All Of The Following Are Examples Of Product Costs Except
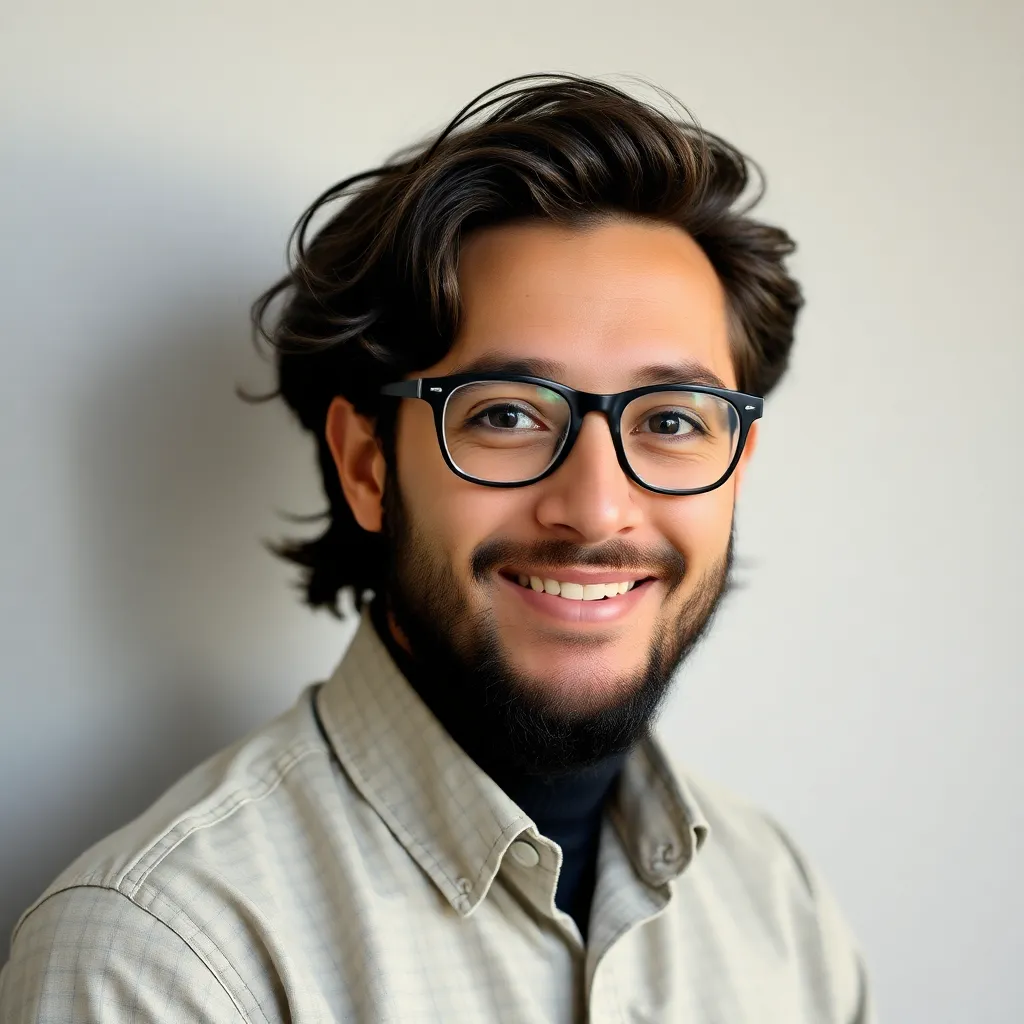
Holbox
Apr 02, 2025 · 6 min read

Table of Contents
- All Of The Following Are Examples Of Product Costs Except
- Table of Contents
- All of the Following Are Examples of Product Costs Except... Understanding Cost Classification for Profitability
- What are Product Costs?
- Examples of Product Costs: A Detailed Breakdown
- 1. Direct Materials
- 2. Direct Labor
- 3. Manufacturing Overhead
- Examples of Costs That Are Not Product Costs: Period Costs
- 1. Selling Expenses
- 2. General and Administrative Expenses (G&A)
- 3. Research and Development (R&D) Costs (Generally)
- 4. Interest Expense
- Different Costing Methods and Their Impact
- 1. Job-Order Costing
- 2. Process Costing
- 3. Activity-Based Costing (ABC)
- The Importance of Accurate Product Costing
- Conclusion: Mastering Product Cost Classification
- Latest Posts
- Latest Posts
- Related Post
All of the Following Are Examples of Product Costs Except... Understanding Cost Classification for Profitability
Understanding product costs is crucial for businesses of all sizes. Accurate cost accounting directly impacts pricing strategies, profit margins, and overall financial health. This comprehensive guide will delve into the intricacies of product costs, clarifying what constitutes a product cost and highlighting common examples of expenses that aren't classified as such. We'll explore different costing methods and their implications, ensuring you have a solid grasp of this essential business concept.
What are Product Costs?
Product costs, also known as inventoriable costs, are all costs directly attributable to the production of goods. These costs are "inventoried" – meaning they are initially recorded as an asset on the balance sheet and only become an expense when the goods are sold. This is in contrast to period costs, which are expensed in the period they are incurred, regardless of sales.
Key characteristics of product costs:
- Directly related to production: These costs are specifically tied to creating a finished product.
- Capitalized: They are recorded as assets until the product is sold.
- Included in inventory valuation: They form part of the cost of goods sold (COGS) when the product is sold.
Examples of Product Costs: A Detailed Breakdown
Several categories fall under the umbrella of product costs. Let's explore them in detail:
1. Direct Materials
These are the raw materials that become an integral part of the finished product. Think of the wood in a chair, the fabric in a shirt, or the flour in a loaf of bread. This is a straightforward and easily identifiable component of product cost.
Examples:
- Raw materials: The basic materials used in manufacturing.
- Packaging materials: The materials used to package the finished product for sale.
- Freight-in: The cost of transporting raw materials to the production facility. This is considered a direct cost because it is directly related to getting the raw materials to where they are needed.
2. Direct Labor
This encompasses the wages and benefits paid to workers directly involved in the manufacturing process. It's the time spent physically creating the product.
Examples:
- Wages of assembly line workers: The hourly pay of individuals directly assembling the product.
- Salaries of machine operators: Compensation for those operating machinery used in production.
- Employee benefits related to production: Healthcare, retirement contributions, and other benefits directly tied to production workers.
3. Manufacturing Overhead
This is a broad category encompassing all indirect costs associated with production. These costs are difficult, if not impossible, to trace directly to individual products. They support the production process but aren't directly part of the finished product.
Examples:
- Factory rent: The cost of renting or owning the factory space where production occurs.
- Factory utilities: Electricity, gas, and water used in the production facility.
- Factory insurance: Insurance premiums for the factory building and equipment.
- Depreciation of factory equipment: The allocation of the cost of equipment over its useful life.
- Supervisory salaries: Salaries of supervisors overseeing the production process.
- Maintenance and repairs of factory equipment: Costs associated with keeping production equipment functioning.
- Indirect materials: Small, insignificant materials used in production, such as lubricants or cleaning supplies.
Examples of Costs That Are Not Product Costs: Period Costs
These are expenses that are not directly related to the production of goods. They are expensed in the period they are incurred, regardless of whether any products were sold. This is a critical distinction from product costs.
1. Selling Expenses
These are costs incurred to market and sell the finished product.
Examples:
- Sales salaries: Salaries of the sales team.
- Advertising and promotion: Costs of marketing campaigns.
- Sales commissions: Payments to sales representatives based on sales volume.
- Shipping and handling costs (to customers): The cost of shipping the finished goods to customers. Note that freight-in is a product cost, while freight-out is a period cost.
- Sales office rent: Rent for the space where sales activities occur.
2. General and Administrative Expenses (G&A)
These are costs related to the overall management and administration of the business.
Examples:
- Executive salaries: Salaries of top management.
- Office rent: Rent for administrative offices.
- Utilities for administrative offices: Electricity, gas, and water for administrative offices.
- Legal and professional fees: Fees paid to lawyers and consultants.
- Insurance (general liability): Insurance premiums that don't specifically relate to the factory.
- Accounting and audit fees: Costs associated with financial reporting and auditing.
- Research and development (R&D): Costs related to the development of new products or processes (this can be complex and might sometimes be considered a product cost if directly tied to a specific product).
3. Research and Development (R&D) Costs (Generally)
While R&D can sometimes be directly related to a specific product under development, generally, it's treated as a period cost. This is because the benefit of R&D extends beyond the production of a single product and contributes to the overall advancement of the company.
4. Interest Expense
Interest payments on loans are always period costs. They are a financing cost, not directly tied to production.
Different Costing Methods and Their Impact
The method a company uses to account for product costs significantly influences its financial statements and decision-making. Several methods exist, each with its own advantages and disadvantages:
1. Job-Order Costing
This method is used when the company produces unique or customized products. Costs are tracked for each individual job or project. This allows for precise cost determination for each specific product.
2. Process Costing
This is suitable for mass production where identical or very similar products are manufactured. Costs are tracked for each production process or department, then averaged across all units produced. This method is simpler and less expensive than job-order costing but might not reflect the precise cost of each individual product.
3. Activity-Based Costing (ABC)
This sophisticated method assigns overhead costs based on the activities that drive those costs. It provides a more accurate picture of the costs associated with specific products or services, especially useful for businesses with diverse product lines.
The Importance of Accurate Product Costing
Accurate product cost accounting is vital for several reasons:
- Pricing decisions: Understanding the true cost of producing a product allows for effective pricing strategies that ensure profitability.
- Inventory valuation: Accurate product costs are crucial for accurately valuing inventory on the balance sheet.
- Profitability analysis: Correct cost accounting is essential for determining the profitability of individual products and the business as a whole.
- Cost control: By tracking costs meticulously, businesses can identify areas for improvement and reduce expenses.
- Performance evaluation: Cost data aids in evaluating the efficiency of production processes and identifying areas for improvement.
Conclusion: Mastering Product Cost Classification
Differentiating between product costs and period costs is essential for sound financial management. Understanding the various categories of each, along with the different costing methods, empowers businesses to make informed decisions regarding pricing, production, and overall profitability. By accurately tracking and analyzing these costs, businesses can optimize operations, enhance competitiveness, and achieve sustainable growth. Remember to consult with accounting professionals for specific guidance tailored to your business's unique circumstances.
Latest Posts
Latest Posts
-
Provide The Reagents Necessary To Carry Out The Following Conversion
Apr 05, 2025
-
Beginning Cash Balance Plus Total Receipts
Apr 05, 2025
-
The Array Perimeter Should Not Be Empty
Apr 05, 2025
-
In A Market System Firm Are Subject To Business Risk
Apr 05, 2025
-
Pressure Injury Training 8 0 Modules I Iv Answers
Apr 05, 2025
Related Post
Thank you for visiting our website which covers about All Of The Following Are Examples Of Product Costs Except . We hope the information provided has been useful to you. Feel free to contact us if you have any questions or need further assistance. See you next time and don't miss to bookmark.