A Process That Performs At A 6 Sigma Level
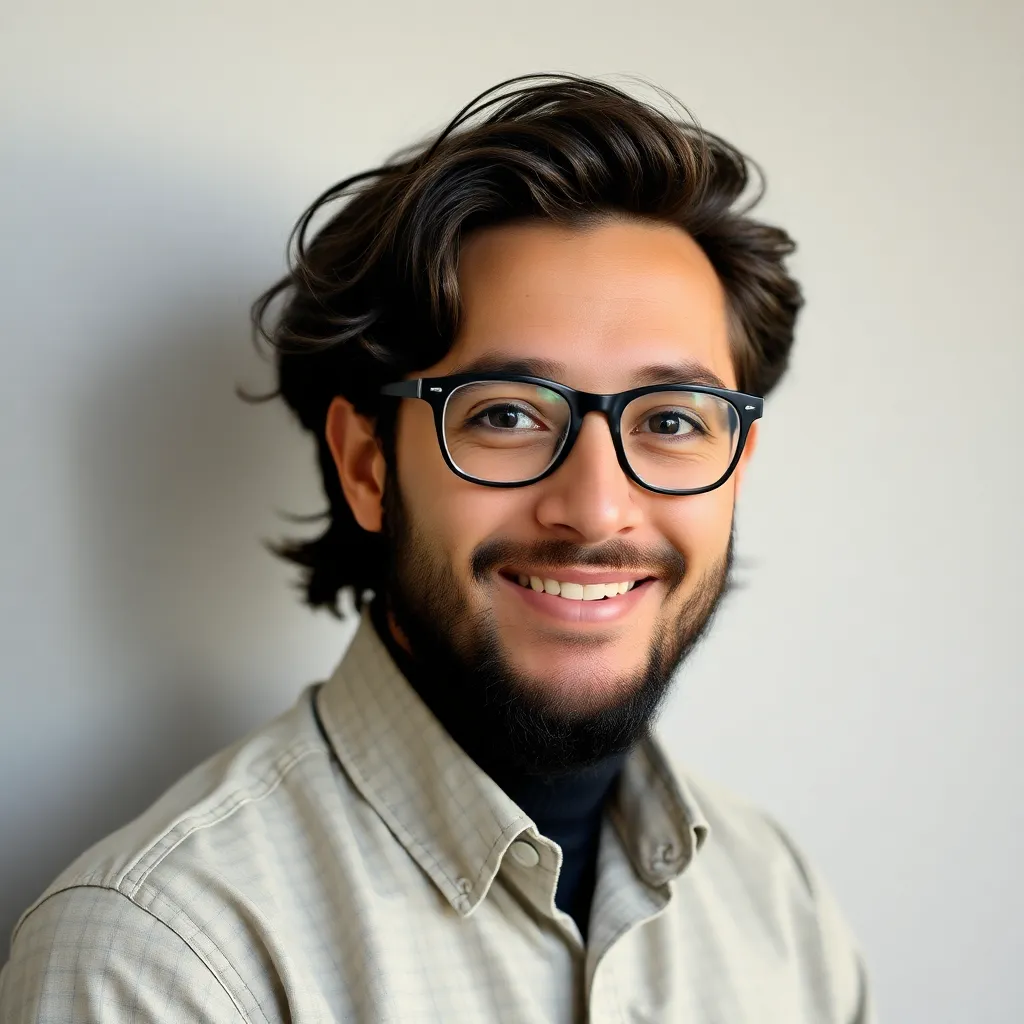
Holbox
Apr 26, 2025 · 6 min read
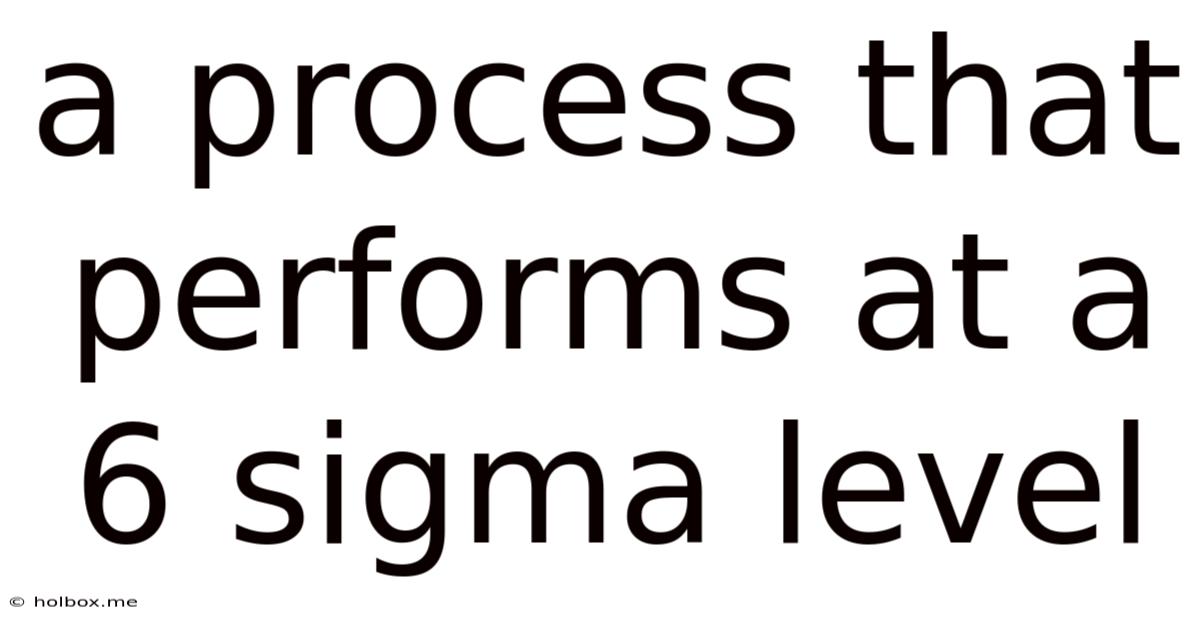
Table of Contents
- A Process That Performs At A 6 Sigma Level
- Table of Contents
- Achieving Six Sigma: A Deep Dive into a Process of Near-Perfection
- Understanding Six Sigma: Beyond the Numbers
- Key Principles of Six Sigma:
- The DMAIC Methodology: A Roadmap to Six Sigma
- 1. Define: Setting the Stage for Success
- 2. Measure: Quantifying the Current State
- 3. Analyze: Uncovering the Root Causes
- 4. Improve: Implementing Solutions and Optimizing the Process
- 5. Control: Sustaining Improvements and Preventing Regression
- Benefits of Implementing a Six Sigma Process
- Challenges in Implementing Six Sigma
- Case Study: Hypothetical Example of a Six Sigma Process in Manufacturing
- Conclusion: Embracing the Pursuit of Excellence
- Latest Posts
- Latest Posts
- Related Post
Achieving Six Sigma: A Deep Dive into a Process of Near-Perfection
The pursuit of perfection is a driving force in many industries. While true perfection may remain elusive, achieving a Six Sigma level of performance represents a remarkable level of operational excellence. This signifies a process with incredibly low defect rates, translating to significant improvements in quality, efficiency, and customer satisfaction. This article delves into the intricacies of a Six Sigma process, examining its methodology, benefits, and the crucial steps involved in its implementation and maintenance.
Understanding Six Sigma: Beyond the Numbers
Six Sigma is a data-driven methodology aimed at minimizing variation and defects in any process. The term itself refers to a statistical measure representing the standard deviation from a process mean. A Six Sigma process exhibits a defect rate of only 3.4 defects per million opportunities (DPMO). This translates to an incredibly high level of precision and consistency, minimizing errors and maximizing efficiency.
It’s important to understand that Six Sigma is more than just a statistical target; it's a comprehensive management philosophy. It emphasizes a structured approach to problem-solving, continuous improvement, and proactive risk management. It empowers employees at all levels to identify and eliminate defects, creating a culture of continuous improvement.
Key Principles of Six Sigma:
- Data-driven decision making: Six Sigma relies heavily on statistical analysis and data-driven insights to identify root causes of defects and measure the effectiveness of improvement initiatives.
- Customer focus: The ultimate goal of Six Sigma is to deliver products and services that meet or exceed customer expectations. Customer needs are central to the entire process.
- Process improvement: The methodology emphasizes systematic improvement of processes to reduce variability and minimize defects.
- Continuous improvement (Kaizen): Six Sigma fosters a culture of continuous learning and improvement, promoting ongoing refinements to optimize processes.
- Teamwork and collaboration: Successful Six Sigma implementation requires strong teamwork and collaboration across departments and functional areas.
The DMAIC Methodology: A Roadmap to Six Sigma
The heart of Six Sigma lies in the DMAIC methodology – a five-phase structured approach to process improvement:
1. Define: Setting the Stage for Success
This initial phase involves clearly defining the project's goals, scope, and objectives. This includes:
- Identifying the problem: Pinpointing the specific process that needs improvement and quantifying the current level of defects.
- Defining customer requirements: Understanding what customers expect from the process and setting performance goals accordingly.
- Setting measurable goals: Establishing clear, specific, measurable, achievable, relevant, and time-bound (SMART) goals for the project.
- Defining project scope: Establishing the boundaries of the project to ensure focus and efficiency.
2. Measure: Quantifying the Current State
This phase focuses on collecting data to understand the current performance of the process. This involves:
- Identifying key process variables: Determining the factors that influence the process and its outcomes.
- Collecting data: Gathering data on the process performance through various methods like surveys, observations, and data mining.
- Analyzing data: Using statistical tools to analyze the data and understand the sources of variation.
- Establishing baseline metrics: Creating a baseline measurement of the current performance of the process to track improvements later. This might include metrics like defect rates, cycle times, and customer satisfaction scores.
3. Analyze: Uncovering the Root Causes
This critical phase involves investigating the root causes of defects and process variations. This often involves:
- Identifying potential root causes: Using tools like fishbone diagrams (Ishikawa diagrams) and brainstorming sessions to identify potential causes of defects.
- Analyzing data to confirm root causes: Applying statistical methods like regression analysis and hypothesis testing to confirm the root causes of defects.
- Prioritizing root causes: Focusing efforts on the most significant root causes that contribute the most to defects.
4. Improve: Implementing Solutions and Optimizing the Process
This phase focuses on developing and implementing solutions to address the identified root causes. This may involve:
- Developing potential solutions: Brainstorming and evaluating various solutions to address the identified root causes.
- Implementing solutions: Implementing the chosen solutions in a controlled manner.
- Monitoring the results: Tracking the impact of the implemented solutions on process performance.
- Making necessary adjustments: Fine-tuning solutions based on the results to ensure optimal performance. This is where iterative improvements are crucial.
5. Control: Sustaining Improvements and Preventing Regression
The final phase aims to maintain the improved performance and prevent future regression. This involves:
- Establishing control charts: Implementing control charts to monitor process performance and detect any deviations from the desired levels.
- Developing standard operating procedures (SOPs): Creating and implementing SOPs to ensure consistency in the process.
- Training employees: Providing employees with the necessary training to maintain the improved process.
- Regular monitoring and review: Continuously monitoring process performance and making adjustments as needed to sustain improvements. This creates a feedback loop for continuous improvement.
Benefits of Implementing a Six Sigma Process
The benefits of achieving a Six Sigma level of performance are substantial and far-reaching:
- Reduced defects: The most obvious benefit is the significant reduction in defects, leading to higher quality products and services.
- Improved efficiency: Streamlined processes lead to increased efficiency, reduced waste, and faster cycle times.
- Increased customer satisfaction: Higher quality products and services result in improved customer satisfaction and loyalty.
- Reduced costs: Lower defect rates, improved efficiency, and reduced waste translate into significant cost savings.
- Improved employee morale: Empowering employees to participate in process improvement initiatives can boost morale and engagement.
- Enhanced competitiveness: Achieving Six Sigma can provide a competitive advantage by differentiating a company from its rivals.
Challenges in Implementing Six Sigma
While Six Sigma offers numerous benefits, implementation can present some challenges:
- Resistance to change: Employees may resist changes to established processes, requiring careful change management strategies.
- Lack of management support: Without strong management support, Six Sigma initiatives can struggle to gain traction.
- Insufficient training: Proper training for employees is essential for successful implementation.
- Data collection difficulties: Gathering and analyzing sufficient data can be time-consuming and complex.
- Maintaining momentum: Sustaining the improvements achieved through Six Sigma requires continuous effort and commitment.
Case Study: Hypothetical Example of a Six Sigma Process in Manufacturing
Let's consider a hypothetical manufacturing process producing precision screws. Before implementing Six Sigma, the defect rate was 10,000 DPMO – far from the Six Sigma target of 3.4 DPMO. The DMAIC methodology was employed:
- Define: The project goal was to reduce the defect rate to below 100 DPMO. Customer requirements focused on precise dimensions and consistent quality.
- Measure: Data collected revealed variations in temperature and humidity affecting the screw-making machinery.
- Analyze: Root cause analysis identified faulty temperature control as the primary contributor to defects.
- Improve: A new temperature control system was installed, and employee training on machine operation was implemented.
- Control: Control charts were implemented to monitor the temperature and humidity, and regular maintenance schedules were established.
After implementing these improvements, the defect rate dropped dramatically to below 50 DPMO, exceeding the initial target. This illustrates how a well-executed Six Sigma project can yield remarkable results.
Conclusion: Embracing the Pursuit of Excellence
Achieving a Six Sigma level of performance is a testament to a company’s commitment to excellence and continuous improvement. While the journey requires dedication, structured methodologies, and the unwavering support of leadership and employees, the benefits – in terms of improved quality, efficiency, customer satisfaction, and profitability – make the pursuit of Six Sigma a worthwhile endeavor. By embracing data-driven decision-making, focusing on customer needs, and fostering a culture of continuous improvement, organizations can achieve a level of operational excellence that sets them apart in today's competitive landscape. The Six Sigma methodology provides the framework; consistent application and a dedication to meticulous execution are the keys to success.
Latest Posts
Latest Posts
-
Which Of The Following Word Elements Refers To Blood
May 07, 2025
-
At Which Osi Model Layer Does A Media Converter Operate
May 07, 2025
-
During Prophase A Homologous Pair Of Chromosomes Consists Of
May 07, 2025
-
Select Whats True Regarding All In One Computers
May 07, 2025
-
Correctly Label The Following Microscopic Anatomy Of The Liver
May 07, 2025
Related Post
Thank you for visiting our website which covers about A Process That Performs At A 6 Sigma Level . We hope the information provided has been useful to you. Feel free to contact us if you have any questions or need further assistance. See you next time and don't miss to bookmark.