Which Of The Following Are Related To Lean Production
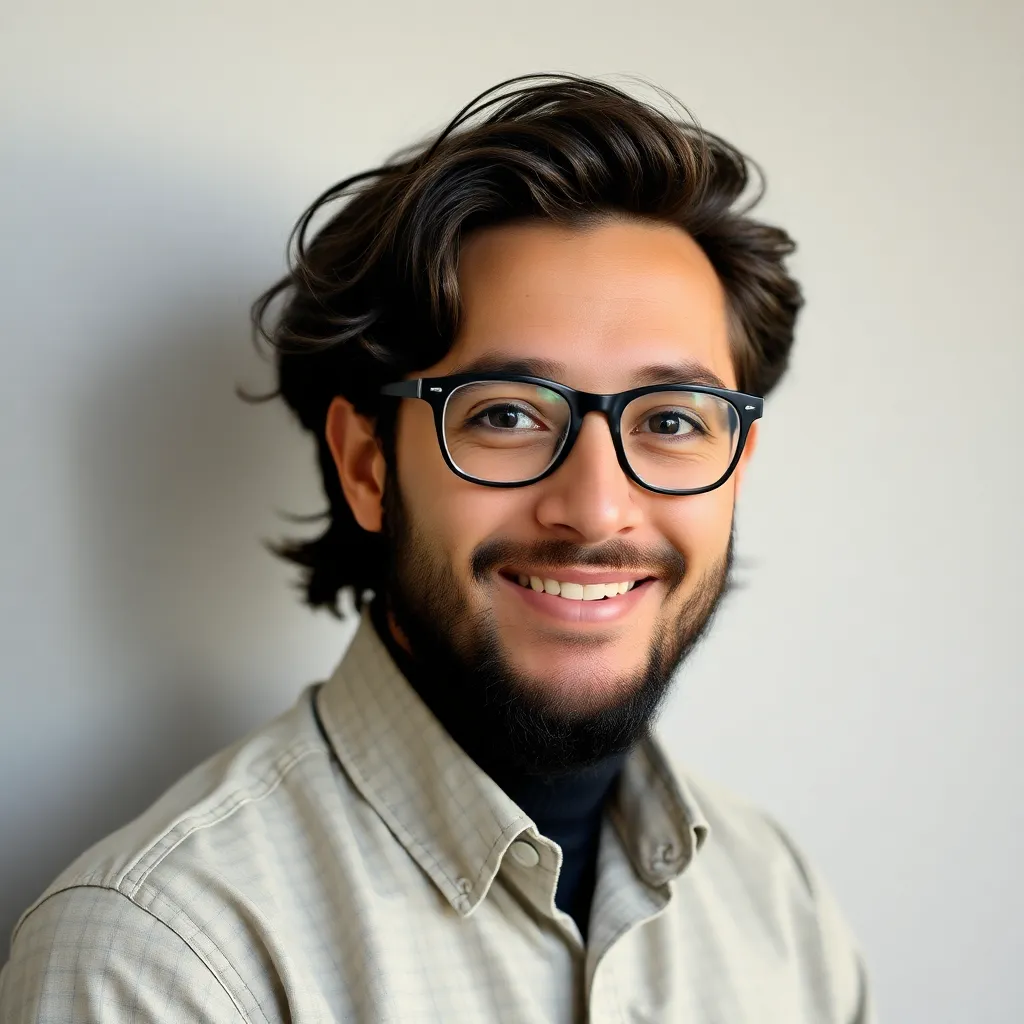
Holbox
May 10, 2025 · 6 min read
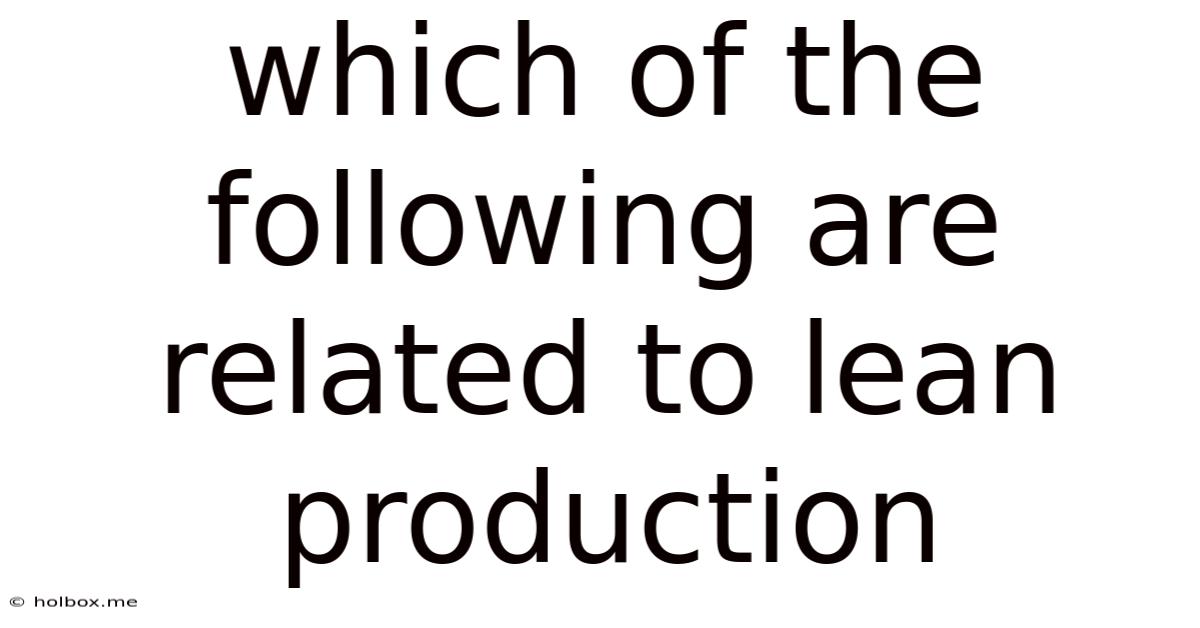
Table of Contents
- Which Of The Following Are Related To Lean Production
- Table of Contents
- Which of the Following are Related to Lean Production? A Deep Dive into Lean Principles and Practices
- Core Principles of Lean Production
- 1. Value: Defining Value from the Customer's Perspective
- 2. Value Stream: Mapping the Entire Process
- 3. Flow: Optimizing the Process for Smooth and Continuous Movement
- 4. Pull: Responding to Customer Demand
- 5. Perfection: Continuous Improvement (Kaizen)
- Identifying Lean-Related Practices: A Comprehensive List
- Expanding Lean Beyond Manufacturing: Applications in Other Sectors
- Implementing Lean Production: A Step-by-Step Approach
- Conclusion: The Enduring Relevance of Lean Production
- Latest Posts
- Latest Posts
- Related Post
Which of the Following are Related to Lean Production? A Deep Dive into Lean Principles and Practices
Lean production, also known as lean manufacturing, is a systematic method for minimizing waste and maximizing value within a manufacturing process. It's not simply about reducing costs; it's about optimizing the entire value stream to deliver exactly what the customer wants, when they want it, at the right price. This philosophy has expanded far beyond manufacturing, impacting various industries and business functions. Let's delve into the core principles and identify which practices align with the lean methodology.
Core Principles of Lean Production
Before we examine specific practices, it's crucial to understand the foundational principles that underpin lean production. These principles guide the implementation and continuous improvement efforts within a lean system.
1. Value: Defining Value from the Customer's Perspective
The cornerstone of lean is understanding and defining value strictly from the customer's perspective. What features and functionalities do customers truly value? What are they willing to pay for? Anything that doesn't add value from this perspective is considered waste. This requires a deep understanding of customer needs and expectations.
2. Value Stream: Mapping the Entire Process
A value stream map is a visual representation of all the steps involved in bringing a product or service from its inception to the customer. This map helps identify areas of waste and bottlenecks that hinder efficiency. By understanding the entire flow, lean practitioners can pinpoint opportunities for improvement.
3. Flow: Optimizing the Process for Smooth and Continuous Movement
Lean strives for a smooth, continuous flow of materials and information throughout the entire value stream. This means eliminating interruptions, delays, and bottlenecks that impede progress. A smoothly flowing process minimizes waste and maximizes efficiency.
4. Pull: Responding to Customer Demand
Rather than producing based on forecasts or pushing products onto the market, lean production operates on a "pull" system. Production is triggered by actual customer demand, ensuring that only what is needed is produced, eliminating excess inventory and reducing waste.
5. Perfection: Continuous Improvement (Kaizen)
Lean is not a destination but a journey of continuous improvement. Kaizen, the Japanese term for "continuous improvement," is integral to the lean philosophy. Teams continuously seek ways to eliminate waste, improve processes, and enhance efficiency.
Identifying Lean-Related Practices: A Comprehensive List
Now let's examine a range of practices and determine their relationship to lean production. Many practices support lean principles, while others might be counterproductive.
Practices Related to Lean Production:
-
5S Methodology: This organizational system (Sort, Set in Order, Shine, Standardize, Sustain) creates a clean, organized, and efficient work environment. By eliminating clutter and improving workplace organization, 5S directly supports lean's focus on reducing waste and improving workflow.
-
Kanban: This visual signaling system manages workflow by limiting work-in-progress (WIP) and ensuring that only the necessary tasks are undertaken. Kanban helps to control inventory, prevent bottlenecks, and improve flow, aligning perfectly with lean principles.
-
Just-in-Time (JIT) Inventory: JIT aims to minimize inventory levels by delivering materials and components exactly when needed for production. This reduces storage costs, minimizes waste from obsolescence or damage, and improves responsiveness to customer demand, a core element of lean thinking.
-
Poka-Yoke (Mistake-Proofing): Poka-Yoke focuses on designing processes and systems that prevent errors from occurring in the first place. By eliminating defects at the source, poka-yoke reduces waste associated with rework, scrap, and customer dissatisfaction.
-
Value Stream Mapping (VSM): As mentioned earlier, VSM is a crucial tool for visualizing the entire value stream and identifying areas for improvement. This visual representation provides a clear understanding of the flow of materials and information, enabling targeted improvement efforts.
-
Cellular Manufacturing: This approach organizes production into self-contained cells, where a group of workers performs a series of related operations on a product. Cellular manufacturing improves workflow, reduces lead times, and enhances flexibility.
-
Andon System: This visual signaling system alerts management to production problems as they occur. By quickly addressing issues, the andon system prevents them from escalating and causing widespread disruptions, minimizing downtime and waste.
-
Total Quality Management (TQM): TQM focuses on continuous improvement of quality throughout all aspects of the organization. This aligns perfectly with lean's focus on Kaizen and eliminating defects.
-
Six Sigma: This data-driven methodology aims to reduce variation and improve quality by identifying and eliminating defects. Six Sigma's focus on data analysis and process improvement complements lean's continuous improvement ethos.
Practices NOT Directly Related to Lean Production (or Potentially Counterproductive):
-
Mass Production: This approach relies on economies of scale and high volumes, often resulting in large inventories and potentially high levels of waste. It directly contradicts lean's emphasis on minimizing inventory and producing only what is needed.
-
High Inventory Levels: Holding large quantities of inventory ties up capital, increases the risk of obsolescence and damage, and masks problems within the production process. This is directly opposed to lean principles.
-
Batch and Queue Production: Producing in large batches creates delays, increases lead times, and often leads to higher inventory levels. Lean emphasizes a continuous flow, avoiding batch processing wherever possible.
-
Functional Layouts: In functional layouts, machines are grouped by function, resulting in longer transportation times and more complex workflows. Lean prefers cellular layouts for improved flow.
Expanding Lean Beyond Manufacturing: Applications in Other Sectors
While originating in manufacturing, the principles of lean production have found widespread application in diverse sectors. Here are a few examples:
-
Healthcare: Lean principles can optimize patient flow, reduce wait times, improve efficiency in hospital operations, and streamline administrative processes.
-
Software Development: Lean software development methodologies like Scrum and Kanban help to improve project management, reduce development time, and enhance product quality.
-
Education: Lean principles can be used to improve teaching methods, reduce administrative burden on teachers, and enhance the learning experience for students.
-
Government Services: Lean principles can streamline processes, reduce bureaucracy, and improve service delivery to citizens.
Implementing Lean Production: A Step-by-Step Approach
Implementing lean production is a continuous journey, not a one-time project. Here’s a simplified approach:
- Identify Value: Define value from the customer’s perspective.
- Map the Value Stream: Create a visual representation of the current process.
- Improve Flow: Identify and eliminate bottlenecks and wastes.
- Establish Pull: Implement a pull system based on actual customer demand.
- Pursue Perfection: Continuously improve processes through Kaizen.
Conclusion: The Enduring Relevance of Lean Production
Lean production is more than just a set of tools and techniques; it’s a philosophy centered on continuous improvement and delivering maximum value to the customer. By understanding its core principles and adopting appropriate practices, organizations across diverse sectors can enhance efficiency, reduce waste, and achieve sustainable growth. The practices listed above provide a clear indication of which methods align with and support this powerful management philosophy. The enduring relevance of lean lies in its adaptability and ability to address the ever-changing demands of the modern business environment. Continuous learning and adaptation are key to maximizing the benefits of this powerful approach.
Latest Posts
Latest Posts
-
How Many Inches Is 26 Cm
May 21, 2025
-
How Many Metres Is 50 Yards
May 21, 2025
-
How Many Stones In 76 Kg
May 21, 2025
-
How Much Is 57 Kg In Pounds
May 21, 2025
-
What Is 8 5 Stone In Lbs
May 21, 2025
Related Post
Thank you for visiting our website which covers about Which Of The Following Are Related To Lean Production . We hope the information provided has been useful to you. Feel free to contact us if you have any questions or need further assistance. See you next time and don't miss to bookmark.