Iso 9000 Currently Stresses _____ Of A Certified Organization.
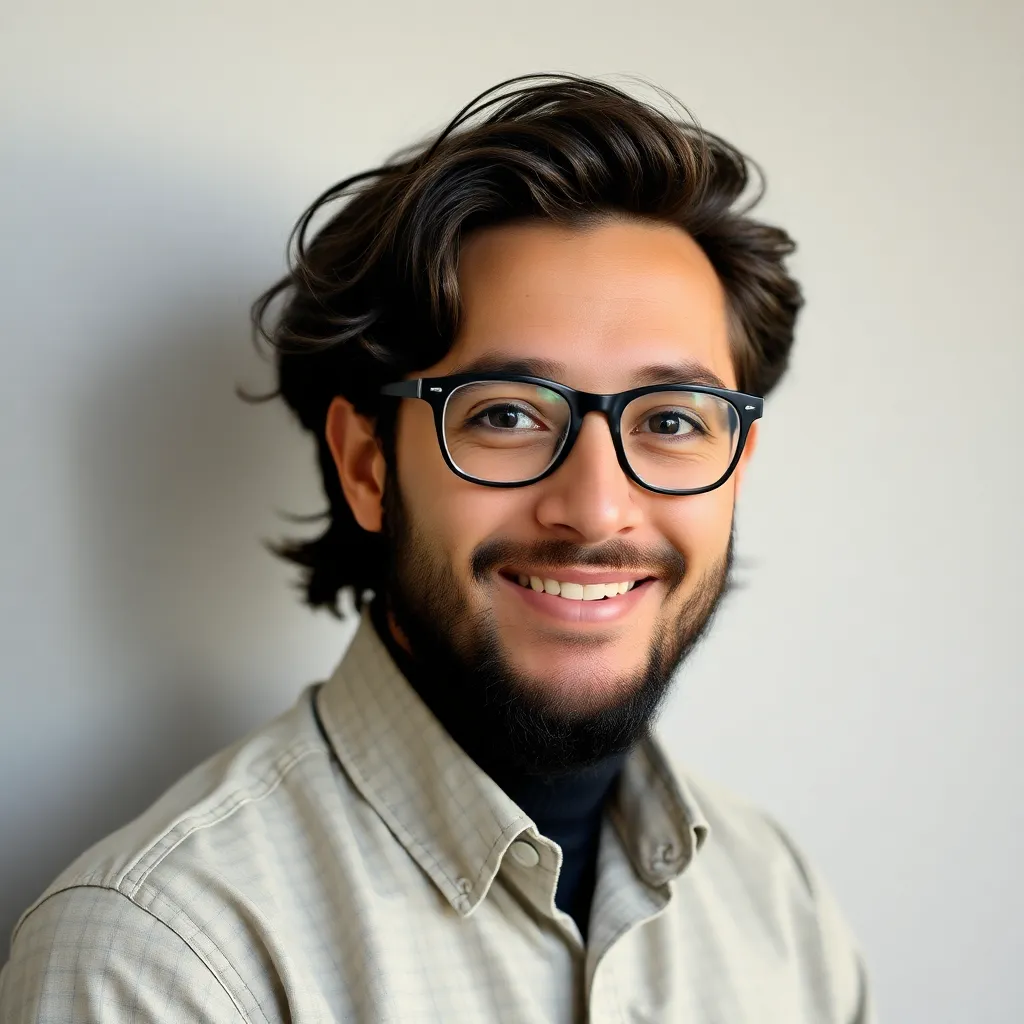
Holbox
Mar 28, 2025 · 6 min read

Table of Contents
- Iso 9000 Currently Stresses _____ Of A Certified Organization.
- Table of Contents
- ISO 9000 Currently Stresses Continuous Improvement of a Certified Organization
- Understanding Continuous Improvement in ISO 9001:2015
- The PDCA Cycle: The Engine of Continuous Improvement
- Key Aspects of Continuous Improvement in ISO 9001
- 1. Proactive Identification of Opportunities
- 2. Data-Driven Decision Making
- 3. Employee Engagement and Empowerment
- 4. Management Commitment and Leadership
- 5. Regular Monitoring and Review
- The Benefits of Continuous Improvement
- Integrating Continuous Improvement into Your QMS
- Conclusion: Continuous Improvement – The Heart of ISO 9001
- Latest Posts
- Latest Posts
- Related Post
ISO 9000 Currently Stresses Continuous Improvement of a Certified Organization
The ISO 9000 family of standards, specifically ISO 9001:2015, places a significant emphasis on continuous improvement as a core tenet for certified organizations. This isn't merely a suggestion; it's a fundamental principle woven into the fabric of the standard, driving ongoing enhancement of processes, products, and services. This article delves deep into the concept of continuous improvement within the ISO 9001 framework, exploring its various aspects and its crucial role in maintaining certification and achieving sustained success.
Understanding Continuous Improvement in ISO 9001:2015
Continuous improvement, often referred to as CI or Kaizen (a Japanese term emphasizing incremental change), is a philosophy that encourages ongoing refinement and enhancement of an organization's Quality Management System (QMS). It's not about achieving perfection; instead, it’s a journey of consistent progress, always striving to do things better. Within the ISO 9001 framework, continuous improvement is intrinsically linked to customer satisfaction, operational efficiency, and organizational resilience.
The PDCA Cycle: The Engine of Continuous Improvement
The Plan-Do-Check-Act (PDCA) cycle, also known as the Deming cycle, provides a structured approach to implementing continuous improvement. This cyclical process forms the backbone of many improvement initiatives within ISO 9001-certified organizations.
- Plan: This phase involves identifying areas for improvement, defining objectives, developing a plan of action, and allocating resources. This might include analyzing customer feedback, identifying process bottlenecks, or reviewing performance data.
- Do: This phase involves implementing the planned changes, testing them on a small scale, and collecting data on their effectiveness. This could involve piloting a new process, implementing a new technology, or training employees on a new technique.
- Check: This phase involves analyzing the data collected during the "Do" phase to assess the effectiveness of the changes implemented. This might involve comparing performance data before and after the implementation of the changes.
- Act: This phase involves standardizing successful changes, documenting lessons learned, and taking corrective actions for any issues encountered. This might involve updating procedures, implementing new standards, or providing additional training.
The PDCA cycle is iterative; successful improvements often lead to further opportunities for enhancement, perpetuating a cycle of ongoing progress.
Key Aspects of Continuous Improvement in ISO 9001
ISO 9001 doesn't prescribe specific methods for continuous improvement; instead, it encourages organizations to adopt a systematic approach that aligns with their context and objectives. However, several key aspects are crucial for effective implementation:
1. Proactive Identification of Opportunities
Continuous improvement shouldn't be a reactive process; it necessitates proactively identifying potential areas for enhancement. This involves actively seeking feedback from customers, employees, suppliers, and other stakeholders. Analyzing data, auditing processes, and conducting regular reviews are also essential elements. Identifying trends, anticipating future challenges, and taking proactive steps to mitigate risks are vital for sustained success.
2. Data-Driven Decision Making
Effective continuous improvement relies heavily on data-driven decision-making. Organizations need to collect and analyze relevant data to identify trends, assess performance, and measure the effectiveness of improvement initiatives. This data might include customer satisfaction scores, process efficiency metrics, defect rates, and employee feedback. The use of appropriate analytical tools and techniques, such as statistical process control (SPC) and root cause analysis (RCA), is crucial for making informed decisions.
3. Employee Engagement and Empowerment
Continuous improvement requires the active participation and engagement of all employees. Creating a culture that fosters open communication, encourages innovation, and empowers employees to identify and suggest improvements is paramount. Training employees on relevant improvement techniques, such as Lean and Six Sigma, can enhance their ability to contribute to continuous improvement initiatives. Recognizing and rewarding employee contributions helps to foster a culture of continuous improvement.
4. Management Commitment and Leadership
Successful continuous improvement necessitates strong commitment and leadership from top management. Management must actively support continuous improvement initiatives, provide the necessary resources, and foster a culture that values continuous improvement. Leaders must champion the cause, set clear expectations, and hold employees accountable for their contributions. Their active involvement and demonstrated commitment are vital for driving and sustaining the continuous improvement process.
5. Regular Monitoring and Review
Regular monitoring and review of the QMS is essential for tracking progress and identifying areas needing further improvement. Internal audits, management reviews, and regular performance evaluations provide opportunities to assess the effectiveness of continuous improvement initiatives. This iterative review process allows for timely adjustments and course corrections, ensuring that the organization remains on track to achieve its objectives. Identifying deviations from plans and promptly addressing them ensures the continuous improvement efforts remain effective.
The Benefits of Continuous Improvement
The benefits of embracing a culture of continuous improvement extend beyond maintaining ISO 9001 certification. It leads to numerous tangible and intangible advantages:
- Enhanced Customer Satisfaction: By continually improving products, services, and processes, organizations can better meet customer needs and expectations, leading to increased customer satisfaction and loyalty.
- Increased Efficiency and Productivity: Streamlining processes and eliminating waste can significantly improve efficiency and productivity, reducing costs and increasing profitability.
- Reduced Defects and Errors: Continuous improvement initiatives can help identify and eliminate defects and errors, reducing waste and improving quality.
- Improved Employee Morale: Engaging employees in continuous improvement initiatives can boost morale and job satisfaction, leading to increased employee retention and productivity.
- Enhanced Competitive Advantage: Organizations that consistently improve their processes and products gain a significant competitive advantage in the marketplace.
- Stronger Organizational Resilience: A culture of continuous improvement makes organizations more adaptable and resilient to change, allowing them to respond effectively to new challenges and opportunities.
- Improved Risk Management: Continuous improvement helps identify and mitigate risks proactively, preventing costly errors and disruptions.
Integrating Continuous Improvement into Your QMS
Integrating continuous improvement into your QMS requires a strategic and systematic approach. Consider these steps:
- Define your improvement goals: Clearly articulate what you aim to achieve through continuous improvement. Align these goals with your overall business objectives.
- Identify key performance indicators (KPIs): Choose KPIs that accurately reflect your improvement goals. These KPIs should be measurable and trackable.
- Establish a feedback mechanism: Create a system for collecting feedback from customers, employees, and other stakeholders.
- Implement the PDCA cycle: Use the PDCA cycle as a framework for implementing continuous improvement initiatives.
- Provide training and resources: Equip your employees with the necessary training and resources to effectively participate in continuous improvement initiatives.
- Regularly review and update your QMS: Conduct regular reviews of your QMS to ensure that it remains effective and aligned with your continuous improvement goals.
- Celebrate successes: Recognize and reward employees for their contributions to continuous improvement initiatives.
Conclusion: Continuous Improvement – The Heart of ISO 9001
Continuous improvement isn't merely a requirement for ISO 9001 certification; it's a vital driver of organizational success. By embracing a culture of continuous improvement, organizations can enhance their QMS, improve their products and services, increase efficiency, and gain a competitive edge. It's a journey, not a destination – a commitment to ongoing refinement and enhancement that drives long-term growth and sustainability. The emphasis on continuous improvement within ISO 9001 underscores its importance in a dynamic and ever-evolving business landscape. It's not simply about meeting the standards but exceeding them, continually striving for excellence and adapting to the ever-changing needs of the marketplace. The future of success lies in the consistent pursuit of improvement, aligning organizational goals with the dynamic demands of the global market. Embracing this philosophy ensures sustained growth, increased competitiveness, and ultimately, lasting success.
Latest Posts
Latest Posts
-
Correctly Label The Following Anatomical Features Of The Neuroglia
Mar 31, 2025
-
What Is The Term Premium In The Context Of Bonds
Mar 31, 2025
-
A Hypothesis Can Be Defined As
Mar 31, 2025
-
Marginal Thinking Is Best Demonstrated By
Mar 31, 2025
-
A Monopolists Profits With Price Discrimination Will Be
Mar 31, 2025
Related Post
Thank you for visiting our website which covers about Iso 9000 Currently Stresses _____ Of A Certified Organization. . We hope the information provided has been useful to you. Feel free to contact us if you have any questions or need further assistance. See you next time and don't miss to bookmark.