What's One Solution To Vibrating Tool Hazards
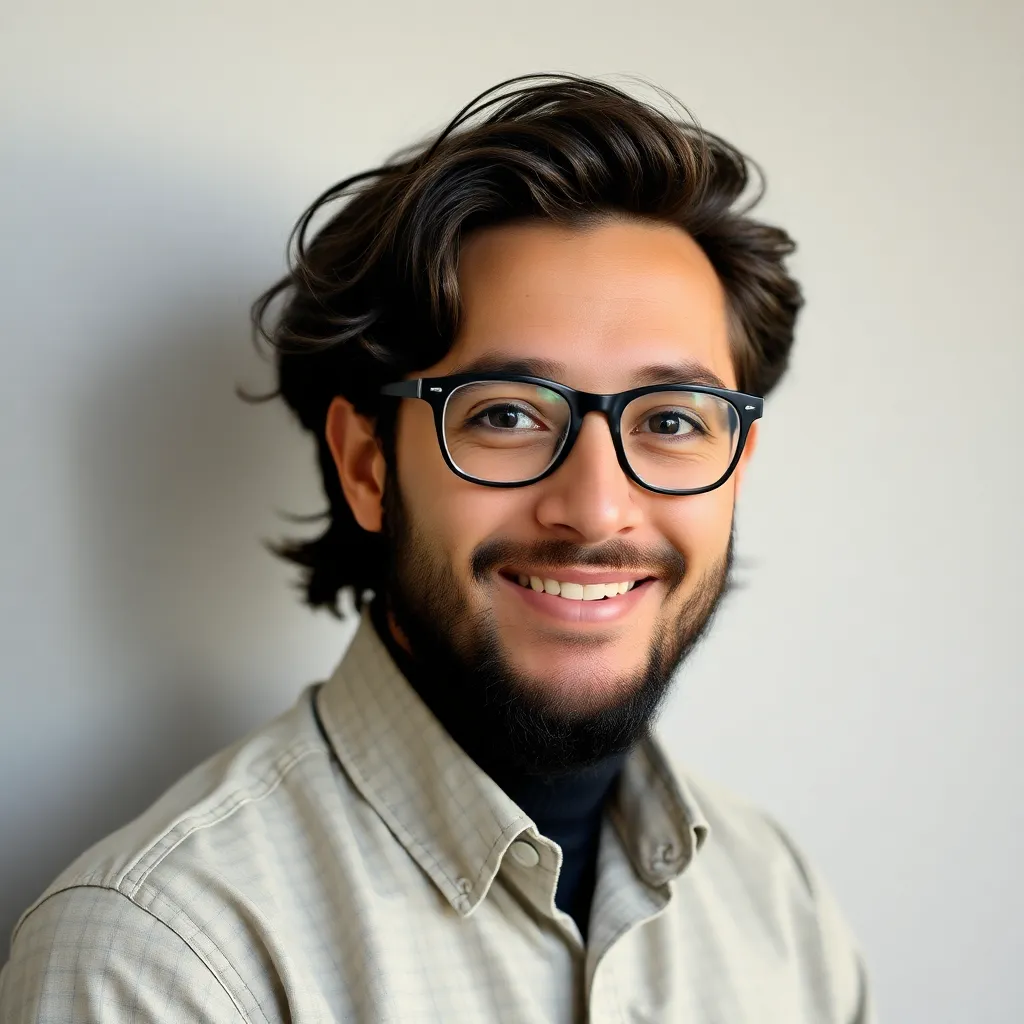
Holbox
May 09, 2025 · 6 min read
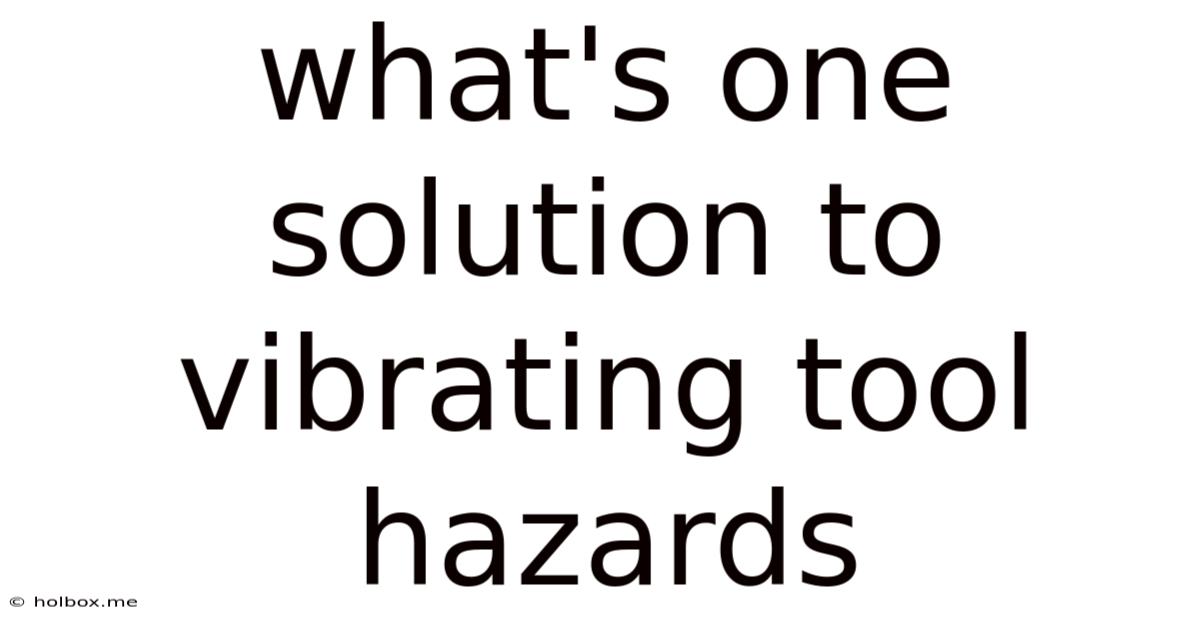
Table of Contents
- What's One Solution To Vibrating Tool Hazards
- Table of Contents
- What's One Solution to Vibrating Tool Hazards? A Deep Dive into Hand-Arm Vibration Syndrome (HAVS) Prevention
- Understanding Hand-Arm Vibration Syndrome (HAVS)
- Symptoms of HAVS
- The Crucial Role of Vibration Control
- 1. Source Control: Selecting Low-Vibration Tools
- 2. Path Control: Minimizing Vibration Transmission
- 3. Exposure Control: Limiting Time of Exposure
- Beyond Tool Selection: The Importance of a Holistic Approach
- Case Studies: Real-World Examples of Successful Vibration Control
- Conclusion: A Proactive Approach to HAVS Prevention
- Latest Posts
- Latest Posts
- Related Post
What's One Solution to Vibrating Tool Hazards? A Deep Dive into Hand-Arm Vibration Syndrome (HAVS) Prevention
Hand-Arm Vibration Syndrome (HAVS), a debilitating condition caused by prolonged exposure to vibrating tools, affects thousands of workers globally. The symptoms range from uncomfortable tingling to irreversible nerve damage, significantly impacting quality of life and earning potential. While eliminating vibration entirely is often impractical, focusing on effective vibration control presents the most comprehensive solution to mitigate these hazards. This article explores this crucial aspect of occupational health and safety, providing a detailed understanding of HAVS, its causes, and the vital role of vibration control in its prevention.
Understanding Hand-Arm Vibration Syndrome (HAVS)
HAVS, also known as vibration-induced white finger (VWF), is a serious occupational health problem arising from the repeated exposure to vibrations transmitted through hand-held power tools. The vibrations damage the blood vessels and nerves in the hands and arms, leading to a range of symptoms that can progressively worsen over time. The severity of the condition depends on various factors, including:
- Frequency and intensity of vibration: Higher frequency and intensity vibrations cause more damage.
- Duration of exposure: The longer the exposure, the greater the risk.
- Individual susceptibility: Some individuals are more susceptible to HAVS than others.
- Type of tool used: Different tools generate different vibration levels.
- Proper use of the tool: Incorrect tool usage can exacerbate vibration exposure.
Symptoms of HAVS
The symptoms of HAVS typically manifest gradually and can range in severity. Early symptoms might include:
- Numbness and tingling: A feeling of pins and needles in the fingers and hands.
- Coldness and pallor: Discoloration of the fingers, becoming pale or white.
- Reduced sensitivity to touch: Difficulty feeling textures or temperatures.
- Loss of grip strength: Weakening of the hands and fingers.
As the condition progresses, more serious symptoms can develop, such as:
- Severe pain: Chronic pain in the hands and arms.
- Joint stiffness: Difficulty bending and moving the fingers and wrists.
- Bone cysts: Formation of cysts in the bones of the hand.
- Permanent nerve damage: Irreversible loss of sensation and function.
The Crucial Role of Vibration Control
Effective vibration control is the cornerstone of HAVS prevention. This involves a multi-pronged approach that tackles the problem at its source: the vibrating tools themselves. Simply put, reducing the amount of vibration transmitted to the user's hands and arms is paramount. This can be achieved through various methods:
1. Source Control: Selecting Low-Vibration Tools
Choosing tools designed with low vibration levels is the most fundamental step. Manufacturers provide vibration data for their tools, usually expressed in m/s² (meters per second squared). When purchasing new tools, always prioritize models with the lowest possible vibration levels within the required performance specifications. Look for tools with features specifically designed to reduce vibration, such as:
- Anti-vibration handles: These handles are ergonomically designed to absorb vibration, minimizing transmission to the user's hands.
- Balanced design: A well-balanced tool reduces the amount of vibration generated.
- Improved motor technology: Advancements in motor technology contribute to lower vibration output.
2. Path Control: Minimizing Vibration Transmission
Even with low-vibration tools, minimizing vibration transmission is essential. This can be achieved through:
- Regular maintenance: Well-maintained tools operate more smoothly and generate less vibration. Check for loose parts, worn bearings, and ensure proper lubrication.
- Proper tool selection: Selecting the right tool for the job is crucial. Overloading a tool can increase vibration significantly.
- Ergonomic grips and posture: Maintaining a relaxed grip and proper posture reduces stress on the hands and arms, mitigating the impact of vibrations.
- Use of anti-vibration gloves: Special gloves designed to absorb vibration can provide an additional layer of protection. These gloves often have layers of cushioning material and ergonomic designs to distribute the impact.
- Vibration damping materials: In some applications, incorporating vibration damping materials into the tool's structure or the work environment can further reduce vibration transmission.
3. Exposure Control: Limiting Time of Exposure
Minimizing exposure time to vibration is a critical component of HAVS prevention. This involves strategies like:
- Work rotation: Rotating employees through different tasks to reduce the cumulative exposure to vibration.
- Scheduled breaks: Regular breaks allow for recovery and reduce the cumulative effect of vibrations.
- Task analysis: Careful analysis of work processes to identify opportunities for reducing vibration exposure time. This might involve changing work procedures or using different tools altogether.
- Work-rest schedules: Implementing structured work-rest schedules based on assessed vibration exposure levels.
Beyond Tool Selection: The Importance of a Holistic Approach
While choosing low-vibration tools is essential, a holistic approach to HAVS prevention extends beyond just the tools. Several other critical factors play a significant role:
- Training and education: Workers must be properly trained on the risks of HAVS, safe tool operation, and the importance of preventative measures. Regular training reinforces best practices and encourages safer work habits.
- Regular health surveillance: Periodic medical check-ups specifically focused on HAVS symptoms are vital. Early detection allows for intervention and prevents irreversible damage.
- Personal protective equipment (PPE): Although not a replacement for source and path control, appropriate PPE such as anti-vibration gloves can offer an extra layer of protection. However, it's important to note that PPE should be considered a supplementary measure, not a primary solution.
- Ergonomic workplace design: The work environment itself should be ergonomically designed to minimize strain on the hands and arms. This includes proper workstation setup, tool accessibility, and appropriate seating.
- Legislation and regulation: Adhering to relevant safety regulations and legislation ensures that adequate measures are in place to protect workers from HAVS. Staying informed about updates and changes in regulations is critical.
Case Studies: Real-World Examples of Successful Vibration Control
Several industries have implemented successful vibration control programs, leading to a significant reduction in HAVS cases. These programs typically involve a combination of the strategies outlined above. For instance, construction companies have adopted strategies such as:
- Implementing a rigorous tool selection policy: Prioritizing low-vibration tools and regularly auditing tool performance.
- Providing comprehensive worker training: Educating workers on safe tool use, maintenance, and HAVS prevention.
- Introducing regular health checks: Monitoring workers for early signs of HAVS.
- Implementing work-rest schedules: Managing exposure time through carefully planned work rotations.
These initiatives not only protect workers' health but also improve productivity and reduce the costs associated with work-related injuries.
Conclusion: A Proactive Approach to HAVS Prevention
Hand-Arm Vibration Syndrome is a preventable condition. By implementing a comprehensive vibration control strategy that combines tool selection, path control, and exposure control, businesses can significantly reduce the risk of HAVS among their workers. This proactive approach not only protects employees' health and well-being but also demonstrates a commitment to workplace safety and fosters a positive work environment. Remember, the most effective solution to vibrating tool hazards lies in a holistic approach that addresses all aspects of vibration control and incorporates ongoing monitoring and improvements. Prioritizing worker safety is not merely a legal requirement; it's a moral imperative and a sound business practice.
Latest Posts
Latest Posts
-
How Many Hours Is 9 Days
May 21, 2025
-
How Many Litres In 5 Gallons
May 21, 2025
-
What Is 64 Kg In Pounds
May 21, 2025
-
48 Kg Is How Many Pounds
May 21, 2025
-
74 70 Kg In Stones And Pounds
May 21, 2025
Related Post
Thank you for visiting our website which covers about What's One Solution To Vibrating Tool Hazards . We hope the information provided has been useful to you. Feel free to contact us if you have any questions or need further assistance. See you next time and don't miss to bookmark.