What Triggers The Need For A Value Stream
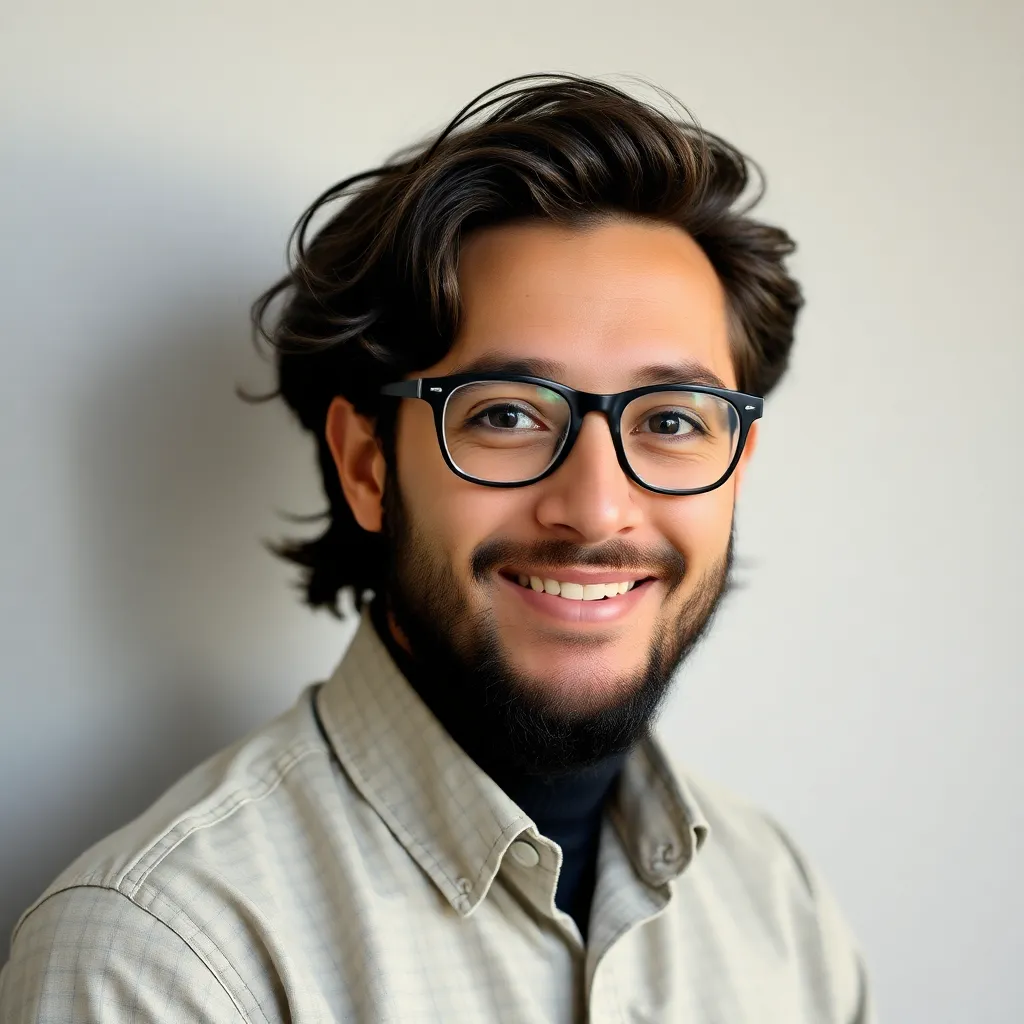
Holbox
Mar 11, 2025 · 7 min read

Table of Contents
- What Triggers The Need For A Value Stream
- Table of Contents
- What Triggers the Need for a Value Stream?
- Identifying the Need: Key Triggers for Value Stream Mapping
- 1. Declining Profitability and Margins
- 2. Long Lead Times and Cycle Times
- 3. High Inventory Levels and Waste
- 4. Poor Customer Satisfaction and Feedback
- 5. High Defect Rates and Rework
- 6. Missed Deadlines and Project Delays
- 7. Increased Competition and Market Pressure
- 8. Lack of Process Visibility and Transparency
- 9. Strategic Initiatives and Change Management
- 10. Mergers, Acquisitions, and Organizational Restructuring
- The Value Stream Mapping Process: A Detailed Overview
- Benefits Beyond Efficiency: The Broader Impact of Value Stream Mapping
- Conclusion: Proactive Improvement Through Value Stream Mapping
- Latest Posts
- Related Post
What Triggers the Need for a Value Stream?
Understanding when and why to implement a value stream map is crucial for organizational success. While the benefits of lean methodologies and value stream mapping are widely acknowledged, knowing the specific triggers that necessitate this process is equally important. This article delves into the various scenarios that signal the need for a value stream analysis, providing a comprehensive overview of the telltale signs and underlying reasons.
Identifying the Need: Key Triggers for Value Stream Mapping
Several factors can indicate the necessity of implementing a value stream. These can range from obvious operational inefficiencies to more subtle organizational challenges. Let's explore these triggers in detail:
1. Declining Profitability and Margins
Persistent reduction in profit margins is a major red flag. When profits are shrinking despite stable or increasing sales volume, it's a clear sign that operational costs are too high. A value stream map can help visualize the entire process, pinpoint areas of waste, and identify opportunities for cost reduction. This could involve streamlining processes, reducing inventory, or improving efficiency in production or service delivery. Analyzing the flow of materials and information reveals bottlenecks and unnecessary steps draining profitability.
2. Long Lead Times and Cycle Times
Excessively long lead times (the time it takes to fulfill a customer order) and cycle times (the time it takes to complete a single process step) directly impact customer satisfaction and competitiveness. If customers are waiting too long for products or services, you risk losing them to competitors offering faster turnaround times. Value stream mapping helps identify the root causes of these delays, whether it's excessive work-in-progress (WIP), inefficient processes, or communication breakdowns. By visually representing the flow, bottlenecks become immediately apparent, allowing for targeted improvements.
3. High Inventory Levels and Waste
Excessive inventory ties up capital, increases storage costs, and risks obsolescence. A value stream map highlights the inventory build-up points, revealing where materials or products are sitting idle for extended periods. This analysis allows for a reduction in WIP, implementation of just-in-time inventory systems, and identification of other forms of waste, such as overproduction, waiting, transportation, motion, over-processing, defects, and underutilized talent. Lean principles, made visible through the value stream map, facilitate waste reduction strategies.
4. Poor Customer Satisfaction and Feedback
Negative customer feedback consistently pointing towards long wait times, inconsistent product quality, or unreliable service delivery should trigger a thorough value stream analysis. Understanding the customer journey and mapping the entire process from order placement to delivery allows for pinpointing areas where customer experience is negatively impacted. This may reveal issues within individual processes, handoffs between departments, or systemic problems affecting the overall customer journey.
5. High Defect Rates and Rework
Significant rework and defect rates are costly and damaging to reputation. Value stream mapping can identify the steps where defects are most likely to occur, allowing for preventive measures and improved quality control. By understanding the flow of materials and information, you can pinpoint the source of defects, whether it's faulty equipment, inadequate training, or poor process design. This visualization allows for the implementation of quality control measures at critical points in the process.
6. Missed Deadlines and Project Delays
Recurring missed deadlines and project delays point to inefficiencies in planning, execution, and resource allocation. A value stream map can help uncover bottlenecks and resource constraints that contribute to these delays. This can range from issues with communication and collaboration between different teams to lack of clear roles and responsibilities.
7. Increased Competition and Market Pressure
Increased competition necessitates continuous improvement and optimization of processes. Value stream mapping allows organizations to identify areas for improvement in efficiency, speed, and quality, making them more competitive in the market. This is especially crucial in rapidly changing industries where adaptability and speed are key success factors.
8. Lack of Process Visibility and Transparency
Without a clear understanding of how processes work, it’s nearly impossible to identify areas for improvement. Value stream mapping provides a visual representation of the entire process, increasing transparency and fostering better collaboration across teams. This increased visibility empowers teams to identify areas for improvement and allows for better decision making.
9. Strategic Initiatives and Change Management
Implementing a major strategic initiative, such as a new product launch or a significant organizational restructuring, requires a clear understanding of the existing processes and their impact on the overall value chain. Value stream mapping can serve as a vital tool to support these initiatives, ensuring a smooth transition and minimizing disruptions.
10. Mergers, Acquisitions, and Organizational Restructuring
Following a merger, acquisition, or significant organizational restructuring, processes often become fragmented and inefficient. Value stream mapping facilitates the integration of disparate processes, identifying redundancies and opportunities for streamlining operations. This helps in creating a unified and efficient operational structure post-integration.
The Value Stream Mapping Process: A Detailed Overview
Once the need for a value stream map is established, the mapping process itself should follow a structured approach:
1. Define the Value Stream: Clearly define the scope of the value stream to be mapped, specifying the starting and ending points of the process. This could be the entire process from raw materials to finished product or a specific sub-process requiring improvement.
2. Identify the Process Steps: Map out all the steps involved in the chosen value stream, including both value-added and non-value-added activities. This involves documenting each step, its duration, and the resources required.
3. Gather Data: Collect data on each process step, such as processing time, cycle time, lead time, and inventory levels. This data is crucial for accurate analysis and identification of bottlenecks.
4. Create the Map: Use a visual representation to illustrate the flow of materials and information, highlighting the key process steps, inventory levels, and bottlenecks.
5. Analyze the Map: Analyze the completed map to identify areas of waste, inefficiencies, and bottlenecks. This often involves using lean tools and principles to identify areas for improvement.
6. Develop Improvement Strategies: Based on the analysis, develop specific improvement strategies aimed at eliminating waste, reducing cycle times, and improving overall efficiency.
7. Implement Improvements: Implement the planned improvements, monitoring their impact on the value stream.
8. Continuous Improvement: Value stream mapping is an iterative process. Regularly review and update the map to reflect any changes in the process and identify new opportunities for improvement.
Benefits Beyond Efficiency: The Broader Impact of Value Stream Mapping
The benefits of value stream mapping extend beyond immediate efficiency improvements. By fostering a culture of continuous improvement, it creates a ripple effect throughout the organization:
- Improved Collaboration: The process encourages cross-functional collaboration, breaking down silos and fostering a shared understanding of the overall process.
- Enhanced Employee Engagement: Involving employees in the mapping and improvement process increases their ownership and engagement.
- Increased Transparency: The visual representation of the process increases transparency, making it easier to identify and address problems.
- Faster Time to Market: Streamlined processes lead to faster delivery of products or services, enhancing competitiveness.
- Better Customer Satisfaction: Improved efficiency and quality lead to better customer experiences.
- Reduced Costs: Eliminating waste and improving efficiency directly translates into cost savings.
- Increased Agility: A well-mapped value stream allows for greater flexibility and responsiveness to changing market demands.
Conclusion: Proactive Improvement Through Value Stream Mapping
The need for a value stream map often arises from a combination of internal and external pressures. While declining profitability or customer dissatisfaction might be obvious triggers, even subtle signs like missed deadlines or high inventory levels can point towards significant underlying problems. By proactively identifying these triggers and implementing value stream mapping, organizations can gain a deeper understanding of their processes, optimize operations, and achieve sustainable growth in a competitive landscape. It’s not just about fixing immediate issues; it’s about building a culture of continuous improvement that drives long-term success. The investment in this process yields far-reaching benefits, affecting efficiency, customer satisfaction, employee engagement, and ultimately, the bottom line. The earlier the trigger is recognized and addressed, the greater the potential for positive transformation.
Latest Posts
Related Post
Thank you for visiting our website which covers about What Triggers The Need For A Value Stream . We hope the information provided has been useful to you. Feel free to contact us if you have any questions or need further assistance. See you next time and don't miss to bookmark.