A Company Bought A New Machine For Its Warehouse
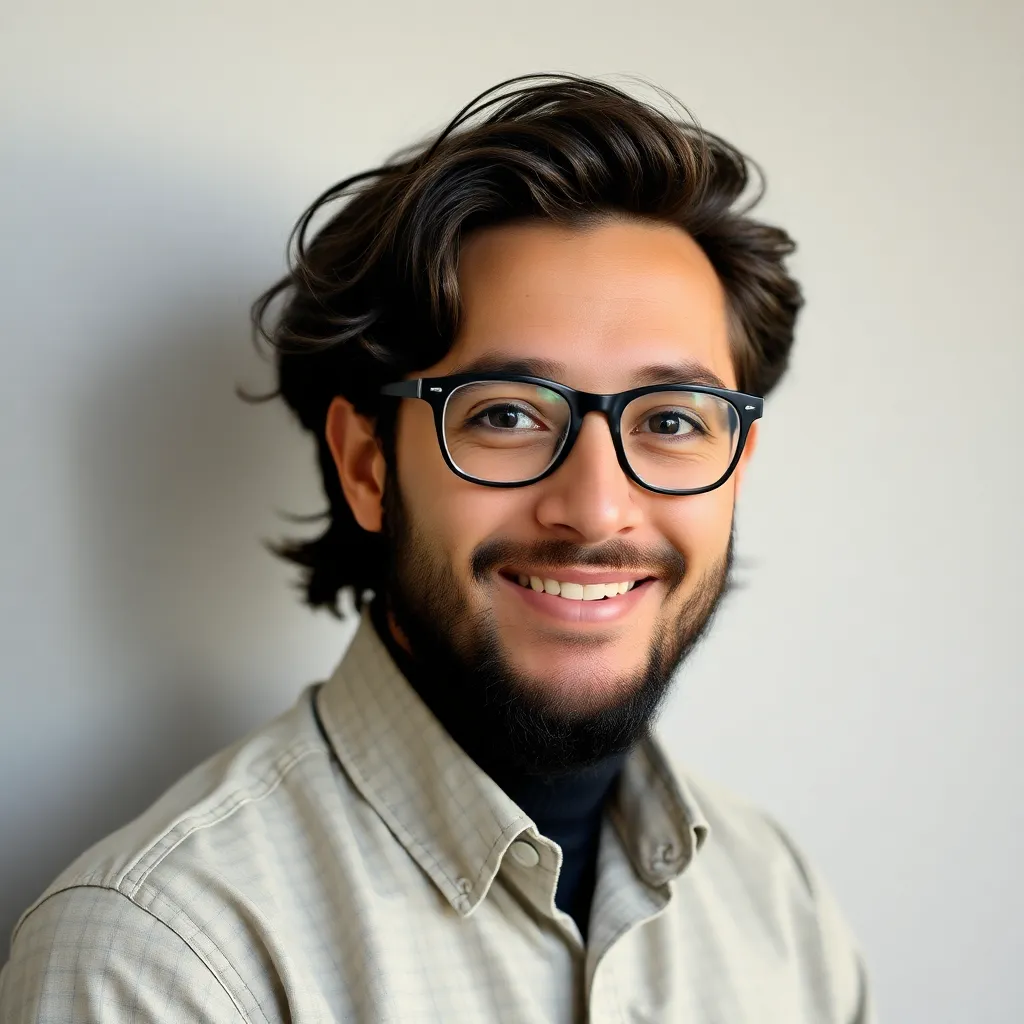
Holbox
Mar 20, 2025 · 6 min read
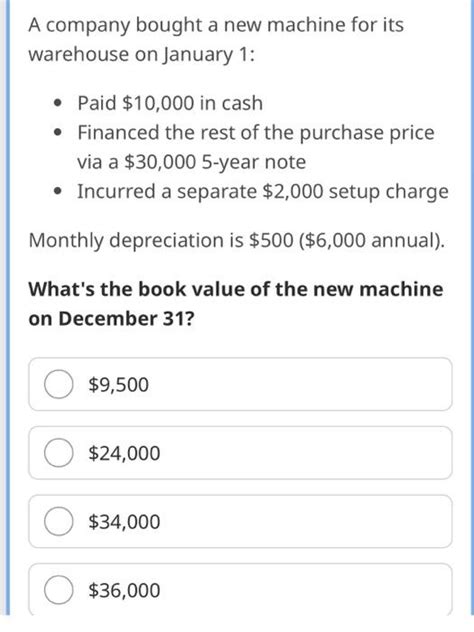
Table of Contents
Streamlining Operations: How a New Warehouse Machine Revolutionized Efficiency at Acme Corp
Acme Corp, a leading distributor of consumer goods, recently invested in a state-of-the-art automated storage and retrieval system (AS/RS) for its primary warehouse. This significant upgrade has already yielded impressive results, streamlining operations, boosting productivity, and improving overall warehouse efficiency. This detailed account explores the process of acquiring and implementing the new machine, the challenges faced, and the tangible benefits reaped by Acme Corp.
The Need for Technological Advancement
Acme Corp’s existing warehouse infrastructure, while functional, was increasingly struggling to keep pace with the company’s rapid growth. Manual processes were becoming bottlenecks, impacting order fulfillment times and increasing labor costs. Order accuracy suffered, leading to customer dissatisfaction and returns. The warehouse space was efficiently utilized, but the processes involved were inefficient, leading to significant operational losses. These challenges highlighted a critical need for technological improvement and automation to maintain competitiveness and meet growing demands.
Identifying the Solution: Automated Storage and Retrieval Systems (AS/RS)
After a thorough market research and assessment of various automation solutions, Acme Corp decided that an AS/RS was the optimal solution. AS/RS systems use automated guided vehicles (AGVs), or in some cases, robotic arms to store and retrieve goods in high-density racking systems. This eliminates manual handling, reduces the risk of errors, and significantly improves speed and efficiency. The selection process involved carefully considering factors such as:
- Throughput Capacity: The AS/RS needed to handle Acme Corp's current order volume with a significant buffer for future growth.
- Scalability: The system had to be adaptable to accommodate increasing inventory levels and future expansion.
- Integration with Existing Systems: Seamless integration with Acme Corp's existing warehouse management system (WMS) was crucial for a smooth transition.
- Cost and Return on Investment (ROI): A thorough cost-benefit analysis was conducted to ensure that the investment was financially viable and would provide a substantial return within a reasonable timeframe.
- Vendor Selection: Acme Corp meticulously evaluated potential vendors based on their reputation, experience, and technical capabilities.
The Acquisition and Implementation Process
The process of acquiring and implementing the AS/RS was a multi-phased project that involved extensive planning and coordination.
Phase 1: Needs Assessment and Vendor Selection
This initial phase involved a detailed assessment of Acme Corp's current warehouse operations and future needs. This assessment identified the specific challenges and opportunities for improvement, which in turn informed the specifications for the new AS/RS. Multiple vendors were then contacted, and their proposals were carefully evaluated based on the predetermined criteria. This phase also included site surveys to ensure that the warehouse space was suitable for the chosen system.
Phase 2: System Design and Customization
Once a vendor was selected, the design and customization phase began. This phase involved close collaboration between Acme Corp's warehouse management team and the vendor's engineers. The system design was tailored to meet Acme Corp's specific requirements, including considerations for product dimensions, weight limitations, and storage capacity needs. This detailed planning phase minimized potential disruption during implementation.
Phase 3: System Installation and Integration
This phase involved the physical installation of the AS/RS equipment and its integration with Acme Corp's existing WMS. This included the installation of the high-density racking system, the AGVs (or robotic arms), the control system, and all necessary software and hardware components. The vendor provided extensive technical support throughout this phase, ensuring a seamless and error-free installation.
Phase 4: Training and Testing
Before the full operational launch, Acme Corp's warehouse staff underwent comprehensive training on the operation and maintenance of the new AS/RS. This training covered all aspects of the system, including operation procedures, safety protocols, and basic troubleshooting. Rigorous testing was conducted to ensure the system's functionality and identify any potential issues before full operation. This included testing throughput capacity, order accuracy, and overall system performance under various simulated scenarios.
Phase 5: Go-Live and Ongoing Optimization
The final phase involved the transition to full operational use of the AS/RS. This included a gradual transition to minimize disruption and maximize efficiency. Ongoing monitoring and optimization of the system was critical to ensuring optimal performance and maximum ROI. This ongoing optimization involves regularly analyzing performance data, identifying areas for improvement, and making necessary adjustments to the system's configuration and operational parameters.
Overcoming Challenges: Lessons Learned
The implementation process wasn't without its challenges. Acme Corp encountered several hurdles, including:
- Integration Issues: Integrating the new AS/RS with the existing WMS proved to be more complex than initially anticipated. This required significant effort from both Acme Corp's IT team and the vendor's integration specialists.
- Staff Training: Training warehouse staff on the new system required a significant investment of time and resources. However, this investment paid off significantly in increased operational efficiency and reduced errors.
- Unexpected Downtime: Despite rigorous testing, some unexpected downtime occurred during the initial operational phase. This highlighted the importance of having contingency plans in place to minimize the impact of such events.
The Tangible Benefits: A Quantifiable Impact
Despite the challenges, the implementation of the AS/RS has yielded significant tangible benefits for Acme Corp. These benefits include:
- Increased Throughput: The AS/RS has significantly increased the warehouse's throughput capacity, allowing Acme Corp to process more orders per day and improve order fulfillment times.
- Reduced Order Fulfillment Times: Order fulfillment times have been dramatically reduced, leading to increased customer satisfaction and repeat business.
- Improved Order Accuracy: The automation of the storage and retrieval process has significantly reduced errors, leading to improved order accuracy and fewer returns.
- Reduced Labor Costs: While the initial investment was significant, the long-term savings in labor costs are substantial. The AS/RS has reduced the need for manual labor, freeing up human resources for more value-added tasks.
- Enhanced Space Utilization: The high-density racking system used by the AS/RS has maximized storage capacity within the existing warehouse space.
- Improved Safety: The automated system has greatly reduced the risk of workplace injuries associated with manual material handling.
- Increased Inventory Visibility: The AS/RS provides real-time visibility into inventory levels, allowing for better inventory management and reduced stockouts.
Conclusion: Investing in the Future of Warehouse Efficiency
Acme Corp's investment in a new AS/RS represents a strategic commitment to enhancing warehouse efficiency and operational excellence. While the initial investment and implementation process required significant planning and resources, the long-term benefits far outweigh the costs. The increased throughput, reduced error rates, improved order fulfillment times, and reduced labor costs have significantly improved Acme Corp's bottom line. The implementation also showcases the importance of thorough planning, effective vendor selection, and comprehensive staff training for a successful automation project. This case study demonstrates that investing in advanced warehouse technology is not merely a cost, but a crucial investment in the future of operational efficiency and competitiveness. The successful implementation of this AS/RS positions Acme Corp for continued growth and success in the dynamic world of consumer goods distribution. Furthermore, it serves as a testament to the transformative power of automation in modern warehouse management. The quantifiable gains in efficiency and cost savings underscore the long-term value of embracing technological advancements in the pursuit of operational excellence.
Latest Posts
Latest Posts
-
A Student Sets Up The Following Equation
Mar 20, 2025
-
Has Have Helped Firms To Concentrate On Their Core Business
Mar 20, 2025
-
A Rectangular Loop Of Wire With Sides Is Located
Mar 20, 2025
-
A Rectangular Loop Of Wire Of Height H
Mar 20, 2025
-
Telephone Wire Is Also Called Pair Wire
Mar 20, 2025
Related Post
Thank you for visiting our website which covers about A Company Bought A New Machine For Its Warehouse . We hope the information provided has been useful to you. Feel free to contact us if you have any questions or need further assistance. See you next time and don't miss to bookmark.