Experiment 10 Analysis Of An Aluminum Zinc Alloy
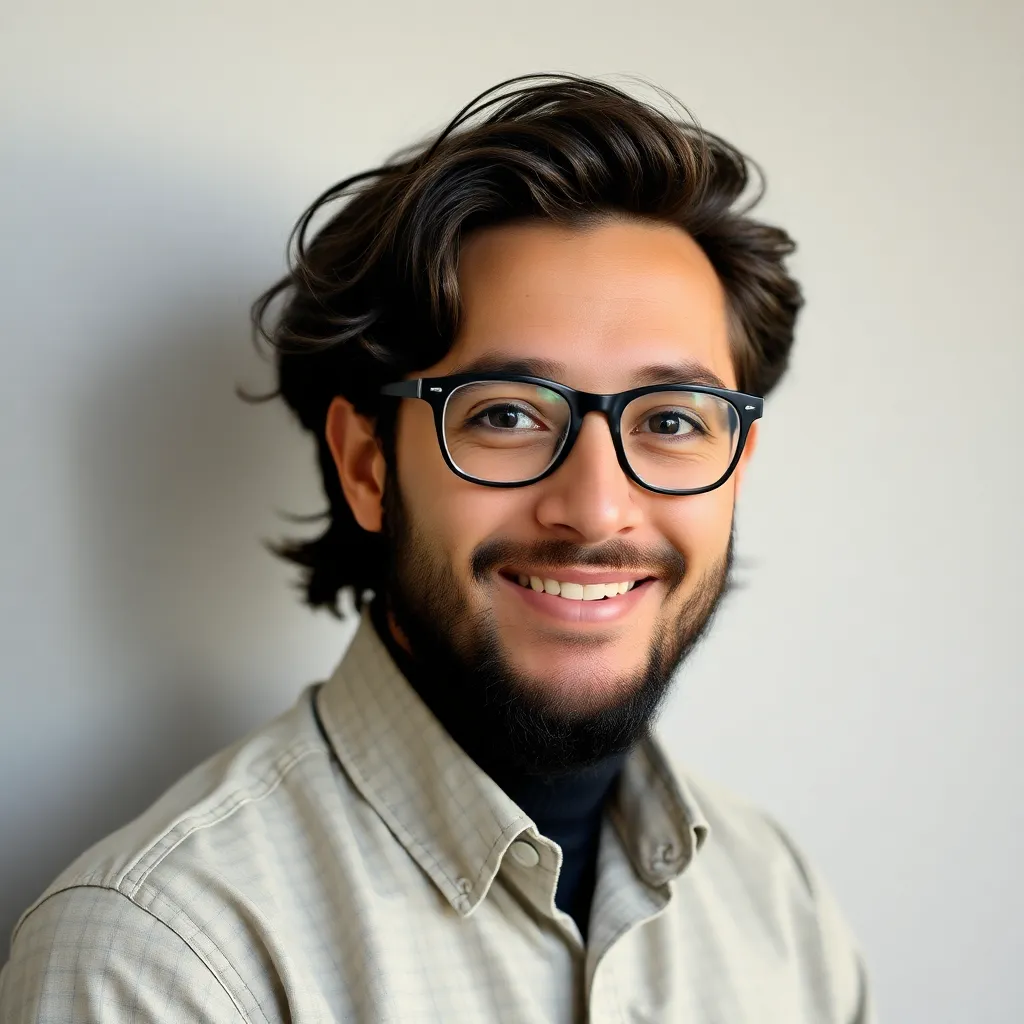
Holbox
Apr 02, 2025 · 6 min read
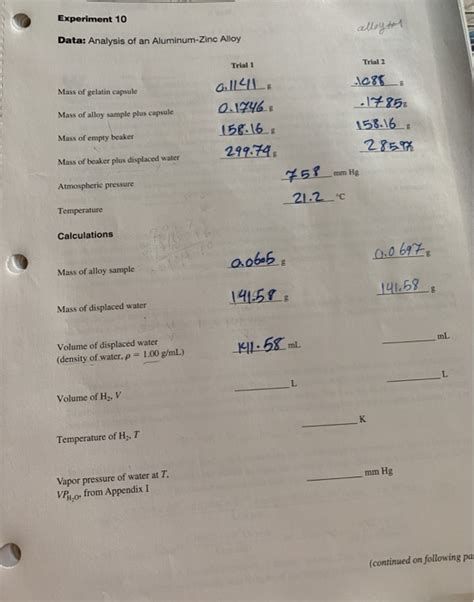
Table of Contents
- Experiment 10 Analysis Of An Aluminum Zinc Alloy
- Table of Contents
- Experiment 10 Analysis of an Aluminum Zinc Alloy: A Comprehensive Guide
- Understanding Aluminum Zinc Alloys
- Key Characteristics of Al-Zn Alloys:
- Experiment 10: Methodology and Procedures
- Sample Preparation:
- Experimental Techniques Employed:
- Experiment 10: Results and Interpretation
- Microscopic Analysis:
- Mechanical Testing Results:
- Corrosion Testing Results:
- Error Analysis and Limitations
- Conclusion and Future Work
- Latest Posts
- Latest Posts
- Related Post
Experiment 10 Analysis of an Aluminum Zinc Alloy: A Comprehensive Guide
This article delves into a comprehensive analysis of Experiment 10, focusing on an aluminum zinc alloy. We'll explore various analytical techniques, interpret results, and discuss potential applications of this important material. Understanding the properties and behavior of aluminum zinc alloys is crucial in various industries, from aerospace to automotive manufacturing. This in-depth analysis will cover key aspects of the experiment and provide valuable insights for researchers and students alike.
Understanding Aluminum Zinc Alloys
Aluminum zinc alloys, also known as Al-Zn alloys, represent a class of materials known for their high strength-to-weight ratio and excellent corrosion resistance. The specific properties of an Al-Zn alloy are heavily influenced by the zinc content and the presence of other alloying elements. These alloys often undergo specific heat treatments to achieve desired mechanical properties. The interplay between composition, processing, and resulting microstructure is fundamental to understanding the alloy's behavior.
Key Characteristics of Al-Zn Alloys:
- High Strength: The addition of zinc significantly increases the strength of aluminum, making it suitable for structural applications.
- Lightweight: Aluminum's inherent lightness remains a key advantage, contributing to fuel efficiency in transportation and reduced structural weight in aerospace applications.
- Corrosion Resistance: Al-Zn alloys generally exhibit good corrosion resistance, although this can be enhanced further through surface treatments like anodizing.
- Weldability: The weldability of Al-Zn alloys depends on the specific composition and can vary. Proper welding techniques are crucial to ensure integrity.
- Formability: The formability of these alloys can be tailored through controlled processing techniques, making them adaptable to various manufacturing processes.
Experiment 10: Methodology and Procedures
Experiment 10 likely involved a series of tests designed to characterize the aluminum zinc alloy's physical, mechanical, and microstructural properties. A detailed account of the experimental setup and procedures is crucial for accurate interpretation of the results. Let's outline a potential methodology for such an experiment, keeping in mind that specific details would depend on the actual experiment conducted.
Sample Preparation:
- Specimen Selection: Representative samples of the Al-Zn alloy would be carefully selected to ensure the results are truly representative of the material.
- Surface Preparation: This step is crucial for accurate analysis. It typically involves polishing the sample to a mirror finish to remove surface imperfections that might interfere with testing. This might involve several stages using different grades of abrasive papers and polishing compounds.
- Etching (Optional): Etching is often used to reveal the microstructure of the alloy. This involves immersing the polished sample in a specific etchant solution to reveal grain boundaries and other microstructural features.
Experimental Techniques Employed:
-
Optical Microscopy: This technique provides a visual representation of the alloy's microstructure. The etched sample is observed under an optical microscope, allowing the identification of different phases, grain sizes, and any defects present. Microphotographs are then taken to document the observations. Image analysis software can be used to quantify parameters such as grain size distribution.
-
Scanning Electron Microscopy (SEM): SEM offers higher magnification and resolution compared to optical microscopy, enabling detailed examination of the microstructure, including the identification of individual phases and precipitates. Energy-dispersive X-ray spectroscopy (EDS) can be coupled with SEM to determine the elemental composition at specific locations within the sample.
-
Tensile Testing: This is a fundamental mechanical test to determine the alloy's tensile strength, yield strength, elongation, and Young's modulus. A standardized tensile testing machine is used to apply a controlled tensile force to a specimen until failure. The resulting stress-strain curve provides valuable information about the alloy's mechanical properties.
-
Hardness Testing: Hardness tests, such as Vickers or Brinell hardness tests, measure the alloy's resistance to indentation. These tests provide a quick and easy assessment of the alloy's overall strength and are often used for quality control purposes.
-
Corrosion Testing: Various corrosion tests, such as salt spray testing or electrochemical impedance spectroscopy (EIS), can be conducted to evaluate the alloy's resistance to corrosion in specific environments. These tests help determine the alloy's susceptibility to degradation in different conditions.
-
X-ray Diffraction (XRD): XRD is a powerful technique used to identify the crystalline phases present in the alloy. It provides information on the crystal structure, lattice parameters, and phase percentages. This is particularly useful for identifying different intermetallic compounds that might form in the Al-Zn alloy.
Experiment 10: Results and Interpretation
The results of Experiment 10 would consist of a comprehensive dataset encompassing the various tests conducted. The interpretation of these results requires a thorough understanding of materials science principles and the specific techniques employed. Let's consider some potential results and their interpretations:
Microscopic Analysis:
- Grain Size: A smaller grain size typically indicates higher strength and hardness due to increased grain boundary area hindering dislocation movement. The grain size distribution can also provide insights into the alloy's processing history.
- Phase Identification: The identification of different phases, including the aluminum matrix and zinc-rich precipitates, is crucial. The distribution and morphology of these phases influence the alloy's properties.
- Defect Analysis: The presence of defects, such as voids, cracks, or inclusions, can significantly affect the alloy's mechanical properties and corrosion resistance.
Mechanical Testing Results:
- Tensile Strength: A higher tensile strength signifies greater resistance to deformation under tensile loading.
- Yield Strength: The yield strength indicates the stress at which the alloy begins to undergo permanent deformation.
- Elongation: Elongation measures the alloy's ductility, representing its ability to deform before fracture.
- Young's Modulus: Young's modulus represents the alloy's stiffness or resistance to elastic deformation.
Corrosion Testing Results:
- Corrosion Rate: The corrosion rate indicates the speed at which the alloy corrodes in a specific environment. A lower corrosion rate is desirable.
- Corrosion Resistance: The overall corrosion resistance is evaluated based on the extent of corrosion observed in the tests. This could be assessed visually, by weight loss measurements, or through electrochemical techniques.
Error Analysis and Limitations
A crucial aspect of any scientific experiment is the assessment of potential sources of error and limitations. In Experiment 10, potential sources of error could include:
- Sample Preparation Errors: Improper sample preparation can lead to inaccurate results in microscopy and mechanical testing.
- Measurement Errors: Errors in measuring forces, displacements, or other parameters during testing can affect the accuracy of the results.
- Instrumental Errors: Calibration errors or malfunctions of the instruments used can also lead to inaccuracies.
- Environmental Factors: Temperature fluctuations or humidity levels during testing can influence the results.
Conclusion and Future Work
Experiment 10 provides valuable data on the properties and behavior of an aluminum zinc alloy. The detailed analysis of the microstructure, mechanical properties, and corrosion resistance provides crucial insights into its suitability for specific applications. The results can be used to optimize the alloy's composition and processing to achieve desired properties. Future work could involve investigating the effects of different alloying elements or processing parameters on the alloy's properties. Exploring the alloy's behavior under different loading conditions or environmental exposures would also expand our understanding. Furthermore, comparing experimental results with computational modeling could provide a deeper understanding of the alloy's behavior at a microstructural level. The insights gained from Experiment 10 contribute significantly to the body of knowledge on aluminum zinc alloys, paving the way for improved materials design and applications in diverse fields. This detailed analysis emphasizes the importance of rigorous experimental methodology and comprehensive data interpretation in advancing materials science.
Latest Posts
Latest Posts
-
National Income Accountants Define Investment To Include
Apr 05, 2025
-
Based On The Frequency Distribution Above Is 22 5 A
Apr 05, 2025
-
The Smallest Units Of Speech That Affect Meaning Are Called
Apr 05, 2025
-
Find And Interpret The Z Score For The Data Value Given
Apr 05, 2025
-
Match The Following Terms To Their Definitions
Apr 05, 2025
Related Post
Thank you for visiting our website which covers about Experiment 10 Analysis Of An Aluminum Zinc Alloy . We hope the information provided has been useful to you. Feel free to contact us if you have any questions or need further assistance. See you next time and don't miss to bookmark.