency
- 3. Safety Inspections: Prioritizing Risk Mitigation
- 4. Compliance Inspections: Ensuring Regulatory Adherence
- The Importance of Regular Inspections: A Holistic Approach to Facility Management
- Implementing an Effective Inspection Program: Key Considerations
- Conclusion: The Vital Role of Regular Inspections in Facility Success
- Latest Posts
- Latest Posts
- Related Post
Regular Inspections Performed in Facilities are Called: A Comprehensive Guide to Facility Management
Regular inspections are the cornerstone of effective facility management. They're not just about ticking boxes; they're about proactively identifying and mitigating risks, ensuring regulatory compliance, and maintaining a safe, productive, and efficient environment. But what are these inspections actually called? The terminology can vary depending on the industry, the type of facility, and the specific focus of the inspection. This comprehensive guide delves into the various names used, the different types of inspections, and the crucial role they play in overall facility success.
Understanding the Nomenclature: What are Regular Inspections Called?
There isn't one single universally accepted term for regular facility inspections. The names used often reflect the specific purpose or scope of the inspection. Here are some common terms you might encounter:
- Facility Inspections: This is a broad, encompassing term that covers a wide range of inspections. It's a general term that can be applied to most situations.
- Routine Inspections: This term highlights the regular and scheduled nature of the inspection. These are typically conducted at set intervals, such as daily, weekly, monthly, or annually.
- Preventive Maintenance Inspections: This term emphasizes the proactive nature of the inspection, aiming to prevent problems before they arise. These inspections focus on identifying potential issues and addressing them before they escalate into costly repairs or downtime.
- Safety Inspections: These inspections prioritize the identification and mitigation of safety hazards. This is often a key component of larger inspections but can also be a standalone inspection.
- Compliance Inspections: These inspections ensure the facility adheres to relevant regulations, codes, and standards. The frequency and scope of these inspections depend heavily on the industry and applicable laws.
- Regulatory Inspections: This is similar to compliance inspections but often refers to inspections conducted by external regulatory bodies, such as government agencies or industry associations.
- Periodic Inspections: Similar to routine inspections, this term highlights the scheduled nature of the inspections, indicating they occur at regular intervals.
- Quality Control Inspections: These inspections are focused on ensuring that the facility's operations meet established quality standards.
- Operational Inspections: These focus on the smooth and efficient functioning of the facility's systems and processes.
Types of Regular Inspections and Their Specific Names
The naming conventions often further specify the target area within the facility:
1. Building Inspections: Assessing the Structure and Systems
These encompass a broad range of checks focusing on the structural integrity, safety, and functionality of the building itself. This might include:
- Structural Inspections: Examining the building's foundation, walls, roof, and other structural elements for signs of damage or deterioration.
- Electrical Inspections: Checking wiring, circuits, outlets, and electrical equipment to ensure compliance with safety codes and prevent electrical hazards.
- Plumbing Inspections: Inspecting pipes, fixtures, drains, and water heaters to identify leaks, blockages, or other plumbing issues.
- HVAC Inspections: Reviewing heating, ventilation, and air conditioning systems to ensure proper functionality, energy efficiency, and safety.
- Fire Safety Inspections: Checking fire alarm systems, sprinkler systems, fire extinguishers, and emergency exits to ensure they are properly functioning and compliant with safety regulations.
2. Equipment Inspections: Maintaining Operational Efficiency
Regular inspections are crucial for maintaining the functionality and longevity of equipment. The specific names reflect the type of equipment:
- Machinery Inspections: For manufacturing facilities, regular inspections of machinery are essential for safety and productivity.
- Computer System Inspections: IT departments conduct regular inspections to ensure the smooth operation of computer systems, networking equipment, and data storage.
- Vehicle Inspections: Organizations with fleets of vehicles conduct regular inspections to maintain safety and compliance.
- Medical Equipment Inspections: Hospitals and clinics have rigorous inspection programs for medical devices to ensure accuracy, safety, and reliability.
3. Safety Inspections: Prioritizing Risk Mitigation
Safety inspections are paramount across all types of facilities. The focus is on identifying and addressing potential hazards:
- Workplace Safety Inspections: These are conducted to identify and eliminate hazards in the workplace, protecting employees from injury.
- Environmental Safety Inspections: These focus on compliance with environmental regulations and the prevention of pollution.
- Security Inspections: These inspections focus on access control, surveillance systems, and other security measures to protect the facility and its assets.
4. Compliance Inspections: Ensuring Regulatory Adherence
Compliance inspections are crucial for avoiding penalties and maintaining a positive reputation. The specific names often reflect the regulated industry:
- OSHA Inspections: In the United States, Occupational Safety and Health Administration (OSHA) inspections ensure workplace safety compliance.
- FDA Inspections: The Food and Drug Administration (FDA) conducts inspections of food processing plants and pharmaceutical facilities to ensure compliance with regulations.
- HIPAA Inspections: Healthcare facilities face regular HIPAA inspections to ensure compliance with the Health Insurance Portability and Accountability Act.
The Importance of Regular Inspections: A Holistic Approach to Facility Management
Regular inspections are not merely a legal requirement; they're a crucial component of a proactive and efficient facility management strategy. The benefits extend far beyond compliance:
- Cost Savings: Early detection of issues through regular inspections prevents minor problems from escalating into major, costly repairs. This is particularly true for things like HVAC systems, plumbing, and electrical systems. A small leak identified early can save thousands of dollars in water damage.
- Improved Safety: Regular safety inspections identify and mitigate potential hazards, creating a safer work environment for employees and visitors. This translates to lower insurance premiums and reduced liability risks.
- Enhanced Productivity: Well-maintained facilities contribute to increased employee productivity. A comfortable and functional work environment improves morale and efficiency.
- Extended Equipment Lifespan: Regular maintenance identified through inspections prolongs the lifespan of equipment, reducing replacement costs and minimizing downtime.
- Regulatory Compliance: Regular inspections ensure the facility complies with all applicable regulations and standards, avoiding potential penalties and legal issues.
- Better Risk Management: Proactive identification of risks through regular inspections allows for effective mitigation strategies, minimizing disruptions and protecting the facility's assets.
Implementing an Effective Inspection Program: Key Considerations
Establishing a robust and effective inspection program requires careful planning and execution:
- Develop a Comprehensive Inspection Checklist: Create detailed checklists that cover all aspects of the facility, equipment, and systems. These checklists should be tailored to the specific needs of the facility and its industry.
- Establish a Regular Inspection Schedule: Determine the frequency of inspections based on the criticality of different aspects of the facility. Some areas may require daily checks, while others might only need annual inspections.
- Assign Responsibilities: Clearly assign responsibility for conducting inspections and reporting findings.
- Utilize Inspection Software: Consider using inspection software to streamline the process, automate reporting, and track issues over time.
- Implement Corrective Actions: Establish a system for addressing issues identified during inspections promptly and effectively. This might involve assigning repairs, ordering replacement parts, or scheduling maintenance.
- Document All Inspections: Maintain detailed records of all inspections, including dates, findings, corrective actions, and follow-up activities. This documentation is crucial for demonstrating compliance and tracking progress over time.
- Train Inspection Personnel: Proper training ensures that inspection personnel have the knowledge and skills to identify potential issues and document findings accurately.
- Regularly Review and Update Inspection Procedures: The inspection program should be regularly reviewed and updated to reflect changes in regulations, technology, and best practices.
Conclusion: The Vital Role of Regular Inspections in Facility Success
Regular inspections, regardless of what they're called, are fundamental to successful facility management. They are a proactive strategy that ensures safety, compliance, efficiency, and cost-effectiveness. By implementing a well-planned and diligently executed inspection program, facilities can minimize risks, optimize operations, and create a productive and safe environment for everyone. The investment in time and resources is far outweighed by the long-term benefits, making regular inspections a crucial investment in the health and success of any facility.
Latest Posts
Latest Posts
-
A Supply Curve Slopes Upward Because
Mar 25, 2025
-
The Contribution Margin Ratio Is Interpreted As The Percent Of
Mar 25, 2025
-
Kirchoffs Loop Law Is Based On The Conservation Of
Mar 25, 2025
-
Historically Entrepreneurs In The United States
Mar 25, 2025
-
Which Of The Following Would Not Be Water Soluble
Mar 25, 2025
Related Post
Thank you for visiting our website which covers about Regular Inspections Performed In Facilities Are Called . We hope the information provided has been useful to you. Feel free to contact us if you have any questions or need further assistance. See you next time and don't miss to bookmark.