Which Of The Following Would Most Likely Use Process Costing
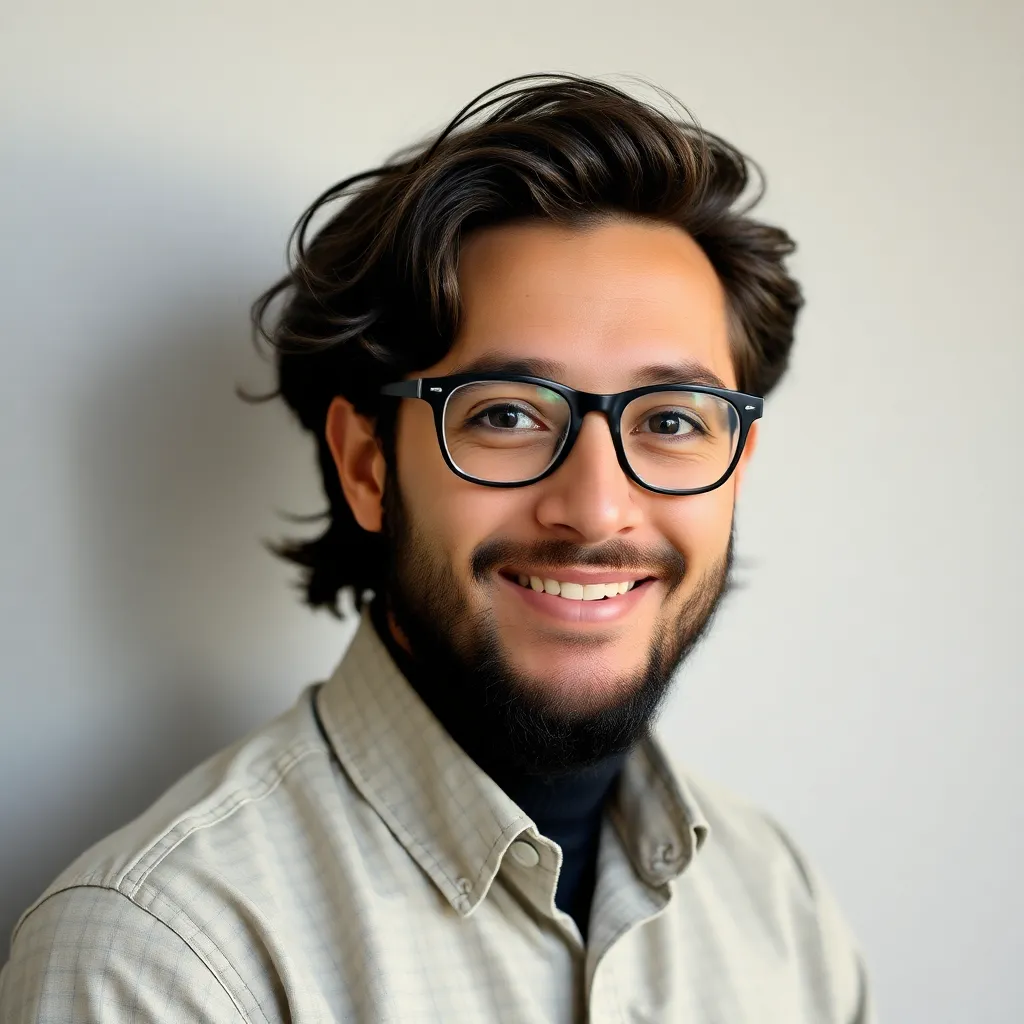
Holbox
Apr 05, 2025 · 6 min read

Table of Contents
- Which Of The Following Would Most Likely Use Process Costing
- Table of Contents
- Which of the Following Would Most Likely Use Process Costing?
- Understanding Process Costing: A Deep Dive
- When to Choose Process Costing Over Job-Order Costing
- Industries That Commonly Utilize Process Costing
- 1. Food Processing:
- 2. Chemical Manufacturing:
- 3. Oil Refining:
- 4. Textile Manufacturing:
- 5. Paper Manufacturing:
- 6. Plastics Manufacturing:
- The Process Costing Formula: A Step-by-Step Guide
- Advantages and Disadvantages of Process Costing
- Conclusion: Choosing the Right Costing Method
- Latest Posts
- Latest Posts
- Related Post
Which of the Following Would Most Likely Use Process Costing?
Process costing is a crucial costing method in accounting, particularly relevant for businesses producing large quantities of homogeneous products. Understanding when to apply process costing is vital for accurate financial reporting and effective cost management. This article delves into the situations where process costing shines, differentiating it from job-order costing and highlighting the industries and production processes where it’s most suitable.
Understanding Process Costing: A Deep Dive
Process costing is a system that assigns costs to masses of similar products or services. Unlike job-order costing, which tracks costs for individual projects or jobs, process costing averages costs across a large production run. This means that the cost of each individual unit is determined by dividing the total costs incurred in a specific production process by the total number of units produced during that process. This averaging makes it ideal for situations with high-volume, standardized production.
Key Characteristics of Industries Suitable for Process Costing:
- Mass Production: The cornerstone of process costing lies in the production of numerous, identical units. Think about food processing, oil refining, or chemical manufacturing – all characterized by high-volume, standardized outputs.
- Continuous Production: Processes typically involve continuous flow, with materials moving consistently through various stages of production. This constant flow allows for the tracking of costs at each stage.
- Homogeneous Products: The products or services produced are largely similar in terms of materials, labor, and overhead. Variations are minimal, making the averaging process relatively accurate.
- Difficult to Track Individual Costs: It’s impractical or impossible to track the specific costs associated with each individual unit produced. The sheer volume renders individual tracking inefficient and costly.
When to Choose Process Costing Over Job-Order Costing
The choice between process costing and job-order costing hinges on the nature of the production process and the product itself. While process costing excels in mass production scenarios, job-order costing is perfect for customized or unique projects.
Process Costing is ideal when:
- Products are homogenous: Each unit is nearly identical to the next.
- Production is continuous: Materials move through production stages in a steady flow.
- Costs are difficult to trace to individual units: The volume is too high for individual cost tracking.
- Mass production is the norm: Large quantities of similar items are produced.
Job-order costing is preferred when:
- Products are unique or customized: Each job is distinct with specific requirements.
- Production is sporadic: Projects are completed one at a time, rather than in a continuous flow.
- Costs can be easily traced to individual units: Tracking costs for each job is feasible and practical.
- Small production runs are common: The volume doesn't justify the use of averaging costs.
Industries That Commonly Utilize Process Costing
Several industries rely heavily on process costing due to their production characteristics. These include:
1. Food Processing:
Food processing plants exemplify the ideal scenario for process costing. Imagine a large-scale cereal manufacturer. Thousands of identical cereal boxes roll off the production line daily. Tracking the individual cost of each box would be an administrative nightmare. Instead, the total cost of production (raw materials, labor, overhead) is divided by the total number of boxes produced to arrive at the cost per unit. This applies to various food products, from canned goods to baked goods to beverages.
2. Chemical Manufacturing:
The chemical industry is another prime example. Chemicals are often produced in vast quantities, with the final product being largely homogeneous. The production process involves several stages, each contributing to the final cost. Process costing provides a clear and manageable method to allocate costs across these stages and determine the cost per unit of the chemical product.
3. Oil Refining:
Oil refining is a continuous process with a high volume of output. Crude oil is transformed into various petroleum products – gasoline, diesel, kerosene, etc. – and process costing is the most efficient method to allocate the cost of refining to each product type. The complexity of the refinery process makes individual cost tracking impossible.
4. Textile Manufacturing:
Textile mills produce vast quantities of cloth. While different colors and patterns might exist, the basic production process is largely the same. The cost of raw materials (cotton, yarn), labor, and overhead are averaged across the total output to determine the cost per unit of fabric.
5. Paper Manufacturing:
Paper production is a continuous and high-volume process. Raw materials are processed into paper rolls, which are then cut and packaged. Process costing facilitates the allocation of costs across various stages, from pulp preparation to final packaging.
6. Plastics Manufacturing:
Plastic production involves similar characteristics to those of the chemical and textile industries. Large quantities of plastic products are made, with minimal variation between individual items. The cost of raw materials (polymers), energy, labor, and overhead is distributed across the total production volume to determine the cost of each unit.
The Process Costing Formula: A Step-by-Step Guide
While the specific calculations can be complex, the fundamental process costing formula is straightforward:
Cost per Unit = Total Costs / Total Units Produced
This seemingly simple equation encompasses several key elements:
-
Total Costs: This includes all costs associated with the production process, categorized as:
- Direct Materials: Raw materials directly used in production.
- Direct Labor: Labor directly involved in production.
- Manufacturing Overhead: Indirect costs like rent, utilities, and depreciation of equipment.
-
Total Units Produced: The total number of units completed during the accounting period.
The process often involves calculating costs for different stages of production (departments or processes) and then aggregating them to determine the overall cost per unit. This often requires accounting for work-in-progress (WIP) inventory at the beginning and end of the accounting period, adding another layer of complexity.
Advantages and Disadvantages of Process Costing
Like any accounting method, process costing has its strengths and weaknesses. Understanding these is crucial for determining its suitability for a particular business.
Advantages:
- Simplicity and Efficiency: Relatively easy to implement and manage, particularly for high-volume, standardized production.
- Cost-Effectiveness: Reduces the administrative burden associated with tracking individual costs.
- Provides Average Unit Costs: Helpful in pricing decisions and inventory valuation.
- Suitable for Continuous Production: Perfectly aligned with processes involving a continuous flow of materials.
Disadvantages:
- Less Accurate for Heterogeneous Products: Averaging costs can be misleading if products show significant variations.
- Ignores Individual Job Differences: Doesn't account for variations in materials or labor costs within a production run.
- Complex Calculations: Can be complicated, especially with multiple production stages and significant WIP inventory.
- May Not Be Suitable for Custom Orders: Inflexible for businesses producing custom or specialized products.
Conclusion: Choosing the Right Costing Method
The decision to utilize process costing hinges on a careful assessment of the production process and the nature of the products or services being offered. Businesses involved in mass production of homogeneous goods will find process costing to be a highly efficient and effective tool for cost management and financial reporting. However, companies with unique or customized offerings should opt for job-order costing. Understanding the nuances of each method and carefully evaluating your specific circumstances is paramount for accurate financial reporting and informed business decisions. Remember, consulting with an accounting professional is always recommended to ensure you're applying the most appropriate costing method for your unique business needs.
Latest Posts
Latest Posts
-
Anatomy And Physiology An Integrative Approach Mckinley
Apr 12, 2025
-
If A Company Reports A Net Loss It
Apr 12, 2025
-
Identify The Statement Below That Is Correct
Apr 12, 2025
-
What Do The Credit Terms 2 15 N 30 Mean
Apr 12, 2025
-
The Optimal Allocation Of Resources Occurs When Blank
Apr 12, 2025
Related Post
Thank you for visiting our website which covers about Which Of The Following Would Most Likely Use Process Costing . We hope the information provided has been useful to you. Feel free to contact us if you have any questions or need further assistance. See you next time and don't miss to bookmark.