An Assembly Line Is An Example Of A
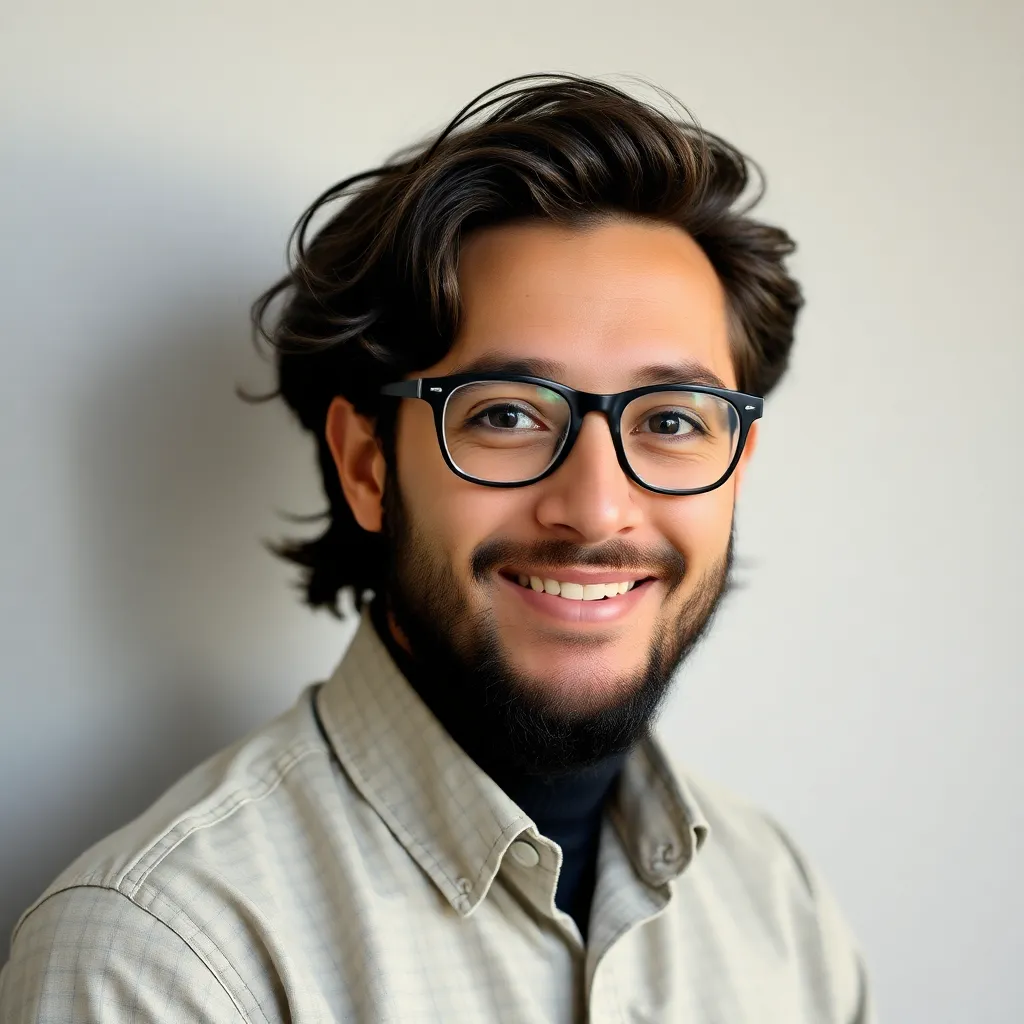
Holbox
Apr 04, 2025 · 6 min read

Table of Contents
- An Assembly Line Is An Example Of A
- Table of Contents
- An Assembly Line is an Example of a: Production System Optimization Through Specialization
- The Core Principles of an Assembly Line
- Division of Labor: The Key to Efficiency
- Standardization and Interchangeable Parts: The Foundation of Mass Production
- Process Optimization: Continuous Improvement and Waste Reduction
- Types of Assembly Lines
- 1. Straight-Line Assembly Line: The Classic Model
- 2. U-Shaped Assembly Line: Improved Efficiency and Flexibility
- 3. Parallel Assembly Line: Increased Capacity
- 4. Rotary Assembly Line: Circular Motion and Continuous Production
- Assembly Line and Modern Manufacturing Techniques
- 1. Lean Manufacturing: Eliminating Waste and Maximizing Efficiency
- 2. Just-in-Time (JIT) Inventory: Minimizing Inventory Costs
- 3. Automation and Robotics: Enhancing Speed and Precision
- 4. Computer-Integrated Manufacturing (CIM): Data-Driven Optimization
- Challenges and Limitations of Assembly Lines
- 1. Inflexibility: Adapting to Change
- 2. Worker Deskilling and Monotony: Impact on Employees
- 3. Dependence on Supply Chain: Vulnerability to Disruptions
- 4. High Initial Investment: Cost of Setup
- Conclusion: The Enduring Legacy of the Assembly Line
- Latest Posts
- Latest Posts
- Related Post
An Assembly Line is an Example of a: Production System Optimization Through Specialization
An assembly line is a prime example of a highly specialized and efficient production system. It represents a sophisticated application of several core manufacturing and operational principles, demonstrating the power of division of labor, standardization, and process optimization. Understanding how an assembly line functions reveals insights into broader concepts like lean manufacturing, mass production, and the impact of technological advancements on industrial processes.
The Core Principles of an Assembly Line
At its heart, an assembly line embodies the principles of Frederick Winslow Taylor's scientific management, which advocates for breaking down complex tasks into smaller, simpler components. This division of labor allows for specialization, where workers become highly proficient at performing a limited set of actions. The result is increased speed, reduced errors, and improved overall efficiency.
Division of Labor: The Key to Efficiency
The hallmark of an assembly line is its division of labor. Instead of one worker completing an entire product, the process is divided into numerous small, repetitive tasks. Each worker is responsible for a specific step, leading to a highly streamlined and efficient workflow. This specialization reduces the time required to produce each unit, leading to increased output. This specialization is further enhanced through ergonomic design, optimizing the workspace and tools to minimise worker strain and maximize efficiency.
Standardization and Interchangeable Parts: The Foundation of Mass Production
The assembly line relies heavily on standardization. Components are manufactured to precise specifications, ensuring interchangeability and reducing downtime caused by fitting issues. This principle is central to mass production, enabling the consistent creation of large quantities of identical products. The use of standardized tools and fixtures further enhances efficiency, making the production process easier to learn and execute.
Process Optimization: Continuous Improvement and Waste Reduction
An effective assembly line continuously strives for process optimization. This involves the constant analysis and improvement of every step in the production process. Methods like time-and-motion studies are used to identify bottlenecks and inefficiencies, leading to the refinement of workflows and the elimination of wasted time and materials. This iterative approach is integral to lean manufacturing principles, focusing on eliminating waste (muda) in all its forms.
Types of Assembly Lines
Assembly lines aren't monolithic; they adapt to different production needs and product complexities. Several types exist, each with its own strengths and weaknesses:
1. Straight-Line Assembly Line: The Classic Model
This is the most common type, where the product moves along a straight line, with workers performing their tasks in a sequential order. It’s highly effective for high-volume production of standardized products with a straightforward assembly process. However, it can be inflexible and difficult to adapt to changes in product design or demand.
2. U-Shaped Assembly Line: Improved Efficiency and Flexibility
A U-shaped layout allows for better worker interaction and material flow, reducing the distance materials need to travel. It offers increased flexibility and allows for easier reconfiguration if needed. The U-shape enhances communication between workers and allows for easier supervision and quality control.
3. Parallel Assembly Line: Increased Capacity
This type uses multiple straight-line assembly lines running simultaneously, increasing overall production capacity. It's particularly useful for products with variations or when high production volumes are needed. However, it necessitates greater management and coordination.
4. Rotary Assembly Line: Circular Motion and Continuous Production
In this type, the product rotates on a turntable, with workers stationed around the circle performing their tasks as the product passes. This is suitable for products requiring a high degree of rotation during assembly, such as certain electronic components.
Assembly Line and Modern Manufacturing Techniques
The assembly line's core principles have influenced many modern manufacturing techniques:
1. Lean Manufacturing: Eliminating Waste and Maximizing Efficiency
Lean manufacturing, inspired by the Toyota Production System (TPS), embraces many assembly line principles, focusing on reducing waste (muda) in all its forms – including overproduction, waiting, transportation, over-processing, inventory, motion, and defects. It emphasizes continuous improvement (kaizen) and a "pull" system, where production is triggered by actual demand rather than forecasts.
2. Just-in-Time (JIT) Inventory: Minimizing Inventory Costs
JIT inventory management, closely linked to lean manufacturing, aims to minimize inventory holding costs by delivering materials exactly when and where they are needed. This reduces storage space requirements and minimizes the risk of obsolescence or damage. The assembly line's efficiency relies on JIT principles to ensure a steady flow of parts without excessive storage.
3. Automation and Robotics: Enhancing Speed and Precision
Modern assembly lines increasingly incorporate automation and robotics to further enhance speed, precision, and consistency. Robots perform repetitive tasks with greater accuracy and speed than human workers, reducing errors and improving overall productivity. This automation is particularly beneficial for complex or dangerous tasks.
4. Computer-Integrated Manufacturing (CIM): Data-Driven Optimization
CIM uses computers to control and monitor all aspects of the manufacturing process, including design, production planning, and quality control. Data gathered from various points in the assembly line can be analyzed to identify areas for improvement, further optimizing efficiency and reducing waste. This advanced integration utilizes data analytics to improve production decisions.
Challenges and Limitations of Assembly Lines
While extremely effective, assembly lines also face challenges:
1. Inflexibility: Adapting to Change
Assembly lines can be inflexible when it comes to adapting to changes in product design or demand fluctuations. Retooling an assembly line for a new product can be costly and time-consuming.
2. Worker Deskilling and Monotony: Impact on Employees
The repetitive nature of assembly line work can lead to worker deskilling and monotony, potentially affecting morale and productivity. Strategies such as job rotation and employee empowerment are crucial for mitigating this issue.
3. Dependence on Supply Chain: Vulnerability to Disruptions
Assembly lines are highly dependent on a reliable supply chain. Disruptions in the supply of parts can cause significant production delays and losses.
4. High Initial Investment: Cost of Setup
Setting up an assembly line requires a significant initial investment in equipment, facilities, and training. This can be a barrier to entry for smaller businesses.
Conclusion: The Enduring Legacy of the Assembly Line
Despite these challenges, the assembly line remains a cornerstone of modern manufacturing. Its principles of specialization, standardization, and process optimization continue to shape industrial practices. The ongoing integration of automation, lean principles, and data-driven optimization further enhances the efficiency and effectiveness of assembly line systems, ensuring their continued relevance in the ever-evolving landscape of global manufacturing. The assembly line is not merely a production method; it’s a testament to the power of systematic thinking and continuous improvement in driving efficiency and productivity. Its legacy extends beyond the factory floor, influencing various aspects of operational management across diverse industries. The core principles of streamlined processes and optimized workflows remain highly valuable in optimizing organizational effectiveness and achieving strategic goals.
Latest Posts
Latest Posts
-
What Would Be The Effect Of A Reduced Venous Return
Apr 06, 2025
-
Iso 9000 Seeks Standardization In Terms Of
Apr 06, 2025
-
If Xy 2 X 2 Y 5 Then Dy Dx
Apr 06, 2025
-
Below Is The Lewis Structure Of The Formaldehyde Molecule
Apr 06, 2025
-
Art Labeling Activity Anatomy And Histology Of The Thyroid Gland
Apr 06, 2025
Related Post
Thank you for visiting our website which covers about An Assembly Line Is An Example Of A . We hope the information provided has been useful to you. Feel free to contact us if you have any questions or need further assistance. See you next time and don't miss to bookmark.