Who Makes Sure Whmis Requirements Are Implemented In A Workplace
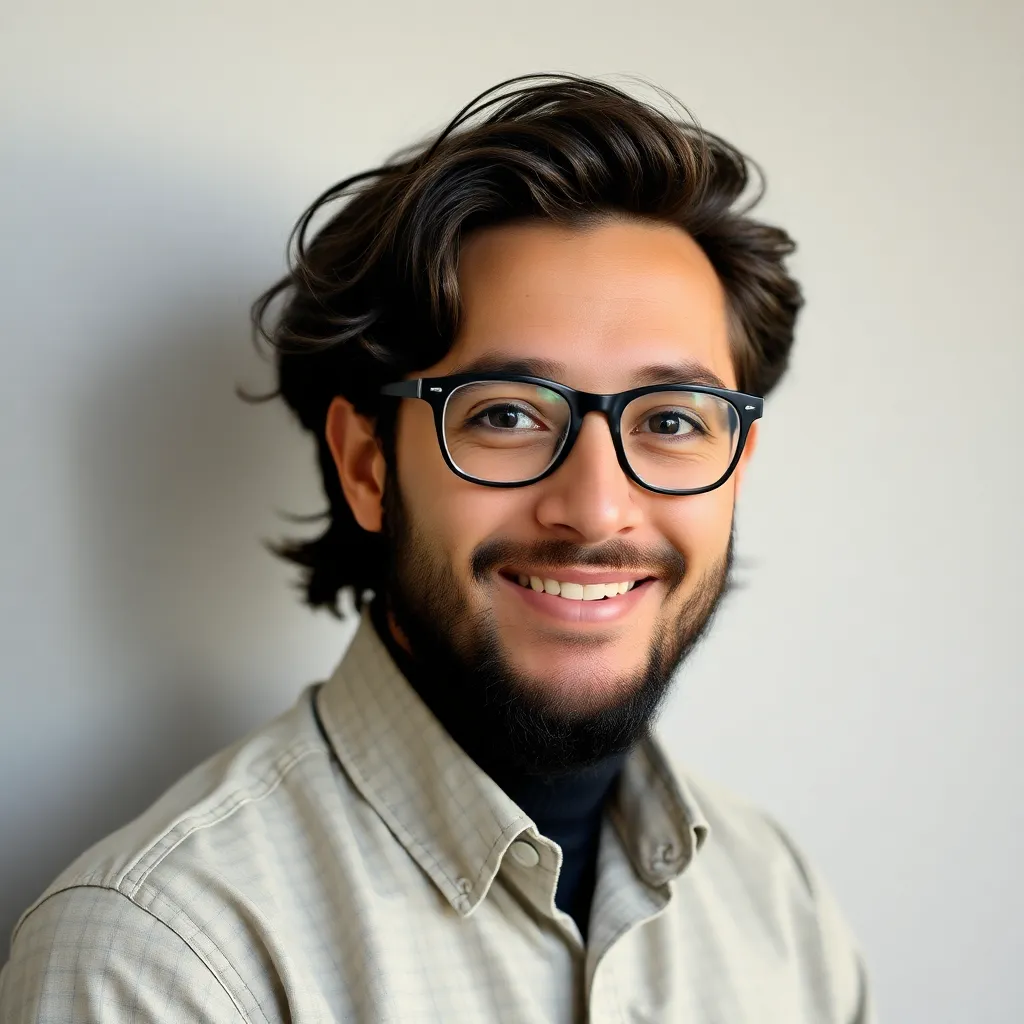
Holbox
Mar 12, 2025 · 6 min read
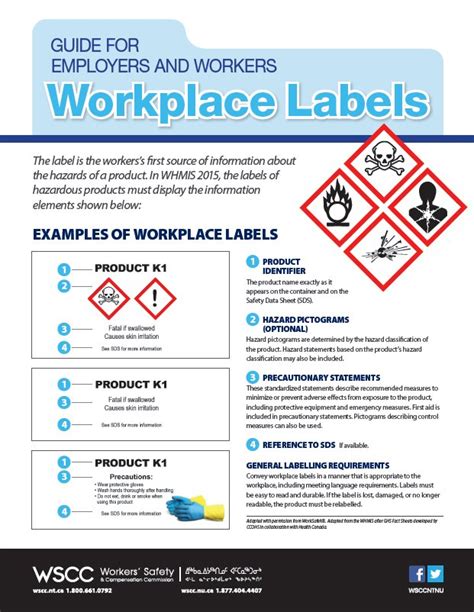
Table of Contents
- Who Makes Sure Whmis Requirements Are Implemented In A Workplace
- Table of Contents
- Who Makes Sure WHMIS Requirements Are Implemented in a Workplace?
- The Employer's Crucial Role in WHMIS Compliance
- 1. Providing Training and Information
- 2. Providing and Maintaining SDSs
- 3. Implementing Control Measures
- 4. Maintaining Compliance Records
- The Supervisor's Role: Implementing and Monitoring WHMIS
- The Worker's Responsibility: Safe Handling and Reporting
- Other Stakeholders: Joint Responsibility
- Consequences of Non-Compliance
- Conclusion: A Shared Commitment to Safety
- Latest Posts
- Related Post
Who Makes Sure WHMIS Requirements Are Implemented in a Workplace?
Workplace safety is paramount, and the Globally Harmonized System of Classification and Labelling of Chemicals (GHS), implemented in Canada as the Workplace Hazardous Materials Information System (WHMIS), plays a crucial role in ensuring a safe working environment. But who is responsible for ensuring that WHMIS requirements are properly implemented and followed? The answer isn't a single person or department; rather, it's a collaborative effort involving various stakeholders. This article delves into the responsibilities of employers, supervisors, workers, and other key players in maintaining WHMIS compliance.
The Employer's Crucial Role in WHMIS Compliance
The employer bears the ultimate responsibility for WHMIS implementation. This responsibility is non-negotiable and extends to all aspects of the system. This includes, but is not limited to:
1. Providing Training and Information
Employers are legally obligated to provide comprehensive training to all workers who handle hazardous materials. This training must cover:
- Hazard identification: Recognizing hazardous materials through labels, safety data sheets (SDS), and other means.
- Safe handling procedures: Understanding the proper techniques for storing, using, and disposing of hazardous materials.
- Emergency response: Knowing what to do in case of spills, leaks, or other accidents involving hazardous materials.
- WHMIS legislation: Familiarizing workers with their rights and responsibilities under WHMIS legislation.
The training must be provided before workers handle any hazardous materials and must be updated regularly to reflect any changes in procedures or legislation. The training should be tailored to the specific hazards present in the workplace and the tasks performed by the workers. Documentation of this training is essential for demonstrating compliance.
2. Providing and Maintaining SDSs
Employers must ensure that Safety Data Sheets (SDS) are readily available for all hazardous materials used or stored in the workplace. SDSs provide detailed information about the hazards associated with a particular material, including its physical and chemical properties, health effects, and safe handling procedures. Employers must:
- Obtain SDSs: Procure SDSs from suppliers whenever hazardous materials are purchased.
- Maintain SDSs: Keep SDSs up-to-date and readily accessible to workers. This often involves a centralized system for storing and retrieving SDSs, such as a dedicated computer or file cabinet.
- Translate SDSs: If necessary, translate SDSs into the language understood by all workers.
- Ensure accessibility: Make SDSs accessible to all workers, regardless of their physical abilities or literacy levels.
3. Implementing Control Measures
Beyond simply providing information, employers must actively implement control measures to minimize worker exposure to hazardous materials. These measures might include:
- Engineering controls: Implementing engineering solutions such as ventilation systems, enclosed processes, or substitution of less hazardous materials.
- Administrative controls: Establishing safe work procedures, implementing a permit-to-work system, or rotating workers to minimize exposure.
- Personal protective equipment (PPE): Providing and ensuring the correct use of PPE such as gloves, respirators, eye protection, and safety footwear.
- Emergency preparedness: Developing and implementing emergency response plans to address spills, leaks, or other accidents involving hazardous materials. This includes training staff on emergency procedures, providing appropriate equipment, and practicing emergency drills.
4. Maintaining Compliance Records
Employers must maintain detailed records demonstrating their WHMIS compliance. This includes:
- Training records: Documentation of worker training sessions, including the date, attendees, and content covered.
- SDS records: A system for tracking and maintaining SDSs for all hazardous materials in the workplace.
- Incident reports: Records of any accidents or incidents involving hazardous materials.
- Inspections and audits: Documentation of regular inspections and audits conducted to ensure WHMIS compliance.
These records must be readily available for inspection by government officials and other authorized personnel.
The Supervisor's Role: Implementing and Monitoring WHMIS
While the employer holds ultimate responsibility, supervisors play a critical day-to-day role in WHMIS implementation. Their responsibilities include:
- Ensuring worker training: Supervising staff to ensure they understand and follow WHMIS procedures.
- Monitoring workplace practices: Regularly checking that workers are using hazardous materials safely and following established procedures.
- Enforcing WHMIS rules: Taking appropriate disciplinary action against workers who violate WHMIS regulations.
- Reporting incidents: Promptly reporting any accidents or incidents involving hazardous materials to the employer.
- Identifying hazards: Proactively identifying potential hazards related to hazardous materials and recommending corrective actions.
The Worker's Responsibility: Safe Handling and Reporting
Workers also play a critical role in maintaining WHMIS compliance. Their responsibilities include:
- Participating in training: Actively participating in WHMIS training and seeking clarification if anything is unclear.
- Following safe work procedures: Adhering to established procedures for handling, storing, and disposing of hazardous materials.
- Using PPE correctly: Properly using and maintaining any PPE provided.
- Reporting hazards: Immediately reporting any unsafe conditions or accidents involving hazardous materials to their supervisor.
- Reading SDSs: Familiarizing themselves with the SDS for any hazardous materials they handle.
Other Stakeholders: Joint Responsibility
While employers, supervisors, and workers are the primary players, other stakeholders also contribute to WHMIS compliance. These include:
- Suppliers: Suppliers of hazardous materials are responsible for providing accurate and up-to-date SDSs and labels that comply with WHMIS regulations.
- Government agencies: Government agencies such as the provincial occupational health and safety boards are responsible for enforcing WHMIS regulations and conducting workplace inspections.
- Health and safety committees: Health and safety committees, where established, play a crucial role in advising employers on WHMIS matters and promoting a safe working environment.
- Consultants and specialists: External consultants and specialists can assist employers in developing and implementing effective WHMIS programs.
Consequences of Non-Compliance
Failure to comply with WHMIS regulations can result in significant consequences, including:
- Fines and penalties: Employers can face substantial fines for WHMIS violations.
- Legal action: Workers injured due to WHMIS non-compliance may take legal action against their employers.
- Reputational damage: Non-compliance can damage an employer's reputation and affect its ability to attract and retain employees.
- Workplace accidents: The most serious consequence is the potential for workplace accidents resulting in injuries, illnesses, or even fatalities.
Conclusion: A Shared Commitment to Safety
WHMIS compliance isn't solely the responsibility of a single individual or department. It's a collective responsibility involving employers, supervisors, workers, suppliers, and government agencies. A strong WHMIS program requires a shared commitment to safety, proactive hazard identification, thorough worker training, robust control measures, and diligent record-keeping. By working together, all stakeholders can create a safer and healthier workplace for everyone. This collaborative approach is not only legally mandated but also ethically necessary to protect the well-being of all those who work in environments where hazardous materials are present. Continuous improvement and regular review of WHMIS practices are key to ongoing safety and compliance. Staying informed about updates and changes in WHMIS regulations is vital for maintaining a safe and compliant workplace.
Latest Posts
Related Post
Thank you for visiting our website which covers about Who Makes Sure Whmis Requirements Are Implemented In A Workplace . We hope the information provided has been useful to you. Feel free to contact us if you have any questions or need further assistance. See you next time and don't miss to bookmark.