A Basic Characteristic Of Flexible Manufacturing Is That It
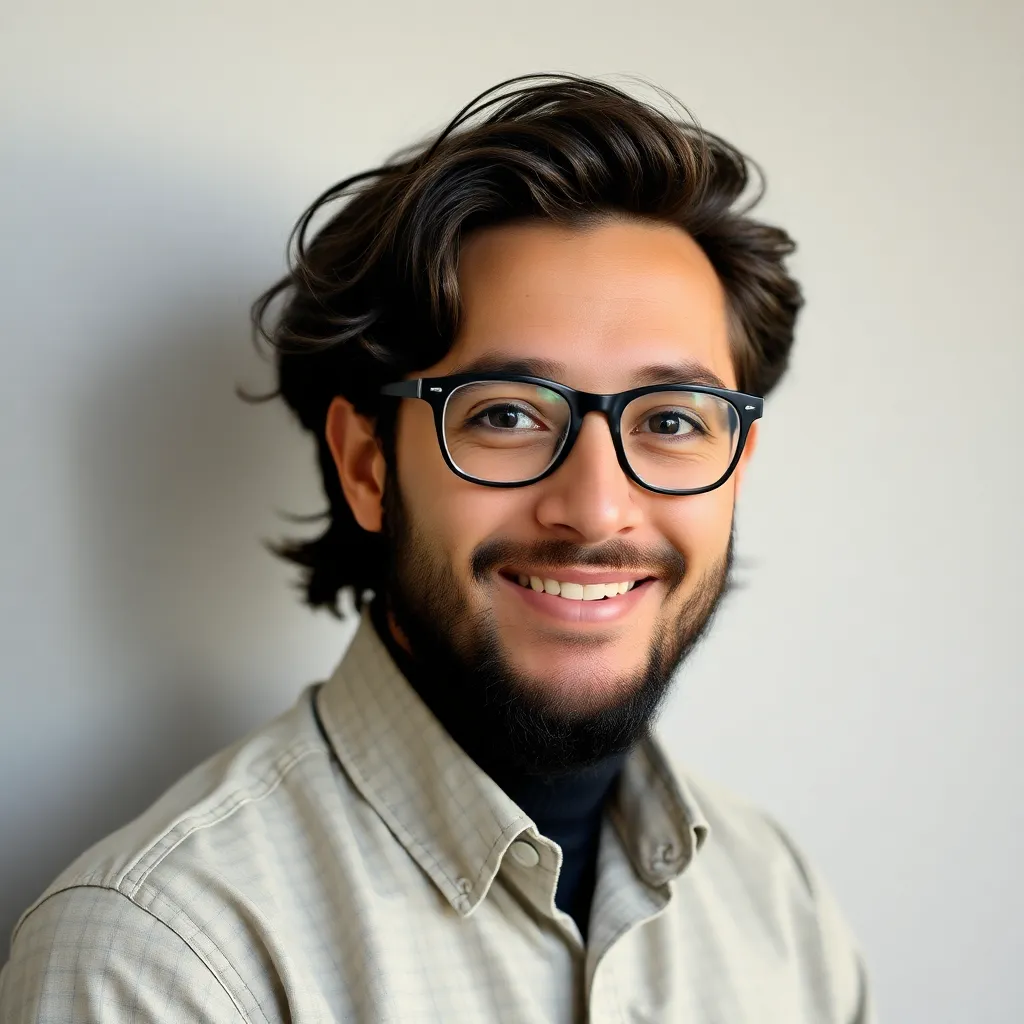
Holbox
Mar 19, 2025 · 6 min read

Table of Contents
A Basic Characteristic of Flexible Manufacturing is that it Adapts
Flexible manufacturing is revolutionizing industries worldwide, enabling businesses to respond swiftly to fluctuating market demands and customize products efficiently. A core characteristic underpinning this transformative capability is its inherent adaptability. This isn't merely the ability to switch between different products; it's a fundamental design principle encompassing various interconnected elements. Let's delve into this defining characteristic of flexible manufacturing systems (FMS) and explore its multifaceted nature.
The Dynamic Nature of Adaptability in Flexible Manufacturing
Adaptability in flexible manufacturing isn't a single feature but a constellation of capabilities working in harmony. It's the system's capacity to readily accommodate:
1. Changes in Product Mix:
This is perhaps the most immediately apparent aspect of FMS adaptability. Unlike traditional manufacturing lines rigidly designed for a single product or a limited range, a flexible system can smoothly transition between producing different items with minimal downtime. This requires:
- Programmable Machines: CNC (Computer Numerical Control) machines, robots, and automated guided vehicles (AGVs) are programmed to execute various operations, allowing for quick reconfiguration.
- Modular Design: The system's layout is designed with modularity in mind. This allows for easy reconfiguration of workstations and the addition or removal of machines as needed to accommodate new product requirements.
- Flexible Routing: The production flow can be easily altered based on the specific product being manufactured. This ensures optimal resource utilization and minimizes bottlenecks.
The ability to swiftly adjust to changing product demands is crucial in today's dynamic market. It allows manufacturers to cater to diverse customer preferences and capitalize on emerging trends. This is achieved through intelligent scheduling algorithms and robust control systems that dynamically allocate resources based on real-time demand forecasts.
2. Variations in Production Volume:
Adaptability also manifests in the system's capacity to adjust production volume to match fluctuating market demand. Whether facing a surge or a lull, the FMS should be able to scale its operations effectively without significant disruptions. This relies on:
- Scalable Infrastructure: The system's capacity for scaling up or down production without major capital investments is crucial. This might involve adding or removing workstations, adjusting machine speeds, or implementing flexible staffing strategies.
- Real-time Monitoring and Control: Continuous monitoring of the production process enables real-time adjustments to production volume based on demand. This ensures that resources are utilized optimally, preventing overproduction or stockouts.
- Automated Inventory Management: Efficient inventory management is essential to support fluctuating production levels. Automated systems that track inventory levels in real time and automatically trigger replenishment orders are critical.
This responsiveness reduces inventory holding costs and prevents shortages, allowing for optimal response to fluctuating demand. This reduces lead times and improves customer satisfaction.
3. Incorporating Technological Advancements:
A truly flexible manufacturing system must be capable of integrating new technologies and processes without requiring a complete overhaul. This requires:
- Open Architecture Systems: The system's architecture should be open and modular, allowing for the easy integration of new machines, software, and technologies.
- Continuous Improvement Processes: A culture of continuous improvement is essential. Regular reviews and assessments of the system's performance identify areas for optimization and integration of emerging technologies.
- Skilled Workforce: The success of an FMS relies heavily on a skilled workforce that can operate and maintain the system effectively and adapt to technological changes. Training and upskilling are crucial for maintaining a competitive edge.
The ability to adapt to technological advancements ensures the long-term viability and competitiveness of the manufacturing operation. This also reduces the risk of technological obsolescence and maintains the facility's cutting-edge status.
The Key Components Enabling Adaptability
Several core components work in concert to achieve the adaptability characteristic of flexible manufacturing:
1. Computer-Integrated Manufacturing (CIM):
CIM acts as the nervous system of an FMS, integrating all aspects of the manufacturing process into a single, coordinated system. This centralized control system enables seamless data flow and facilitates efficient decision-making, leading to improved responsiveness to changes in demand or product specifications.
2. Programmable Logic Controllers (PLCs):
PLCs are the brains behind many automated processes in an FMS. They control the individual machines and coordinate their actions, allowing for easy reprogramming to accommodate different products or production volumes. Their ability to handle complex control logic is essential for efficient and adaptable operation.
3. Automated Guided Vehicles (AGVs):
AGVs automate material handling within the factory, transporting components and finished goods between workstations. Their flexibility allows for dynamic routing adjustments, maximizing efficiency in response to changes in the production schedule.
4. Flexible Manufacturing Cells (FMCs):
FMCs are groups of machines dedicated to specific manufacturing processes. They are designed to be highly adaptable, capable of handling a range of tasks and easily reconfigured to accommodate new products or processes. This modularity is a cornerstone of FMS adaptability.
Benefits of Adaptability in Flexible Manufacturing
The adaptability inherent in flexible manufacturing systems provides numerous benefits, including:
- Increased Productivity: By optimizing resource allocation and minimizing downtime, FMSs significantly improve overall productivity.
- Reduced Lead Times: Faster production processes and streamlined workflows lead to reduced lead times, enabling quicker delivery to customers.
- Improved Product Quality: The precision and consistency of automated processes enhance product quality and reduce defects.
- Enhanced Customer Satisfaction: Meeting customer demands for customized products and short lead times enhances satisfaction and loyalty.
- Greater Flexibility: The ability to quickly adapt to changing market conditions provides a competitive edge, allowing businesses to respond quickly to new opportunities.
- Reduced Costs: Optimizing resource utilization, minimizing waste, and improving efficiency significantly reduce manufacturing costs.
- Improved Efficiency: Automated processes and streamlined workflows improve the overall efficiency of the manufacturing operation.
Challenges of Implementing Flexible Manufacturing Systems
While offering substantial benefits, implementing FMS presents several challenges:
- High Initial Investment: The cost of implementing an FMS can be significant, requiring a substantial upfront investment in equipment and software.
- Complex Integration: Integrating various components and technologies into a cohesive system can be complex and require specialized expertise.
- Training and Skills Gap: Operating and maintaining an FMS requires a skilled workforce with specialized training.
- System Maintenance: Maintaining the complex machinery and software of an FMS requires ongoing maintenance and potentially specialized technicians.
Conclusion: Embracing the Adaptability of the Future
The adaptability inherent in flexible manufacturing systems is not just a feature; it's the fundamental driver of their transformative potential. By seamlessly adjusting to changing product mixes, production volumes, and technological advancements, FMSs empower manufacturers to remain competitive in today's dynamic market. While the initial investment and implementation challenges are substantial, the long-term benefits – increased productivity, reduced costs, enhanced customer satisfaction, and improved agility – make flexible manufacturing a crucial element in achieving sustainable manufacturing success. The ability to adapt is no longer a luxury; it's a necessity for survival and growth in the modern manufacturing landscape. Embracing adaptability is not merely adopting a technology; it's transforming the very core of manufacturing operations, paving the way for a more responsive, efficient, and profitable future. The future of manufacturing is undeniably flexible, and its ability to adapt is the key to unlocking its full potential.
Latest Posts
Latest Posts
-
Customers Receive Rewards Points Based On The Purchase Type
Mar 19, 2025
-
Which Statement Is An Accurate Summary Of Meiosis
Mar 19, 2025
-
Absolute Advantage Is Found By Comparing Different Producers
Mar 19, 2025
-
At A Team Meeting The Restaurant Manager
Mar 19, 2025
-
All Of The Following Are Heart Valves Except
Mar 19, 2025
Related Post
Thank you for visiting our website which covers about A Basic Characteristic Of Flexible Manufacturing Is That It . We hope the information provided has been useful to you. Feel free to contact us if you have any questions or need further assistance. See you next time and don't miss to bookmark.