With Regard To Suppliers Lean Systems Typically Involve
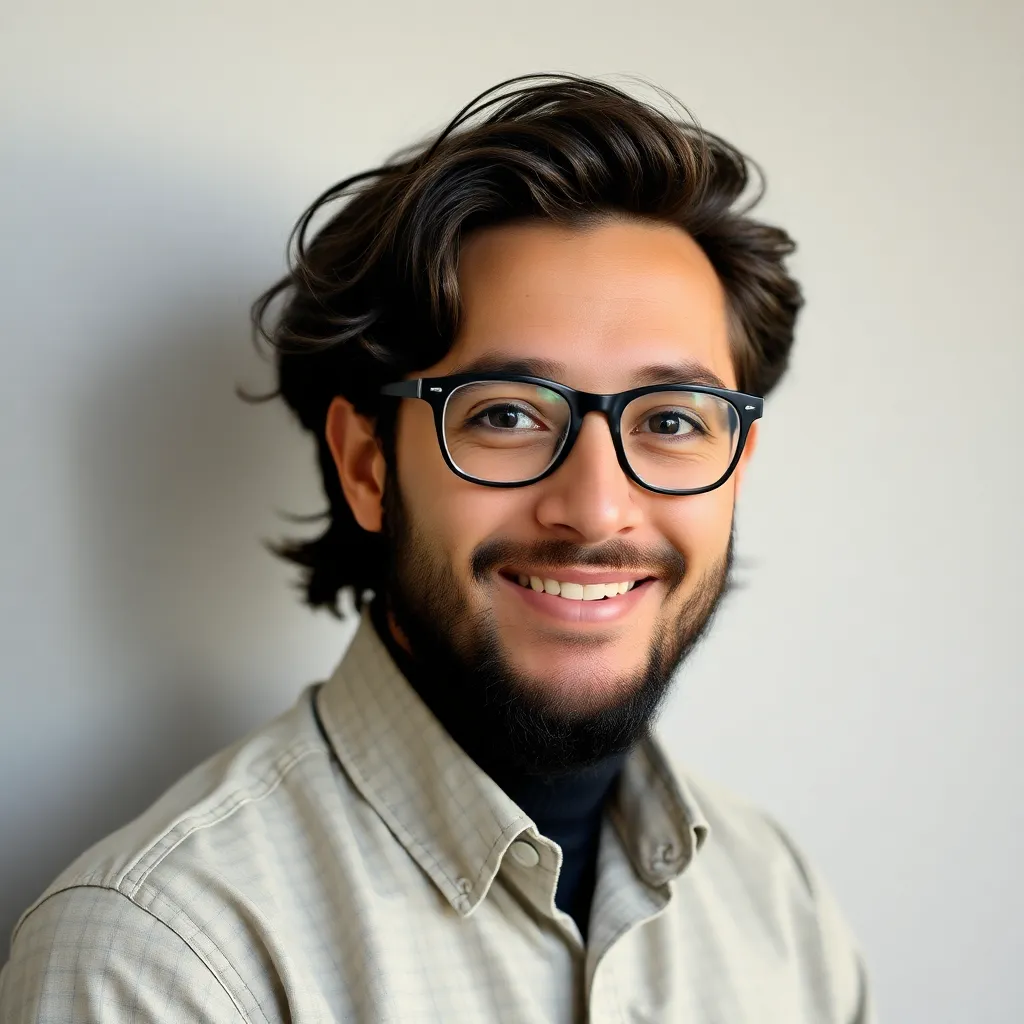
Holbox
Apr 04, 2025 · 6 min read

Table of Contents
- With Regard To Suppliers Lean Systems Typically Involve
- Table of Contents
- With Regard to Suppliers: Lean Systems Typically Involve
- The Foundation: Understanding Lean Principles and Supplier Relationships
- Key Ways Lean Systems Involve Suppliers
- 1. Collaborative Partnerships & Long-Term Relationships
- 2. Supplier Development & Capacity Building
- 3. Just-in-Time (JIT) Inventory Management
- 4. Continuous Improvement (Kaizen) and Value Stream Mapping (VSM)
- 5. Supplier Selection and Evaluation
- Challenges in Implementing Lean with Suppliers
- Best Practices for Successful Lean Supplier Collaboration
- Conclusion: A Symbiotic Relationship for Success
- Latest Posts
- Latest Posts
- Related Post
With Regard to Suppliers: Lean Systems Typically Involve
Lean systems, built on the principles of eliminating waste and maximizing value, significantly impact a company's relationship with its suppliers. Implementing lean principles doesn't just streamline internal processes; it fundamentally reshapes the entire supply chain. This article delves deep into the specific ways lean systems typically involve suppliers, exploring the benefits, challenges, and best practices for successful collaboration.
The Foundation: Understanding Lean Principles and Supplier Relationships
Before diving into the specifics, it's crucial to establish a common understanding of lean principles and their application to supplier relationships. Lean manufacturing, often associated with Toyota's production system, focuses on identifying and eliminating seven types of waste (muda):
- Transportation: Unnecessary movement of materials.
- Inventory: Excess stock tying up capital and space.
- Motion: Unnecessary movements of people or equipment.
- Waiting: Delays in the production process.
- Overproduction: Producing more than needed.
- Over-processing: Performing more work than necessary.
- Defects: Errors leading to rework or scrap.
Applying these principles to supplier relationships means minimizing waste throughout the entire supply chain, from raw material sourcing to final product delivery. This requires a collaborative and trust-based relationship between the buyer and supplier, moving beyond the traditional adversarial transactional model.
Key Ways Lean Systems Involve Suppliers
Lean systems typically involve suppliers in several key ways:
1. Collaborative Partnerships & Long-Term Relationships
Lean emphasizes building strong, long-term relationships with suppliers. This involves moving beyond simple transactional exchanges to fostering a collaborative partnership where both parties work together to achieve mutual success. This often involves:
- Joint problem-solving: Open communication and shared responsibility for identifying and resolving issues throughout the supply chain.
- Shared goals: Aligning supplier goals with the buyer's lean objectives.
- Trust and transparency: Openly sharing information and data to improve efficiency and reduce waste.
- Mutual improvement: Continuously working together to improve processes and reduce costs.
Example: A manufacturer might work with a key supplier to jointly develop a new, more efficient packaging system that reduces waste and improves delivery times.
2. Supplier Development & Capacity Building
Lean systems recognize that supplier capabilities directly impact overall efficiency. Therefore, many companies actively invest in developing their suppliers' lean capabilities through:
- Training and education: Providing training on lean principles, techniques, and tools.
- Process improvement assistance: Offering support and guidance in implementing lean practices within the supplier's operations.
- Technology transfer: Sharing technology and knowledge to help suppliers improve their efficiency and quality.
- Financial incentives: Offering incentives for suppliers who meet or exceed lean performance targets.
Example: A company might offer financial assistance to a supplier to upgrade their equipment, enabling them to improve production speed and reduce defects.
3. Just-in-Time (JIT) Inventory Management
JIT is a cornerstone of lean systems. It requires close collaboration with suppliers to ensure that materials are delivered exactly when needed, minimizing inventory holding costs and reducing the risk of obsolescence or damage. This necessitates:
- Precise demand forecasting: Accurate prediction of future demand to optimize production scheduling.
- Reliable delivery systems: Implementing robust transportation and logistics systems to ensure timely delivery.
- Real-time information sharing: Utilizing technology to track inventory levels and delivery schedules in real-time.
- Close communication: Maintaining open and continuous communication to address any potential disruptions.
Example: A car manufacturer might work with a parts supplier to implement a system where parts are delivered directly to the assembly line, just as they are needed.
4. Continuous Improvement (Kaizen) and Value Stream Mapping (VSM)
Lean systems emphasize continuous improvement. This involves regularly reviewing processes and identifying areas for improvement across the entire supply chain. Value stream mapping is a crucial tool for visualizing the flow of materials and information, identifying bottlenecks, and generating improvement ideas. This collaborative process often involves:
- Joint VSM workshops: Collaborative sessions with suppliers to map the entire value stream, from raw material sourcing to final product delivery.
- Regular performance reviews: Frequent meetings to review performance against targets and identify areas for improvement.
- Problem-solving techniques: Utilizing tools like 5 Whys, root cause analysis, and other lean problem-solving methods.
Example: A company might conduct a joint VSM workshop with a supplier to identify and eliminate bottlenecks in the delivery process, thereby reducing lead times and improving efficiency.
5. Supplier Selection and Evaluation
Lean principles influence the process of selecting and evaluating suppliers. The focus shifts from simply finding the cheapest supplier to identifying partners who align with the company's lean goals and have the capability to meet the required quality and delivery standards. This typically involves:
- Stricter supplier selection criteria: Beyond price, evaluating factors like lean capabilities, quality management systems, and delivery performance.
- Regular supplier audits: Conducting audits to assess the supplier's adherence to lean principles and quality standards.
- Performance measurement: Establishing key performance indicators (KPIs) to track supplier performance and identify areas for improvement.
Example: A company might establish a scoring system for evaluating potential suppliers, weighing factors like lean capabilities, quality, and delivery performance equally with price.
Challenges in Implementing Lean with Suppliers
While the benefits of lean supplier collaboration are significant, implementation can present several challenges:
- Resistance to change: Suppliers may resist adopting new processes or technologies.
- Lack of trust: Building trust and collaboration can take time and effort.
- Information asymmetry: Information sharing may be difficult due to competitive concerns.
- Coordination challenges: Coordinating activities across multiple suppliers can be complex.
- Cost of implementation: Implementing lean practices can require upfront investment.
Overcoming these challenges requires strong leadership, effective communication, and a willingness to invest in building long-term relationships.
Best Practices for Successful Lean Supplier Collaboration
Several best practices can increase the likelihood of success when implementing lean principles with suppliers:
- Start small and build momentum: Begin with a pilot project involving a select group of key suppliers.
- Build strong relationships: Invest time in building trust and collaboration with suppliers.
- Use technology to improve communication and collaboration: Implement systems for real-time information sharing.
- Provide training and support: Equip suppliers with the knowledge and resources they need to implement lean practices.
- Establish clear performance metrics: Track and monitor supplier performance against established KPIs.
- Regularly review and improve processes: Continuously seek ways to optimize the supply chain.
- Establish a collaborative culture: Foster a culture of mutual respect and cooperation.
Conclusion: A Symbiotic Relationship for Success
Successfully integrating suppliers into a lean system is not a one-time event but an ongoing journey of continuous improvement. It requires a fundamental shift in the mindset of both buyers and suppliers, moving from an adversarial transactional relationship to a collaborative partnership focused on shared success. By embracing the principles of long-term partnerships, joint problem-solving, and continuous improvement, companies can reap the significant benefits of a lean supply chain – reduced costs, improved quality, increased efficiency, and a more resilient and responsive business. The key lies in recognizing that a truly lean system is not just about internal optimization but also about fostering a symbiotic relationship with suppliers, where mutual success becomes the driving force of innovation and growth.
Latest Posts
Latest Posts
-
Differences In Black White Accumulation Of Wealth Are Not Influenced By
Apr 17, 2025
-
Retailing Is Defined As The Set Of Business Activities That
Apr 17, 2025
-
Determine The Inductor Current For All If
Apr 17, 2025
-
A Call Provision Grants The Bond Issuer The
Apr 17, 2025
-
A Complex Unlearned And Fixed Pattern Of Behavior
Apr 17, 2025
Related Post
Thank you for visiting our website which covers about With Regard To Suppliers Lean Systems Typically Involve . We hope the information provided has been useful to you. Feel free to contact us if you have any questions or need further assistance. See you next time and don't miss to bookmark.