Iso 9000 Seeks Standardization In Terms Of __________.
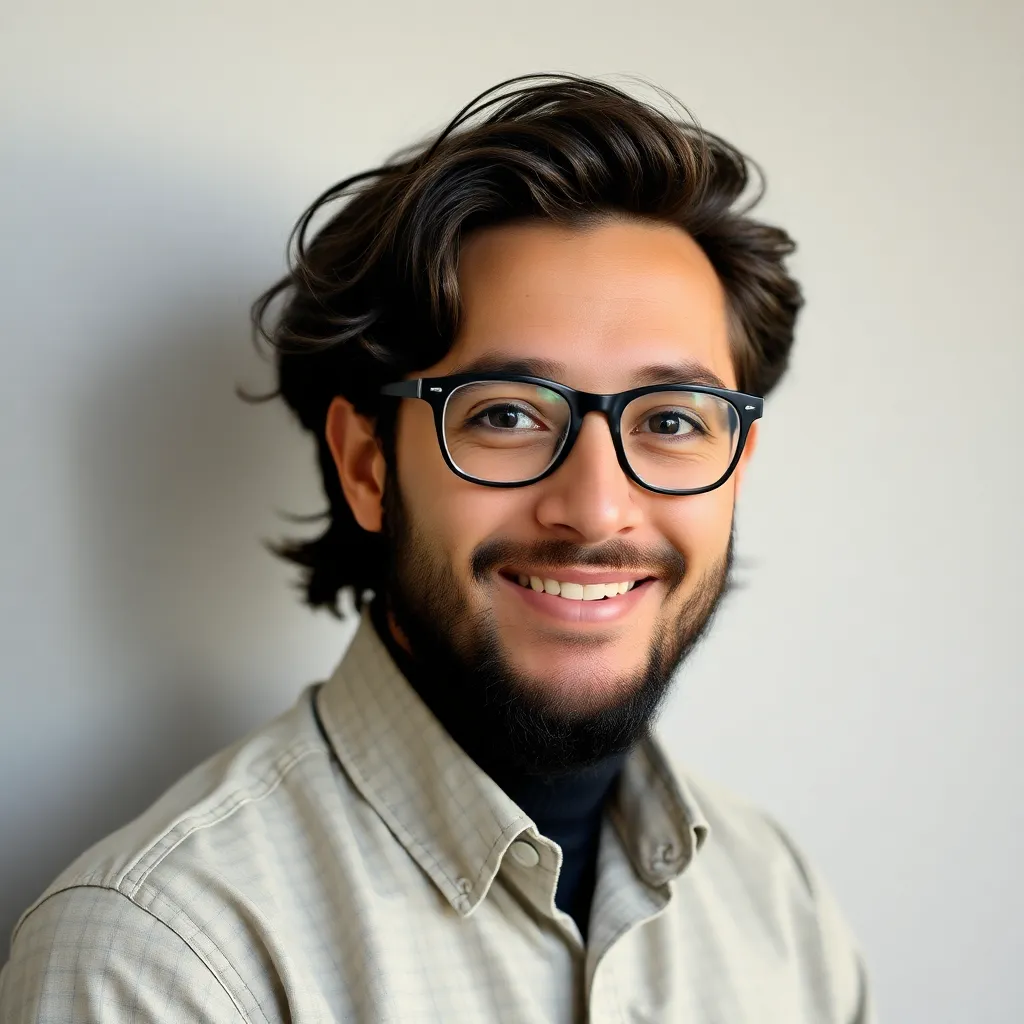
Holbox
Apr 06, 2025 · 6 min read

Table of Contents
- Iso 9000 Seeks Standardization In Terms Of __________.
- Table of Contents
- ISO 9000 Seeks Standardization in Terms of Quality Management Systems
- Understanding the Core of ISO 9000: Quality Management Systems
- Key Elements Standardized by ISO 9000
- Benefits of ISO 9000 Standardization
- The Evolution of ISO 9000: Adapting to Modern Needs
- Risk-Based Thinking: A Proactive Approach to Quality
- Process Approach: Streamlining Operations for Efficiency
- Continuous Improvement: A Foundation for Long-Term Success
- Integration with Other Management Systems
- Conclusion: The Enduring Relevance of ISO 9000
- Latest Posts
- Latest Posts
- Related Post
ISO 9000 Seeks Standardization in Terms of Quality Management Systems
The ISO 9000 family of standards is globally recognized for its focus on quality management systems (QMS). It doesn't seek standardization in terms of a single product or service, but rather in the processes organizations use to consistently meet customer requirements and enhance customer satisfaction. This article will delve deep into the specifics of what ISO 9000 standardizes, exploring its key principles, benefits, and the ongoing evolution to meet modern business needs.
Understanding the Core of ISO 9000: Quality Management Systems
At its heart, ISO 9000 aims to standardize how organizations manage their quality. This isn't about dictating what a company produces or how it does so, but how it ensures its processes are efficient, reliable, and consistently deliver high-quality outputs. A QMS encompasses all the policies, procedures, processes, and resources an organization needs to direct and control its activities related to quality. This includes everything from planning and resource management to product realization, measurement, analysis, and improvement.
Think of it as a framework. ISO 9000 provides the structure, the guidelines, and the best practices. Each organization then tailors this framework to its specific context, industry, and products or services. The standardization lies in the approach to quality management, not in the specific implementation details.
Key Elements Standardized by ISO 9000
ISO 9001, the most widely used standard in the family, outlines the requirements for a QMS. These requirements are grouped into several key areas, all contributing to standardization across various organizations:
-
Context of the organization: This involves understanding the internal and external issues that can impact the organization's ability to deliver consistently high-quality products or services. It's about identifying stakeholders, their needs, and the legal and regulatory framework within which the organization operates. Standardization here focuses on the process of identifying and assessing these factors, ensuring a consistent approach regardless of the organization's size or industry.
-
Leadership: Strong leadership is crucial for driving a quality-focused culture. ISO 9001 standardizes the need for top management commitment, establishing clear responsibility and accountability for quality management. This includes setting quality objectives, providing resources, and promoting continuous improvement. The standardization lies in the approach to leadership—the processes for communication, decision-making, and resource allocation related to quality.
-
Planning: This includes establishing the quality management system, setting objectives, determining the necessary processes, and managing resources. Standardization here relates to how an organization systematically plans for quality, establishing clear goals and methods for achieving them.
-
Support: This element focuses on the resources needed to achieve the organization's quality objectives. It encompasses infrastructure, personnel competency, monitoring, and measuring resources. The standardization ensures consistent management of these resources and ongoing evaluation of their effectiveness.
-
Operation: This covers the processes necessary to deliver products and services that meet customer requirements. It involves operational planning, control, and monitoring of processes. Standardization here emphasizes the structured approach to process management, including risk assessment and control measures.
-
Performance evaluation: This involves monitoring, measuring, analyzing, and evaluating the effectiveness of the QMS. It focuses on data collection, analysis, and the identification of opportunities for improvement. The standardized approach emphasizes data-driven decision-making and regular review of the QMS effectiveness.
-
Improvement: The continuous improvement of the QMS is a fundamental principle of ISO 9001. This involves taking corrective and preventive actions to address nonconformities, implementing improvements, and regularly reviewing the QMS's effectiveness. The standardization centers on the process of improvement, encouraging a proactive approach to identifying and addressing issues.
Benefits of ISO 9000 Standardization
The standardization provided by ISO 9000 offers numerous benefits for organizations across various sectors:
-
Enhanced Customer Satisfaction: By focusing on consistent quality and meeting customer requirements, organizations can significantly improve customer satisfaction and loyalty.
-
Increased Efficiency and Productivity: A well-defined QMS streamlines processes, reduces waste, and improves efficiency, leading to increased productivity.
-
Improved Risk Management: The structured approach to risk assessment and control reduces the likelihood of errors and nonconformities, mitigating potential risks.
-
Enhanced Reputation and Brand Image: ISO 9001 certification demonstrates a commitment to quality, enhancing the organization's reputation and brand image in the marketplace.
-
Improved Employee Morale and Engagement: A well-managed QMS promotes a culture of continuous improvement and employee empowerment, leading to improved morale and engagement.
-
Better Decision Making: Data-driven decision-making based on performance evaluation strengthens the organization's ability to make informed decisions.
-
Access to New Markets: ISO 9001 certification is often a requirement for doing business in certain industries or markets, opening doors to new opportunities.
-
Competitive Advantage: In today's competitive business environment, a robust QMS provides a competitive edge by demonstrating a commitment to quality and customer satisfaction.
The Evolution of ISO 9000: Adapting to Modern Needs
The ISO 9000 standards are not static; they evolve to reflect changes in the business environment and incorporate best practices. Recent revisions emphasize the importance of risk-based thinking, proactive management, and the integration of quality management into all aspects of the organization.
Risk-Based Thinking: A Proactive Approach to Quality
Modern ISO 9001 places a strong emphasis on risk-based thinking. This means identifying, analyzing, and addressing potential risks and opportunities that can affect the organization's ability to meet customer requirements and achieve its objectives. This proactive approach helps organizations prevent problems before they arise, rather than reacting to them after they occur. The standardization focuses on how organizations incorporate risk-based thinking into their QMS, providing a consistent framework for identifying, assessing, and mitigating risks.
Process Approach: Streamlining Operations for Efficiency
ISO 9001 promotes a process approach to quality management. This means understanding the interconnectedness of different processes within the organization and managing them effectively to achieve desired outcomes. A structured approach to process management streamlines operations, reduces waste, and improves efficiency. Standardization here focuses on the method for mapping, analyzing, and improving processes, promoting consistent process optimization across the organization.
Continuous Improvement: A Foundation for Long-Term Success
Continuous improvement remains a cornerstone of ISO 9000. The Plan-Do-Check-Act (PDCA) cycle is a widely used framework for driving continuous improvement by identifying areas for improvement, implementing changes, monitoring their effectiveness, and making further adjustments as needed. The standardization of the continuous improvement process ensures that organizations constantly strive for enhanced quality and performance.
Integration with Other Management Systems
The latest iterations of ISO 9001 emphasize the importance of integrating the QMS with other management systems, such as environmental management systems (ISO 14001), occupational health and safety management systems (ISO 45001), and information security management systems (ISO 27001). This integrated approach enhances efficiency and reduces redundancy by streamlining processes and aligning objectives across different management systems.
Conclusion: The Enduring Relevance of ISO 9000
ISO 9000's enduring relevance stems from its ability to adapt to evolving business needs. By standardizing the approach to quality management, it provides organizations with a framework for continuous improvement, enhanced customer satisfaction, and a stronger competitive position. The focus on risk-based thinking, a process approach, and continuous improvement ensures that ISO 9001 remains a valuable tool for organizations striving for excellence in quality management. The standardization itself isn't about dictating specific practices, but about creating a consistent and effective method for organizations to pursue and achieve their quality goals. This flexibility, combined with its global recognition, ensures that ISO 9000 will continue to be a crucial element in the drive towards quality and excellence in businesses worldwide.
Latest Posts
Latest Posts
-
Draw The Condensed Structural Formula For Hexyl Acetate
Apr 13, 2025
-
Determine Which Ions Are Present In Each Of The Compounds
Apr 13, 2025
-
Derive Linear Density Expressions For Bcc 110 And 111
Apr 13, 2025
-
A Squirrel Runs Along An Overhead Telephone Wire
Apr 13, 2025
-
Determine If The Following Statements Are True Or False
Apr 13, 2025
Related Post
Thank you for visiting our website which covers about Iso 9000 Seeks Standardization In Terms Of __________. . We hope the information provided has been useful to you. Feel free to contact us if you have any questions or need further assistance. See you next time and don't miss to bookmark.