What Is The Line Function Of The Extruder Characteristics
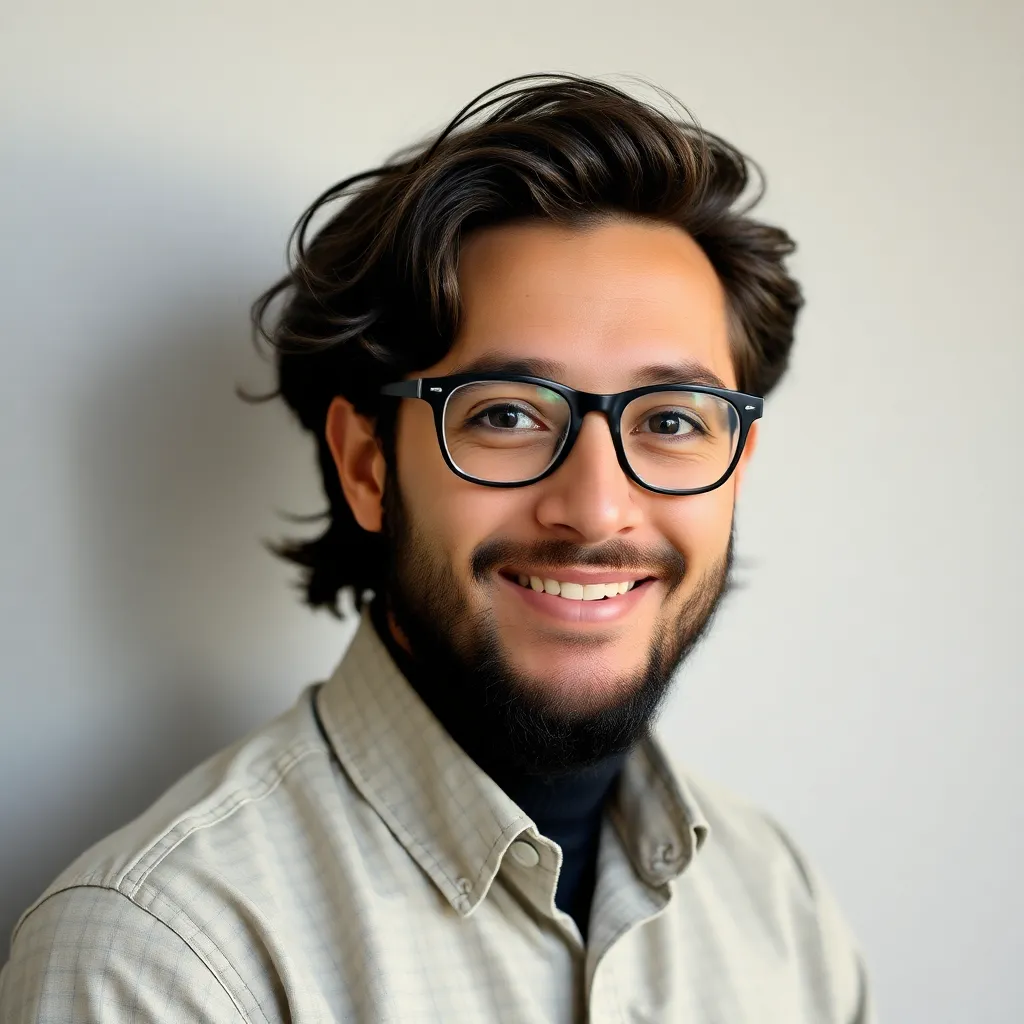
Holbox
Apr 13, 2025 · 6 min read
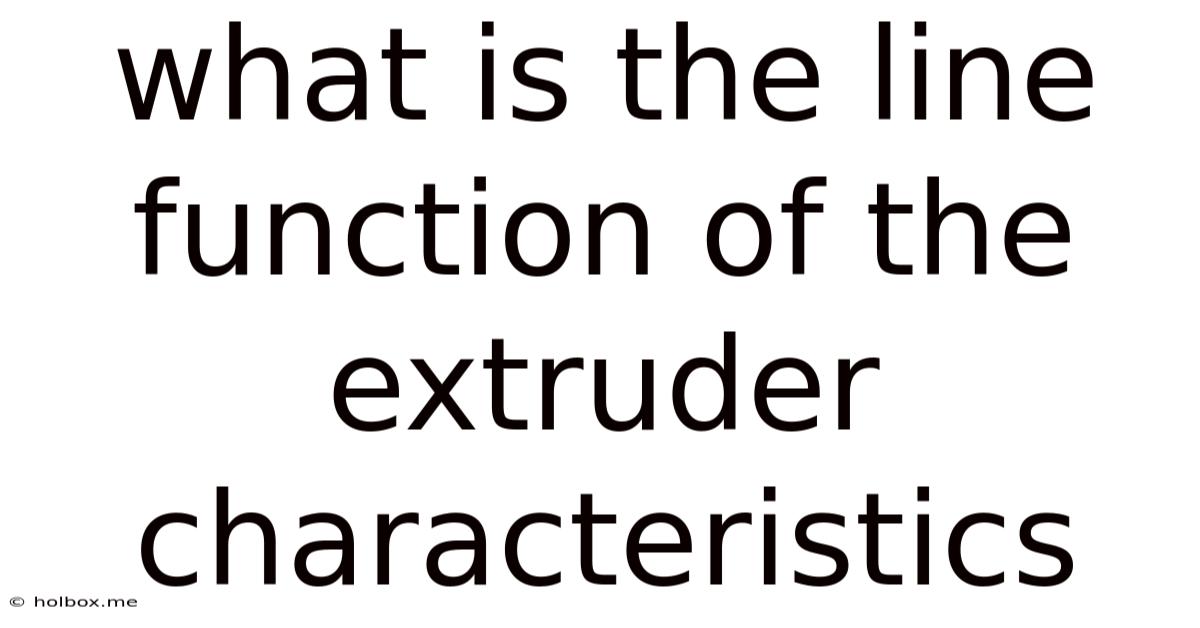
Table of Contents
- What Is The Line Function Of The Extruder Characteristics
- Table of Contents
- What is the Line Function of the Extruder Characteristics?
- Understanding Extruder Functionality: A Foundation
- Defining the Extruder Line Function
- Components of the Line Function Curve
- Factors Affecting the Extruder Line Function
- 1. Screw Design and Geometry:
- 2. Barrel Temperature Profile:
- 3. Screw Speed:
- 4. Die Geometry:
- 5. Material Properties:
- 6. Back Pressure:
- Practical Applications and Interpretations of the Extruder Line Function
- Advanced Considerations: Beyond the Basic Line Function
- Conclusion
- Latest Posts
- Latest Posts
- Related Post
What is the Line Function of the Extruder Characteristics?
Extruders are crucial components in numerous industries, from plastics processing and food manufacturing to pharmaceuticals and 3D printing. Understanding their characteristics, specifically their "line function," is paramount for optimizing their performance and achieving desired product quality. This comprehensive guide delves deep into the intricacies of extruder line function, providing a detailed analysis for both seasoned professionals and newcomers alike.
Understanding Extruder Functionality: A Foundation
Before diving into the line function, let's establish a foundational understanding of how extruders work. Extruders are essentially pumps that convey and melt viscous materials. They achieve this through a rotating screw, housed within a barrel, that pushes material forward while simultaneously applying heat and shear to melt and homogenize it. Key components include:
- Screw: The heart of the extruder, designed with specific geometry to promote melting, mixing, and conveying.
- Barrel: A heated cylinder that houses the screw and provides the necessary thermal energy for melting.
- Die: The final component, shaping the molten material into the desired form.
The screw's design dictates much of the extruder's overall performance. Different screw designs (e.g., single-flight, twin-flight, barrier screws) are tailored to specific applications and material properties.
Defining the Extruder Line Function
The extruder line function graphically represents the relationship between the pressure and flow rate of the melt leaving the die. It's a crucial characteristic curve that reveals essential information about the extruder's capacity and efficiency. The line function isn't a straight line; instead, it typically displays a non-linear relationship, often represented as a curve. This curve provides valuable insight into various aspects of the extrusion process.
Components of the Line Function Curve
The extruder line function graph typically plots pressure (on the y-axis) against flow rate (on the x-axis). Several key regions within the curve deserve attention:
-
Low Flow Rate Region: At low flow rates, the pressure initially increases sharply. This is because the melt is not fully developed and the screw is not operating at its full conveying capacity. Friction and pressure build up significantly in this region.
-
Transition Region: As the flow rate increases, the pressure increase gradually slows down. This transition region signifies the point where the extruder's performance starts to stabilize. The melt is more developed, and the screw's efficiency increases.
-
High Flow Rate Region: At very high flow rates, the pressure increase tapers off or may even slightly decrease. This indicates that the extruder is approaching its maximum capacity. Further increases in flow rate might lead to instability and reduced quality of the extrudate.
-
Melt Fracture Point: This critical point marks the beginning of instability, characterized by irregularities and surface defects on the extrudate. Operating beyond this point should be avoided, as it drastically compromises product quality and efficiency. The exact location of the melt fracture point depends on many factors, including melt viscosity, die geometry, and extruder speed.
Factors Affecting the Extruder Line Function
The shape and position of the extruder line function curve are highly sensitive to various factors. Understanding these influencing factors is crucial for optimizing the extrusion process:
1. Screw Design and Geometry:
The screw's geometry (e.g., channel depth, flight angle, compression ratio) significantly impacts the melt flow and pressure development. A screw designed for high output may have a different line function compared to a screw optimized for high melt homogeneity.
2. Barrel Temperature Profile:
Maintaining an optimal barrel temperature profile is essential for achieving consistent melt flow and reducing pressure fluctuations. Uneven heating can lead to uneven melting and affect the shape of the line function curve.
3. Screw Speed:
The rotational speed of the screw directly influences the melt flow rate. Increasing the screw speed generally increases the flow rate and alters the pressure-flow relationship, shifting the entire line function curve to the right.
4. Die Geometry:
The die's design (e.g., land length, diameter, and shape) plays a vital role in the flow resistance and pressure drop. A longer die land length, for example, will result in a steeper line function curve, signifying increased pressure for the same flow rate.
5. Material Properties:
The material being processed significantly influences the line function. High-viscosity materials will exhibit higher pressure for the same flow rate compared to lower-viscosity materials. Melt elasticity and temperature sensitivity also play a crucial role.
6. Back Pressure:
The pressure at the die exit can affect the overall pressure profile. A higher back pressure (e.g., due to downstream processing equipment) will shift the line function curve upward.
Practical Applications and Interpretations of the Extruder Line Function
The extruder line function is not merely a theoretical concept; it's a powerful tool for process optimization and troubleshooting. Here are several practical applications:
-
Process Optimization: By analyzing the line function, manufacturers can determine the optimal operating parameters (screw speed, temperature profile, back pressure) to maximize throughput while maintaining consistent product quality. It helps in avoiding operating conditions that may lead to melt fracture.
-
Troubleshooting: An unexpected change in the line function can indicate a problem within the extrusion process. For example, a sudden shift in the curve might point to a problem with the screw, die, or heating system. Analyzing the deviation helps in identifying the source of the issue.
-
Predictive Modeling: The line function can be incorporated into predictive models to simulate different operating conditions and anticipate potential challenges before they occur. This facilitates more efficient process design and optimization.
-
Scale-up and Design: The line function is invaluable during the scale-up process from laboratory to industrial production. It helps in predicting the performance of larger extruders and ensuring consistent product quality across different scales.
Advanced Considerations: Beyond the Basic Line Function
While the basic pressure-flow relationship provides a good understanding of extruder performance, more advanced considerations further refine the analysis:
-
Rheological Properties: Incorporating the material's rheological properties (viscosity as a function of shear rate and temperature) into the line function analysis provides a more comprehensive understanding of melt behavior.
-
Numerical Simulation: Computational Fluid Dynamics (CFD) simulations can generate detailed flow fields and pressure distributions within the extruder, enhancing the understanding of the line function and its origins.
-
Statistical Process Control (SPC): Implementing SPC techniques to monitor the extruder line function over time helps in early detection of deviations and prevents quality issues.
Conclusion
The extruder line function is a critical characteristic curve that provides invaluable insight into the performance and capabilities of an extruder. By understanding the factors influencing the line function and employing the techniques described above, manufacturers can optimize their extrusion processes, ensure consistent product quality, and improve overall efficiency. From process troubleshooting to scale-up and design, the line function serves as a cornerstone for effective extrusion processing across diverse industries. Continuous monitoring and analysis of this function are key to maximizing the potential of this crucial piece of equipment.
Latest Posts
Latest Posts
-
Draw The Major Organic Product From The Reaction Sequence Provided
Apr 27, 2025
-
The Last Dance Encountering Death And Dying 11th Edition
Apr 27, 2025
-
How Are Consumer Lifestyles Are Measured
Apr 27, 2025
-
To Show Your Sincerity In An Appreciation Message You Should
Apr 27, 2025
-
Vision Is Primarily Processed In The Lobes
Apr 27, 2025
Related Post
Thank you for visiting our website which covers about What Is The Line Function Of The Extruder Characteristics . We hope the information provided has been useful to you. Feel free to contact us if you have any questions or need further assistance. See you next time and don't miss to bookmark.