Which Of The Following Is Characteristic Of The Lean Philosophy
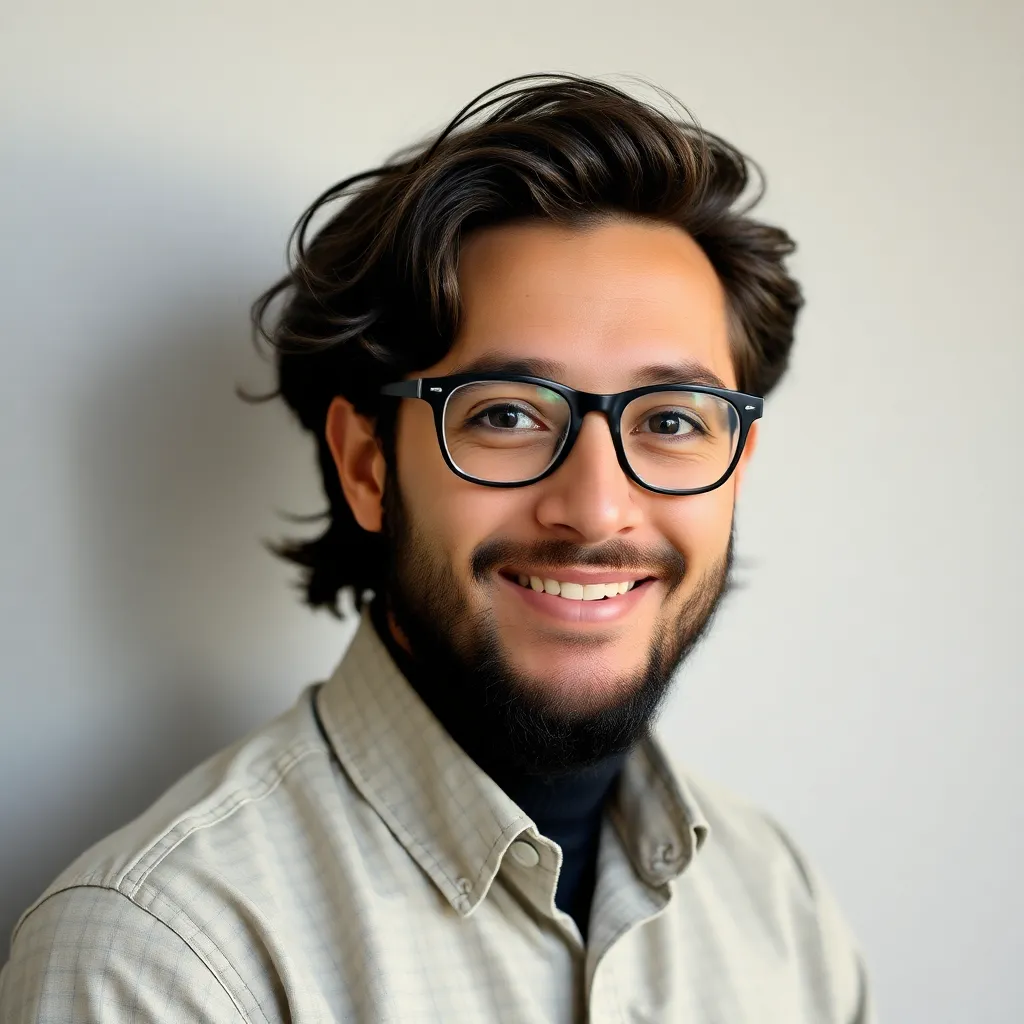
Holbox
May 10, 2025 · 6 min read
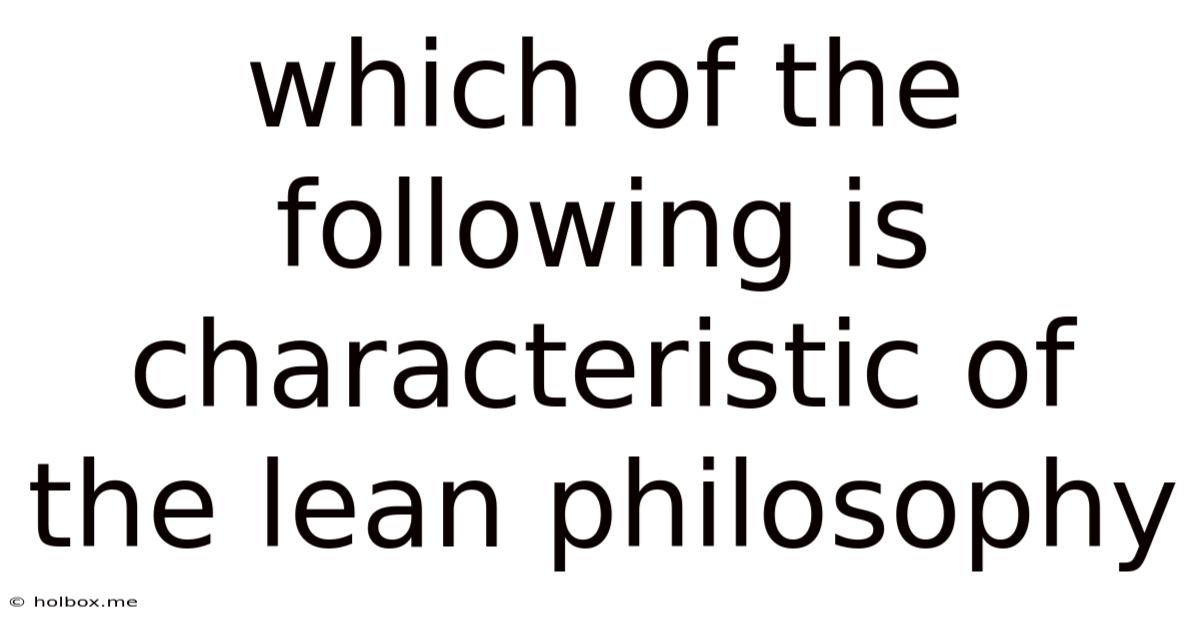
Table of Contents
- Which Of The Following Is Characteristic Of The Lean Philosophy
- Table of Contents
- Which of the Following is Characteristic of the Lean Philosophy? A Deep Dive into Lean Principles
- Core Tenets of Lean Thinking: Identifying the Characteristics
- 1. Value Definition from the Customer's Perspective:
- 2. Value Stream Mapping:
- 3. Waste Elimination (Muda):
- 4. Flow Optimization:
- 5. Pull System:
- 6. Perfection (Kaizen):
- 7. Respect for People:
- Distinguishing Lean from Other Methodologies
- Implementing Lean: A Step-by-Step Guide
- Measuring the Success of Lean Implementation
- Conclusion: Embracing the Lean Philosophy for Sustainable Success
- Latest Posts
- Related Post
Which of the Following is Characteristic of the Lean Philosophy? A Deep Dive into Lean Principles
Lean philosophy, a management approach initially developed by Toyota, has revolutionized industries worldwide. Its core principle centers around eliminating waste and maximizing value for the customer. But what exactly is characteristic of the lean philosophy? This comprehensive guide explores the key characteristics, providing detailed explanations and real-world examples to clarify its implementation.
Core Tenets of Lean Thinking: Identifying the Characteristics
Several key characteristics define the lean philosophy. Understanding these is crucial for successful implementation. Let's delve into the most prominent ones:
1. Value Definition from the Customer's Perspective:
This is arguably the most fundamental characteristic. Lean isn't about internal efficiency for efficiency's sake; it's about identifying and delivering what the customer truly values. This requires a deep understanding of customer needs and wants, often achieved through rigorous market research and direct customer feedback. Only activities directly contributing to this perceived value are considered worthwhile. Everything else is deemed waste.
Example: A car manufacturer focusing solely on producing vehicles quickly, without considering fuel efficiency, safety features desired by customers, or aesthetic preferences, is not applying lean principles effectively. Lean necessitates understanding the customer’s definition of "value" in a car – is it fuel economy, safety features, luxury, or a combination?
2. Value Stream Mapping:
Lean relies heavily on visualizing the entire process involved in delivering value to the customer. This visualization, typically done through value stream mapping, identifies all steps, including those that add value and those that don't. This detailed mapping provides a clear picture of the current state, highlighting areas ripe for improvement.
Example: Consider a restaurant. Value stream mapping would detail every step from receiving ingredients to serving the customer, showing where delays occur, where staff might be inefficient, and where steps could be streamlined or eliminated.
3. Waste Elimination (Muda):
A cornerstone of lean is identifying and eliminating all forms of waste. Lean identifies seven primary types of waste (often called the seven mudas):
- Transportation: Unnecessary movement of materials or products.
- Inventory: Excessive stockpiles of materials or finished goods.
- Motion: Unnecessary movements of people or equipment.
- Waiting: Delays in the production process.
- Overproduction: Producing more than is needed.
- Over-processing: Performing more work than necessary.
- Defects: Producing faulty products or services.
Beyond these seven, many lean practitioners also include non-utilized talent as an eighth muda. This refers to failing to utilize the skills and knowledge of employees effectively.
Example: A manufacturing plant with excessive inventory is wasting resources on storage, insurance, and potential obsolescence. Eliminating this waste through better forecasting and just-in-time delivery significantly improves efficiency.
4. Flow Optimization:
Once waste is identified, the next step is to optimize the flow of work. This involves streamlining processes, reducing bottlenecks, and ensuring a smooth, continuous flow of materials and information. This often requires cross-functional collaboration and a focus on continuous improvement.
Example: A software development team might use Agile methodologies to improve workflow, breaking down large projects into smaller, manageable tasks and ensuring continuous feedback. This fosters a consistent flow of progress and reduces delays.
5. Pull System:
Instead of pushing products through the production process, a pull system uses customer demand to drive production. This prevents overproduction and ensures that only what is needed is produced. The "pull" comes from downstream processes signaling the need for materials or products from upstream processes. This is commonly seen in Kanban systems.
Example: A supermarket uses a pull system; shelves are stocked based on customer purchases. When an item's stock gets low, the system automatically triggers an order for more. This prevents overstocking and ensures fresh products are always available.
6. Perfection (Kaizen):
Lean is not a one-time project; it's a continuous improvement philosophy. Kaizen, meaning "change for the better," emphasizes small, incremental improvements made regularly across all aspects of the organization. This ongoing process of refinement and optimization is vital to maintaining lean's effectiveness.
Example: A team regularly meets to review processes, identify areas for improvement, and implement small changes. These changes might seem minor individually, but cumulatively, they significantly enhance efficiency and reduce waste.
7. Respect for People:
Lean isn't just about processes and efficiency; it's about respecting and empowering employees. Lean principles emphasize teamwork, collaboration, and providing employees with the training and tools they need to improve their work and contribute to the overall success of the organization. Employee involvement is crucial for successful implementation.
Example: A company empowers its employees to identify and suggest improvements through suggestion boxes, regular feedback sessions, and cross-training opportunities. This fosters a culture of continuous improvement and ownership.
Distinguishing Lean from Other Methodologies
It's crucial to understand how lean differs from other management philosophies. While some methodologies share similarities, lean's unique characteristics set it apart:
-
Lean vs. Six Sigma: Both focus on process improvement, but Six Sigma emphasizes statistical methods to reduce variation and defects, while lean focuses on eliminating waste and optimizing flow. They can be complementary, with Six Sigma tools used to refine specific aspects of a lean process.
-
Lean vs. Agile: Both are iterative and focus on customer value, but Agile prioritizes software development, emphasizing flexibility and rapid iteration, while lean applies more broadly across different industries. However, Agile principles align well with a lean mindset and can be incorporated into lean implementation.
-
Lean vs. Total Quality Management (TQM): Both aim for quality improvement, but TQM is broader, focusing on all aspects of an organization, while lean prioritizes value stream optimization and waste elimination. Lean can be considered a subset of TQM focusing specifically on process efficiency.
Implementing Lean: A Step-by-Step Guide
Implementing lean effectively requires a structured approach:
- Identify Value: Define value from the customer's perspective.
- Map the Value Stream: Visualize the current state of the process.
- Create Flow: Eliminate waste and optimize the flow of work.
- Establish Pull: Implement a pull system to respond to customer demand.
- Pursue Perfection: Embrace Kaizen for continuous improvement.
- Engage Employees: Foster a culture of respect and empowerment.
Measuring the Success of Lean Implementation
Measuring the effectiveness of lean implementation requires tracking key metrics:
- Lead time: The time it takes to deliver a product or service.
- Cycle time: The time it takes to complete a single process step.
- Inventory levels: The amount of inventory on hand.
- Defect rates: The number of defective products or services.
- Employee satisfaction: Gauge employee morale and engagement.
Conclusion: Embracing the Lean Philosophy for Sustainable Success
Lean philosophy offers a powerful framework for enhancing organizational efficiency, improving quality, and ultimately, delivering superior customer value. By understanding and implementing its core characteristics, organizations can achieve significant improvements in productivity, profitability, and customer satisfaction. The journey towards lean is a continuous one, requiring commitment, collaboration, and a relentless focus on waste elimination and continuous improvement. Its enduring success lies in its adaptability and its unwavering commitment to customer value. This multifaceted approach ensures that the lean philosophy remains a relevant and effective strategy in today's dynamic business environment.
Latest Posts
Related Post
Thank you for visiting our website which covers about Which Of The Following Is Characteristic Of The Lean Philosophy . We hope the information provided has been useful to you. Feel free to contact us if you have any questions or need further assistance. See you next time and don't miss to bookmark.