Which Of These Is Not A Cost Of Quality
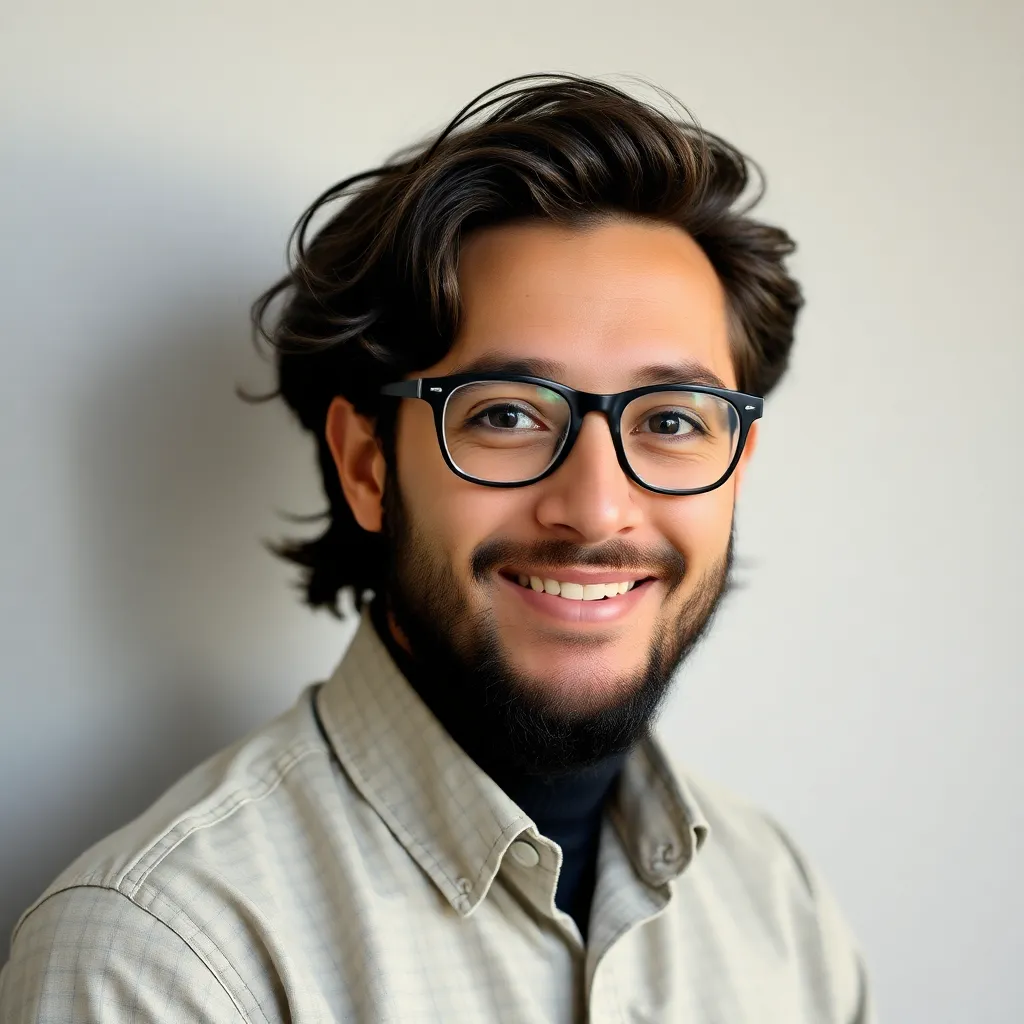
Holbox
Mar 29, 2025 · 6 min read
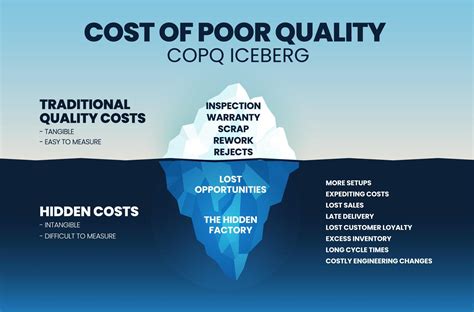
Table of Contents
- Which Of These Is Not A Cost Of Quality
- Table of Contents
- Which of These is NOT a Cost of Quality?
- Understanding the Costs of Quality
- 1. Prevention Costs
- 2. Appraisal Costs
- 3. Internal Failure Costs
- 4. External Failure Costs
- The Expense that ISN'T a Cost of Quality
- Strategic Implications of Understanding COQ
- Optimizing COQ: A Holistic Approach
- Conclusion
- Latest Posts
- Latest Posts
- Related Post
Which of These is NOT a Cost of Quality?
Understanding the costs associated with quality is crucial for any business striving for success. While many associate quality costs solely with the expenses of fixing defects, the reality is far more nuanced. The concept of "cost of quality" encompasses a broader range of expenditures, both preventative and appraisal, and even those seemingly unrelated to direct quality control. This article delves into the various types of quality costs, clearly identifying which expense does not fall under this umbrella and explaining why.
Understanding the Costs of Quality
The cost of quality (COQ) represents the total expenditure an organization incurs to achieve and maintain a specific level of product or service quality. These costs can be broadly categorized into four main groups:
1. Prevention Costs
These are proactive measures taken to prevent defects from occurring in the first place. They are investments made to improve the quality process and ultimately reduce future costs. Examples include:
- Training: Investing in employee training programs to enhance skills and knowledge in quality control procedures.
- Quality planning: Developing comprehensive quality plans and processes before production begins.
- Process improvement: Implementing tools and methodologies like Six Sigma or Lean to optimize processes and minimize defects.
- Design reviews: Conducting thorough reviews of product designs to identify and rectify potential quality issues early on.
- Supplier evaluations: Assessing and selecting reliable suppliers who meet or exceed quality standards.
- Process capability studies: Analyzing the capability of production processes to meet specifications and identify areas for improvement.
- Advanced equipment and technology: Investing in technology that aids in process automation and precision.
2. Appraisal Costs
These costs are associated with evaluating the quality of products, processes, and materials. They are incurred to detect defects before they reach the customer. Examples include:
- Inspections: Conducting routine inspections of materials, components, and finished products.
- Testing: Performing various tests to verify that products meet specifications and quality standards.
- Statistical process control (SPC): Monitoring processes using statistical methods to detect deviations from standards.
- Quality audits: Conducting regular audits to assess the effectiveness of quality systems and identify areas for improvement.
- Calibration of equipment: Regularly calibrating testing and measuring equipment to ensure accuracy.
3. Internal Failure Costs
These are the costs associated with defects discovered before the product or service reaches the customer. These are costs incurred to correct or fix defects within the organization. Examples include:
- Scrap: Discarding defective materials or products.
- Rework: Correcting defects in materials or products.
- Downtime: Production downtime due to equipment failures or quality issues.
- Troubleshooting: Investigating and resolving problems that occur during production.
- Re-inspection: Reinspecting products after rework to ensure quality.
- Inventory write-offs: Removing obsolete or damaged inventory from stock.
4. External Failure Costs
These are the costs associated with defects that are discovered after the product or service reaches the customer. These costs are often significantly higher than internal failure costs as they impact brand reputation, customer loyalty, and legal ramifications. Examples include:
- Warranty claims: Addressing customer complaints and repairing or replacing defective products under warranty.
- Returns: Processing returns of defective products.
- Complaints: Handling customer complaints about defective products or services.
- Legal actions: Dealing with lawsuits or legal actions related to product liability.
- Product recalls: Recalling defective products from the market.
- Lost sales: Decreased sales due to negative publicity and damaged reputation.
- Customer service: Increased workload related to handling customer issues concerning quality.
The Expense that ISN'T a Cost of Quality
While the categories above encompass a wide range of expenses, Marketing and Sales Costs are generally not considered a direct cost of quality.
While effective marketing and sales contribute to building a strong brand reputation and indirectly impact customer satisfaction, they do not directly relate to the prevention, appraisal, or failure related to the product's inherent quality. Strong marketing and sales can compensate for some external failures, but they don’t address the root cause of the quality issue itself.
Why Marketing and Sales aren't COQ:
- Focus on demand generation: Marketing and sales focus on creating demand and selling products. They don't directly involve detecting or preventing defects.
- Indirect impact on quality perception: While effective marketing can enhance the perception of quality, it doesn't address the actual quality of the product or service.
- Separate budget allocation: Marketing and sales are typically managed under separate budget lines distinct from quality management activities.
- Different metrics: Marketing and sales effectiveness is measured using metrics such as market share, sales volume, and brand awareness. Quality is measured using different metrics like defect rates, customer satisfaction scores, and process capability indices.
- Distinct roles and responsibilities: Marketing and sales teams have different roles and responsibilities from quality control and assurance teams.
However, a crucial nuance needs to be addressed. While not a direct cost of quality, poor marketing that misrepresents the quality of a product or service can inadvertently lead to increased external failure costs. For example, exaggerating the product features or capabilities that don't align with reality can lead to a surge in customer complaints, returns, and warranty claims. Therefore, while not a direct COQ element, ethical and accurate marketing is vital for minimizing indirect quality-related expenses.
Strategic Implications of Understanding COQ
Understanding and managing the costs of quality is a critical aspect of effective business management. Organizations that proactively invest in prevention and appraisal costs generally experience lower internal and external failure costs in the long run. This is a crucial element in achieving:
- Improved profitability: Reducing failure costs translates directly into improved profit margins.
- Enhanced customer satisfaction: Higher-quality products and services lead to greater customer loyalty and repeat business.
- Stronger brand reputation: A commitment to quality builds trust and strengthens the brand image.
- Competitive advantage: Consistently delivering high-quality products and services provides a distinct competitive edge in the marketplace.
- Reduced risk and liability: Proactive quality management minimizes the risk of product recalls, legal actions, and other liabilities.
Optimizing COQ: A Holistic Approach
Optimizing COQ requires a holistic approach, encompassing:
- Continuous improvement: Implement continuous improvement methodologies like Six Sigma or Kaizen to constantly identify and address areas for improvement.
- Data-driven decision making: Use data from various sources, including customer feedback, quality audits, and production data, to make informed decisions.
- Employee empowerment: Empower employees to identify and report quality issues and participate in improvement initiatives.
- Effective communication: Foster open communication among all stakeholders, including customers, suppliers, and employees.
- Regular review and adjustments: Regularly review the effectiveness of quality management systems and adjust them as needed.
Conclusion
The cost of quality is a multifaceted concept that encompasses a broad range of expenditures related to preventing, appraising, and rectifying defects. While expenses related to prevention and appraisal are proactive investments that minimize future costs, failure costs represent the financial burden of defects. However, marketing and sales costs, while crucial for business success, are generally not considered a direct cost of quality, although misleading marketing can indirectly inflate external failure costs. A comprehensive understanding and effective management of COQ are fundamental to achieving long-term success, profitability, and customer satisfaction. By strategically investing in prevention and appraisal, organizations can significantly minimize failure costs and secure a sustainable competitive edge.
Latest Posts
Latest Posts
-
The Magnetic Field At A Disn
Mar 31, 2025
-
Which Of The Following Statements About Savings Accounts Is False
Mar 31, 2025
-
Draw The Product Of An Sn2 Reaction Shown Below
Mar 31, 2025
-
When Writers Use Long Paragraphs In Business Messages It
Mar 31, 2025
-
Fill In The Blanks In Symbol Column Of The Table
Mar 31, 2025
Related Post
Thank you for visiting our website which covers about Which Of These Is Not A Cost Of Quality . We hope the information provided has been useful to you. Feel free to contact us if you have any questions or need further assistance. See you next time and don't miss to bookmark.