With Regard To Suppliers Lean Systems Typically Require
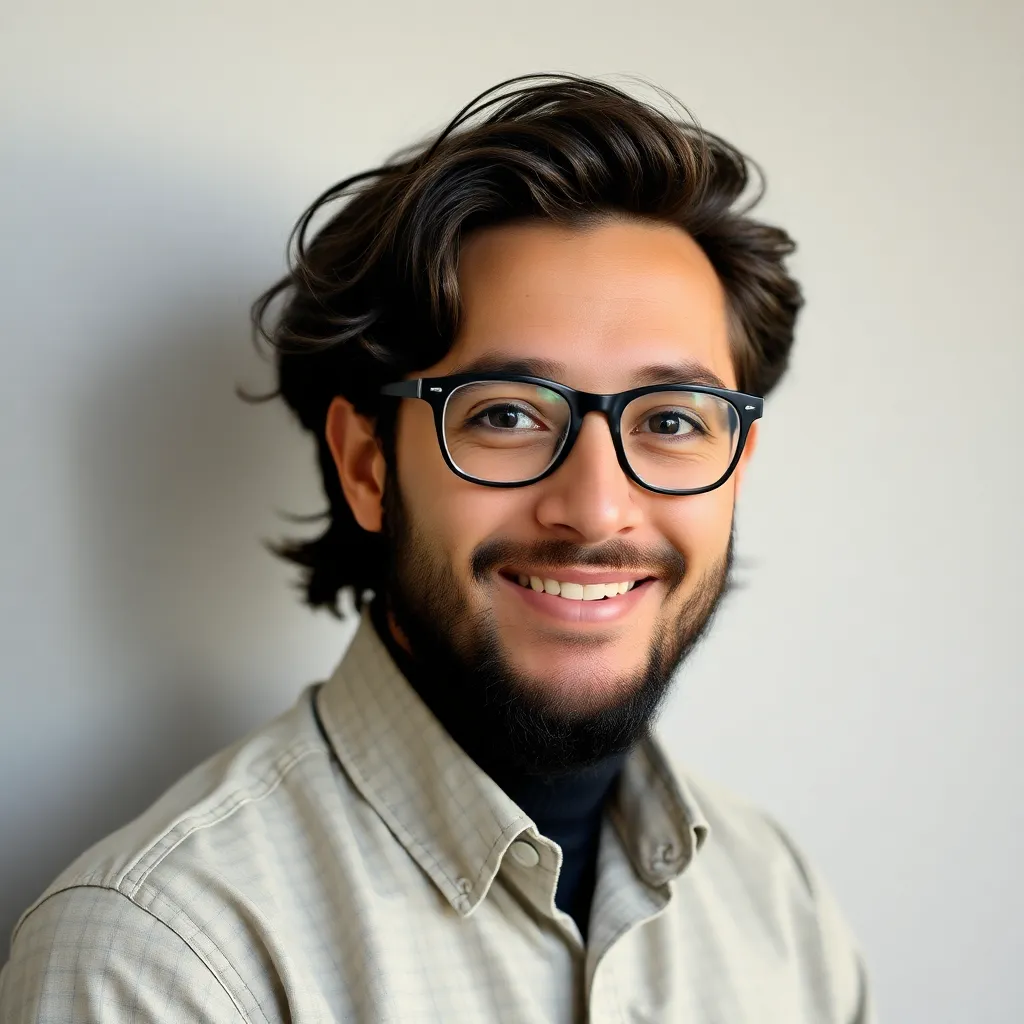
Holbox
Apr 07, 2025 · 7 min read

Table of Contents
- With Regard To Suppliers Lean Systems Typically Require
- Table of Contents
- With Regard to Suppliers: Lean Systems Typically Require
- The Core Principles: Why Lean Demands Specific Supplier Relationships
- 1. Quality Focus: Zero Defects is Paramount
- 2. Just-in-Time (JIT) Delivery: Precision and Predictability
- 3. Continuous Improvement (Kaizen): A Culture of Ongoing Enhancement
- 4. Transparency and Collaboration: Open Communication is Key
- 5. Cost Reduction: Value Engineering and Efficiency
- Supplier Selection in a Lean Environment
- Managing Lean Supplier Relationships
- The Benefits of a Lean Supplier Network
- Conclusion: Embracing the Lean Supplier Partnership
- Latest Posts
- Latest Posts
- Related Post
With Regard to Suppliers: Lean Systems Typically Require
Lean manufacturing, a philosophy focused on eliminating waste and maximizing value, significantly impacts the relationship between a company and its suppliers. Implementing a lean system necessitates a fundamental shift in how suppliers are selected, managed, and integrated into the overall production process. This article delves into the specific requirements lean systems typically place on suppliers, exploring the key elements of a successful lean supplier partnership.
The Core Principles: Why Lean Demands Specific Supplier Relationships
At its heart, lean manufacturing is about optimizing the entire value stream, from raw material sourcing to final product delivery. This holistic approach means that suppliers are not simply vendors; they are integral partners in the pursuit of continuous improvement. Lean systems typically require suppliers to adhere to several core principles:
1. Quality Focus: Zero Defects is Paramount
Lean systems place an unwavering emphasis on quality. This isn't just about meeting minimum specifications; it's about striving for zero defects. Suppliers working within a lean environment must implement rigorous quality control measures throughout their processes. This includes:
- Statistical Process Control (SPC): Implementing SPC allows for the early detection and correction of potential quality issues, preventing defects from reaching the manufacturing floor.
- Robust Quality Management Systems: ISO 9001 certification or similar standards demonstrate a commitment to consistent quality and provide a framework for continuous improvement.
- Proactive Problem Solving: Suppliers must foster a culture where identifying and resolving quality issues is prioritized, often through tools like 5 Whys analysis or Kaizen events.
- Traceability: Complete traceability of materials and processes is crucial for quickly identifying and addressing the root cause of any defects.
2. Just-in-Time (JIT) Delivery: Precision and Predictability
JIT delivery is a cornerstone of lean manufacturing. It eliminates the need for large inventories by ensuring that materials arrive exactly when they are needed. This requires exceptional coordination and collaboration between the manufacturer and its suppliers. Lean systems typically require suppliers to:
- Develop Accurate Forecasting: Reliable demand forecasting is essential for JIT to function effectively. This often involves close collaboration with the manufacturer to share accurate sales and production data.
- Implement Efficient Logistics: Suppliers must have robust logistics systems in place to ensure timely and reliable delivery. This might include Kanban systems, electronic data interchange (EDI), or other methods for precise inventory management.
- Maintain High On-Time Delivery Rates: Consistent on-time delivery is critical for avoiding disruptions in the production process. Any delays can create bottlenecks and negatively impact the entire value stream.
- Flexibility and Responsiveness: Lean systems often require suppliers to be flexible and responsive to sudden changes in demand. The ability to quickly adjust production schedules is crucial for maintaining a smooth flow of materials.
3. Continuous Improvement (Kaizen): A Culture of Ongoing Enhancement
Lean manufacturing embraces a culture of continuous improvement. This means that both the manufacturer and its suppliers must be committed to constantly seeking ways to improve efficiency, reduce waste, and enhance quality. Lean systems typically require suppliers to:
- Embrace Kaizen Events: Participating in regular Kaizen events (focused improvement projects) allows for collaborative problem-solving and the implementation of improvements across the supply chain.
- Utilize Lean Tools and Techniques: Suppliers should be familiar with and implement lean tools such as Value Stream Mapping, 5S, and Poka-Yoke (error-proofing) to identify and eliminate waste.
- Share Best Practices: Open communication and the sharing of best practices between the manufacturer and its suppliers are crucial for driving continuous improvement throughout the supply chain.
- Data-Driven Decision Making: Using data to track performance and identify areas for improvement is essential for a culture of continuous improvement.
4. Transparency and Collaboration: Open Communication is Key
Trust and transparency are paramount in a lean supply chain. Open communication between the manufacturer and its suppliers is crucial for effective collaboration and problem-solving. Lean systems typically require suppliers to:
- Share Real-Time Data: Sharing real-time data on inventory levels, production progress, and quality metrics allows for proactive problem-solving and better coordination.
- Foster Strong Communication Channels: Establishing clear and efficient communication channels, such as regular meetings and shared online platforms, is critical for maintaining transparency and collaboration.
- Develop Collaborative Problem-Solving Processes: Suppliers should be involved in problem-solving processes, contributing their expertise and insights to identify and address issues effectively.
- Build Strong Relationships: Developing strong, trusting relationships built on mutual respect and shared goals is crucial for long-term success.
5. Cost Reduction: Value Engineering and Efficiency
While maintaining quality, lean systems demand a focus on cost reduction. This isn't about cutting corners; it's about identifying and eliminating waste throughout the supply chain. Lean systems typically require suppliers to:
- Participate in Value Engineering: Collaborating on value engineering exercises to identify ways to reduce costs without compromising quality is crucial for optimizing the entire value stream.
- Improve Efficiency: Suppliers must continuously strive to improve their processes to reduce waste and improve efficiency. This might involve streamlining workflows, automating processes, or improving material handling.
- Optimize Inventory Management: Minimizing inventory levels helps to reduce storage costs and the risk of obsolescence. This requires close coordination with the manufacturer to ensure just-in-time delivery.
- Explore Cost-Effective Materials and Processes: Suppliers should actively seek out cost-effective materials and processes without compromising quality or performance.
Supplier Selection in a Lean Environment
Selecting the right suppliers is a critical step in implementing a lean system. The selection process should be rigorous and focus on identifying suppliers who can meet the specific requirements of the lean philosophy. This includes:
- Evaluating Supplier Capabilities: A thorough assessment of the supplier's capabilities, including quality management systems, production capacity, and logistics infrastructure, is essential.
- Assessing Supplier Culture: Understanding the supplier's culture and its commitment to continuous improvement is crucial for ensuring a successful partnership.
- Verifying Supplier Compliance: Ensuring that the supplier complies with all relevant regulations and standards is vital for mitigating risks.
- Building Strong Relationships: Developing strong, collaborative relationships with suppliers is key to achieving the goals of a lean system.
Managing Lean Supplier Relationships
Managing supplier relationships effectively is crucial for the success of a lean system. This requires ongoing communication, collaboration, and monitoring of performance. Key aspects of managing lean supplier relationships include:
- Regular Performance Reviews: Conducting regular performance reviews to monitor key performance indicators (KPIs) such as on-time delivery, quality, and cost is essential for identifying areas for improvement.
- Continuous Improvement Initiatives: Collaborating with suppliers on continuous improvement initiatives, such as Kaizen events, helps to drive efficiency and quality improvements throughout the supply chain.
- Conflict Resolution Mechanisms: Establishing clear processes for resolving conflicts and addressing issues promptly is essential for maintaining a strong and productive supplier relationship.
- Open Communication: Maintaining open and transparent communication with suppliers is crucial for fostering trust and collaboration.
The Benefits of a Lean Supplier Network
Implementing a lean system and establishing a strong network of lean-capable suppliers offers significant advantages, including:
- Reduced Costs: Eliminating waste and improving efficiency throughout the supply chain leads to significant cost reductions.
- Improved Quality: Implementing rigorous quality control measures throughout the supply chain leads to higher quality products and fewer defects.
- Increased Efficiency: Optimizing the flow of materials and information throughout the supply chain improves overall efficiency.
- Enhanced Flexibility: A lean supply chain is more flexible and responsive to changes in demand, allowing for quicker adjustments to production schedules.
- Strengthened Supplier Relationships: Collaborating with suppliers on continuous improvement initiatives fosters stronger and more productive relationships.
Conclusion: Embracing the Lean Supplier Partnership
In conclusion, lean systems place significant demands on suppliers, requiring a fundamental shift towards collaborative partnerships focused on quality, efficiency, and continuous improvement. By carefully selecting suppliers, fostering strong relationships, and implementing effective management strategies, manufacturers can leverage the power of a lean supplier network to achieve significant cost savings, enhance quality, and improve overall competitiveness. The journey towards a truly lean enterprise is inextricably linked to the commitment and capabilities of its supply chain partners. The focus should always be on creating a mutually beneficial, collaborative ecosystem where continuous improvement is the shared goal.
Latest Posts
Latest Posts
-
Give The Iupac Name Of The Following Carboxylate Salt
Apr 14, 2025
-
Asthma Can Be Triggered By All Of The Following Except
Apr 14, 2025
-
During Exercise Dehydration Will Cause A Net Movement Of Water
Apr 14, 2025
-
A Company That Uses Job Order Costing
Apr 14, 2025
-
Determine Ix In The Circuit Of Fig P2 15
Apr 14, 2025
Related Post
Thank you for visiting our website which covers about With Regard To Suppliers Lean Systems Typically Require . We hope the information provided has been useful to you. Feel free to contact us if you have any questions or need further assistance. See you next time and don't miss to bookmark.