Which Describes The Cost To Produce One Item
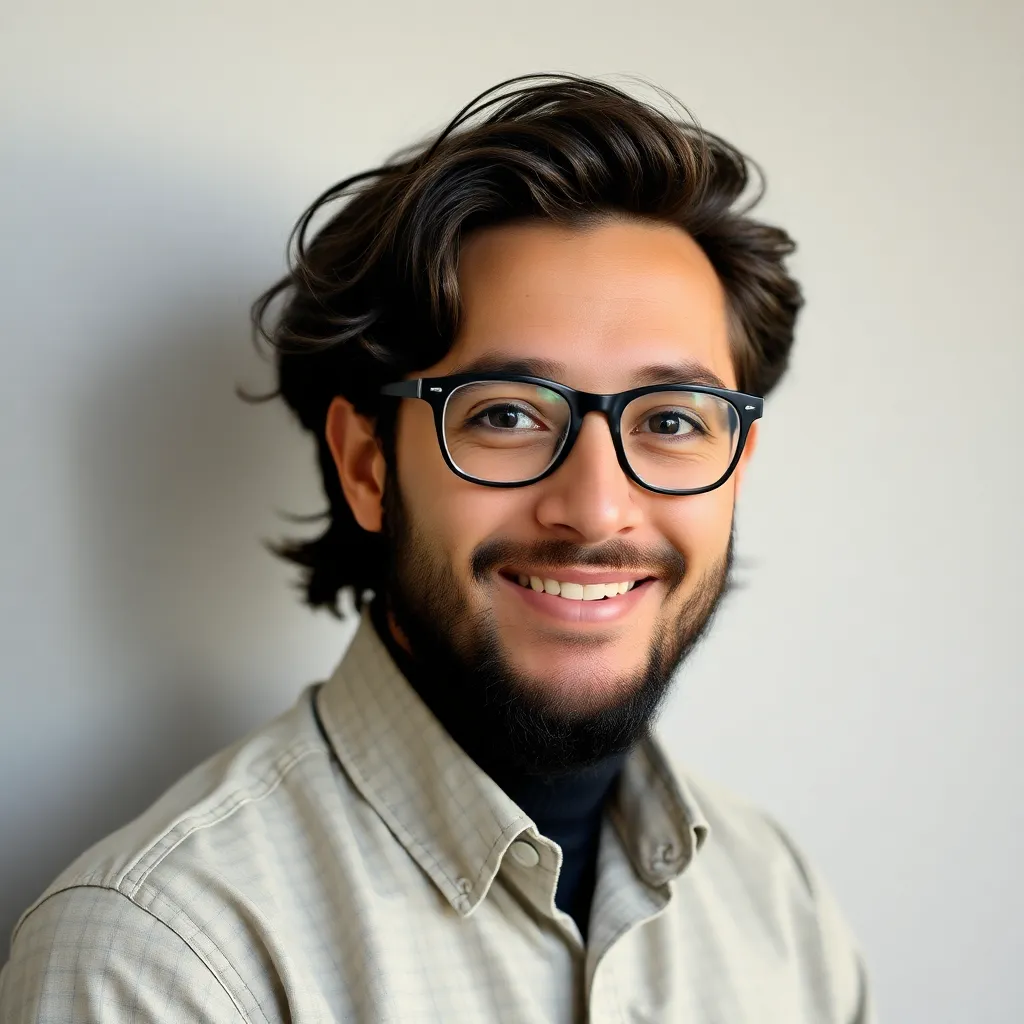
Holbox
Mar 27, 2025 · 6 min read
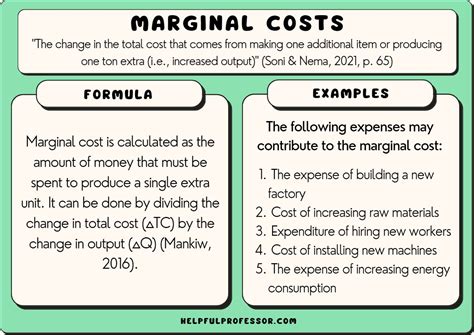
Table of Contents
- Which Describes The Cost To Produce One Item
- Table of Contents
- Decoding the Cost of Producing One Item: A Comprehensive Guide
- Direct Costs: The Foundation of Production
- 1. Raw Materials: The Building Blocks
- 2. Direct Labor: The Human Element
- 3. Manufacturing Overhead: Beyond the Basics
- Indirect Costs: The Hidden Expenses
- 1. Administrative Expenses: Running the Business
- 2. Selling and Marketing Expenses: Reaching Customers
- 3. Research and Development: Innovation and Improvement
- 4. General and Administrative Expenses: The Support System
- Calculating the Cost per Unit: A Step-by-Step Approach
- Beyond the Numbers: Factors Influencing Cost
- Conclusion: Mastering Cost Calculation for Profitability
- Latest Posts
- Latest Posts
- Related Post
Decoding the Cost of Producing One Item: A Comprehensive Guide
Understanding the true cost of producing a single item is crucial for businesses of all sizes. Pricing strategies, profit margins, and overall business viability hinge on this seemingly simple calculation. However, the process of accurately determining this cost is often more complex than it appears, requiring a deep dive into various direct and indirect expenses. This comprehensive guide will delve into the intricacies of cost accounting, providing you with a practical framework for calculating the cost of producing one item, no matter the nature of your business.
Direct Costs: The Foundation of Production
Direct costs are those expenses directly attributable to the creation of a single product. These costs are easy to track and directly impact the final price. Key categories include:
1. Raw Materials: The Building Blocks
Raw materials represent the fundamental components used in manufacturing. This is often the most significant direct cost. For example, a bakery's raw materials include flour, sugar, eggs, and butter. A clothing manufacturer will consider fabric, buttons, and zippers. Accurately calculating this cost requires meticulous inventory management and precise tracking of material usage per unit. Consider variations in material prices; fluctuating market prices can significantly impact your cost per item.
2. Direct Labor: The Human Element
Direct labor encompasses the wages and benefits paid to employees directly involved in the production process. This includes assembly line workers, machine operators, and skilled technicians. For accurate calculation, you need to track the time spent by each employee on a specific product. Consider labor efficiency. A highly skilled worker might produce more items in the same amount of time, thereby reducing the direct labor cost per unit.
3. Manufacturing Overhead: Beyond the Basics
While often overlooked, accurately accounting for manufacturing overhead is vital for a complete picture. This includes costs associated with running the production facility, but not directly tied to a single unit. Examples include:
- Factory rent and utilities: Electricity, gas, water, and the cost of renting or owning the production facility.
- Depreciation of machinery and equipment: The gradual decrease in value of machinery over time.
- Maintenance and repairs: Keeping equipment in optimal working condition.
- Factory supplies: Consumables such as lubricants, cleaning materials, and small tools.
- Quality control: Costs associated with testing and ensuring product quality.
Allocating manufacturing overhead to individual units can be done using various methods, including machine hours, direct labor hours, or a predetermined overhead rate. The choice of method depends on the nature of your production process.
Indirect Costs: The Hidden Expenses
Indirect costs, also known as overhead costs, are not directly tied to the production of a single item. They are essential for business operations but are more challenging to allocate to individual products. Key indirect costs include:
1. Administrative Expenses: Running the Business
This includes salaries of administrative staff, office rent, utilities, insurance, and other general administrative costs. Allocating these costs to individual products can be complex, often requiring a predetermined allocation method based on sales revenue or production volume.
2. Selling and Marketing Expenses: Reaching Customers
Costs associated with selling and marketing the product are also indirect. This includes advertising, sales commissions, shipping and handling, and trade show participation. These costs are often allocated based on sales revenue, with higher-selling items bearing a larger portion of these expenses.
3. Research and Development: Innovation and Improvement
The cost of research and development (R&D) is crucial for innovation and product improvement. These costs can be substantial and are often spread across multiple products over their lifecycle. A proper allocation method is crucial, considering the impact of the R&D efforts on each product.
4. General and Administrative Expenses: The Support System
These encompass the costs associated with running the overall business, including legal fees, accounting services, and IT support. Similar to administrative expenses, these costs need to be appropriately allocated across different products based on a suitable allocation key.
Calculating the Cost per Unit: A Step-by-Step Approach
Calculating the cost per unit requires a systematic approach. Here's a step-by-step guide:
-
Gather Data: Compile all relevant direct and indirect costs for a specific period. This includes raw materials, direct labor, manufacturing overhead, administrative expenses, selling and marketing expenses, research and development, and general and administrative expenses. The level of detail required depends on the complexity of your product and your desired accuracy.
-
Calculate Direct Costs per Unit: Divide the total direct costs (raw materials + direct labor) by the number of units produced during the period. This provides a direct cost per unit.
-
Allocate Indirect Costs: Allocate indirect costs to each product using a suitable method. Common methods include:
- Direct Labor Hours: Allocate indirect costs based on the number of direct labor hours used in production.
- Machine Hours: Allocate indirect costs based on the number of machine hours used in production.
- Sales Revenue: Allocate indirect costs based on the proportion of sales revenue generated by each product.
- Activity-Based Costing (ABC): A more sophisticated method that allocates indirect costs based on the specific activities involved in producing each product. This can be more accurate but also more complex.
-
Add Direct and Indirect Costs: Add the calculated direct cost per unit to the allocated indirect cost per unit. This provides the total cost per unit.
-
Analyze and Refine: Regularly review and analyze your cost data. Identify areas for cost reduction, improvement in efficiency, and optimization of production processes. The continuous improvement cycle is crucial for maintaining competitiveness and profitability.
Beyond the Numbers: Factors Influencing Cost
Several factors can significantly influence the cost of producing one item, beyond the direct and indirect costs. These include:
- Production Volume: Economies of scale often mean that the cost per unit decreases as production volume increases.
- Technology and Automation: Investing in automation can reduce labor costs and improve efficiency, lowering the cost per unit.
- Supplier Relationships: Strong relationships with suppliers can lead to favorable pricing on raw materials.
- Quality Control Measures: While quality control costs money, defects can be far more expensive. Finding the right balance is critical.
- Market Conditions: Fluctuations in raw material prices and labor costs can significantly impact the cost of production.
Conclusion: Mastering Cost Calculation for Profitability
Accurately determining the cost of producing one item is a cornerstone of successful business management. It's not simply a matter of adding up expenses; it requires a thorough understanding of cost accounting principles, careful data collection, and appropriate allocation methods. By mastering this process, businesses can make informed pricing decisions, optimize production processes, and ultimately, improve profitability. Remember to regularly review and refine your cost calculations, adapting to changing market conditions and technological advancements. This continuous process of improvement will ensure your business remains competitive and profitable in the long run.
Latest Posts
Latest Posts
-
Express The Force As A Cartesian Vector
Mar 31, 2025
-
Selling And Administrative Costs Are Blank Costs
Mar 31, 2025
-
Varcarolis Foundations Of Psychiatric Mental Health Nursing A Clinical Approach
Mar 31, 2025
-
For Accounts Receivable The Longer An Account Is Outstanding
Mar 31, 2025
-
Which Of The Following Is Not A Data Cleansing Activity
Mar 31, 2025
Related Post
Thank you for visiting our website which covers about Which Describes The Cost To Produce One Item . We hope the information provided has been useful to you. Feel free to contact us if you have any questions or need further assistance. See you next time and don't miss to bookmark.